Beach homes on the Jersey Shore showcase the versatility and durability of modular construction
- The author used raised foundations and engineered modular construction to build beach homes that survived one of the Northeast’s worst-ever hurricanes
- He uses wide-diameter pilings sunk deep into the ground (that are also reinforced with cross-bracing), which will remain stiff in even the strongest winds while protecting the home from storm surges
- Modules are engineered at the factory to meet all wind codes. They also include extra structural details specified by Zarrilli Homes
- Customers have embraced this building method because they consider it to be of higher quality than conventional construction
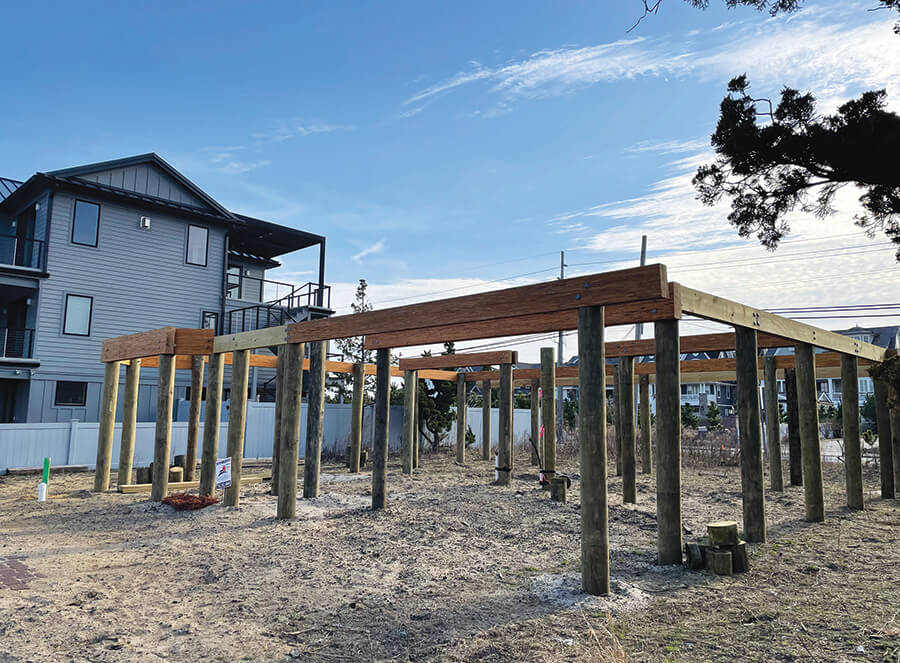
One thing I sometimes do when potential clients express concerns to me about the quality of modular homes is to share my experience with Hurricane Sandy.
Most people on the East Coast remember Sandy, which has been called a “superstorm.” In late 2012, it inflicted nearly $70 billion in damage and killed 233 people across eight countries from the Caribbean to Canada. One of the hardest-hit areas in the Northeastern US was the New Jersey Shore, where 43 people died, and where high winds and a 4-9 ft.-high storm surge destroyed or severely damaged, tens of thousands of homes.
But some homes survived including, I’m happy to say, the ones my company built. We have been building custom homes on the Jersey Shore for about a decade, and by 2012 had completed hundreds of them. Although most of those homes were right on the water, not a single one was lost to the storm. Why?
They had two things in common:
1. All were built on piling foundations that lift the structure well above the flood zone.
2. All were built using factory-built modules reinforced for our wind zone.
Before Sandy, piling foundations were only used in a minority of new homes, even on the water. However, after authorities saw that they made homes more survivable, they were written into the New Jersey state building code. They’re now required for new construction in the majority of coastal flood zones.
The fact that my company was one of the first builders in the area to use pilings, and the only one to use factory-built modules, has been great marketing for us. My business has grown since 2012 and at this writing, we have completed over 750 modular homes. About 80% of them are on, or near, the beach and elevated on pilings. Sizes have ranged from 520 to 11,200 square feet.
Here are the construction details we have come to rely on.
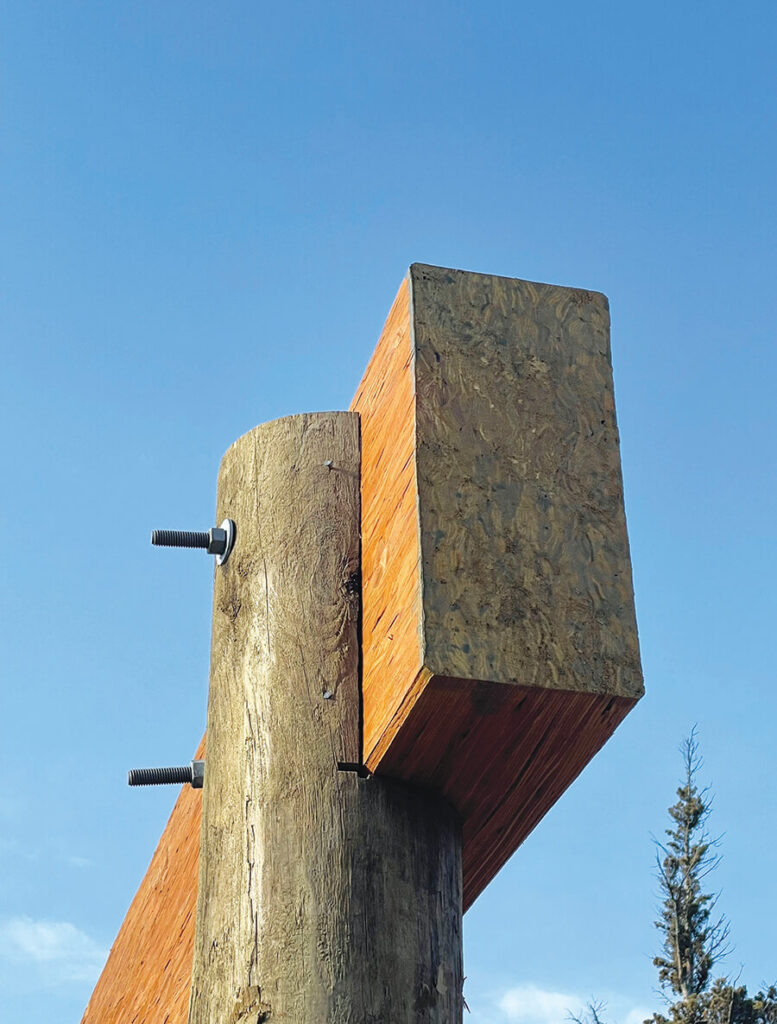
Raised Construction
Some people are surprised that we can place modular homes on top of pilings. Don’t the modules need to be supported at all edges with a concrete foundation or crawlspace wall? The answer is yes; they do need to be supported, but not necessarily with concrete. We use structural beams; i.e. Microlams, LVLs, etc.
To create a base for the modules, we use a vibratory pile driver to drive treated wood pilings a minimum of 15 feet into the ground. Pilings are ACQ-treated southern yellow pine, rated for ground contact; they will last longer than the house. (Piling types can vary by region. We also build in the Florida Keys, where we site pour concrete pilings and reinforce them with steel rods drilled three feet into the underlying coral.)
A lot of people ask us whether the house will sway in high winds. My answer is that they won’t if you use thick pilings and add stiffeners or cross bracing. Not all builders do that. I’ve seen some use 8-in. diameter pilings (a utility pole, basically) placed at the maximum spacing required by code. But with gale-force winds common on the shore, especially during the winter, we don’t think that’s good enough—the homeowners would feel heavy swaying.
Codes are meant to ensure safety, but we also have to worry about customer satisfaction. Basically, we want them to be so impressed with how solid their home feels during a winter blow that they tell all their friends. That’s why we use 10-in. diameter pilings around most of the house and 12-inch diameter ones under mate walls.
We also add cross-bracing between pilings. This isn’t required by code, but to my mind, it’s important. Even in the strongest wind, the home will feel as stiff as if it’s on a concrete foundation.
The tops of the pilings are notched and an LVL or PSL band is bolted into place. Additional posts and beams are added where needed—usually along the home’s centerline—as well as under mate walls.
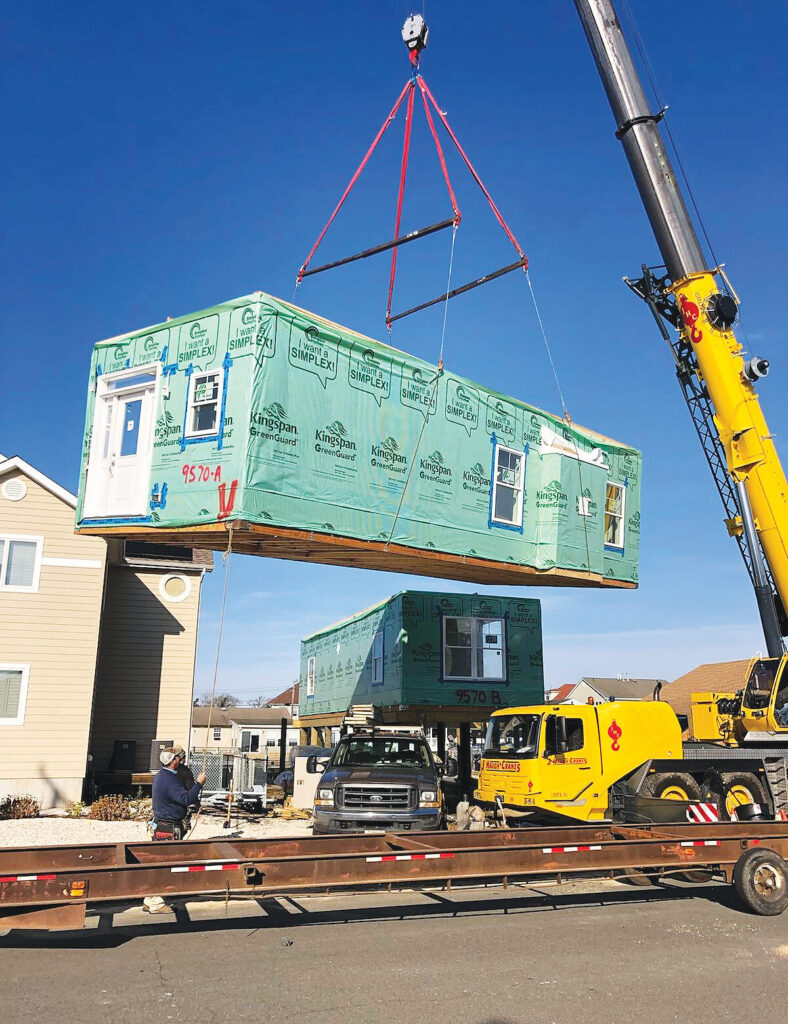
Module Design
Pilings alone won’t make a home storm-resistant—the structure itself has to be designed and built to withstand the elements. This doesn’t preclude modular, but is actually one of its advantages, in my opinion.
That’s because the modular manufacturers we work with can engineer their homes with whatever reinforcement the code requires. Their engineering departments know the specs required for the wind zone where we build. They also have quality control systems to ensure that everything is built to those specs; I never have to scrutinize the work of a framing sub because I know it will be done right at the factory.
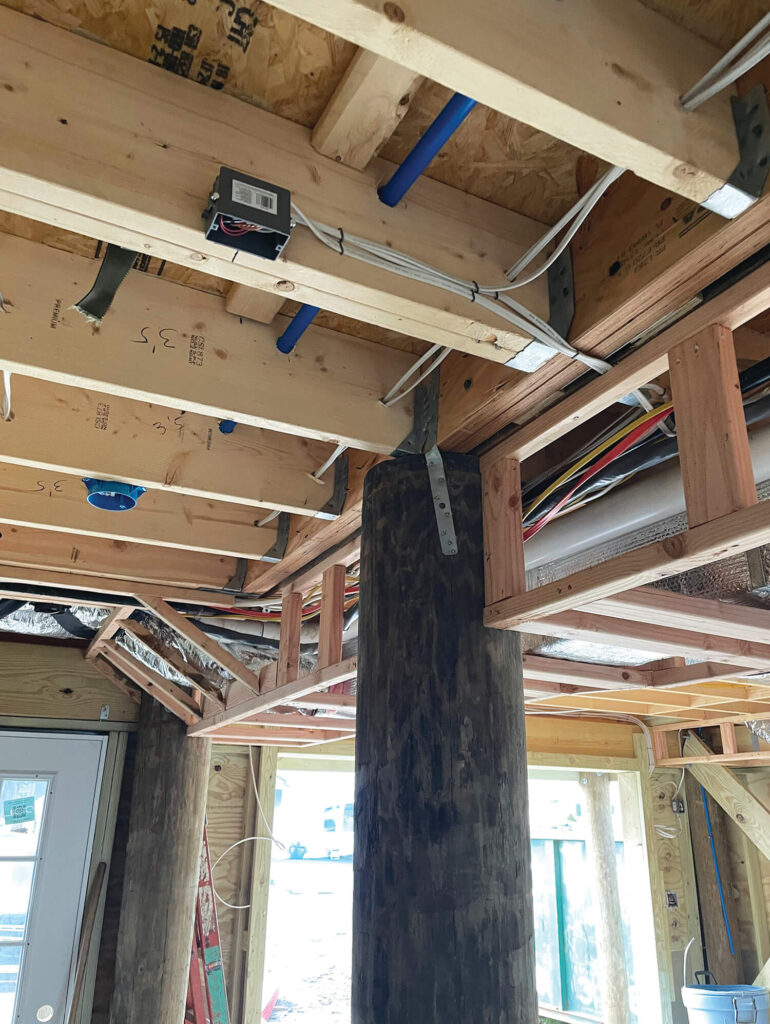
For instance, to meet code, homes on the beach end up needing 18%-24% more structural lumber than homes further inland. They also need in-wall hurricane straps, as well as hurricane clips to secure roof rafters to top plates. I also give the factory a 2-½-page spec sheet of additional details I want, including LVL band joists, which make for a better-built home. The factory is happy to include all of these details and to make sure they meet the required specifications.
Further stiffening is provided by the fact that the factory glues and screws sheathing and drywall to the studs. This is done to keep modules stiff while being driven down the highway, but it also makes them more wind-resistant once in place.
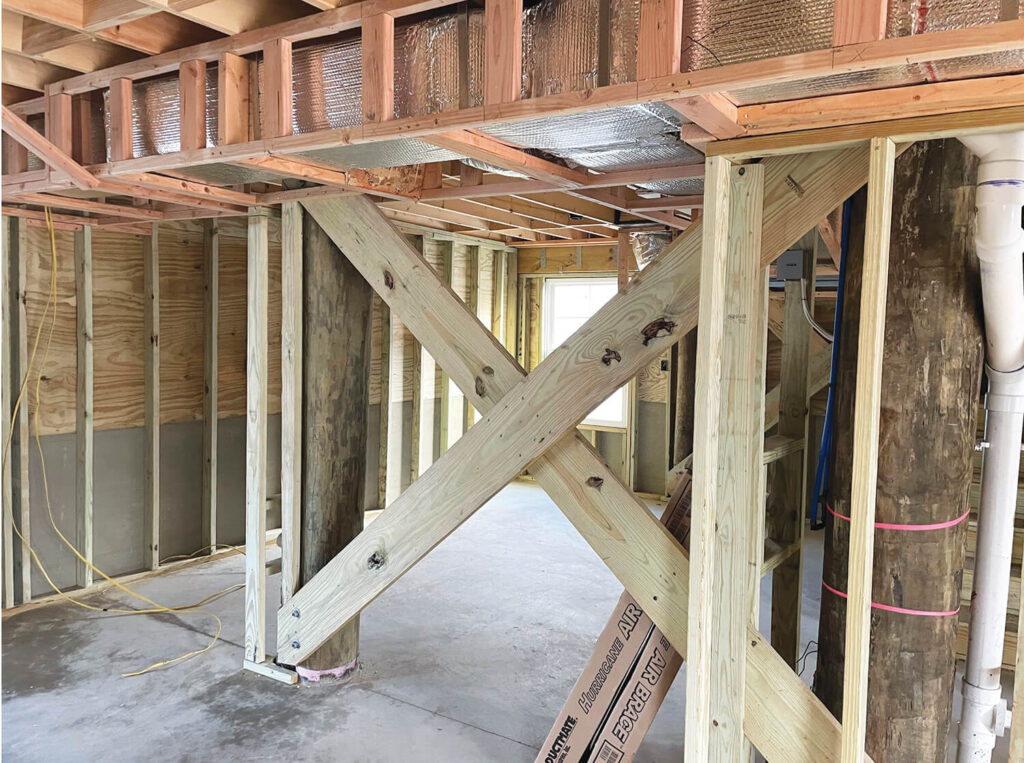
Customers Love Them
Are all of our homes modular? No, they actually represent about 80% of our work. We will site-build a home if the customer really wants one, but I always try to steer them away from site-built. That’s because, in my experience, a factory-built home offers better, more consistent quality.

Fortunately, I get fewer and fewer such requests. When I first started building homes this way I did get a lot of questions from potential clients, but modular homes are so common today that people have more confidence in them. And when I explain the structural details we use, most people see the advantages. In fact, my younger clients actually prefer modular and consider it cutting edge. Some even come to my company specifically because we offer it.
