An engineer learns what it takes to build a Net Zero modular home
In 2019, Bill Spohn and his wife, Marilyn, were building a house. They knew exactly what they wanted: a modular home that performed much better than the norm. The Spohns strove to do everything feasible to make their house as close to Net Zero as possible, and they exceeded their expectations.
What Exactly is Net Zero?
A Net Zero home has solar panels that make as much electricity on-site as the home uses over the course of one year. Sometimes, the home uses more than it makes, while at other times it makes more than it uses, but energy [not?] used will eventually be returned to the grid.
Spohn traces the desire for such a home back to his and his wife’s parents, all of whom lived through the Great Depression of the 1930s. “We were both taught that everything is precious, so it bugs me to waste things,” Spohn says.
The insistence on conservation, combined with a lifelong interest in technology (growing up, he wanted to be the editor of Popular Science magazine) led Spohn to want to build a Net Zero home. However, another key factor empowered him and his wife on their quest.
Spohn has been a mechanical engineer for 40 years. He has owned and operated his own company, TruTech Tools, since 2009. The business is a leading distributor of testing and measuring instruments used to track performance in the built environment.
Through work conferences, a Facebook group he created (SpohnHome) and organizations he is part of, Bill got the inspiration to move forward on the house, along with the confidence that he had a network that could help him through the process. That network helped him develop the following five suggestions for anyone wanting to build a high-performance modular home.
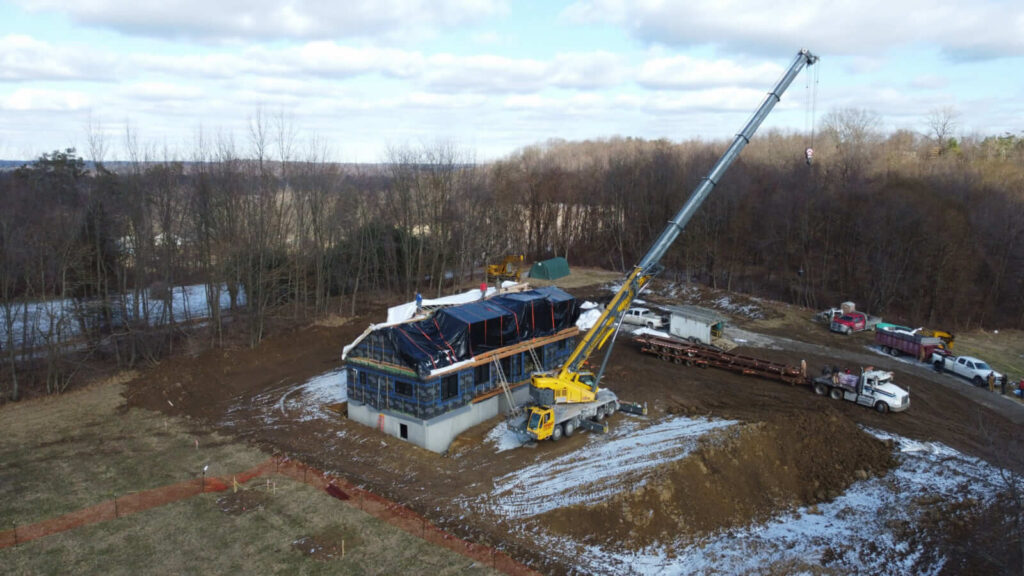
Spohn’s Top Five
1. Use/respect the sun. A high-performance modular home can be just about anywhere. The Spohn’s home is outside of Pittsburgh, Pennsylvania, which is in climate zone five. That means it’s subjected to the extremes of both winter and summer weather.
Wherever a house is sited, it must take full advantage of the sun. For the Spohns, that meant south-facing windows that enabled the interior to benefit from passive solar heating of the living space in the winter.
Permanently affixed, exterior solar shades over most of the south-facing windows, block direct solar heating in the summer, yet allow the low winter sun to help heat the house in the colder months.
Of course, the best window placement will vary with where the house is located and the builder needs to determine how much solar energy the location receives. In a cold climate, there should be enough windows to warm the interior when the sun is out, but not so many that they lose too much heat on cloudy days or at night. In a hot climate, the home needs windows that let light in, but not heat.
2. Develop a detailed contract. The Spohns spent a significant amount of time going over the design of their house with their builder before they signed the contract. Because their house included multiple out-of-the-box details, their builder needed to be on the same page regarding the contract before construction began. Everything must be detailed, Spohn advises.
A builder also needs to understand Net Zero and Passive House philosophy (defined as a voluntary standard for energy efficiency in a building, which reduces the building’s ecological footprint), or at least be open-minded about it.
A modular builder, unlike a stick builder, can be more detail-oriented. Modular building also tends to have more harmonization in the trades because they all work in the same factory.
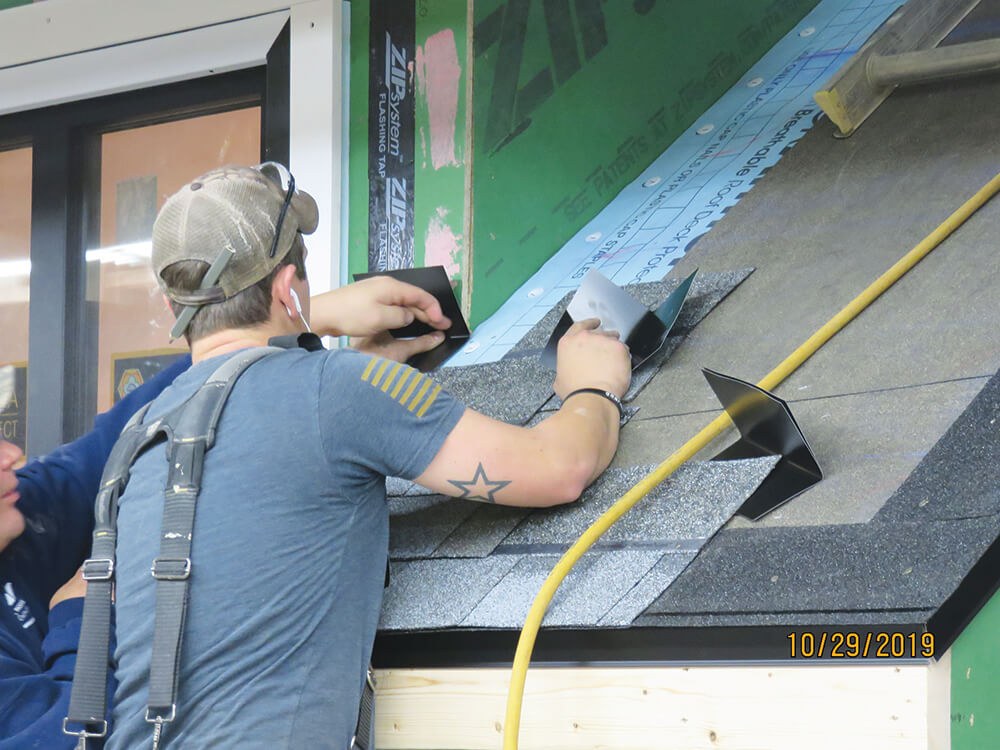
3. Watch the air leaks. Air leakage is the number one cause of energy consumption, according to Spohn, so it’s vital to understand airflow. You need to control all the ways air enters and leaves the house.
One way the Spohns gained control of their home’s airflow was by taping every seam of the sheathing panels. They also had sealant put on every sheathing fastener head. They paid the factory extra for these and a few other energy-related features.
“This was an extra process step, a detail that a modular builder can put into their factory plan,” Spohn says. He adds that working under a roof (in the modular factory) during construction means no weather delays and no potential for weather damage to the materials under construction, so this extra step took minimal time to incorporate.
4. Find the right local finishing contractor. The modular builder and factory can do everything right and strictly adhere to the contract, yet a house may not perform as expected.
Why? Proper assembly of a home is essential. Working with a local finishing contractor (in Spohn’s case, the builder) who understands the Net Zero concept and respects requests is a big step to getting to Net Zero. The Spohns chose their builder based on their certification as a Passive Home builder.
Despite the certification, Spohn says it was important to watch and verify the execution. He and his wife hired a third-party energy consultant who interacted with the builder (and the factory) and made sure the home maxed out its potential.

5. Have detailed wall construction. Wall construction is also key to a high-performing house, since, like any house, modular homes are susceptible to air leakage. The wall construction is also important when it comes to moisture control and insulation.
Because layers of the wall and details matter, the Spohns had specific requests. Their modular builder was willing to comply with the requests and was comfortable building a Net Zero home. “I did factory tours and saw coaching on-site to ensure the construction was according to the specs,” recalls Spohn.
Focus on the demanding specifications of the walls and other components of a house is less likely to happen in a traditional outdoor building location. A consistent workforce is required to successfully implement a demanding level of interconnected details. The workforce may be less consistent with stick building as crew members may be geographically relocated between projects and supervision may not always be present.
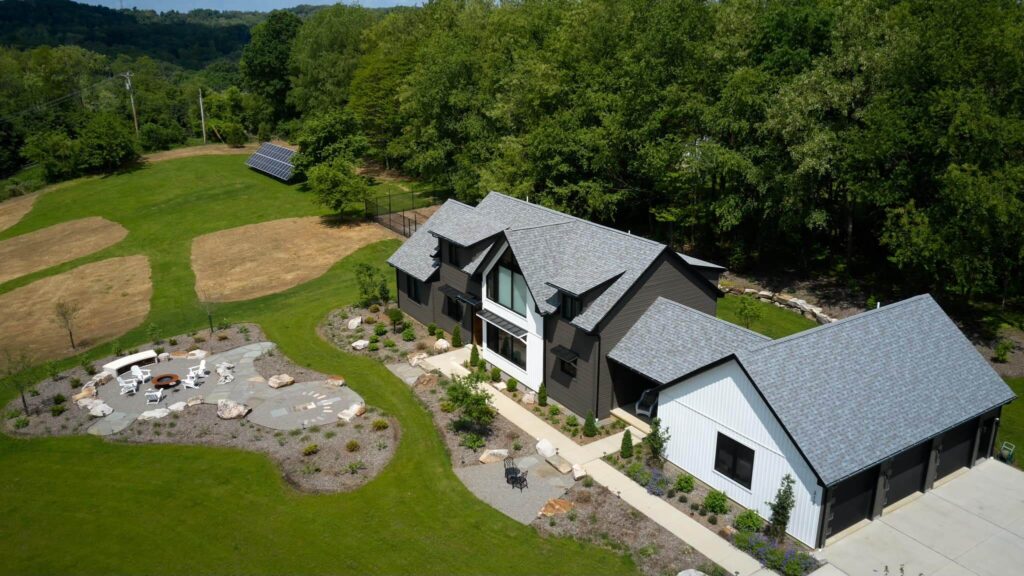
Who Can Do This?
Spohn readily admits that he had advantages that enabled him and his wife to develop a Net Zero home. Among them are knowledge about what was needed for a Net Zero home and a network that could help him with suggestions and encouragement.
Yet, a high-performing modular home is possible for those with less technical background knowledge. A home can also be more moderately priced if the homebuyer is willing to accept less customization than in the Spohn house.
Due to growing environmental concerns, including energy conservation and global warming, the combination of modular and high performance is bound to become more popular. Both are green and lead to less waste. By minimizing energy consumption and materials, others can live with an eco-friendly ethos and recognize that everything is precious.