Island homes and modular construction are a perfect match. However, scheduling and coordination are key to not sinking.
- Building on an island is a highly-coordinated dance.
- The need to barge modules across the water complicates scheduling. It can also lead to weather delays and other logistical headaches.
- The fact that many islands are tourist destinations can cause delays during the busy summer months.
- Despite these difficulties, modular has real advantages for an island build. A modular home can be finished for less, thanks to the high cost of shipping building materials for a site-built home.
It sounds simple enough. Build a volumetric modular product, load it on a truck, then put it on a barge and ship it to an island. Highway travel, ocean travel – same difference, right?
Not quite. The process of building modular homes on an island does pose additional risks and challenges. Island modular builders assert, however, that the lower cost of building and delivering modular compared to the costs of an island on-site, stick-built home outweigh the difficulties.

Westchester Modular sends drivers and trucks as needed with the modular boxes. At the end of the set, they take the trailers off the island on the ferry. The crane is from Baxter Crane out of Hyannis, Mass. and is permanently stored on the island
The Elephant in the Water
The most obvious difference, and the one that presents the greatest challenge, is barge travel. Mainly, the issue revolves around logistics, according to Jason Webster, Co-President and Co-Owner (with his brother Adam) of Huntington Homes in Montpelier, Vermont. The company will build ten homes in 2022 on the islands of Martha’s Vineyard and Nantucket, which are off the coast of Cape Cod, Massachusetts.
Each island has its different requirements. “Martha’s Vineyard will accept deliveries of modules year-round, while Nantucket only allows deliveries from September 15th to June 1st,” he says. “For most of these [Northeastern] islands, the barges come into the downtown areas. Nantucket has rules around not putting tourists and modules on the ferry dock at the same time,” he says. The other major barge challenge is scheduling. Huntington Homes was sharing travel coordination with their clients for a few years, but, says Webster, “we eventually learned
it was easier to coordinate the entirety of it ourselves because it’s typical that some aspect of the delivery will go sideways.”
Sideways tends to be about weather—barge companies prefer to stay in port when it’s really bad. “We might have a barge scheduled for six months in advance, but the night before, we’ll get a call from the barge company telling us they’re canceling because of the weather,” Webster says. Since Huntington Homes schedules in-house, “we can start coordinating and rescheduling all the other aspects necessary for delivery ourselves instead of relying on other people to do that for us.” Webster isn’t quite sure that method saves them money. But it likely saves them headaches.
Westchester Modular in Wingdale, New York, does it differently. The company builds high-end luxury modules for Squash Meadow Construction, a full-service design-build company based on Martha’s Vineyard. “We deliver about a house a month via barge,” says John Colucci, Westchester Modular’s Vice President of Sales and Marketing.
Colucci and Squash Meadow Owner and President Bill Potter work out travel this way: Using its own trucks, Westchester Modular transports units from its facility to the New Bedford, Mass., barge dock to send modules over to Martha’s Vineyard. “Bill does the booking for the barge and pays them directly. He controls that since he’s local and we’re not.” Potter says a barge fits four modules and costs about $15,000 regardless of the number of modules it ships over. “But there is also a smaller-size barge,” he says. “And sometimes a barge may cost more because we have to land on the beach. There are several factors [that go into the cost of the barge].”
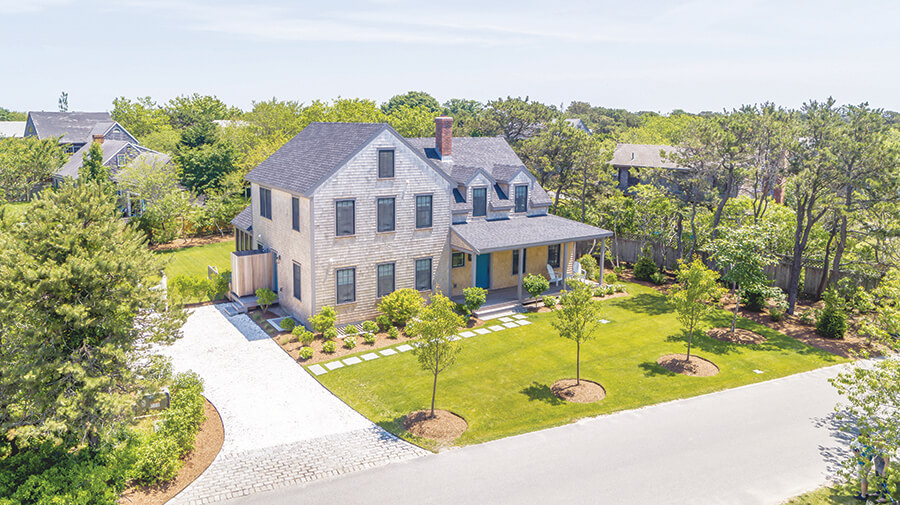
Huntington Homes manufactures single-family, workforce and employee housing, especially on Nantucket. This single-family home is 2,500 square feet and is made up of five modules. The cedar exterior had to be approved by the Nantucket Historic District Commission (HDC) to fit in with the island vernacular.
Regardless of who does the scheduling, modular companies have to work closely with the client (whether it’s a developer, general contractor (GC), or homeowner) on the other end when it comes to scheduling. “You have to book a barge at least two to three months in advance,” says Colucci. “Bill and I do a dramatic amount of coordinating. We need to take into account how long it will take to get a building permit and foundation in the ground so the units can be accepted on time. You don’t want to have a barge booked then not be able to set the modules.”
Westchester Modular also delivers to Peaks Island, a small island off the coast of Maine. They have to use “a landing craft vessel,” which is much smaller than the commercial barges traveling to and from Martha’s Vineyard and Nantucket. It carries only one module at a time and they have to make many more trips over several days because of the tide schedule.
On those smaller islands, in particular, Colucci says it’s important to check road conditions – like whether they’re wide enough, or if there will be electrical wires in the way. And with some islands, you have to time your delivery to coincide with the tide. “We delivered to Fishers Island off the coast of Connecticut, but we had to time the tides because if we got to the dock when it was too low, it would be difficult to unload.”
Craig Lan, president of Signature Building Systems (SBS) in Moosic, Pennsylvania, which manufactures everything from single-family custom homes to student housing, apartments and other commercial buildings on islands, has met trouble at a dock’s holding yard. “If we deliver a 14-module building, there’s only so much space in the holding yard. That could be a bottleneck: keeping you from transporting from a manufacturing facility to a holding yard and then from a holding yard to the site.”
The likelihood of a bottleneck will vary with the season. Islands are often vacation spots, so ferries and barges get busiest right before Memorial Day and stay busy through Labor Day.
There are also worker transportation costs. You have to keep in mind that in all likelihood you’ll also be sending over employees to set and finish the project.
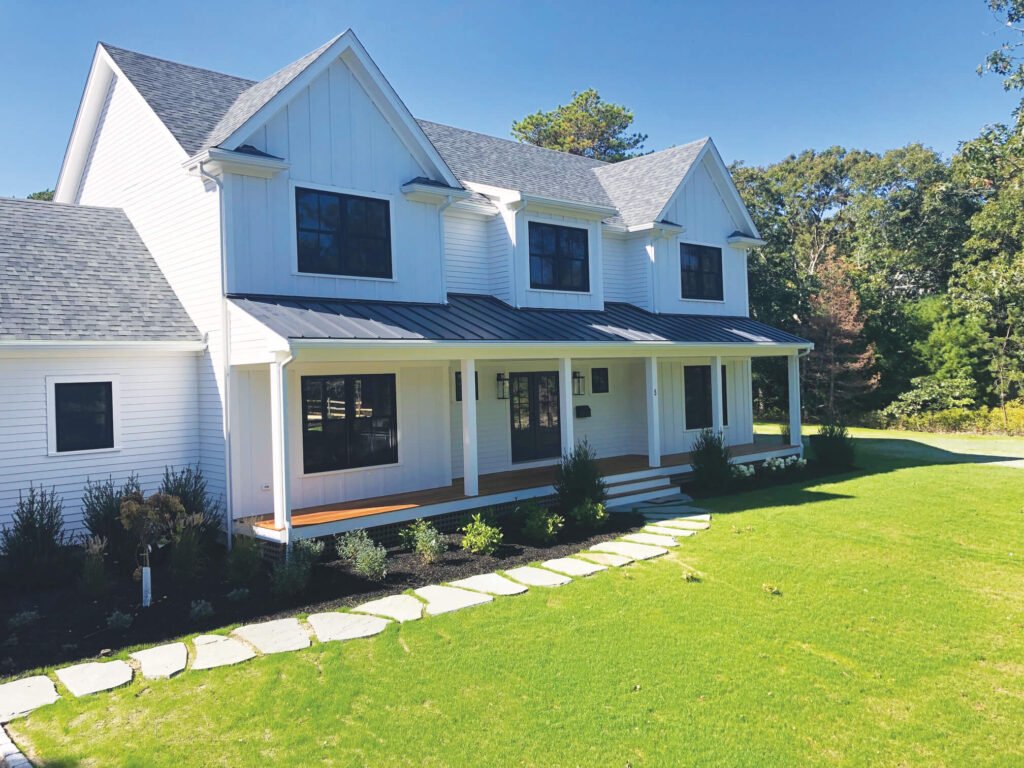
A custom home on Martha’s Vineyard, manufactured by Westchester Modular and built by Squash Meadow construction.
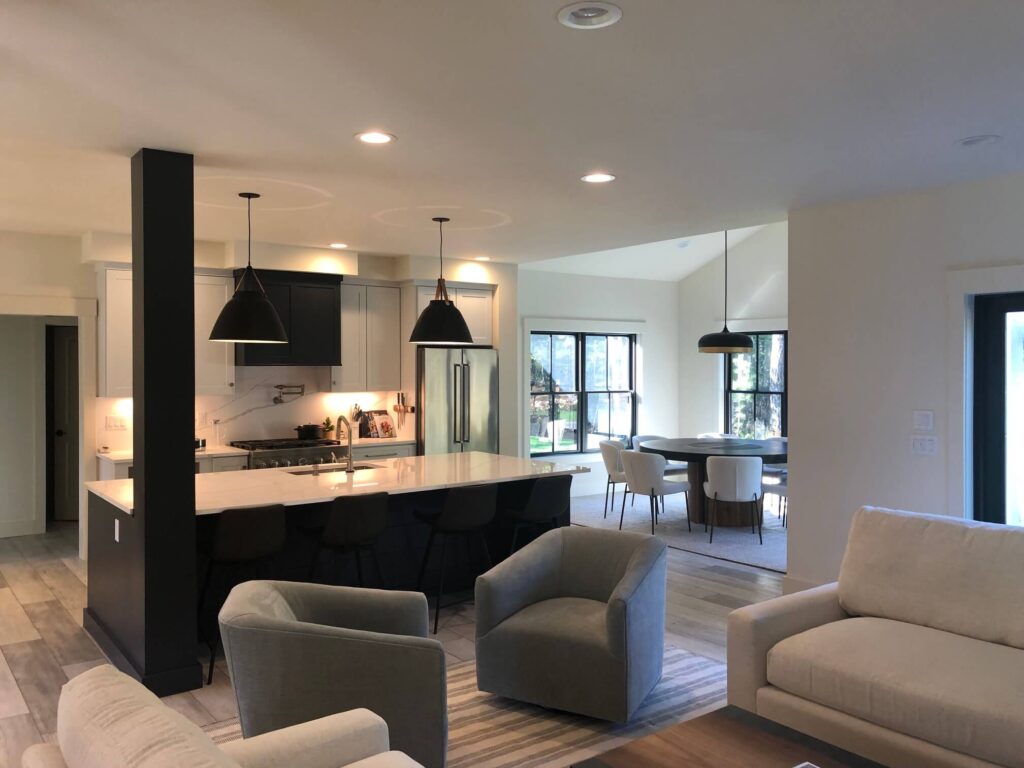
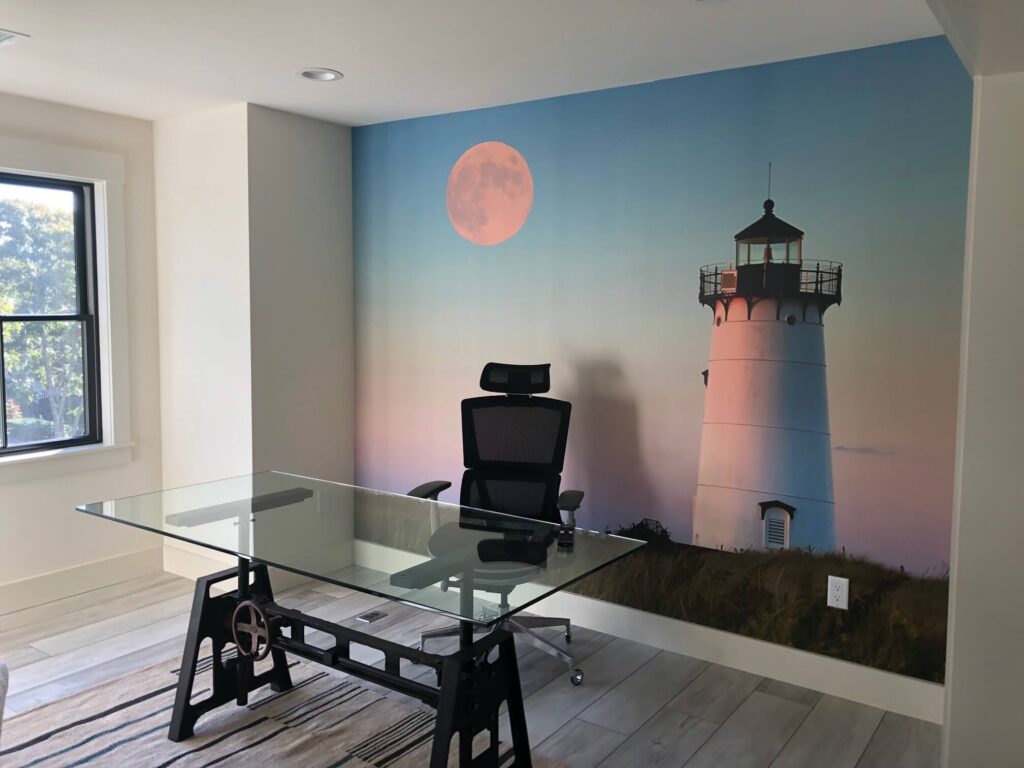
Cost Savings
Module and worker transport challenges might be enough to scare off some builders from using modular, but consider the alternative. “If you’re a builder on an island, you would have to ship over all your building materials anyway,” Landri says. The builder has to pay a premium for everything from dimensional lumber and plywood, to electrical fixtures, wires, switches, drywall and paint.
Then there are labor costs: SBS builds on Nantucket and on Long Island, both of which have affluent populations. In many cases, workers can’t afford to live in these places. “They take the ferry to the island at 6 a.m. and have to leave the job site at 3:00 p.m. to get back on the ferry. It’s not an efficient way to operate,” Landri says.
Modular helps reduce these costs. Squash Meadow project manager Matt Gongola reports that they’re building new, single-family modular homes on Martha’s Vineyard for a starting cost of $450 per square foot. “A stick-built home of comparable quality and finishes starts at around $750 per square foot get the cost down because the majority of building materials and the labor are at off-island rates.”
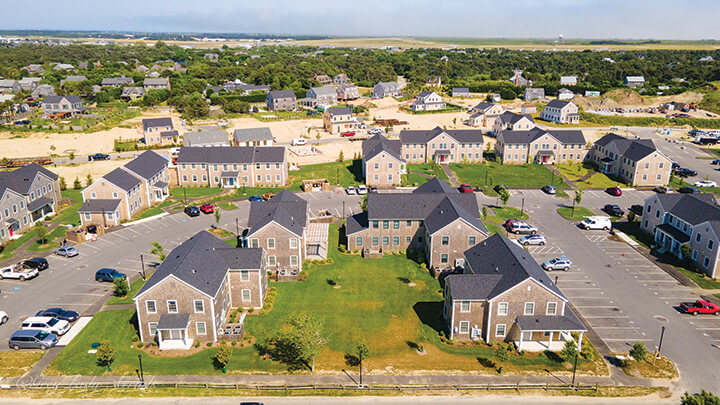
A custom home on Martha’s Vineyard, manufactured by Westchester Modular and built by Squash Meadow construction.
Huntington Homes manufactures a lot of workforce and employee housing, especially on Nantucket. While the product may be repeatable, they’re still customized and have from 1,600 to 2, a square foot of floor area, Webster says. “The barge can add between $20 to $30 a square foot. Even if it’s a 600-sq. ft. cottage, it still requires the same flat fee for the barge.” Still, he says, “we’re probably 30% to 50% less expensive than local site-built construction.”
The other benefit that island builders report with modular is in the timeline. While there are local architectural reviews to consider, especially in historic districts as on Nantucket, the overall timeline from manufacture to move-in is still shorter than an on-island, stick-built home.
Squash Meadow does all of the design work and every home is a custom build. “Depending on the home size, it’s only one to two weeks to build all the modules required for a home,” Gongola says. “The time from when the modules are set on the foundation to the building’s completion, or turnkey, is between three and four months. A stick-built home is a 12-month process.”
Landri says that for SBS it takes about “a week and a half to manufacture a single-family house. Transportation requires about a week and the set another week.” Modules arrive on site about 70% complete. “I believe there’s a complete house in 38 days from there.”
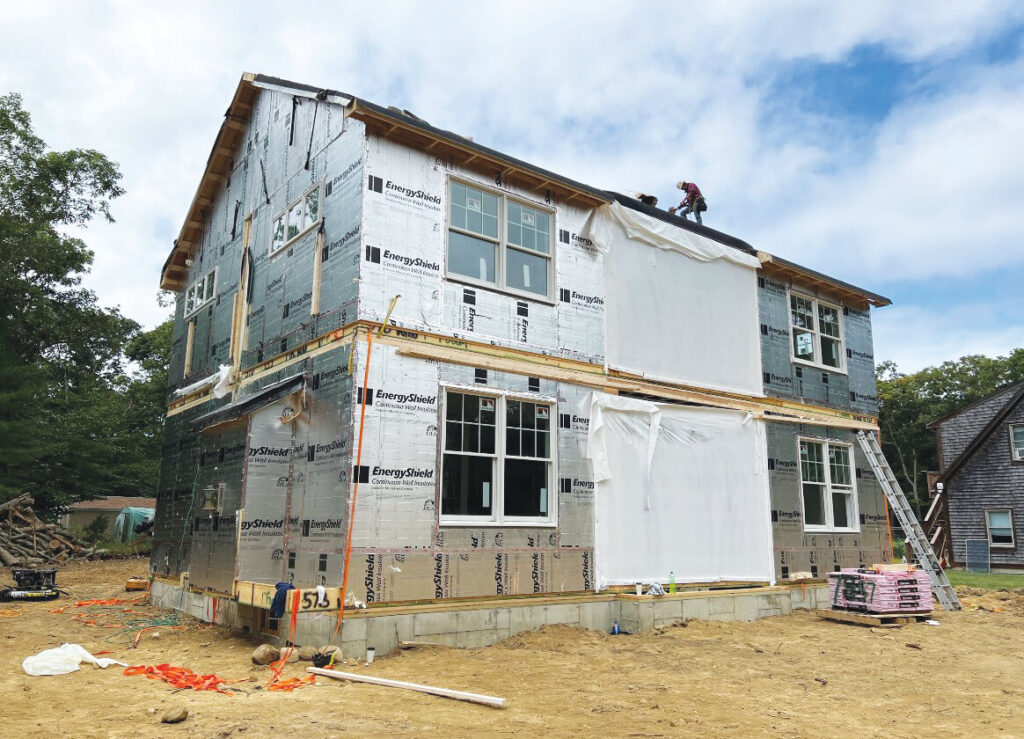
All sets are coordinated and scheduled weeks/months in advance. Squash Meadow tries to start the
set around 8:00 a.m. to utilize the daylight as much as possible, not interrupt the community and
avoid traffic. This house was assembled on the foundation and roofed by 2:00 p.m. on the same day.
Built to Last
Island structures—especially those close to the beach—are more exposed to the elements (wind-driven rain and salt water, for example) than a lot of homes built inland.
Wind load requirements (which change for different regions) mean an island home has to have “extra blocking in the walls and special fasteners to anchor it to the foundation,” Colucci says. In addition, reinforced portal wall framing is sometimes needed around large openings. “The design of many island homes incorporates a lot of glass, which requires more than just normal dimensional lumber framing and plywood sheathing. Materials such as large, laminated beams are incorporated into the structure to support those areas with a lot of glass in high-wind load areas.”
In addition to wind, each state has different energy codes and snow load requirements. For example, Nantucket is a signatory to the Massachusetts Stretch Energy Green Community Code, which requires optimized building performance. According to Landri, this code’s required energy conservation performance levels are 20% higher than the code-mandated ASHRAE Standard 90.1-2007 for low-rise buildings.
“All of these loads have to be calculated by an outside engineer,” Landri says. “And we talk with local GCs since each house has its individual requirements.”
In addition to wind-driven rain, humidity can also be a big issue on islands. For instance, Gongola points out that Martha’s Vineyard is a more humid environment than the mainland. For its subfloor, Squash Meadow specifies an OSB substrate (or wood-based composite) with “quite a bit of resin, which doesn’t allow the product to absorb moisture.”
Ultimately, island modular building is a highly-coordinated dance. Regardless of whom you sell to, Landri says, “as long as they’re involved and transparent and everyone is communicating, a project can be successful.” Take your time before you set sail.
[…] Read Full Article Here – Offsite Builder Magazine […]