This industry insider believes the North American market could potentially support thousands of mass timber fabricators. But getting there will mean overcoming some challenges.
- Mass timber buildings are fabricated in a factory, and then shipped to the jobsite for assembly. They can be engineered with strength equivalent to steel or concrete, but with the look and feel of real wood.
- Although this has promise and is well established in Europe, challenges in North America include a shortage of people with the right skills.
- Fabricators like CutMyTimber take the architect’s design and create a digital model that can be used by all project partners.
- The complexity of this way of building means that bidding has to be done differently than on conventional projects.
Although mass timber is still a niche type of construction, it’s growing. In June of 2022, WoodWorks — a non-profit organization that supports the wood industry — reported that over 1500 mass timber buildings have been completed, are in design, or are under construction in the United States. This versatile building technology has a wide range of applications, from custom homes to high-rises.
Mass timber buildings use large, engineered or solid-wood structural members—panels, columns and beams—that are fabricated off-site. Those members can be engineered with strength ratings comparable to concrete or steel, but weigh less.
Ascent, a 25-story, 284-ft.-tall apartment building in Milwaukee, Minn. became the tallest timber building in the world upon its completion in July 2022. This and other high-profile projects have prompted mainstream media outlets like Fast Company to ask if a mass timber construction boom is on its way.
To learn more about this construction technology, including its potential and challenges, we talked with Greg Howes, Business Development Partner at CutMyTimber, a fabrication company that works with a network of architects, structural engineers, builders and other fabricators to supply custom-manufactured mass timber products including timber frames and glulam beams.
CutMyTimber isn’t a primary manufacturer; instead, they do the detailed work on wood products purchased from primary manufacturers. These products include glulam and other engineered beams, solid timbers, cross-laminated timbers (CLT), mass plywood panels and steel connectors.
Howes co-founded the company in 2010. Its head office is in North Vancouver, British Columbia and its manufacturing plant is located in Portland, Oregon.
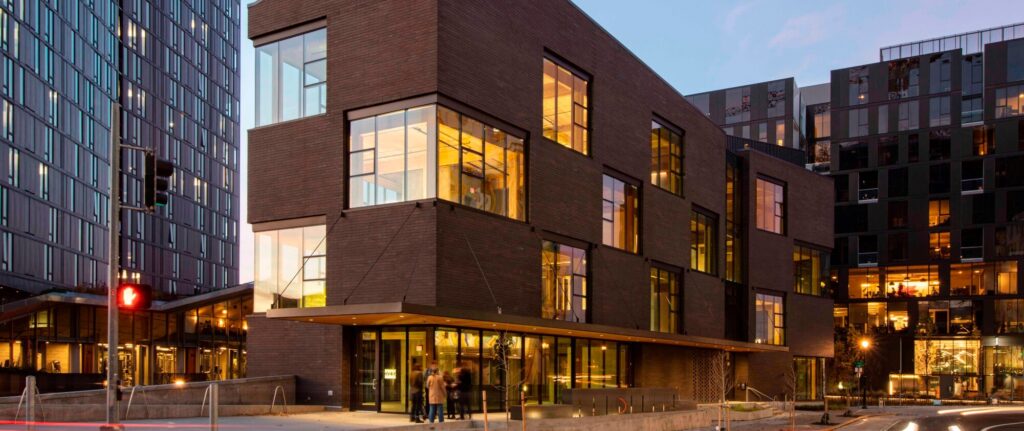
The Nice and the Demand
While mass timber’s strength is appealing, Howes says that the main driver behind its growth is that people like the look and feel of wood. It’s natural and it’s sustainable. “Many people prefer wood to concrete or metal, even though every building is a hybrid of different materials.”
Where is this technology best used? Howes acknowledges that if it’s a low-cost building, with a simple, blocky design, then mass timber isn’t going to be cost-effective. It’s most appropriate where the building is geometrically complex, and where exposed wood is a major part of the aesthetic.
CutMyTimber is typically approached by architects, construction companies, structural engineers, building owners and developers who want that particular aesthetic. They might want to build a new ski resort, but they know there are better approaches than dumping a pile of wood on-site and asking the contractor to figure out how to cut and assemble it. They want to use wood, but they also want efficiency.
While there aren’t many companies supplying custom mass timber in North America, demand is high and everyone is busy. Howes gives the example of Nordic Structures, an engineered wood company in eastern Canada that CutMyTimber has worked with. “They do design and fabrication, and they coordinate assembly and installation. They’re booked out for two years.”
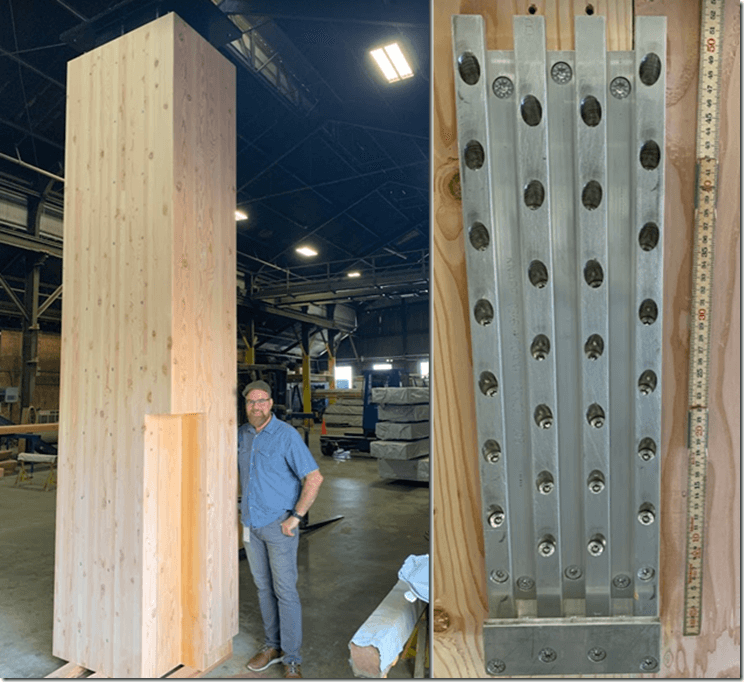
The Process
In the dozen years since its founding, CutMyTimber has worked on over 100 projects, from custom single-family homes to large commercial buildings like stadiums and casinos. Currently, they’re working on a new terminal for Portland International Airport. “This $2 billion project has lots of custom-fabricated glulam beams, plus tens of thousands of smaller wooden parts. We’ve been fabricating a lot of the smaller parts in very large quantities and many of them are unique,” Howes says.
Their role in each project varies, depending on the partners involved. For one project, they might deliver a large number of massive glulam beams and order SIPs (Structural Integrated Panels) from a supplier. On another project, they might simply fabricate a decorative truss for an entryway.
However, the process is consistent from project to project. Working from the architect’s model, CutMyTimber creates a completely new digital model specifically for fabrication and assembly. It includes all the fabrication details such as cuts, slots, holes and milling.
The digital models and underlying data are readable by various machines that different fabricators have. This ensures that components made from different materials fit together when delivered to the construction site.
As much as logistically possible, CutMyTimber puts assemblies together in its plant to make sure the fasteners all fit and everything lines up properly. Then they load everything onto trucks in the reverse order of how they will be installed by the general contractor, or GC. They provide installation drawings with the kits and can provide site supervision or assistance if necessary.
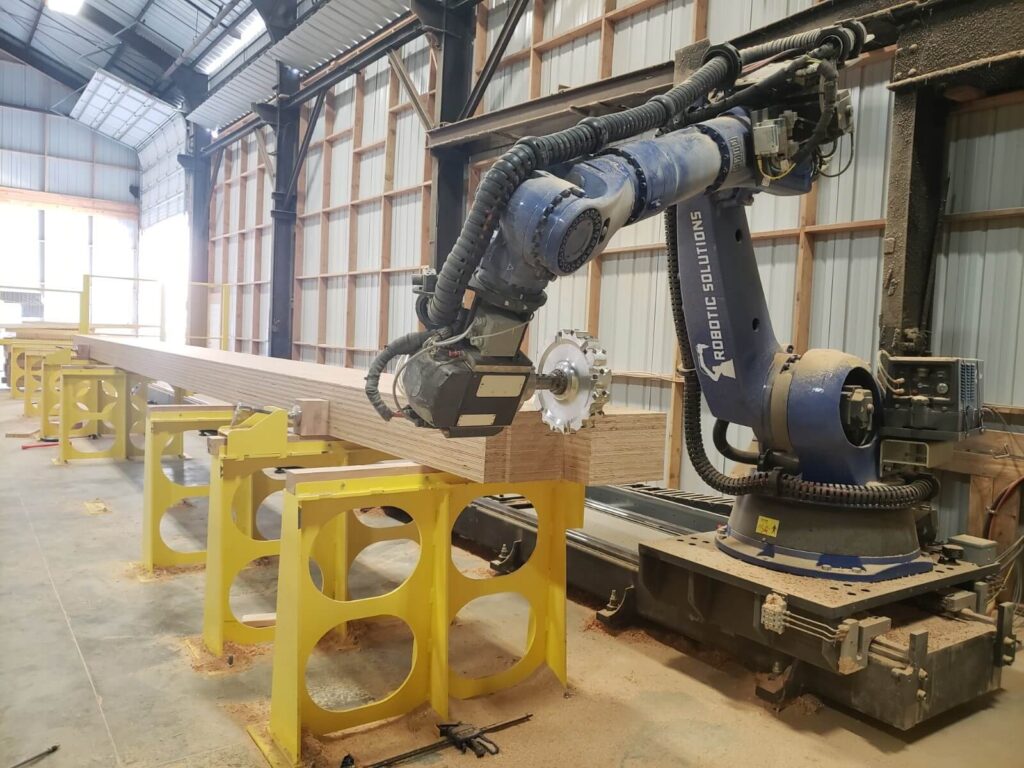
The Challenges
Industrialized construction in general, and mass timber more specifically, are relatively new to North America, but are well established in Germany, Austria and Switzerland. Howes says that most of the machines and software used in the mass timber industry originated in those countries.
Howes goes on to say that the experience of those countries makes him optimistic about mass timber’s growth potential. “Switzerland alone has more than 50 mass timber fabricators with more than 50 employees in a country of just eight million people and where about 10% of the buildings are wood framed.”. He believes the North American construction market, which is far larger, could support thousands of mass timber factories.
However, there are challenges to be overcome. One of these is the shortage of industry expertise. “In Switzerland, for instance, many architects and builders have worked on dozens, or hundreds, of mass timber buildings,” says Howes. Teams in Europe might work together many times and become a well-oiled machine. That level of experience is rare in North America at this point.
“Often, on each construction project in Canada or the US, a new team comes together — a new architect, a new contractor, a new structural engineer, new suppliers, new trades and so on,” Howes says. “And then the project finishes and it’s on to the next one with perhaps an entirely new team.” Working with new teams each time makes it hard for lessons learned on one project to be efficiently passed along to the new project.
Educational and research organizations can help fill this gap. Current institutions include the International Mass Timber Alliance, the Centre for Advanced Wood Processing at the University of British Columbia, the Wood Innovation and Design Centre at the University of Northern British Columbia and the Tallwood Design Institute (a collaboration between Oregon State University and the University of Oregon). Howes says they’re all doing good work, but that North America still needs more education and research.
Another challenge is the current design process. The architect’s model typically doesn’t contain the level of detail or the right kind of data for fabrication. “It would be great if architects could model in Cadwork instead of Revit because they’d be speaking the native language of the mass timber machines,” Howes says. “That does happen quite often in Europe, but not here in North America.”
Once CutMyTimber receives an architect’s model in software like Revit or Rhino, they don’t import it. They use it as a reference, but have to completely re-build the model from scratch in CAD/CAM software such as Cadwork, which creates data various fabrication machines can read. “The model needs to tell the machine where and how to cut, drill, and slot,” says Howes. “The most advanced robots in the world only do what they’re told.”
CutMyTimber shares this model with all project partners, such as companies that fabricate custom steel parts or Cross-Laminated Timber (CLT) panels. This puts everyone on the same page. “If different companies use different models to fabricate various parts for the same building that would be a recipe for disaster,” Howes says. The required level of precision demands that all parties work from the same model.
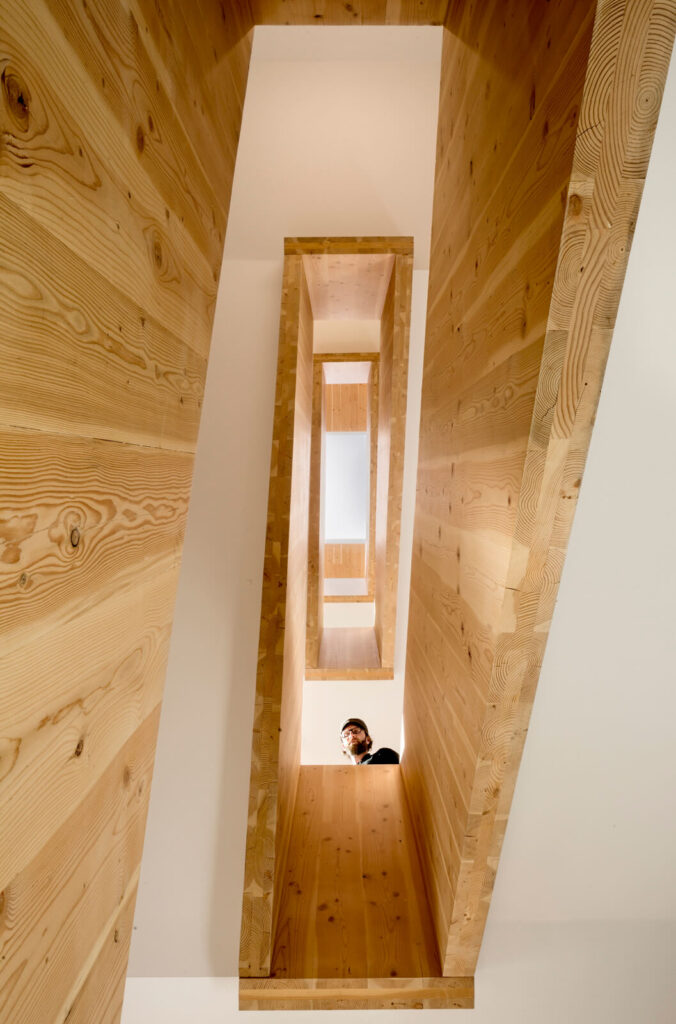
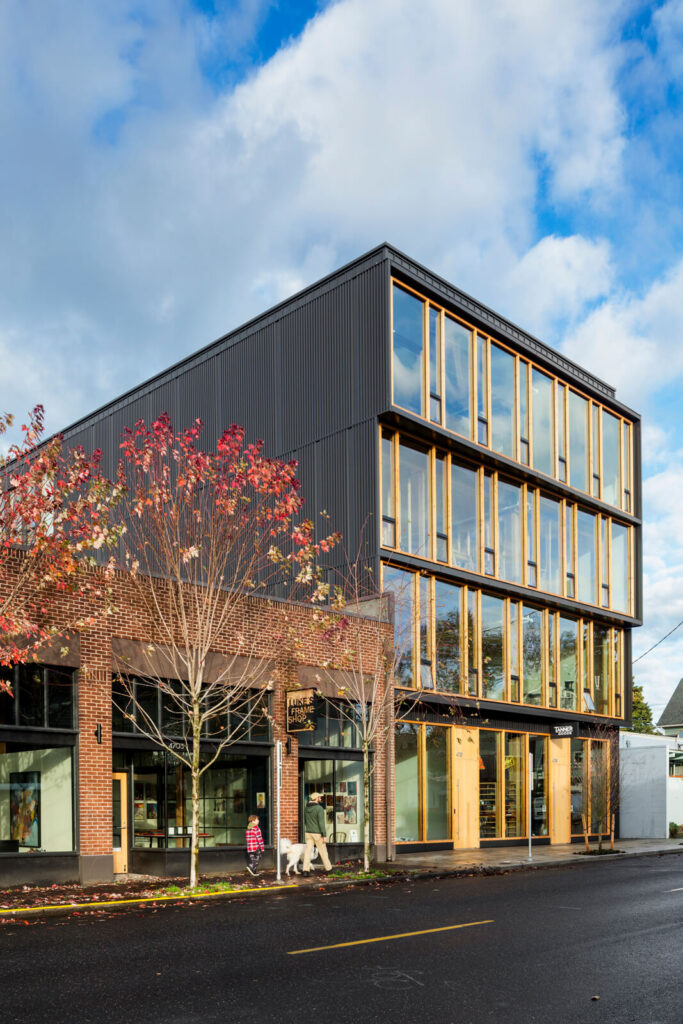
The Bidding Problem
Understandably, people want to know what mass timber costs, but Howes explains that a glulam beam or a CLT panel can’t be accurately priced without knowing how it’s going to be customized. And, because the customization might be very different on each project, the previous pricing may not be relevant. This makes the traditional construction bidding process inadequate.
Imagine that an architect has designed a 10-story mass timber building. The renderings are beautiful and the layout is defined, and so GCs are asked to bid on the project. But the architect’s model doesn’t give GCs nearly enough information. “It doesn’t tell you what size beams will be needed, what kind of wood will be used, the thickness or the grade of the CLT, how the beams will attach or to the concrete elevator shaft.” An accurate price can be generated only after a detailed fabrication model has been created.
At the same time, a company with lots of experience can look at an architect’s design, consider its complexity and make a rough time and cost estimate. “Our team has worked enough buildings that we know the difference between the simple process of chopping off a length of glulam beam compared to a curved beam that has many holes and slots drilled into it that has to fit with many complex metal connectors that all have to be accurately custom-fabricated,” explains Howes.
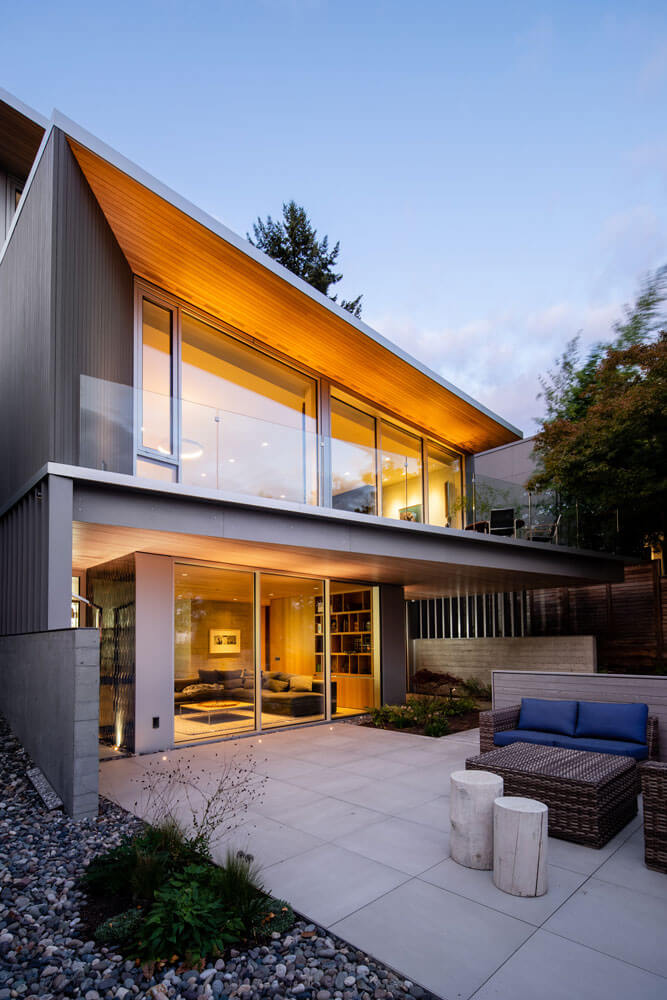
A Range of Skills Needed
He adds that it’s important to know what parts of the process should and shouldn’t be automated. “We use cutting-edge software, five-axis CNC machines and advanced Kuka industrial robots, but all our projects also involve traditional craftsmanship.”
Using hand-held tools for tasks like sanding and finishing is often more efficient than using a CNC machine — and in many cases, machine processing is not possible or not cost-effective. “By far the most important thing you need for success in this industry is people with the right skills.” And that’s the case whether those are trade skills, managerial skills, or tech skills.
Whether a company fabricates with wood or steel, or whether they’re 3D-printing with concrete, “there’s an extreme need to hire people who can take design data and translate it so machines can use it,” Howes says. “If I knew where to find these people, I would hire all of them tomorrow, as would many other companies.”