This DC-area remodeler has found them to be so
- Michael Winn says that modular is a great choice for homes with simple footprints on small suburban lots
- Success with this approach requires in-house design capability, obsessive planning and a flexible manufacturer
- Modular greatly reduces the time homeowners need to be out of their homes, and clients seek him out for that reason
Modules are custom-designed and have to be lowered into place without damaging the existing structure. Prepping the home for the modules includes adding leveled sill plates, as well as structural posts to carry the load.
Given the right market conditions, modular second-story additions can give a remodeler a real edge over the competition, according to Michael Winn. His company, Winn Design + Build in Falls Church, Virginia, has completed about three dozen of these projects in the past eight years.
Winn’s company is the only one he knows of in Northern Virginia that offers modular second stories, and some customers have come to them specifically because of that offering.
With that success under his belt, he has now decided to offer additional modular products.
But while additions have proved a viable business for Winn, whether they work for another remodeler will depend on several factors. These include the existing housing stock, buyer demographics, and the structure of the company.
You Need the Right Fit
Winn’s market is a strong one for second-story additions in general, with an abundance of small, single-story or story-and-a-half homes on tiny lots. They’re being purchased by young, affluent people with growing families who need extra space. Very often, the only way to get that extra space is to go up.
Why does Winn prefer modular to site-built?
It has a lot to do with his area’s housing stock. The most common customer for a second-story addition owns what Winn calls “a shoebox”—a small structure built shortly after WWII with a rectangular footprint. It’s easy to design and manufacture modules for these simple structures.

Another reason is that his clients are receptive. “They tend to be young people with fewer preconceived notions than their parents,” he says. “They’re what I call the Dwell generation. They see modular as cutting edge.”
They also like the cost savings. Even though the second-story addition is almost always part of a whole-house remodel, the use of modular lowers total job costs by 10%-15% compared to site built.
But what mostly draws those young customers to Winn is the compressed project timetable. For a modular addition, the family only has to be out of the house for two to three months, compared to five or six for site-built. “We don’t even start demolition until a week before the modules arrive,” he says.
That means less disruption for the family and less time that they need to be in a high-priced short-term rental.
It’s Not For Everyone
In addition to an appropriate market, Winn believes that success with modular requires the right business model.
As the name implies, his company is a design/build firm with in-house architects. In fact, one of his staff architects had previous experience with modular and that expertise was part of why Winn took a chance on his first project. He knew that the demands placed on each design would be more stringent than with a site-built second story.
Simply put, there’s no room for error.
Once the modules leave the factory you’re stuck with them. “Every time we do one of these projects I imagine that I’m planning a mission to Mars,” says Winn. “The moment the ship blasts off you can’t get it back.”
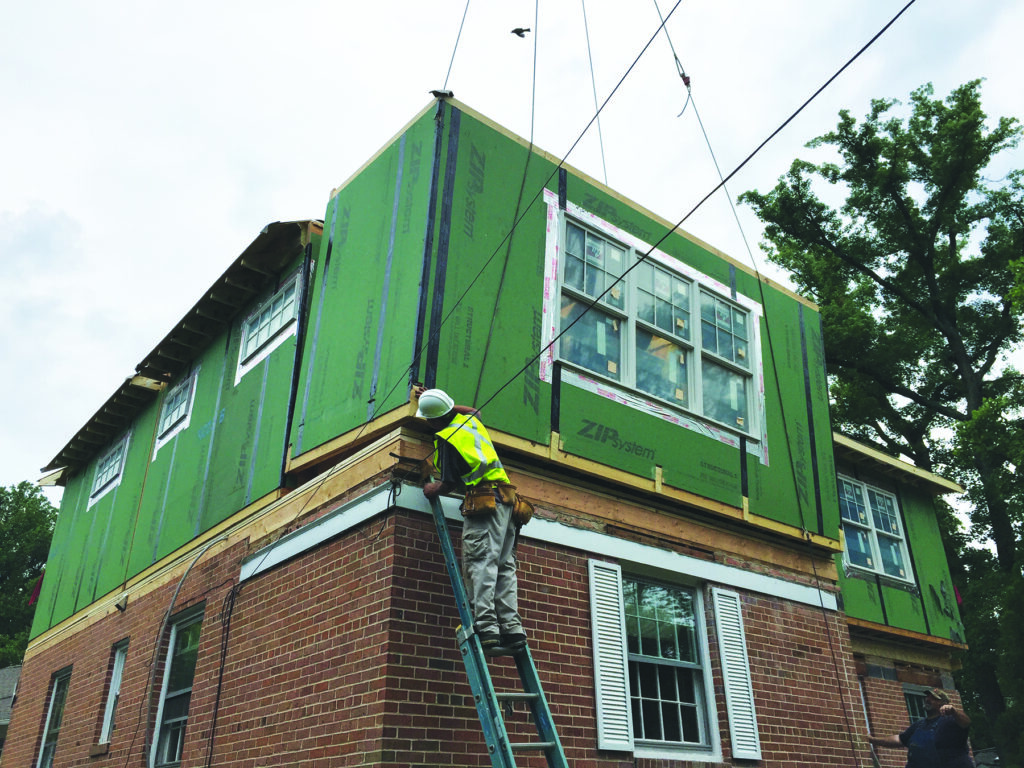
The two big issues are:
- Modules have to fit the existing home perfectly.
- His architects have to ensure proper load paths to support the second story. This often means adding steel beams and in-wall Lally Columns to the existing structure.
That’s not to say there’s no wiggle room. For instance, while modules have perfectly straight walls and perfectly square corners, a lot of old houses don’t. To compensate, Winn’s architects sometimes cantilever the addition 12-14 inches off the back of the house and add a porch or portico at the front.
In addition to hiding wall bulges and other imperfections, overhangs and porches also help the addition and existing houses blend together. They keep the result from looking like a big box.

Another design issue Winn says to be aware of is floor thickness. The finished result is twice as thick as a site-built second story because of the combined depth of the home’s ceiling joists and the modules’ floor joists. That adds a couple of stair rises and runs, which means the stairway requires more floor space. “It’s not a problem in our case because we’re renovating the first floor anyway,” he says.
There also is a good bit of site work. For instance, Winn uses fiber-cement siding, which his module manufacturers don’t offer. And his quality expectations for interior trim are often higher than what he can get from the factory. He has the modules shipped without those items.

And, of course, his crews have to renovate the first floor and build the stairs, and his plumbers and electricians have to tie the existing home and the addition together.
Choose Manufacturers Wisely
Winn has a handful of manufacturers to choose from, with the choice for each job depending on the home design and the factory’s current backlog. He works with niche manufacturers that cater to custom home clients who want design flexibility. “One of the companies we use has the word ‘Custom’ in their name,” says Winn.
When vetting a new manufacturer he shares sample plans and specs with them and asks if there’s anything they wouldn’t be able to achieve.
As mentioned, most don’t offer the quality level Winn needs for interior trim, so his crews do that. “The manufacturers I’ve identified who work to our quality levels tend to be on the West Coast and that’s too far away,” he says. Although trimming the modules on-site is an extra expense, he still saves his customers 10% to 15%.
Material challenges actually go beyond trim. He has to find manufacturers that will install the products and materials he wants, some of which aren’t on their standard spec list.
“For example, we use Advantech subfloors, Zip-R sheathing, 2×6 wall framing, and spray foam or rockwool insulation,” he says. “With some manufacturers, these specs are a nonstarter, but with persistence, we have found companies that will work with us. The custom-oriented manufacturers tend to be more amenable.”
What’s Next?
Despite the challenges, Winn’s experience with second-story modular additions has been largely positive. He believes they give him a real edge in his market.
That edge is sharp enough that he has decided to move into modular single-family homes placed on infill lots.
Between Amazon’s planned new HQ and the Dulles Technology Corridor—a cluster of defense and high-tech companies—more and more affluent families are moving to the area. A growing number of them prefer to tear down those shoebox homes and build from scratch. Winn wants to tap into that market.
“For us to get into new, single-family homes, however, we had to offer something different,” says Winn. “We decided that modular homes with modern designs would be a unique selling proposition.”
His architects have already designed a half-dozen models with “a Scandinavian design ethic,” and modern amenities. They will include high-tech features like a home backup battery and car charger in the garage, as well as smart device integration throughout the home.
Modular will let him offer these homes on a faster timetable than the competition without sacrificing quality.
All photos courtesy of Winn Design + Build