These interesting products and systems hold potential benefits for the offsite construction industry.
This magazine’s definition of offsite construction includes just about any type of factory-based process that can make for a more efficient building process. With that in mind, here are five new, or recently introduced, products we are watching.
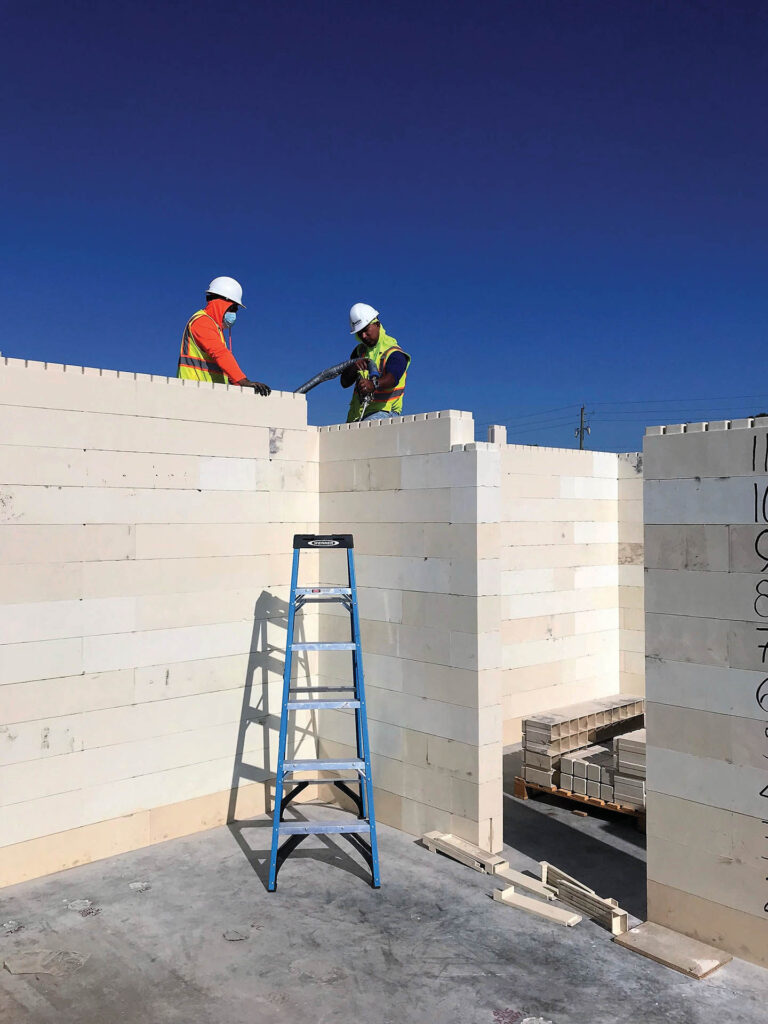
Photo courtesy of RENCO USA
CMUs Simplified
When it comes to engineered building systems, the LEGO analogy has certainly been overused. However, the interlocking CMU replacements made by Miami, Fla.-based RENCO USA actually fit the bill.
According to CEO Kenneth Smuts, buildings made from the blocks can stand up to hurricane-strength winds, and the company has already used them to build a 100-unit multifamily project in Palm Springs, Florida. The RENCO USA structural building system, known as MFCR, won the international award at the BLT Built Design Awards in Lucerne, Switzerland in 2023.
“We came up with a [block] which is made like you’re making waffles on a Sunday morning,” Smuts says. “You take the wet ingredients and mix them together. In our case, it’s unsaturated polyester resin. To that, we add wet calcite, which [comes from] limestone dust, and fiberglass, which is there for tensile and flexural strength.”
“Then you mix that all together and there’s a catalyst that’s added to the mix,” Smuts explains. “It goes from a batter-like consistency to a dough. That takes a few hours. The next day, it goes out to the press-room floor. We mold different shapes. For example, we have a mold that looks like an adult-sized LEGO, the size of a concrete masonry unit, which is made out of carbon steel with some admixtures in it. We use that to press the ‘dough’.”
Using these blocks could save large amounts of time and money and could allow builders to hire more unskilled labor, Smuts says. This is because carpenters, rod setters and cement masons are not required. Constructing a building for the Palm Springs project took a crew of 11 workers eight weeks. A similar building made of reinforced concrete block and plank would have taken 40-50 workers 15 weeks.
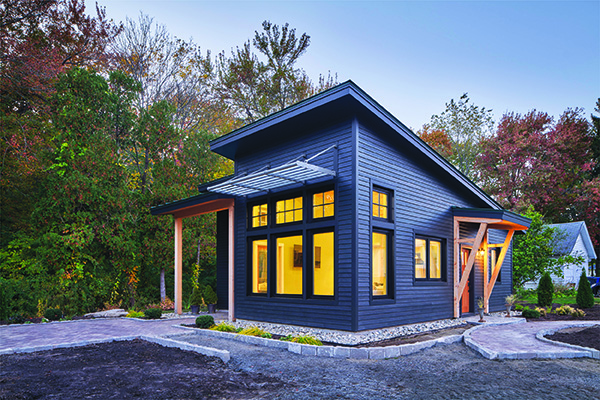
CertainTeed panels were used to build this house in Mystic, Connecticut.
Photo courtesy of Mark Bealer, Studio 66, LLC
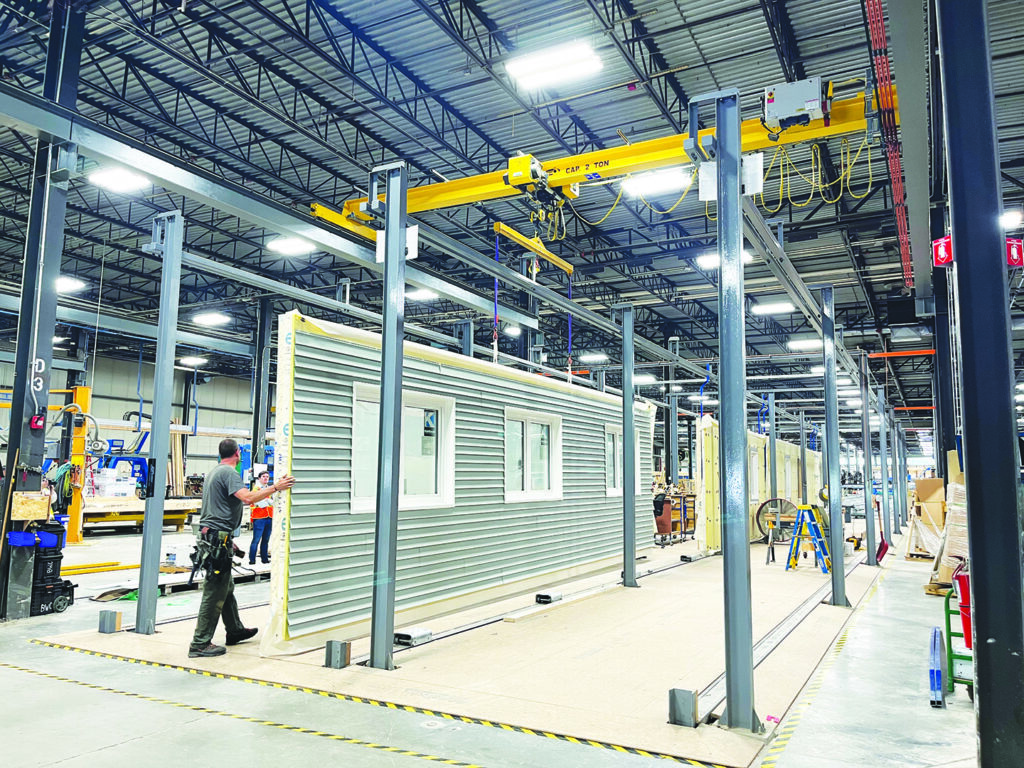
Photo courtesy of CertainTeed
An Evolution in Panels
According to CertainTeed, their ONE PRECISION ASSEMBLIES system won the Offsite Construction Award for Innovative Product or Service from the National Association of Home Builders in October 2023.
The product is “a building-envelope system that includes walls, floors and roof panels, as well as ceiling panels, where the majority of the construction of the panels is happening in a factory setting,” explains Dennis Michaud, the company’s Managing Director of Offsite Solutions.
The finished panels include windows, insulation and siding. Workers complete the plumbing, finish carpentry and electrical work on-site. The process can reduce a 9-to-14-month build time to a five-month build time, according to Michaud.
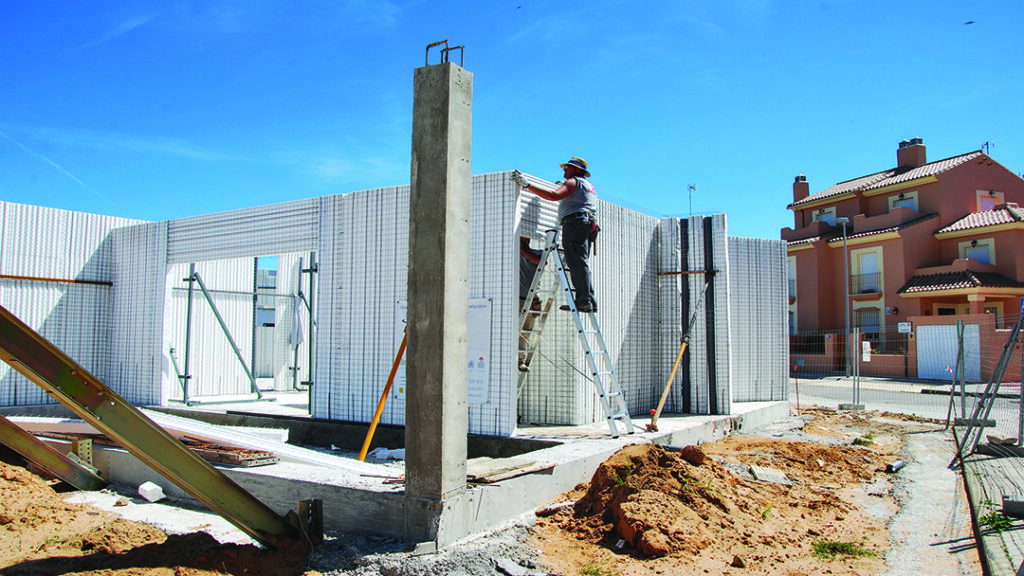
Photo courtesy of Emmedue
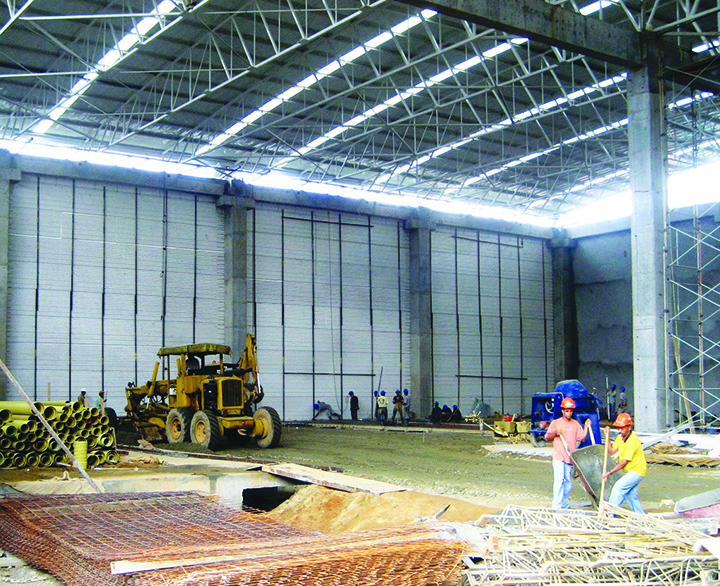
Photo courtesy of Emmedue
Against the Wind
We featured this product in a past issue, but thought it interesting enough to mention again.
Vero Building Systems in Kissimmee, Florida was launched in 2018. Their product, Vero Panels, meets the strictest Florida wind requirements, according to CEO and Co-Founder Annette Rubin.
Each panel consists of a polystyrene core, cut to custom widths, with steel mesh attached on both sides. The wire mesh extends 4 in. beyond the end of the panel, so that it can be connected to an adjacent panel. Panels are secured to the foundation with 2.4 mm rebar.
Once in place, mortar is sprayed onto the face of the panels. “Project needs vary,” says Rubin, “but 4000-psi mortar will give the structural integrity and storm resistance necessary for most structures.”
She recommends building one level at a time, so that mortar on each level can dry before the next level of panels is put in place. Drying takes 12 to 24 hours.
Buildings constructed with the panels have a Category 5 hurricane rating. “Most of Florida requires a Category 3 rating; only Miami Dade requires a Category 5 rating,” Rubin says.
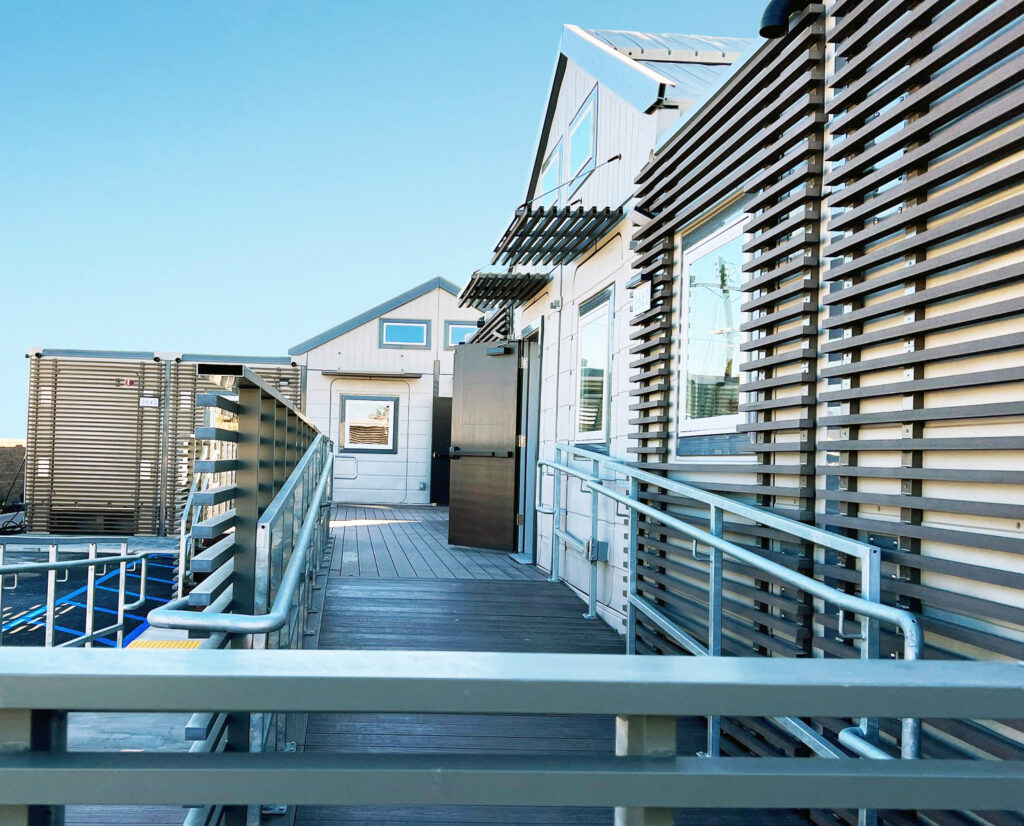
Photo courtesy of LifeArk
Plastic Homeless Housing
The idea for LifeArk modular components came about when architect Charles Wee, the company’s principal designer, visited the Amazon rainforest. After seeing indigenous people’s homes flooded for as long as nine months per year, he decided to design a plastic-based building system that could float during a flood
Paul Cho, CFO of LifeArk in Duarte, California, asked Wee to collaborate on building housing for the homeless in California using this technology. However, the goal was to reduce construction costs rather than resist floods.
“We initially create a hollow, high-density polyethylene shell, using the rotational molding process,” Cho says. “That hollow plastic part gets filled with high-density polyurethane foam,” a rigid foam that provides structural integrity and serves as an insulating material. This material is used for floors, walls and roofs.
“The design is a lot like the YETI cooler,” Cho says. “We know how highly insulated those coolers are. It’s the same concept. The insulation value is tremendous.” He estimates it at R-40.
Cho showed Offsite Builder a video of the assembly process. The floor is elevated above the ground and stands on legs. The wall pieces are slid into the columns and slide down to the floor. Then the roof is put on. The modular rooms are then connected to each other. A forklift is used to assemble the pieces.
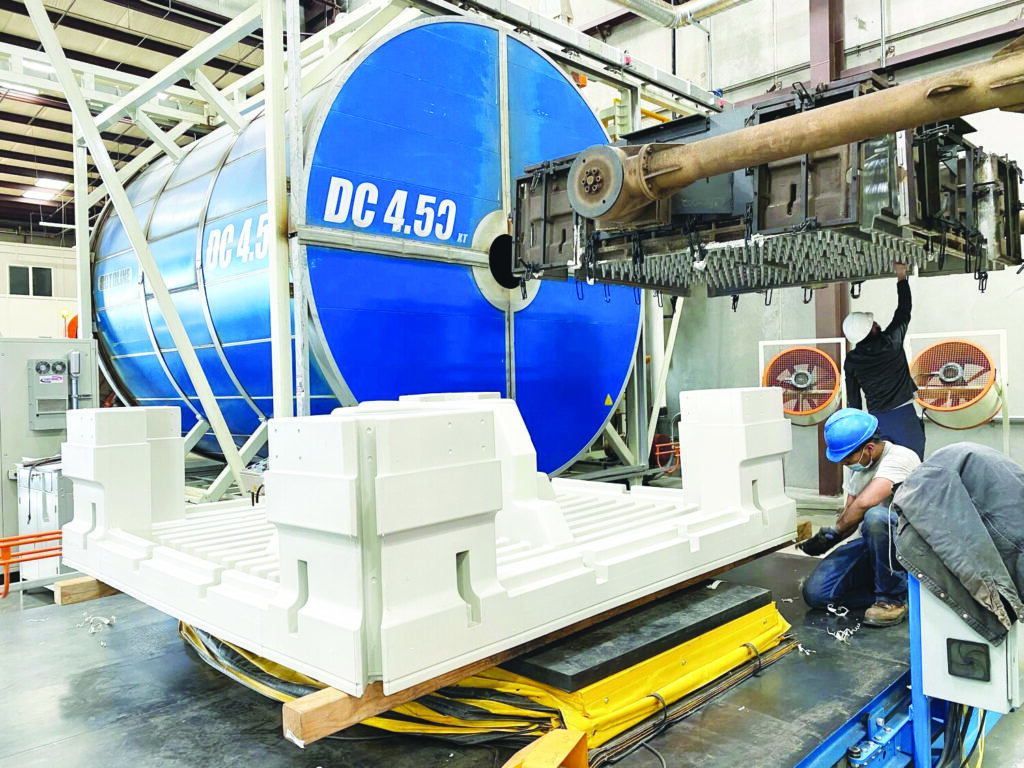
Photo courtesy of LifeArk
“We went through all of the certification process and the permitting process in California to become a factory-built housing program,” Cho explains. “California is [one of the] most rigorous jurisdictions in the world.”
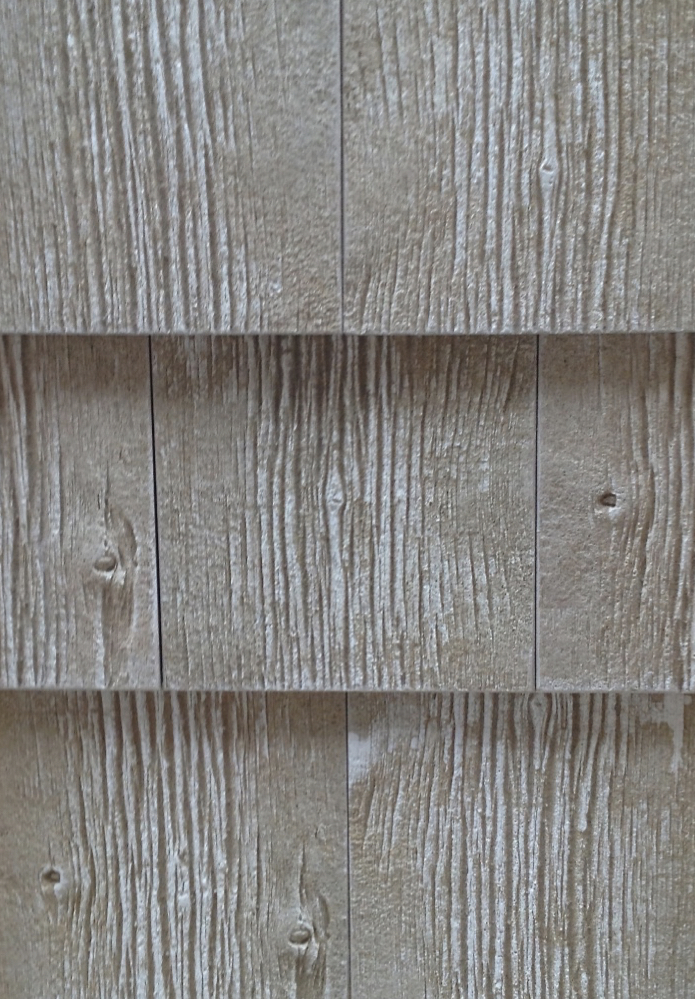
Photos courtesy of MOXY OIDPhoto courtesy of MOXY OID
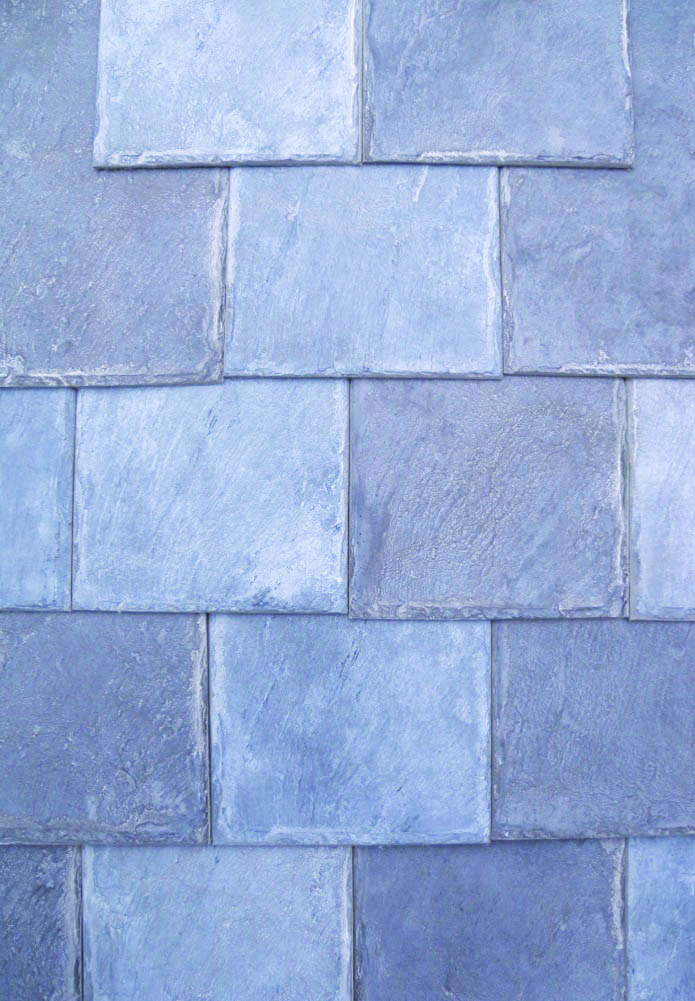
Ceramic-Like Cladding
While not limited to offsite construction applications, we think that CERLOS technology from Las Vegas, Nevada-based MOXY OID has enough potential to warrant featuring it here.
The company currently is negotiating with potential customers about commercially licensing this technology, which transforms wood fibers into a soft stone through mineralization. The company’s website features a wide range of product geometries that can be created with this proprietary process.
The three primary ingredients are plant fiber, a pH-neutral polyphosphate and magnesium oxide, says Robert Bedard, the company’s CEO. “It’s a mineralization in which the commodities bond and become an end product.”
The finished product is resistant to fire, insects, mold and moisture, according to the MOXY OID website. “Because of the mineralization, there are no fibers. It behaves like a ceramic. It would be a cold ceramic,” Bedard says.
“We are in negotiations with the largest panel producers globally and the largest roofing companies globally,” he adds. “We will license our technology to [them] and they will commercialize the products.” He says their long-term plan is to manufacture their own siding products.
Kat Friedrich writes about energy, engineering, physics and technology. She is a graduate of the University of Wisconsin-Madison College of Engineering and is the editor in chief of Solar Today.