Some authorities still look askance at modular homes. Here’s some advice on how to win them over.
- Even some allegedly knowledgeable regulators still don’t grasp the difference between modular and manufactured. Successful modular builders make an effort to educate them ahead of time.
- In jurisdictions where authorities have a habit of putting roadblocks on the path of a modular project, it’s best not to order modules from the factory until all zoning approvals are in place.
- If all else fails, some builders have mounted successful legal challenges to modular restrictions. Courts have ruled that while a community can tell them what to build, it can’t tell them how, as long as the structure meets all code requirements.
More and more homebuyers understand that the quality of modular construction can be equal to, or better than, site built. Unfortunately, however, a lot of the experts who regulate homebuilding still don’t get it.
Custom modular builder Kopper Creek Builders found that out in 2021. The company was new to Divide Ranch, a well-established subdivision in Western Colorado, when nine homebuyers hired them. “People thought the community wouldn’t allow modular homes, but word got out that you could build a modular home, and we got swarmed,” says David Thomas, Kopper Creek’s Vice President of Sales, who attributes the interest to the company’s competitive costs for what is, essentially, a luxury home product. “We’re near Telluride [ski resort] where construction costs are very high. With modular, we can keep costs down.”
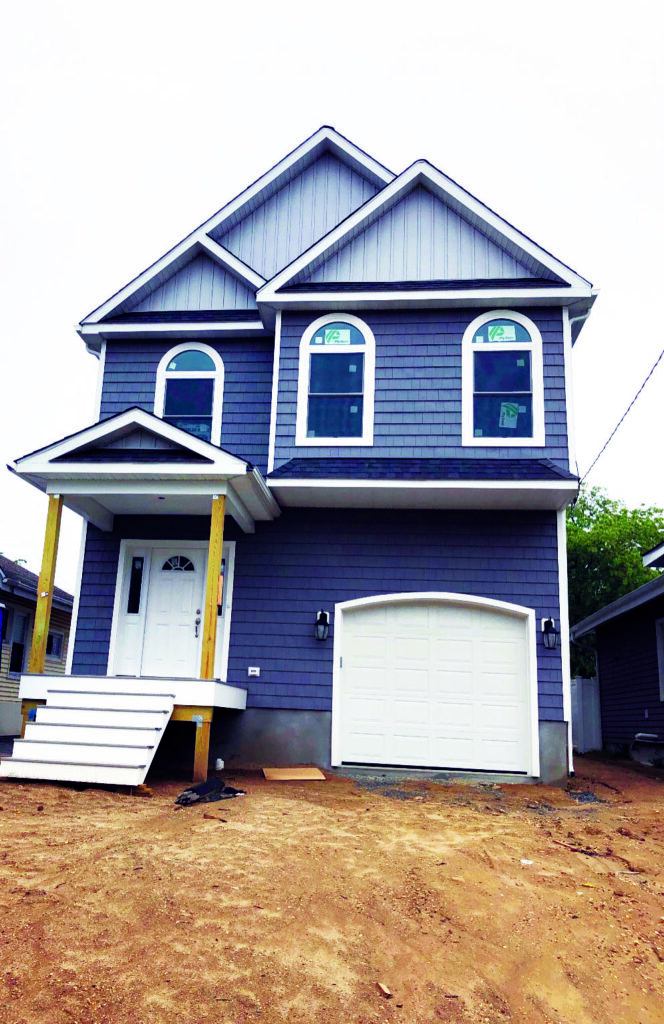
Photo Credit: Zarrilli Homes
Kopper Creek began the process by hosting a meeting of the community’s HOA, where “about 60 of the 200 full-time residents showed up,” Thomas says. He created a PowerPoint presentation to show them examples of modular homes and what the proposed homes would be like. “We got overwhelmingly positive feedback from that meeting,” Thomas says.
The project was approved, but when the modular components began showing up on-site, it all fell apart. The community’s architectural control committee didn’t like what was happening and decided to put a moratorium on modular building.
Fighting the Stigma
One of the main issues was a confusion over terms. “In their zoning ordinances, many localities include modular construction with manufactured housing — homes constructed to the HUD code,” says Devin Perry, Executive Director of Business Improvement Programs at the National Association of Home Builders. “If they do that, modular construction can get locked out.”
Perry says it’s a shame because homes built using modular construction are built to the IRC, or International Residential Code, standards, and also conform to all applicable state and local codes. “They meet all the local building regulations of where they’re being set,” Perry says.
The point is that despite years of builders fighting against the negative image of manufactured homes, which are often referred to as “trailer homes,” the stigma persists.
Dave Endy, Chairman, Stratford Homes in Stratford, Wisconsin, says that several times he has spoken with developers and asked them to show him exactly what they think they’re keeping out of their community. “They envision a mobile home,” he says. “While even some mobile homes are nicer than site-built homes, people have an image of a rusting trailer that will bring down home values.”
The look of the modules when they show up on-site can also make the uninformed skeptical, as Kopper Creek’s team found out when its modular components were delivered. “People thought we were lying to them,” says Thomas, whose company adds customization to the homes on-site. And truth be told, he admits, that when they show up, they’re ugly. “The battle is won and lost on the site.”

Photo Credit: Stratford Homes
Seeking Approvals
Even where zoning allows modular, some builders have had trouble securing permits. While the approval process is more or less the same with modular and stick built, sometimes there are biases because there are a lot of individuals who are anti-modular. It’s not because they don’t like the product; it’s because they lack knowledge.
“It’s easier to say no than to sign off on something and approve it,” says Anthony Zarrilli, Founder and President, Zarrilli Homes in Brick Township, New Jersey. The hoops that modular builders have to jump through in his market seem designed to discourage them. “[Here], a building permit for a stick-built home is about two-and-a-half inches thick. A building permit for a modular is like a foot thick. It’s insane.”
Zarrilli says that the authorities have also been known to demand costly changes once construction starts, but that these can often be avoided with good planning. In fact, his company has a rule that no modular home can be ordered from the manufacturer until it has made it through the zoning process and gotten all the necessary approvals. “After zoning, it’s usually just something small, a GFI isn’t close enough in the kitchen, an oversized bedroom needs another window. These things are easy to modify.”
See You in Court
Sometimes, the issue must be settled by legal action. Endy tells the story of a couple seeking to purchase one of his company’s modular homes for a subdivision in Montana. The subdivision would not allow it because the CC&R (covenants, conditions and restrictions) stated that no modular homes could be built in the development.
“The couple brought a lawsuit in an attempt to get the developer to change the CC&R to allow the home,” Thomas says. The lawsuit went on for three years. On appeal, the homebuyers ultimately won, with the court saying the CC&R could place architectural guidelines, such as a requirement that the house be at least X number of sq. ft., have an attached garage, or have certain slope to the roof. “But it couldn’t have guidelines on how a home would meet the standards, which was essentially what they were saying by restricting modular builds.”
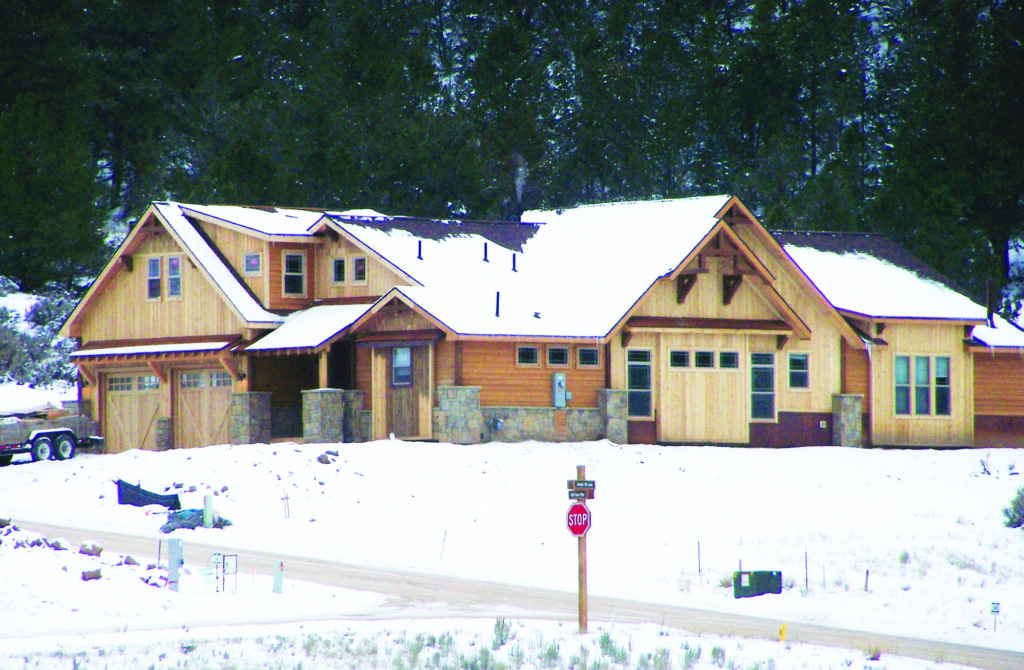
Telluride.
Photo Credit: Kopper Creek
It was a bittersweet win for Endy. “By the time the suit was successfully concluded,” he says, “the couple had moved on and never ended up buying the Stratford Home. But the outcome was helpful from our standpoint since now we could state that a court has ruled that you can tell us what to build, but not how to get there.”
Kopper Creek also lost one of its buyers because of the architectural control committee’s moratorium. “Ultimately, we threatened litigation against the HOA, and then we went to settlement,” Thomas says. “We used the buyer who canceled to reflect the losses we might incur.” The company was able to set their eight other homes and there is no longer a moratorium.
According to Perry, one thing that can help situations like those faced by Stratford Homes and Kopper Creek would be national standards. The industry has been working with the International Code Council to develop standards for modular construction that localities can adopt, and that would eliminate some confusion people have when it comes to modular. “The standards have been written and are going through the adoption process,” Perry says.
Another key is continued education of municipalities, developers and consumers. Perry advises builders to start working with local authorities well before the build starts. “If a modular unit gets shipped to a town, and it’s the first time the local building inspector is hearing about it, that’s where you’ll get questioned. If you’re proactive, the process is a lot smoother.”
Thomas says that upon reflection, although his PowerPoint presentation was well received, he should have really explained what was going to happen. “Stage one, show an image of the day the modular components show up on-site. Stage two, show the modules being put together, and stage three, show the finished project.”
Perhaps it’s just a numbers game. As more modular homes are built, zoning and permitting should become less of an issue. “We did a development just outside a ski resort town in Big Sky, Montana. It had 58 homes and the least expensive was $2.8 million,” Endy says. “If we can build that, we should be able to put a $300,000 home in a development without anyone asking if it will withstand the rigors of traditional site building.”
Stacey Freed is a freelance writer and editor based in Pittsford, New York. She focuses on construction, remodeling, real estate, sustainability and wellness.
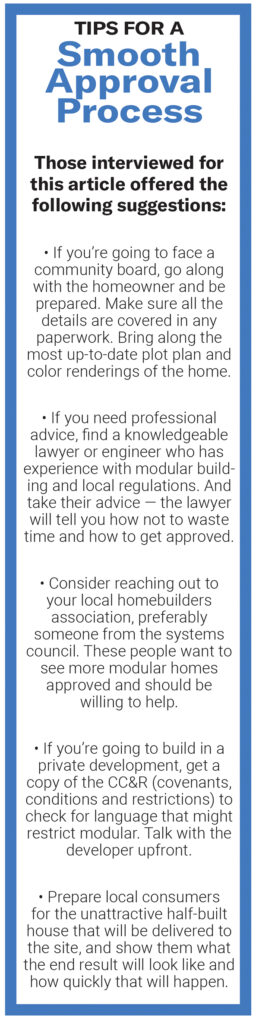