Although this niche isn’t for everyone, there’s a growing worldwide demand
by Zena Ryder
- There’s a need for cleanrooms in the pharmaceutical, electronics and food industries
- Although many cleanrooms are stick-built, panelized and modular construction offers many of the same advantages here as with other types of structures
- While the potential profits are attractive, supplying this niche places high demands on manufacturers
The pandemic increased demand for prefabricated cleanrooms. Manufacturing them can be a lucrative business, but requires a lot of technical know-how.

What is a Cleanroom?
Cleanrooms maintain strict environmental conditions so processes can be carried out with minimal risk of contamination. They’re used in the food and beverage, pharmaceutical and electronics industries.
They’re also used for different purposes, including manufacturing, testing and product development. For example, diagnostic medical tests that are sensitive to contamination by airborne particles such as dust or pollen might be performed in a medical laboratory cleanroom.
Cleanrooms are airtight. Fresh air enters through HEPA filters, which capture at least 99.97% of particles 0.3 microns in size. (A human hair is between 50 and 70 microns in diameter.) Stale air is also constantly removed with minimal turbulence.
ISO, the International Organization for Standards, specifies different levels of air quality for cleanrooms, classified according to the number of particles per cubic meter in the space. These standards are numbered ISO 1 (the cleanest air) to ISO 9 (the least clean).
ISO 7 and 8 cleanrooms are the most common. For an ISO 7 cleanroom, for example, all the air in the room will be changed 30 to 60 times per hour to keep the concentration of particles below the allowable levels. (For comparison, the EPA recommends that homes receive a minimum of 0.35 air changes per hour.)
A cleanroom includes sensors that constantly monitor air quality — and possibly other variables like humidity and temperature — and adjusts its systems to keep air quality within the acceptable range. Data regarding these variables can be collected, stored and shared with clients and partners who need it. (For example, a pharmaceutical company may need to know all of the environmental data associated with the manufacture of each batch of vaccines.)
Cleanrooms can be stick-built. They can also be made from prefabricated panels or volumetric modules. Cleanroom manufacturers and their clients often use the word modular to refer to both panelized and modular construction. To distinguish between panelized cleanrooms and volumetric cleanrooms in this article, I’ll refer to prefabricated volumetric cleanrooms as pods and the technique as podular.
What’s the Demand?
COVID-19 has increased awareness and demand for prefabricated cleanrooms. For example, BioNTech (based in Mainz, Germany) co-created the mRNA COVID-19 vaccine with Pfizer and is shipping podular cleanrooms to some African countries for local manufacturing.
“Seeing major companies like BioNTech use podular cleanrooms will really help other pharmaceutical and biotech companies appreciate the advantages of this approach and make it more popular,” says Christophe Mermaz, Co-Founder and Managing Director of C-Cube, which manufactures structurally-standardized cleanroom pods in Vietnam for worldwide shipping.
Increased demand for medical devices such as ventilators, test kits, masks and so on, has also increased cleanroom demand, according to Jill Gagnon, Client Development Manager at Quebec-based Mecart, a custom manufacturer of loadbearing and non-loadbearing cleanroom panels. “There are now more fully-funded start-ups in this sector than pre-pandemic,” she says.
But it’s not only medical-related demand that has increased—semiconductors also need to be made in cleanrooms. According to Adam Rzepka, Senior Vice President of Global Sales and Business Development at Angstrom Technology in Grand Rapids, Michigan, which designs and builds panelized turnkey cleanrooms, the semiconductor industry may have experienced the worst effects of the global supply chain problems. “Most semiconductors are made in China and COVID-19 brought to light the need to onshore this production again in the US,” he says.
Prefab Versus Stick-Built
Advantages offered by prefab units include less site disruption, faster schedules, easier changes and lower costs than stick-built.
Less disruption. Conventional cleanroom construction can suffer many of the same problems as other stick-built projects, such as unreliable costs and schedules. It’s also disruptive, with workers, traffic and equipment coming to the site, making noise and generating dust.
With cleanrooms, these problems aren’t just an irritation. For example, if the cleanroom is a medical lab, construction can be detrimental to patient care. If there are other cleanroom processes taking place nearby, stick-building usually means suspending cleanroom operations for extended periods while lab processes are underway. By contrast, prefabrication keeps the mess in the factory and away from the site.
Speed. When building a stand-alone cleanroom facility from scratch, using pods is faster than stick-building, because the pods are manufactured while the foundations are poured and cured. Mermaz says 95% of podular construction can be handled off-site, leaving only 5% to the final assembly on-site.
When panelized cleanrooms are installed in an existing building, the time spent on-site is also greatly reduced compared to conventional construction. “Cleanroom panels are simply put together on-site. It’s a matter of assembly rather than construction,” Rzepka says. “Stick-built construction requires 30% to 40% more time on-site than using prefabricated panels.”
Flexibility. Once completed, stick-built cleanrooms are difficult and costly to change. “When you want to modify stick-built cleanrooms, people have to stop working in them because pulling out walls and ceilings and cutting materials makes a lot of mess, which is exactly what cleanroom users don’t want,” Mermaz says.
Prefabricated cleanrooms can be more easily changed in the future as clients’ needs change. C-Cube’s pods are designed so that new pods can be connected as a client’s operations grow. And, like shipping containers, they’re sized so they’re transportable to new locations as needed.
In addition, standardized components are interchangeable. For example, “If the owner wants to modify the ceiling in their pod, we can take it out and just plug in a new one,” Mermaz says.
Panels also offer more flexibility than stick-built. “If more space is needed, the current cleanroom can continue to operate, while we assemble the additional space adjacent to the one currently in operation. When the client is ready to combine the spaces, we can come work an evening or weekend to remove the wall in between,” Rzepka explains. “If they’re able to shut the cleanroom down for a short period, we can disassemble the wall, and the panels are re-usable in the expansion.”
Financial benefits. Using panels instead of standard construction inside an existing building can generate financial benefits. “Permanent construction often becomes the property of a landlord,” Gagnon explains. In contrast, “when a client opts for a panelized solution – which can be disassembled and moved to a new location or host building — the entire capital expenditure is fully owned by the purchaser.”
In addition, “unlike traditional, permanent construction, a panelized cleanroom can be classified as equipment.” This can have beneficial tax implications for the client.
More On Cost
Although cleanroom pods are often more expensive than conventionally-built cleanrooms, Mermaz says that C-Cube’s pods aren’t. This is partly because they’re manufactured in Asia, where labor is cheaper than in Europe or North America.
C-Cube also saves costs by using industrialized construction processes and standardized designs. They manufacture pods in only three sizes. The pod sizes cannot be customized (just as the length of a Toyota Camry can’t be customized), but any number of C-Cube’s pods can be put together in various configurations — including stacked atop one another.
Gagnon says it’s difficult to directly compare the costs of a turnkey panelized cleanroom with traditional construction. This is partly because the latter varies by location.
The comparison is also complicated by the fact that conventional construction involves many different trades (electricians, plumbers, carpenters, etc.), whereas “Mecart panels come pre-wired for electricity and pre-plumbed for water, pressurized air, pressurized gases, etc.” She says that once all these factors are taken into consideration, “panelized solutions are much more cost-effective than traditional construction.”
However, she points out that, even when traditional construction does cost less, “few contractors can guarantee the lifespan of drywall inside cleanrooms and they can’t guarantee the air quality inside their cleanrooms.” Mecart guarantees their cleanrooms’ air quality performance and they guarantee the components they manufacture for five years.
Rzepka estimates that, generally, a panelized cleanroom will cost 20% to30% more than conventional construction. However, offsetting that upfront cost is “the speed to completion, which means clients can generate revenue sooner — and the tax savings offered by panelized construction can be significant.” He explains that, at least in the US, a panelized cleanroom can be depreciated for tax purposes within seven years, compared to a conventionally built cleanroom, which depreciates over 39 years.
Of course, a crucial consideration is that clients can take panelized cleanrooms to new premises, just as they can with their computers, desks, chairs and any other pieces of equipment. “Customers routinely relocate their cleanrooms to different buildings,” Rzepka says. “Also, if a cleanroom is no longer needed, it can be sold without the client having to relocate to new premises. These options are simply not available for stick-built cleanrooms.”
Panels or Pods?
Whether it makes sense to use panels or pods depends on the client’s needs.
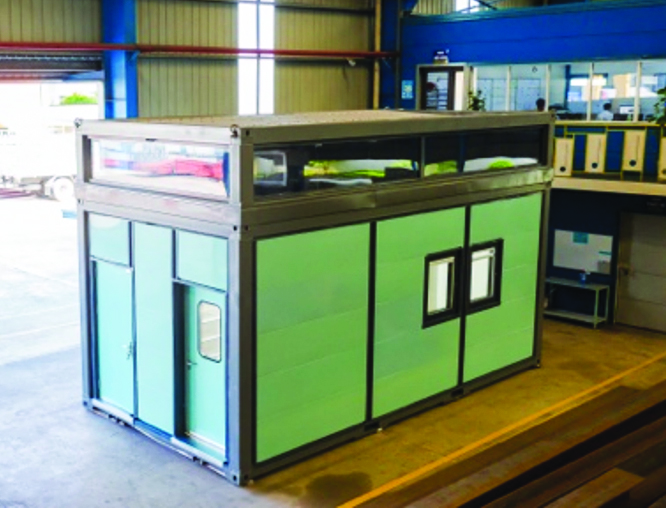
Inside an existing building. Panelized cleanrooms are rarely installed as outdoor structures because they’re not designed to be watertight. Rather, they’re intended for use inside a host building — such as a warehouse. Completed panelized cleanrooms are like “buildings within a building” as Rzepka puts it.

If a client already owns or rents an existing building and wants to add a cleanroom inside, panels are likely to make more sense than pods — not least because panels are smaller parts and easier to get inside an existing building.
Angstrom’s systems involve structural framing, plus panels. Typically, they don’t rely on the host building’s wall framing. “Walkable ceilings are either suspended from the host building’s roof, or from the superstructure that we provide as a part of our package,” Rzepka explains.
Cleanroom ceilings must be walkable so maintenance personnel can work on the equipment when needed.

Mecart’s load-bearing panel system doesn’t require framing and usually, the walkable ceilings are supported by the panels, rather than suspended from the host building’s roof. “We anchor a track system in the floor. Our structural wall panels slot into the track, and the walls support the walkable ceiling and ductwork. The walkable ceiling supports the HVAC system,” Gagnon says.
Stand-alone, watertight cleanrooms. If a client needs a watertight, stand-alone cleanroom, then pods are likely to be the better fit. Each C-Cube pod is completely self-contained, with its own HVAC system, electricity, automation, fire safety, and utilities, and is fully insulated and watertight.
Manufacturing Issues
It’s unlikely that an off-site housing manufacturer would build cleanrooms in the same facility as it builds housing, Mermaz says. “In residential modular construction, manufacturers are often doing the same as on-site construction —they’re just doing it under a roof,” he says.
By contrast, manufacturing C-Cube’s pods is more similar to car manufacturing. “The cleanroom components — the framing, the HVAC, the cladding and so on — are all manufactured by partners, according to our designs. We put all the parts together in our clean facility. We don’t do any metalworking, welding, or painting there.”
To begin making cleanrooms, an off-site manufacturer would also need access to experts in cGMP [current Good Manufacturing Practices] in their customers’ industries. “They need someone who understands the processes used in the industry they serve,” says Mermanz. For example, one of C-Cube’s founders, Fabrice Dumont Dayot, is CEO of SP Groups, a pharmaceutical and life sciences engineering company based in Switzerland. “He understands the processes in those industries, which is essential to designing cleanrooms that will meet our customers’ needs.”
Mermaz mentions a challenge for volumetric modular housing that’s lessened for podular cleanrooms, though: “Transporting modules is expensive.”
In residential construction, transportation costs can make it hard for the modular company to compete. However, he says that biotech facilities cost so much—up to $8,700 per square meter—that transportation costs are low compared to the cost of the facility. “You can transport life sciences pods worldwide and still be competitive on cost,” says Mermanz.
Zena Ryder is a freelance writer who writes about construction for businesses, magazines, and websites. Find her at zenafreelancewriter.com