Circular Economy (CE) is an approach to business that accelerates the transition towards sustainable construction while providing companies with additional revenue streams.
- CE thinking builds on Lean principles. In fact, the author calls it the next step in the evolution of Lean.
- A transition model developed by the Circular Supply Chain Network includes seven phases that can be taken in any order.
- A company need not commit to all seven phases; any one of them will get it onto the CE path.
Construction accounts for more than 30% of natural resource extraction and 25% of solid waste generation, globally. These problems can be attributed to the dominant linear economic model of “take, make, waste.”
A more environmentally and financially sustainable alternative — one that’s a great match for offsite prefabricated construction — is the Circular Economy (CE) model. In this approach, the builder/manufacturer uses interconnected systems to maximize resources, and reuses end-of-life materials to create material banks for new construction projects.
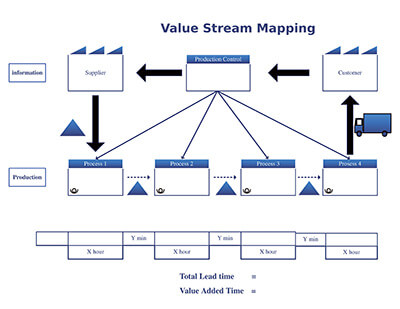
CE is an evolutionary step in that it expands on the time-tested principles of Lean manufacturing/construction. But while Lean focuses on minimizing waste, CE attempts to monetize it. In effect, waste becomes another source of profit.
Challenges to achieving CE in the construction industry include unique projects and complex supply chains. The repeatable designs and supply chain simplification that come with prefab ease these challenges, but don’t eliminate them. To help companies get on board, this article introduces a transition model developed by Circular Supply Chain Network (see Figure 1).
The model has seven phases, and companies can get started with any one of them before adopting others. I have included real-world examples of companies that have done so, and I offer some insights on how to incorporate them into your transition process.
Phase 1: Identify. The first step in any process improvement effort is to define the materials and resources that are involved in the process. A valuable Lean exercise is “Value Stream Mapping,” which offers visibility into the value and the waste streams of your business cycle. (For more information see “Value Stream Mapping” by Daniel Small in the December 2022 issue of Offsite Builder.)
For instance, in commercial projects that use flooring composed of hot rolled steel sections welded together, this phase would include meticulously tracking the quantity of raw materials used, as well as the cuts made in the steel. This analysis provides valuable insights into material use efficiency and can be applied to other materials and project types.
This stage should also include a close look at waste management practices. It should be obvious that waste generation can be effectively minimized and contained in an offsite factory setting. There are opportunities to reduce waste during installation, storage, on-site segregation, transfer and final storage of raw materials, as well as of finished products like modules.
Best practices include on-site waste segregation, well-defined acceptance criteria for waste and quality standards for recycled materials.
Phase 2: Intensify. This phase is about using materials in ways that extract their highest value. Let’s consider the example of a shipping pallet that’s used just one week per month — a utilization rate of just 25%. The aim should be to increase the utilization rate as much as possible. Ways to do so might include sharing the pallet between different parts of the company or different members of the supply chain.
A specific example would be galvanized steel ceiling and roof components that arrive at the factory on purpose-built racks. These racks can be returned to the suppliers for reuse.

Photo credit: Vandkunsten Architects
Phase 3: Narrow. This phase is about reducing the number of resources needed to do the work. In the manufacturing plant, these resources include water, gas, building materials and other consumables.
Phase 3 thinking can also be used in the design of finished products. One system that has fully embraced it is Passivhaus, a low-energy design standard that ensures year-round comfort with minimal active heating or cooling. It relies on passive contributions from solar radiation and internal heat generation.
Phase 4: Predict. Here, we are accurately forecasting the availability of materials and resources across the supply chain network.
While we already use forecasting to manage demand, the CE approach also includes the forecasting of how much waste will be generated, and of what type.

Photo credit: Vandkunsten Architects
A useful tool in this process is Building Information Modeling (BIM) technology. Rapid generation of 3D models allows instant computation and graphical presentation of waste generation on a dashboard, alongside other project performance metrics. By validating designs early on, the use of BIM can help minimize waste resulting from improper design and unexpected changes during construction. BIM can also contribute to waste reduction by supporting Lean construction practices.
The Predict phase includes coming to an understanding of how others can use our “waste” materials and resources. We want to look for and serve companies who are interested in purchasing that waste as a valuable resource. Not only does this reduce the amount of waste going to the landfill, but it also opens up a new revenue stream.

Photo credit: Vandkunsten Architects
Phase 5: Slow. This phase is about finding ways to extend the lifespan of the products that go into our buildings. Modular building designs that combine parts with similar expected lifespans offer an excellent example of how we can achieve product longevity. It avoids the necessity of having to demolish a building when some, but not all, parts of it have worn out.
Another proven way to extend product lifespan is by refurbishing existing buildings rather than building new ones. Materials like brick, wood and steel members, and carpet tiles offer greater potential for reuse or refurbishment (compared to materials like cement, concrete, mortar, and plaster, which often must be disposed of in landfills).
Phase 6: Close. This phase consists of looking for ways to use secondary or regenerative materials and resources. It’s about matching material uses to needs, and introducing substitute materials where appropriate. This phase also includes activities like the identification of scrap materials and the development of marketplaces for such materials.

Photo credit: Falcon Structures
One example is Yorkon, a company based in York, UK, that makes wall panels. It reuses and recycles 65% of its generated waste. Excess steel components are sent for recycling, and unused insulation is repurposed for use in modular buildings. As a result, the production and assembly of wall panels sends zero waste to the landfill.
Another example is a Passivhaus system (part of an affordable housing program) that’s being used in Scotland, UK. It includes insulated wall panels with mechanical fixings that are made in a way that allows for easy dismantling and reuse of materials like mineral wool, OSB boards and insulation.

Photo credit: Vandkunsten Architects
Phase 7: Capture. This involves sourcing and transforming available and affordable secondary materials for supply chain operations.
This phase embraces the concept of upcycling, for instance the use of cross-laminated timber (CLT) to replace materials with higher environmental impacts. The focus in this phase should be on enhancing the performance of alternative materials, making it practical to use them in place of more environmentally impactful primary resources.
Companies like Falcon Structures, based in Manor, Texas, for example, use repurposed shipping containers for modular structures. Containers offer quick and cost-effective solutions for applications that include offices, homes and even medical facilities.

Photo credit: Vandkunsten Architects
This article should make clear that Circular Economy, or CE, is a way of thinking that can be entered into at any of the seven phases, and that can bring many benefits to companies that embrace it. It should also be clear that CE principles can accelerate the transition towards sustainable construction, and that a controlled factory environment, like an offsite factory, provides the ideal platform for CE.
For more information on CE, please go to https://ellenmacarthurfoundation.org/topics/circular-economy-introduction/overview.
Sneha Kumari is a California-based, Lean/Six Sigma and Circular Economy expert. She has been recognized as one of the few Operations Women Leaders by McKinsey & Co. Please follow her work on LinkedIn.