Tstud reduces thermal bridging and also offers other benefits
- This truss-like component consists of two framing members separated by dowels, which creates a space that can be filled with blown insulation
- An R20 wall framed with this product will actually be R20, a result that can’t be achieved with standard framing unless you install exterior foam
- This reduces the heating and cooling loads on the HVAC system
- Tstuds can be used as part of an on-site, off-site, or hybrid construction system
Most homes are built with traditional wood framing members—studs, headers, top plates and bottom plates. Wood is a great structural material, but it’s also a conductor. It allows heat to flow easily from the exterior to the interior, or vice versa, reducing the energy efficiency of walls and increasing heating and cooling costs.
To solve this problem, Iowa-based, US Engineered Wood has invented the Tstud, an engineered replacement for wood studs that improves the energy efficiency of buildings by acting as a thermal break. It consists of a pair of 2×3 and 2×4 pine studs separated by dowels, making it look like a truss of sorts.
The company used to sell a version of the Tstud in which the gap created by the dowels was filled with foam insulation. However, due to supply chain issues and shutdowns, they had to temporarily stop making them. For now, they only manufacture an uninsulated version called the “BareNaked” Tstud.
In this article, I compare traditional wood studs and Tstuds in terms of dimensions, performance, feasibility and price.
How They’re Made
Tstuds can replace most framing members, including wall studs, top and bottom plates, and king, jack and cripple studs.
The lumber used to make Tstuds is manually inspected and only the highest quality members are used; those that are straight and don’t have large knots or cracks. A machine then drills the needed holes, pre-glues the dowels and then shoots them through one member and into the other at opposing angles, forming a web-like pattern. The 2x members are perpendicular to one another, so the finished product has one wide and one narrow surface, like a ‘T’.
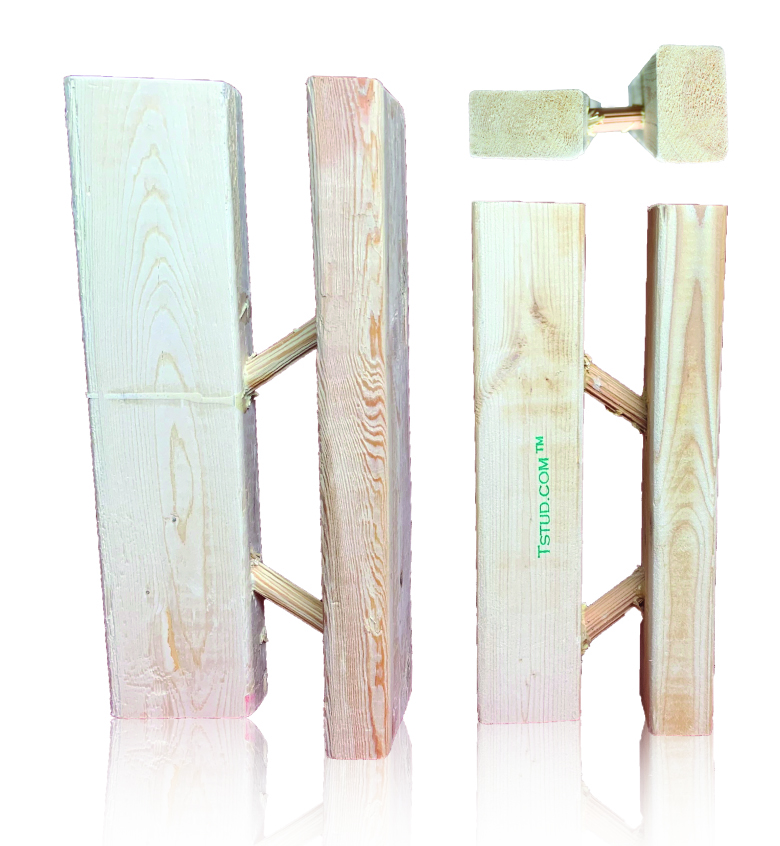
This allows for some versatility in construction and installation. If you need more surface area on the outside to secure sheathing and rigid foam insulation, the wide surface can face the exterior. If you need more surface area on the inside to secure cabinets and shelves, simply install the Tstud with the wide surface facing inward.
Product Specs
Relevant specifications that architects and builders will be concerned with are as follows.
R-Value
About 25% of a traditional wall consists of wood studs that act like a thermal bridge. Even if you install R20 insulation in between the studs, the effective R-value is reduced to as little as R15. Builders typically deal with this by installing a layer of exterior foam insulation.
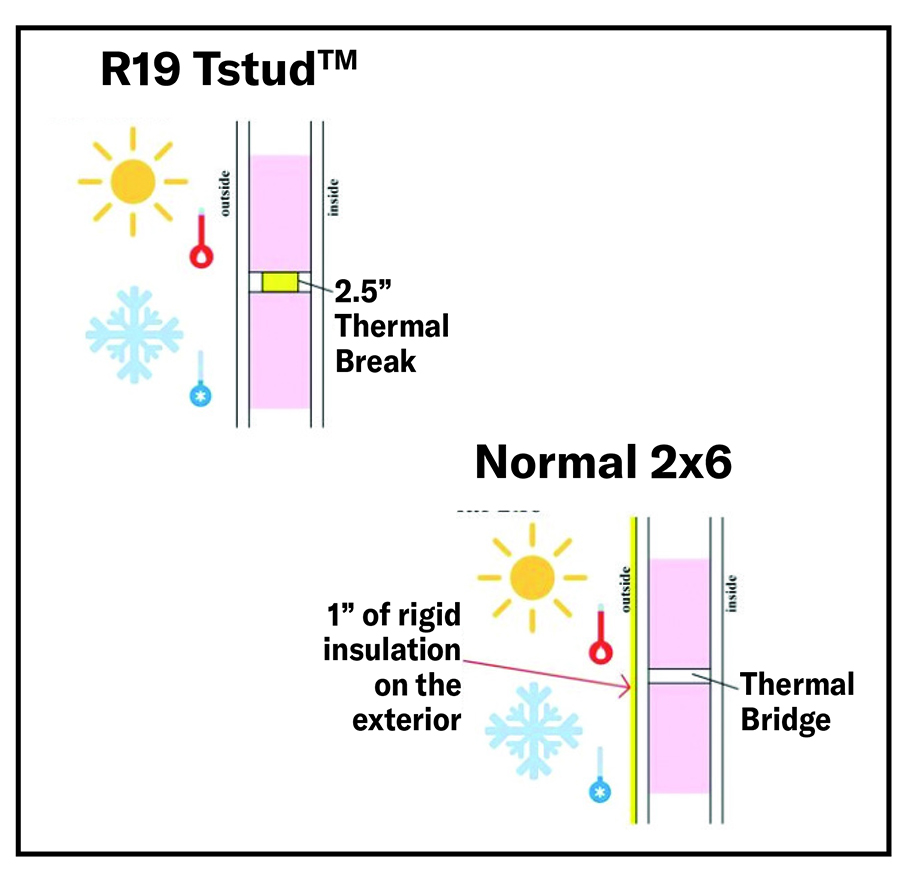
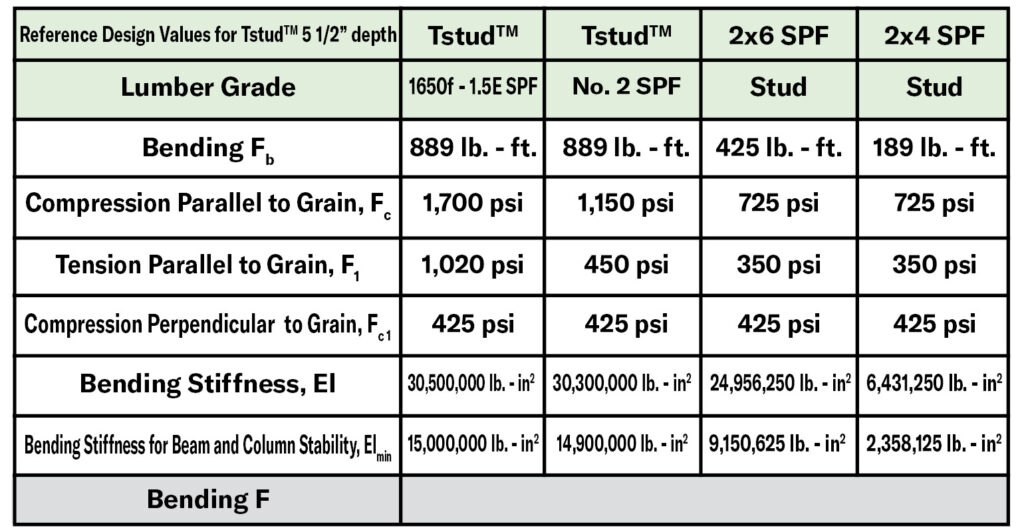
The result is a wall with a higher load carrying capacity. While a 2×4 can hold 900 lbs. and a 2×6 stud can hold 2,200 lbs., a Tstud can hold 8,600 lbs.
Utility Runs
In addition to reducing thermal bridging, the gap in the Tstud is a huge advantage when it comes to running utilities. Instead of hacking through perfectly good studs, wires and PEX piping can be run through the gaps in Tstuds without compromising their structural integrity. If the plumber needs to run larger PEX pipes, an inch can be cut from the outer stud.
Installation and Cost
Installing Tstuds is very similar to nailing traditional studs, so there is a minimal learning curve associated with them.
One thing that is different is the fastening of Tstuds to the subfloor. Instead of a threaded J bolt or lag bolt, you need a wide plate that straddles the two wood studs and transfers its hold-down power.
As for cost, Tstuds are obviously more expensive than traditional studs, but their increased cost is offset in a few ways:
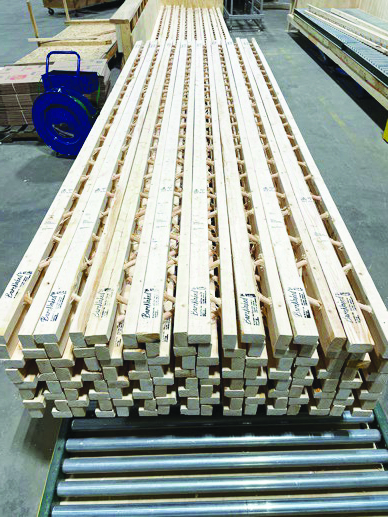
Less waste. About 5% of traditional studs are usually too warped and damaged to be used. On the other hand, less than 1% of Tstuds are unusable.
Wider stud spacing. Tstuds can be spaced 24 in. on center instead of 16 in.
Reduced weight. A Tstud wall is lighter than one framed with traditional studs, which can lower the cost of other framing members and even the foundation.
Energy savings. By eliminating the thermal bridge in your walls, the interior space is essentially unaffected by the temperature outside. In this way, Tstuds help lower the energy consumption of your HVAC system.
Conclusion
One downside with this product is that it takes up more interior space because it’s as deep as a 2×6. It may not be usable in tight enclosures where every square foot counts. It’s also not a good choice for interior walls because of the added expense and because thermal bridging is not an issue inside.
Tstuds are not the only way to create a thermal break; you can also use continuous exterior insulation, or strips of insulation on wood studs. However, I admire the role of Tstuds in raising awareness of the problem of thermal bridging and the need to address it.