How can bottlenecks be prevented on your factory’s floor?
Sometimes, the simplest questions are the most difficult to answer. For example, production bottlenecks. There are many reasons why bottlenecks occur in modular factories and those reasons may be systemic.
To fully understand the causes of bottlenecks and how to curtail them, you need to look at the fundamentals and function of the factory. Long-term solutions can require changes to production systems, plant infrastructure, personnel training, product mix, the materials used and the quantity of materials kept in stock.
We spoke with several modular manufacturers to see how they have reduced bottlenecks and streamlined their production lines. They offered the following advice:
1. Focus Your Production Lines
Donald Aheron, General Manager of Nationwide Custom Homes (Nationwide) in Martinsville Virginia, credits his company’s mitigation of bottlenecks to its dedicated component plant. The Nationwide component plant has been around for decades and has proven its worth — the building of sub-assemblies offline makes the modular production facility more productive.
The component plant supplies the parent facility with vital pre-cut lumber and assembled components that include pre-cut rafters, studs and joists, as well as pre-assembled turn gables and dormers. The component plant also fabricates on-site countertops, builds door jamb assemblies and paints trim and doors.
“The component factory allows us to do custom work and maintain a high level of quality while keeping a consistent workflow,” Streamlining Production(LDR) Aheron.
Nationwide also avoids production line bottlenecks with its plant’s design. The factory has three production lines, which are designated as A, B and C. Each is set up to handle a different type of work.
During the production scheduling meeting, the first thing the plant manager and supervisors decide is which line a home will travel along. For example, the C line may be relegated to customized homes that have unique designs, or that require special materials or a specialized plumbing layout.
2. Stock More Inventory
Recent supply chain shortages have also led Nationwide Custom Homes to grow its existing inventory of materials. Previously, there was a two- to three-week supply of stocked building materials; today, they have grown that inventory to eight to 10 weeks. This inventory includes unassembled cabinets that are stored until they are needed on the production line.
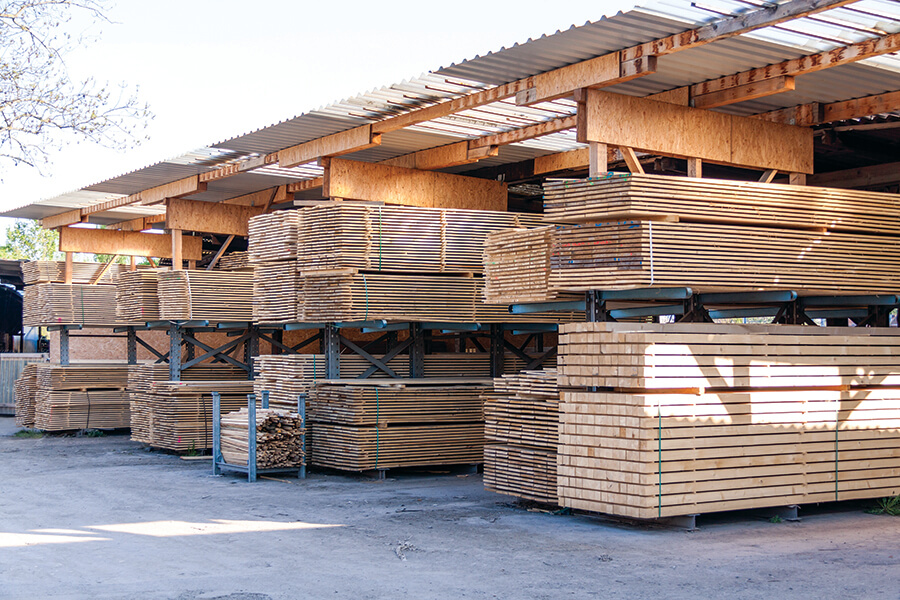
3. Control the Product Mix
Not all companies have the luxury of multiple production lines. One of these is Rochester Homes in Rochester, Indiana. Tyler Anderson, o-owner and Vice President of Production says he would love to add 15,000 sq. ft. of space for additional production lines, but that changing his plant’s infrastructure isn’t in the cards right now.

Photo Credit: Guerdon Modular Buildings
The 50-year-old company, which Anderson’s grandfather founded, currently has one manufacturing line. The way he mitigates bottlenecks is by controlling his product mix.
The company tries to schedule its production so that homes moving down the line at any given time are as similar as possible. Anderson considers three major factors when evaluating his running order: “the average length per floor, the cost per floor and the product type.”
When bottlenecks do happen at Rochester Homes it is typically in the center of the plant where ceilings and roof assemblies are constructed. “A lot is going on at that station,” Anderson adds.
4. Centralize Storage
Eric John, co-owner and Vice President of Production at Ritz-Craft Corporation in Mifflinburg, Pennsylvania, says that the causes of bottlenecks are multi-faceted and that solutions are never simple. Better planning and seeking out the hidden issues that can cause delays are important, John says. That includes ensuring proper material handling and storage.
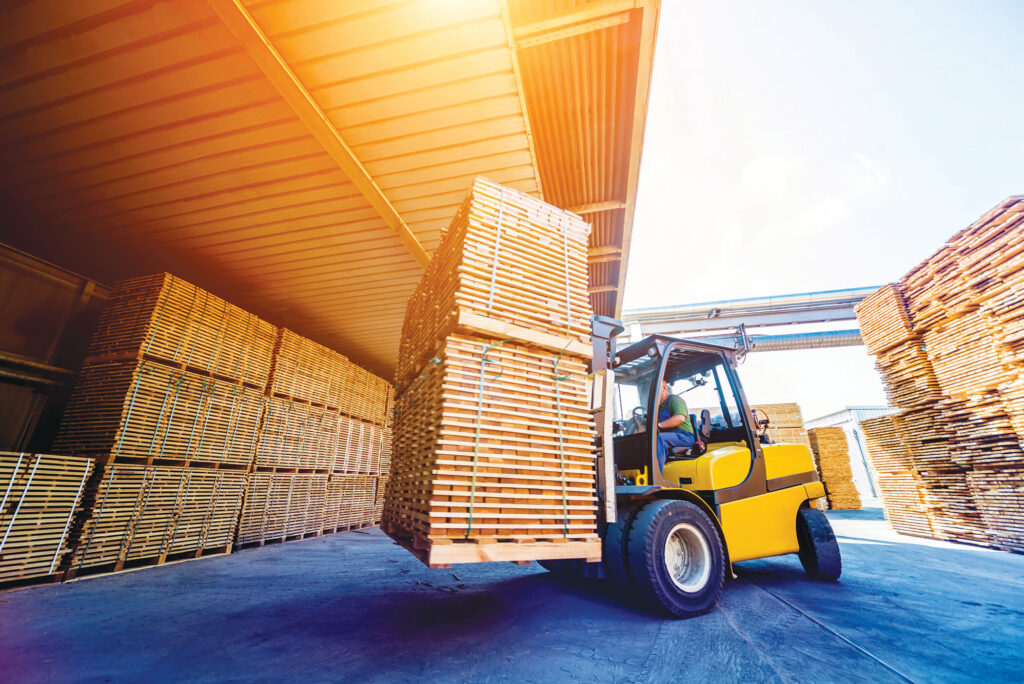
“All day, you have operators on their forklifts delivering material to the line,” John says. “If they are five or 10 minutes late, guys are just standing around waiting. What if that happens a couple of times a day? How much time are you wasting?” To quicken the pace of production, John has created a system where materials are staged in a central storage facility and then quickly delivered to relevant stations when needed.
5. Pre-Build Assemblies
The company also makes sure that pre-cut floor joists and other framing members are stacked next to assembly stations before the upcoming production week.
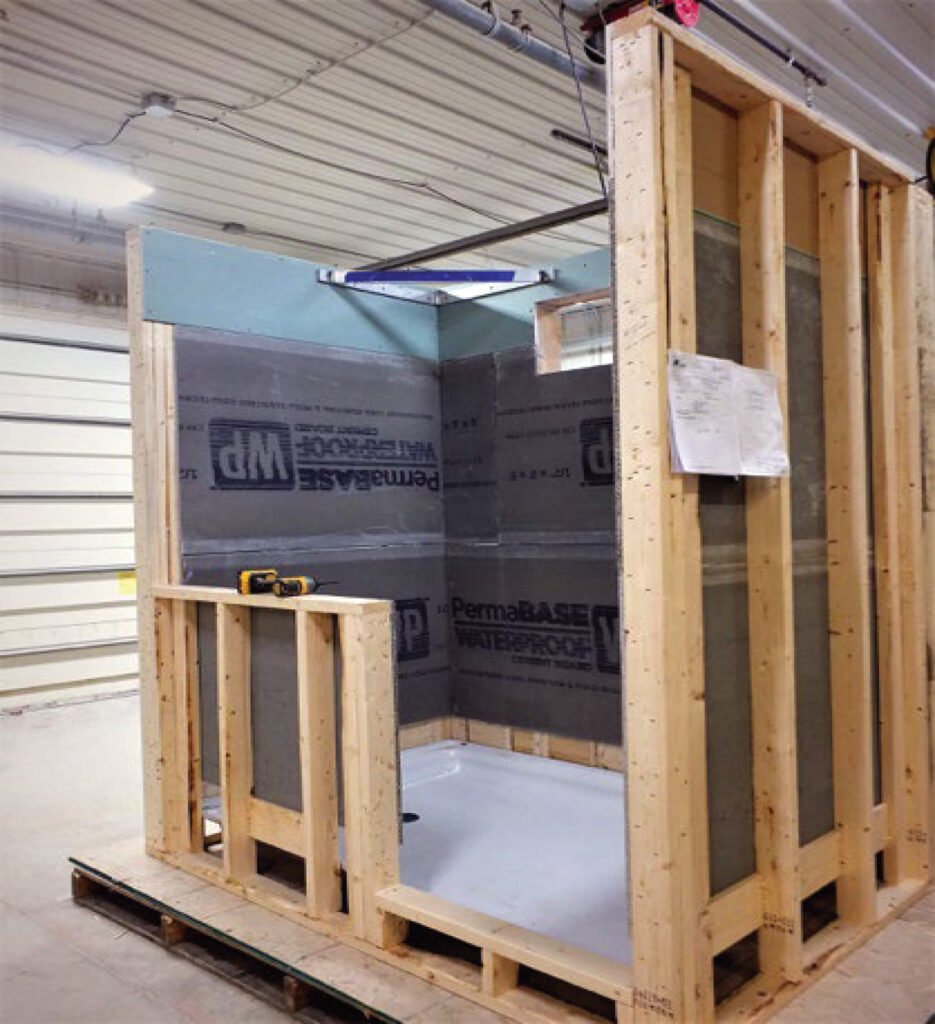

Photo Credit: Ritz-Craft Corporation
Recently, John and others traveled to Sweden to tour the Lindbäck modular production facility, where large-scale automation is being used. The Lindbäck factory builds products for its own projects that include a lot of repetitive designs and dimensions.
Because Ritz-Craft does semi-custom work, full-on automation isn’t applicable. However, the application of bathroom pods was something John says he liked and Ritz-Craft has begun manufacturing shower pods offline. This is a time-saver on the production line, partly because line workers no longer need to do tile work, which is a bottleneck in many factories.
If Ritz-Craft has a silver bullet in avoiding costly delays, John said it would be its cabinet subsidiary, Legacy Crafted Cabinets, which builds all its own cabinets and does its millwork.
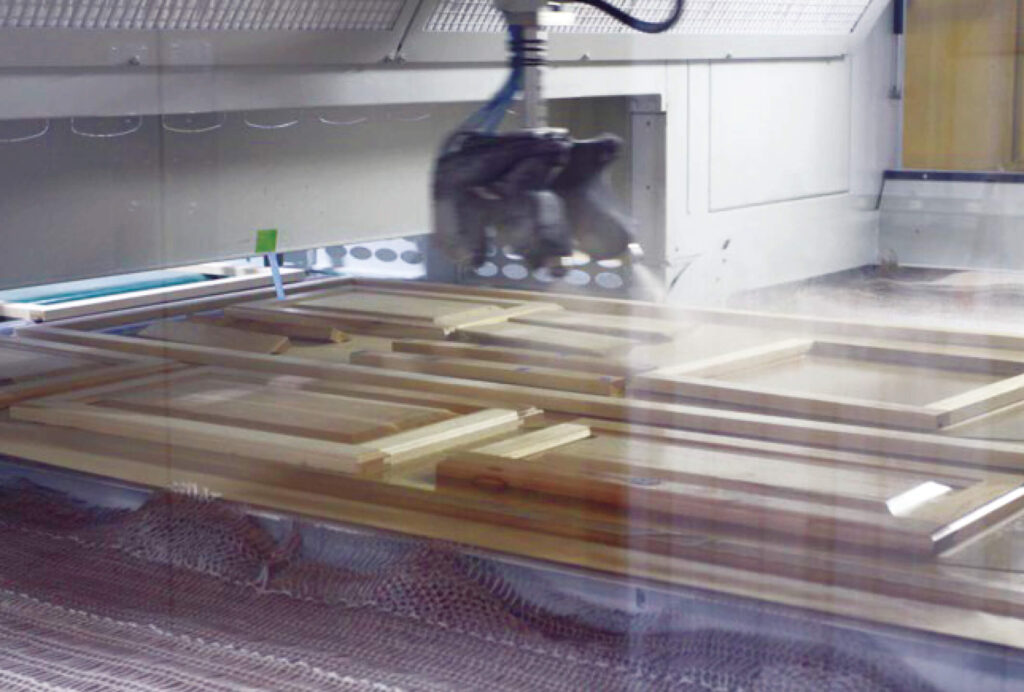
Photo Credit: Ritz-Craft Corporation
“If a builder wants a totally different crown molding profile than we currently offer, we can do it,” John says. Legacy Crafted Cabinets has a fully-automated stain and finish line where custom cabinets can be fully assembled and ready for installation minutes away from Ritz-Craft’s Mifflinburg manufacturing facility.
6. Move Drywall Offline
Over the span of his long career in the modular industry, Tommy Rakes, CEO of Guerdon Modular Buildings located in Boise, Idaho, has seen both the differences and similarities between single-family and multifamily modular construction.
He finds that bottlenecks occur in essentially three areas: “Most volumetric modular plants are designed in a similar fashion,” Rakes explains. “Bottlenecks usually happen in roof build sections, roof storage [when roofs are stored prior to being installed] and drywall stations.”
Factory completion of drywall takes time. Rakes states, “To have throughput you must have the correct percentage of modules fully drywalled and ready to paint. This means you need to create room in the production line to spread out the finishing process.”
Rakes says that many factories lack offline drywall finishing sub-assemblies. Adding this capability will help prevent line delays and increase production capacity.

Photo Credit: Guerdon Modular Buildings
7. Break Some Conventions
Delays in multifamily production often occur for different reasons than for single-family production. Those delays are mostly in HVAC installed in ceilings, as well as mechanical, sprinkler, electrical and plumbing work.
Vic DePhillips, a 49-year veteran of the modular industry and President of The System-Built Group LLC, Scranton, Pa. has concluded that the biggest adversary is time.
The ability to manufacture two additional boxes per week brings the manufacturer more annual revenue. It also gets projects done faster, which saves financing costs for the developer and, in the case of a for-rent project, gets tenants into the building sooner.
DePhillips has spent his career looking for ways to save time by adjusting practices and processes on production lines. Specific to modular building, “People keep doing the same things they did in 1973,” says DePhillips, who says one of his favorite books is If It Ain’t Broke, Break It, by Robert J. Kriegel and Louis Palter. “People get stuck in a paradigm and don’t look at ways to do things better and more efficiently. My ultimate goal is to produce a good, deliverable price-competitive product that meets quality expectations.”
At his former company, DePhillips changed the procedure for the floor framing so that the framing jig was moved to the side of the line. The point of doing this was that the next floor system could be built on the jig and then quickly lifted into place when needed. Workers would need only glue and nail the floor panels.
A lot of bottlenecks occur in ceiling and roof assemblies. In the past, DePhillips has created redundancy by adding additional ceiling and roof jigs and moving them 100 feet offline. He has also saved time by pre-drilling the floor framing for rough plumbing.
Whatever system you use, employee cooperation is essential. DePhillips stresses that employees in the factory must be “in-sync” with each other and must use standard operating procedures (SOPs). “If one person is out of sync that throws off everybody,” DePhillips says.