Understanding the basic types of steel wall panels and their uses
- According to the author, this system is a perfect fit for buildings up to 5 stories.
- Customers can choose from various levels of finishing, load-bearing capacities, and insulation.
- Shipping and installation are similar to other panelized systems.
The oft-cited advantages of panelized construction include cost savings and shorter construction timelines. But the actual savings will vary by panel type. Panels can be framed with either dimensional lumber or light-gauge steel (which has a thickness range of 14 to 25 gauge).
In this article, I outline the types of light-gauge steel panels that are available, what they offer to owners and general contractors, and how to get the most from them.
As their name implies, one advantage that light-gauge steel panels have is that they weigh less than wood, which makes them easier to transport and to install. At the same time, they’re sturdy enough for structural, load-bearing applications as well as for curtain walls that have to resist wind and rain. Clients have also told me that steel-framed buildings hold their value longer than their wood counterparts.
The sweet spot for light-gauge steel panels is in four to five-story structures, including hotels and multifamily projects. Buildings of this height don’t necessarily need iron or concrete columns; structural support can be provided by the panels themselves. The panels will, of course, be supplemented by I-beams when needed to support interior spans with no load bearing walls, or as headers for big window or door openings.
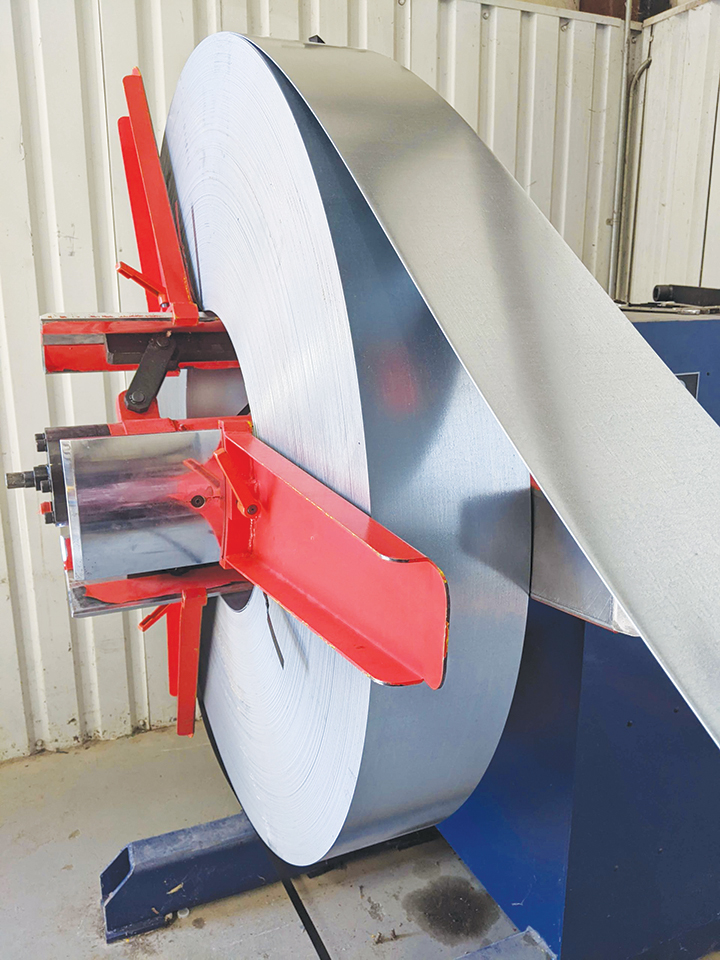
The steel framing members for the panels are manufactured using small, specialized roll formers. In the past, roll-forming machines were expensive and had to be housed in large manufacturing facilities. However, today’s small machines lower the financial barrier to entering this market and can be housed in smaller facilities. Notable brands include Knudson, Framemac, Framecad and Howick.
Small roll formers also allow builders to roll their own custom-length metal studs based off of a CAD generated kit-of-parts instead of buying stock lengths from a distributor.
Degrees of Finishing
As with other offsite technologies, panel construction involves the manufacturing of components in a factory. These components are transported to the construction site and then installed using a crane, a lift or (in the case of small and light panels) manual labor.
The degree of factory-based finishing varies. Clients can opt for basic panels with just the steel framing. Or they can choose panels that are sheathed, stuccoed and insulated in the factory, thereby reducing the work that needs to be done on-site.
Load-Bearing Panels
Exterior, load-bearing steel wall panels function like any other frame wall. That is, they’re designed to carry the vertical and lateral loads of the structure while also providing a durable surface for the exterior finish, which is installed on-site.
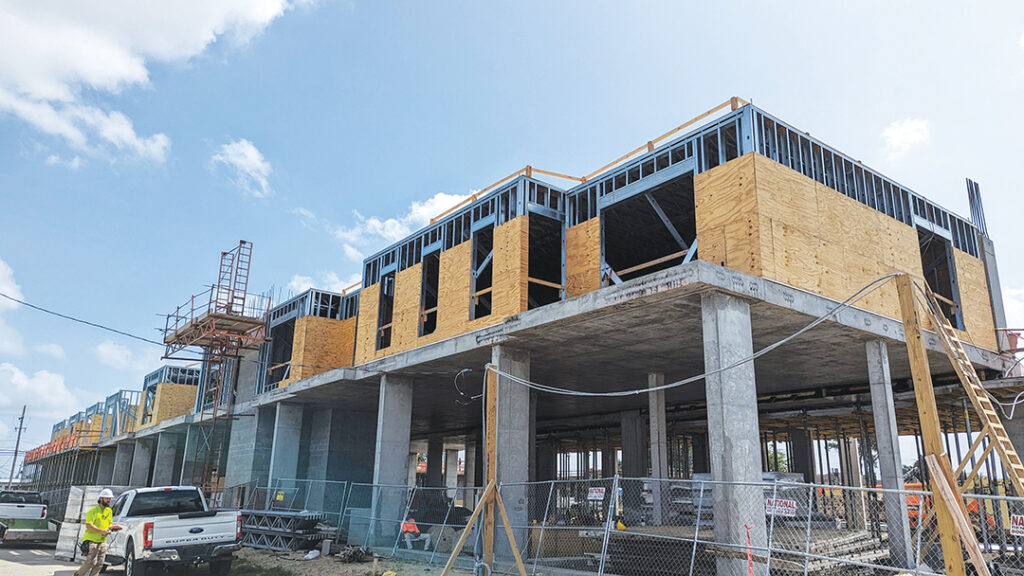
Structural panels use a minimum of 3 5/8-inch deep, 18-gauge steel studs. For more support, studs as deep as 12 inches can be used, in thicknesses up to 14-gauge. The exact sizing will be determined by local codes, wind loads and the number of stories.
As an example, we recently manufactured the panels for a five-story building in the New Orleans, La. area. It consisted of a concrete podium that supported four steel-framed stories. We used 16-gauge studs for the non-load-bearing infill walls underneath the podium, and 14-gauge for the load-bearing walls above.
Panels range in length (horizontally) from 8 to 14 feet. Although they can be made tall enough to span two stories, one-story panels are more common because they don’t exceed over-the-road shipping limitations. They can also be installed by smaller crews.
Insulated Panels
Some builders, especially those in Canada and the Northern US, elect to have their panels insulated in the factory. The types of insulation used varies from fiberglass or hemp batts, to blown-in expanded polystyrene (EPS) or polyurethane foam. Insulated panels are an especially good choice where the client needs an airtight building and/or wants to secure a good LEED rating.
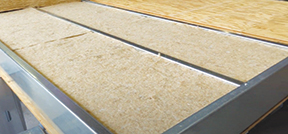
Cladded Façade Panels
Panels with factory-applied exterior cladding are called façade panels, and they include a light-gauge steel frame with plywood or oriented strand board (OSB) sheathing and stucco or brick. While used mostly in urban projects of five stories or more, they can also be cost-effective for smaller buildings.
The extra weight of the cladding means that installation will require a crane.
An example of a company that specializes in these is Atlanta, Georgia-based Southern Wall Systems, which primarily makes stucco-clad panels.
Design and Fabrication

Although panels can accelerate the construction schedule, additional time will be needed during the design phase. It’s necessary to involve the factory’s engineer right from the start of the building design process. The factory’s engineer will be a specialist in cold-formed steel design and will work alongside the client’s structural engineer and architect.
Note that there are subtle factors that could affect the price and complexity of a panelization project. For instance, in a hotel design, if doors are recessed from hallways, that will necessitate breaking up interior load-bearing walls and incorporating costly headers.
There are various software programs available to aid engineers and panel manufacturers in designing light-gauge steel panels. At US Frame Factory we use Strucsoft and AGACAD, which work with an existing Revit model and provide metal stud sizing, wall panel dimensions and the creation of detailed framing models.

Once the design is complete, we use a software-generated cut list to run our roll formers. The roll formers shape and cut steel coils into the studs and tracks needed for the panels.

We use a Knudson Manufacturing roll former, which allows us to manufacture a range of stud sizes from 3 ⅝ to 12 in. deep. Studs and tracks include pre-punched screw holes, which greatly simplifies assembly.
After the panels have been finished and successfully passed through a quality assurance and quality control procedure, they are either placed onto trailers or kept on-site to be delivered at a later time. Each individual panel is assigned a distinctive piece marker, which designates its specific position within the structure.
Shipping Considerations
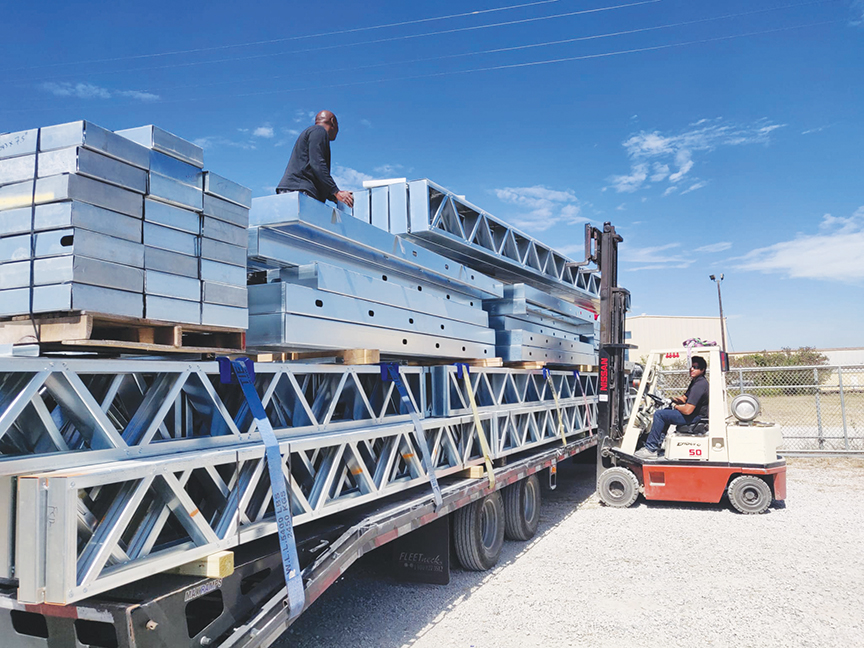
Wall panels can be stacked on a flatbed either vertically or horizontally, but the load shouldn’t exceed an 8-foot 6-inch width. Anything wider is considered oversized and will require extra permits. Also, when stacking panels, bear in mind that 13 feet 6 inches is the legal height limit for a loaded 18-wheeler.
A 53-foot flatbed 18-wheeler could comfortably fit about 7,000 to 12,000 square feet of panels, depending on panel thickness.
Installing the Panels
Most panels are set using cranes. To minimize crane movement, panels need to be staged on the site in close proximity to each other and in the order they will be needed. This type of sequential installation requires meticulous pre-planning.
As I already mentioned, the time and labor savings for light-gauge steel panels will vary by building size and type. However, four to five-story buildings that can be built purely from light-gauge steel, with minimal structural I-beams, offer the most savings when compared to wood. Savings will also be greater in areas with high on-site labor rates, such as the Northeastern and West Coast states.
Tiago Atwi is Co-Founder of US Frame Factory, a manufacturer of steel panels based in New Iberia, Louisiana. All photos courtesy US Frame Factory.