For homebuilders, precast concrete offers speed of installation, durability and design flexibility, especially with repetitive designs.
- Precast concrete components are designed and manufactured off-site in a controlled environment, ensuring a high-quality product.
- Components can be installed considerably faster than the more commonly used concrete block or poured-in-place concrete.
- However, precast concrete doesn’t make sense, cost-wise, for a complex design such as a one-of-a-kind, custom home. It’s more economical when used with repetitive designs.
Precast concrete components are regularly used in commercial construction, both as a structural system and an exterior finish. The picture is somewhat different in residential, where if homebuilders use precast, it’s primarily for foundations and exterior walls.
But as precast manufacturers spread the word about its advantages —durability, resilience, speed of installation and design flexibility — the housing community is starting to take notice.
For instance, builder/developer Dan Bamdas of Bamdas Development, Millburn, N.J., has been using a precast foundation and wall system by Superior Walls, New Holland, Pa., for 10 years, and says he’ll never go back to concrete block or any other foundation system.
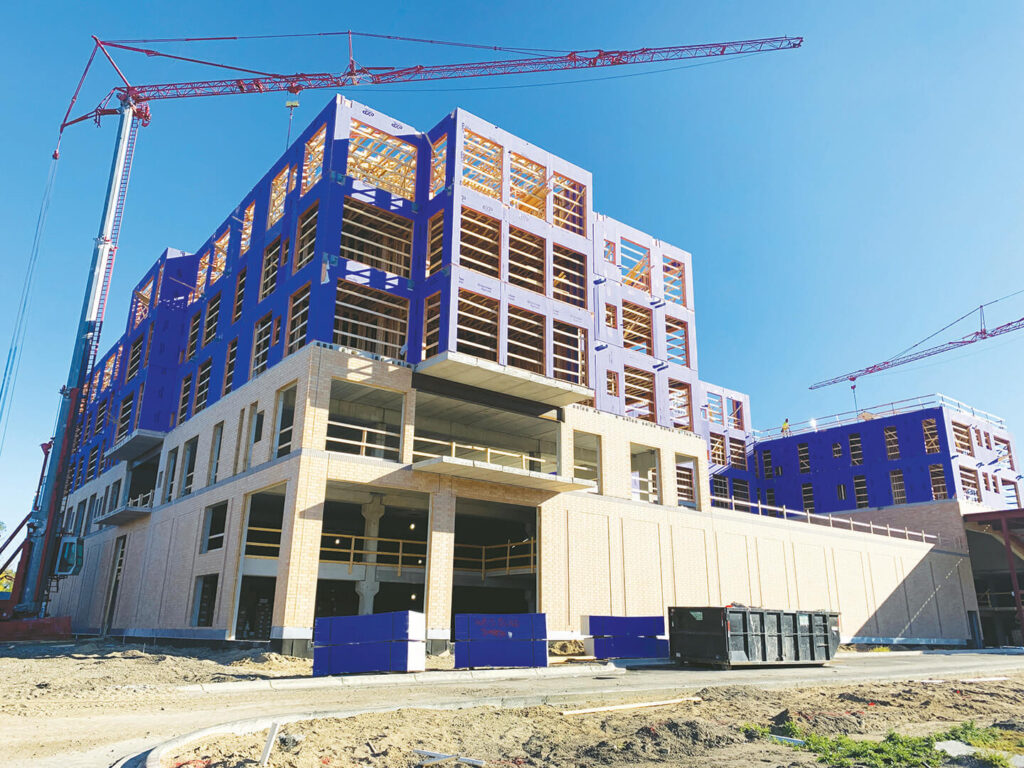
Photo Credit: Molin Concrete Products
The insulated foundation walls sit on gravel footings, which do a good job of draining rainwater away from the house. The entire basement foundation can be set in a day, compared to a week of concrete masons setting block.
“Time is money, so if you’re able to shorten your cycles by using a prefabricated, or panelized, system, it’s much easier to rationalize a slight premium in cost,” says Bamdas.
In situations where the house size and lot size are limited, Bamdas uses concrete floor planks to build basements underneath garages. The bonus living space maximizes usable square footage and has been so popular with customers that he has sold it in seven homes to date.
The floor-plank system, known as Prespan, is made by Northeast Precast in Millville, N.J. Prespan allows for extra space to be constructed under the garage during the construction stage of a project. The system eliminates the need for interior structural supports and leaves a completely open space with no columns or load-bearing walls.
At press time, builder/developer Rob Howard of Howard Building Science in Granite Falls, N.C., was planning to build his first home with a precast foundation by either Superior Walls or Ideal Building Systems, Durham, N.C. The home will be modular, possibly with additional precast elements.
Howard, who used to be a Home Energy Rating System (HERS) rater, has always been impressed with the energy efficiency of the precast foundation system. “It has good R values and insulation is already built in at the factory. You can have additional insulation installed in the wall cavity if you choose before the facade is finished,” he says.
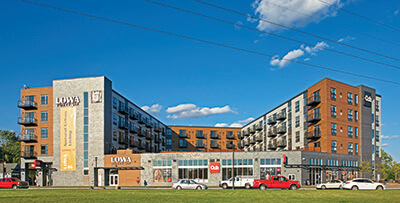
Howard prefers precast to poured concrete and concrete masonry units (CMUs), because while both systems cost less per square foot than concrete panels, “If you want to get the same level of [thermal] performance from them as you would from a precast concrete foundation, by the time you add rigid insulation on the inside and do the additional waterproofing on the outside you’ll be making a similar investment.” In other words, the savings are minimal.
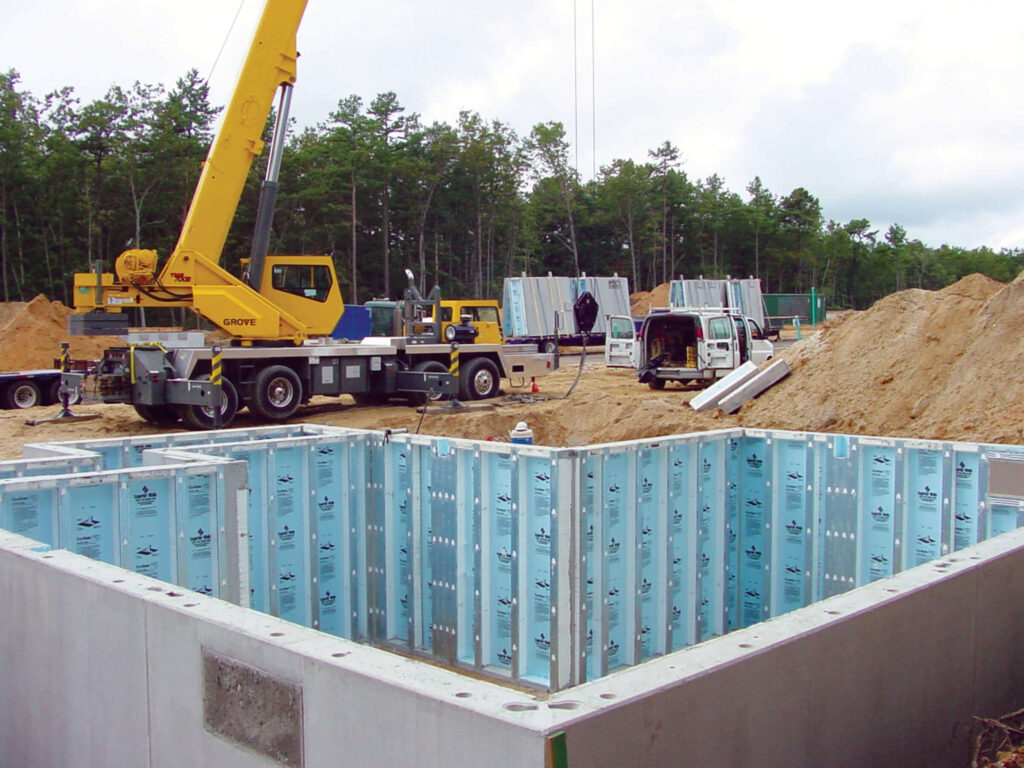
In his mind, the biggest advantage of precast is that it’s a turnkey set solution. That’s something builders should look for when determining if precast is a good fit for their operation. Precast manufacturers, Howard says, “are not just selling you a product and leaving you to figure out who’s going to set it.” Many modular builders, he says,use precast foundations for this reason: “As a builder, if the manufacturer is taking responsibility for the full installation, I feel a lot more confident that they’re going to get it right.”
Cost Considerations
In a precast project, simple designs help keep costs in check, says Bob Clauson, Vice President of Sales and Marketing for Molin Concrete Products in Lino Lakes, Minn.
“The simplicity of design and repetition go hand in hand,” says Clauson. “They are both design features intended to value engineer a project and keep costs down.”
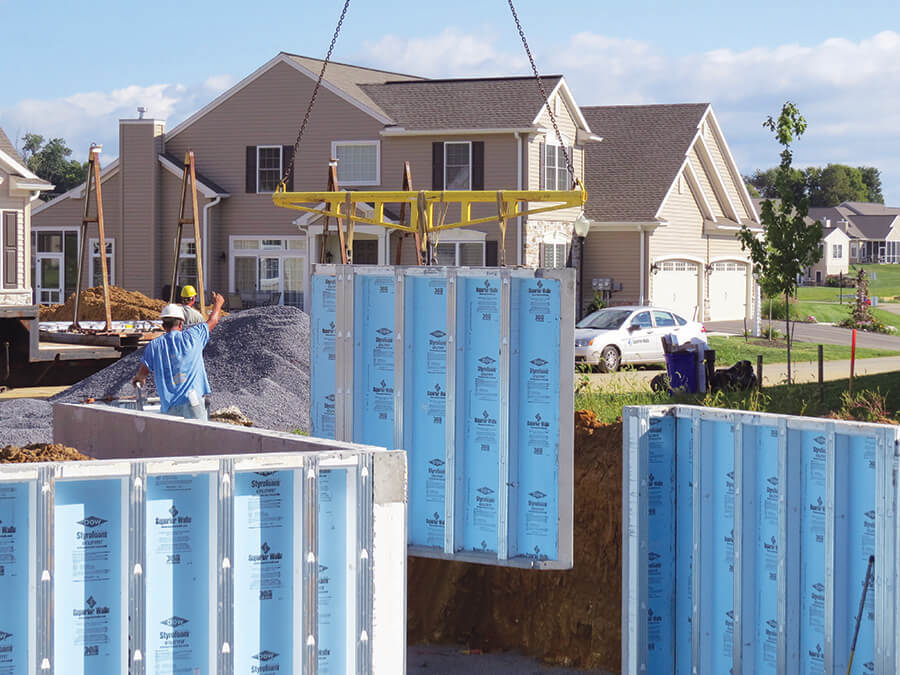
Clauson views precast as a viable option for multifamily builders and developers. A big percentage of his company’s sales and revenue is generated by multifamily buildings that include mixed-use, senior housing, assisted living and market-rate rental apartments. They are typically podium buildings with underground parking, retail or office space at the street level and apartments above.
Precast concrete components used in these projects include hollow core plank, columns and wall panels, as well as prestressed concrete beams. Prestressed concrete is substantially compressed during production, giving it strength against tensile (stretching) forces.
“Precast is more economical when it’s repetitious — when you can make the same pieces over and over again,” points out Clauson.
Another benefit, at least for northern builders, is the ability of precasters to keep meeting their production goals despite winter weather. During the winter months, Molin manufactures its products in a Precast/Prestressed Concrete Institute (PCI) controlled environment, which ensures quality.
“Our field crews set our products at -11 degrees Fahrenheit,” Clauson says. “We do not slow down or need on-site heating that would be needed with other products such as post-tensioned systems or CMUs.”
Peter Hildebrand, Sales Consultant for Coreslab Structures in Dundas, Ontario, Canada, says certain buildings are going to gain more cost and time advantages than others by using precast. With simple designs such as square boxes and rectangles, precast saves a lot of time. “If it’s a complicated building that takes a lot of site work and installation of the precast components, it might make more sense [to stick build all or part of the structure],” says Hildebrand.
He suspects that designers may not be aware of the potential advantages of precast, or are unsure of how to design with it. For this reason, Coreslab, like other precasters, strives for collaboration with all partners early in the process.
“We always try to educate designers and engineers about creating living spaces [with precast components],” Hildebrand says. “The earlier we can start working with them, the higher the success rate.”
Precasters can create various colors, details and patterns with façade panels, making a building look like brick, stone and other natural elements that would take on-site crews many hours to complete. The panels are finished and ready to install when delivered, a key factor in cutting down construction time. That’s critical for building owners, says Hildebrand.
“The speed at which [components] can be installed is very compelling for a lot of building owners, who can have a project completed weeks or months earlier than originally projected,” he says. “Think about all the extra revenue to be gained there.”
Susan Bady is a freelance writer based in Chicago, Ill., who focuses on residential and commercial design and construction topics including sustainability and building technology.
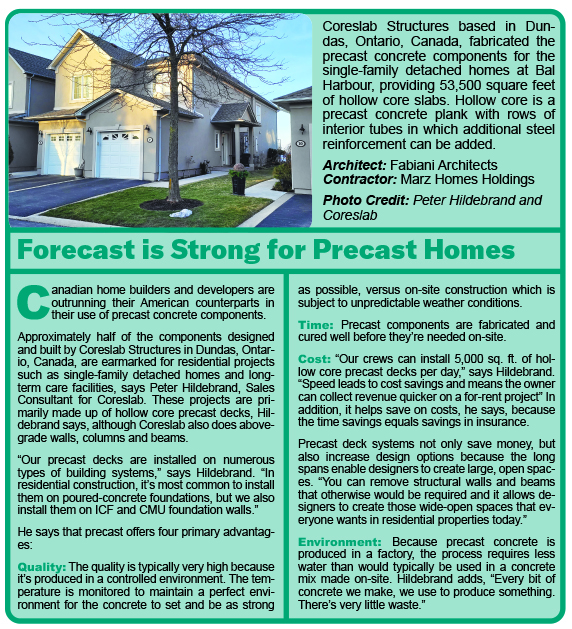