Sweden has lessons to teach the US construction industry, but not all that country’s practices will work here
- According to Helena Lidelöw Sweden originally learned the concept of offsite construction from the US, but unlike the US, they embraced it
- The country’s high percentage of prefabricated buildings is thanks to a nationwide ecosystem that supports it.
- Sweden’s consistent code and contract requirements have helped create an environment conducive to factory building.
- Lidelöw believes that vertically integrated operations will be a key to expanding offsite’s US market share.
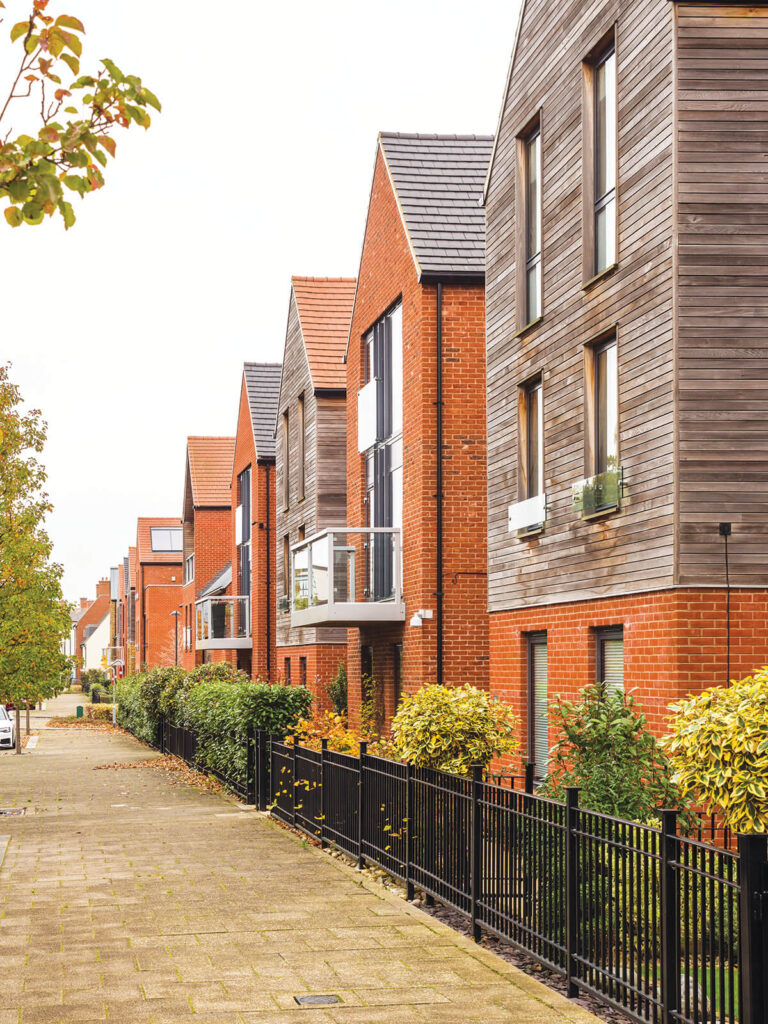
When it comes to industrialized construction, Sweden is often held up as a model the US should emulate. After all, it’s the world leader in prefabricated construction, with 84% of its detached dwellings created in whole, or in part, in factories. (In the US, offsite construction is only 3% of the market according to NAHB.)
Many people in the US look to Sweden’s experience with industrialized construction for an answer to our housing shortage. But while that experience has lessons to teach us, simply copying Sweden’s building methods won’t work here. That’s because there’s more to building than the construction process. There are also cultural differences, consumer expectations and government regulations.
The Borrowers
Sweden didn’t invent factory building. “We actually borrowed [the concept of] prefabrication from the United States in the 1920s,” says Helena Lidelöw, a former academic with a Ph.D. in timber engineering who is also a leader in the modular industry with 20 years of research and development experience for Sweden’s premier modular manufacturer Lindbäcks Bygg. “We had people watch what you were doing and bring it back home.”
The impetus was a Swedish housing crisis that lasted 80 years, from about 1890 to 1970. The US was a good model because companies here began offering kit houses, catalog homes and mail-order houses in the late 19th century, according to the National Park Service.
However, prefab didn’t really take off in Sweden until the post-World War II recovery period. That period saw massive government support through The Million Homes Programme (begun in the mid-1960s), during which Sweden factory-built a million homes over the course of a decade. It was quite a feat for a country of what was then only five million people.
Sweden’s love affair with prefab has continued to the present day for reasons that include a labor shortage, consistent government regulations, cultural acceptance and education, links between the banking and construction industries and even the weather. (Factory building makes sense in a country with short summers and long, dark winters.)
Drivers and Support
Sustainability has also been a driver. While sustainability is important to many homebuyers in the US, it doesn’t drive the industrialized construction industry the way it does in Sweden, where it’s the number one priority, Lidelöw says.
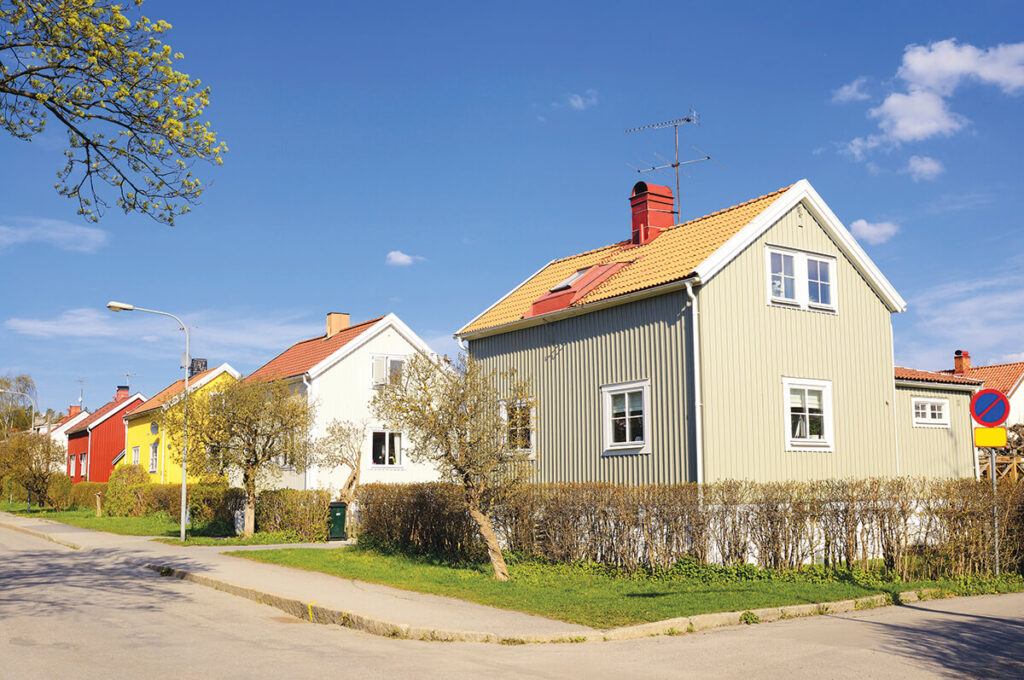
Scandinavian housing, summer day with blue sky
It began with the oil crisis of the 1970s, when the country began converting everything to electric. Then “in the ’80s and ’90s, we began wondering if the forest would be able to sustain us. We were one of the first people to accept that there was a climate crisis. It’s imprinted on [Swedish] people’s minds that they need to save on energy, save resources and take care of Mother Earth.”
Sustainability is built into the Swedish construction industry’s DNA both through general education and its building code. “In the Nordic countries’ building code, we’re required to deliver a carbon footprint calculation for every project,” Lidelöw says. The way Nordic builders reach the requirements is up to them. “The code system is built on functional requirements; it’s not material specific. Nordic builders are told to comply and how they solve for it is up to them. In the US, it’s prescriptive.”
For example, she says, “The Euro code might say that we must have a fire rating of 90 minutes. I can show that happens by simulation or calculation. There’s nowhere in the Euro code that says I can’t build with carbon fiber, for example, as long as I get to the required rating.” In the US by contrast, you “have to have your staples so many inches on center. Why? That information can be in a handbook; it doesn’t have to be in the code.” She believes this kind of prescriptive effort creates stumbling blocks to production.
A countrywide, performance-based code makes it easier for factories to build homes because they don’t have to change specs for every locality and because they can choose whatever structural system makes the most sense for their operation, as long as the final result passes a code check.
Sweden’s building code also helped to develop a kind of ecosystem within the industry, with everyone pulling together. “It’s a mature community. The ecosystem has consolidated into something that’s more or less an organism,” she says. The people who make up that ecosystem can self-regulate and learn from each other.
Another advantage she cites is Swedish contract law. In the US “there is [nothing] pre-approved or pre-agreed upon.” Every contract is different. However, in Sweden “when you write a contract you can refer to nationally recognized rules that everyone is taught in school.” This translates into faster turnaround times on contracts.
Consumer Culture
The post-war years gave Sweden an edge not only in perfecting production but also in creating a culture of acceptance. In the US, many in the modular industry still complain about the negative stereotype that equates industrialized construction with cheaply produced HUD homes. Sweden just doesn’t have that negative stereotype to overcome.
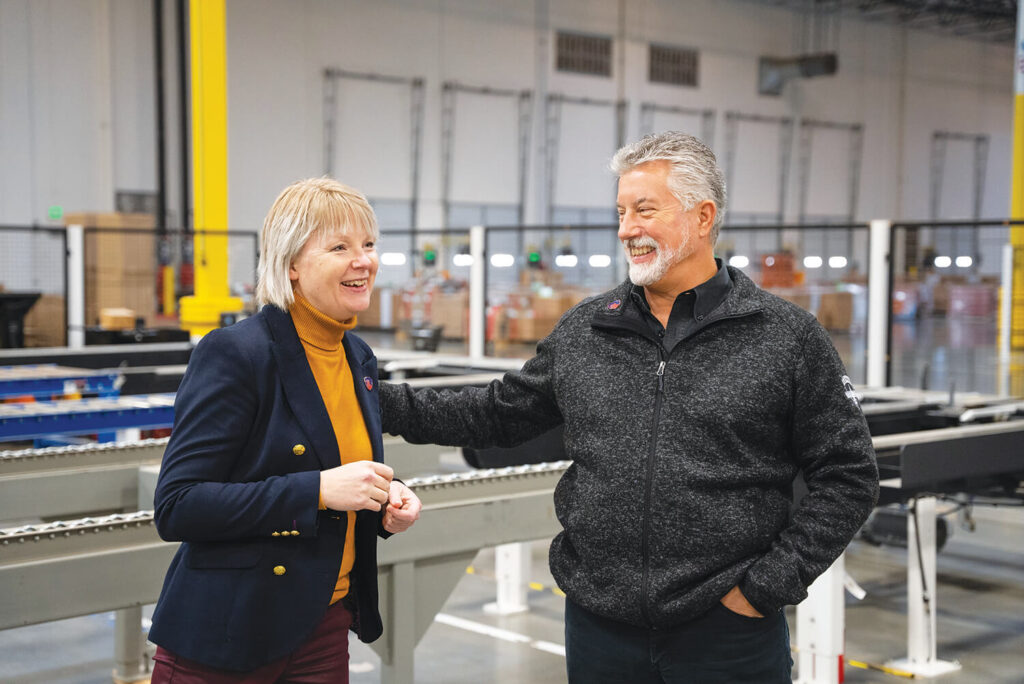
Helena Lidelow, CTO, and Glenn Ford VP of West Coast Operations at VBC’s Tracy California plant.
Lidelöw says this is thanks in large part to the legacy left by The Million Homes Programme. “We’re living on that heritage and Sweden’s culture is really set up for [prefab construction]. We know that there’s a housing factory that gives jobs to people and we bring our kids to see how it’s done,” she says. “It’s not strange to make a house in a factory or see it delivered on a truck.”
Plus, native Swedes, who account for 3/4 of the 10 million population, share similar values, while the US is home to nearly 330 million people from hundreds of distinct ethnic groups. “The struggles of communicating to the public are much larger in the US.”
Production Stumbling Blocks
What gets built in US factories is also different from what gets built in Swedish factories. Lidelöw has found that “when people in the US say ‘panelized,’ what they have in mind is a frame with sheathing on it.” The panel might have electrical wiring, but usually doesn’t.
In Sweden, “panelized” means “a frame that’s fully insulated. It has both the electrical and the potential plumbing there. It has sheathing on the outside; the windows are installed. It could potentially also be faced (sided). For me, the value-add is higher in Sweden.”
The same goes for modular, she says, although the American version of modular is closer to what’s offered in Sweden. Some of this goes back to having a more mature building ecosystem. Each level of the supply chain is attuned to the needs of Sweden’s offsite industry
First-Hand Comparison
The importance of the supply chain was recently driven home to Lidelöw. She is now the chief technical officer at Philadelphia-based Volumetric Building Companies (VBC) and is taking the lead on its new Tracy, California factory, which once belonged to now-defunct Katerra and which VBC is switching over from panel to module manufacturing.
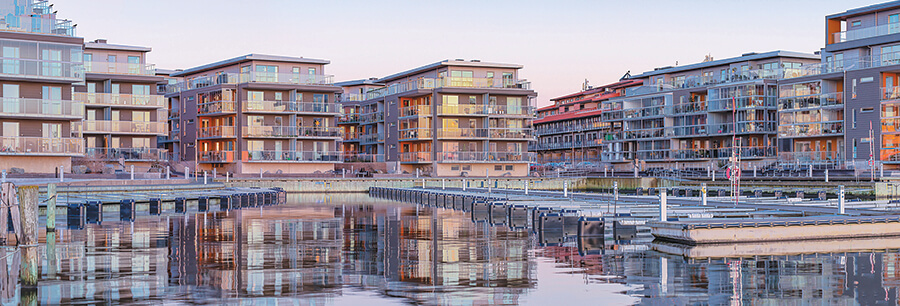
She is finding some things more difficult to source here. “It’s a lot of little things,” she says. “For instance, I’m used to working with a sheathing manufacturer who can give me any width of sheathing,” while US suppliers only make 4 ft. x 8 ft. sheets.
She also has difficulty finding people in the US who can design or operate the automated equipment needed for the factory. She says she was happy to “scoop up” people who had worked for Katerra.
The other difference in the US market has to do with government regulations. Sweden has plenty of regulations, and Lidelöw has nothing against them, acknowledging that there have to be rules to ensure quality. What she has difficulty with is the variety of state and local codes.
With 50 individual states, “the state has an opinion, the city has an opinion and at every level there’s another opinion. If you’re moving between cities when you’re an offsite builder, you need to set up a production system that can handle all the different building codes. Or, you choose to go with the most difficult and restrictive one and then you add costs.”
What’s Transferrable?
A lot of the efficiencies developed in Sweden can be implemented in the US, but it will take time and a certain level of cooperation among all stakeholders.
And scaling the industry will likely require more vertically-integrated operations.
That’s the path for VBC. The former Katerra plant will not only give the company West Coast access, but will also give it the ability to produce windows, cabinets, countertops, floor systems, wall panels and roof trusses.
Lidelöw is fully cognizant of Katerra’s trajectory but believes it served a useful purpose. It paved the way for “the discussions that are happening right now.” Although the execution was flawed, she agrees with Katerra’s assumption that a more vertically-integrated manufacturing and supply chain will be a key to growing offsite’s market share.
Katerra’s ultimate failure came from trying to do too many things at once, which caused their operations to lose focus. “But kudos to them for taking all this on at scale,” she says. “I’m fortunate enough to have former Katerra employees here. What they learned during that ‘upspeed’ period is valuable to us now. Those employees carry the tribal knowledge that the industry really needs.”
She does note that there’s something Sweden could glean from the American market. “One thing that grabs me is this attitude of ‘It can be done.’ The US is much more open to innovation than I’m used to. You celebrate individuals, you celebrate ideas, you celebrate success. That’s refreshing when you work in an area in which there can be a real struggle. Americans keep up the energy and we can learn from that.”