Good analytics will help you navigate your way to offsite construction excellence.
In the dynamic world of offsite construction, the compass steering us toward excellence now comes in the form of data-driven decision-making. In fact, the industry stands at the precipice of a transformative era where harnessing the power of analytics can propel a factory towards unparalleled efficiency and innovation.
Consider this article as a call to action. It’s a call to make data-driven decision-making the cornerstone of your factory’s optimization journey.
Data Collection and Integration
We all know that the world is teeming with data, but that begs the question of how to manage it. The answer is that the art of data management lies not just in its collection, but also in the act of weaving it into a coherent narrative that illuminates the nuances of your factory’s operations.
Imagine a Gemba walk, a Lean method that managers can use to observe and improve processes on the shop floor. (For more information see my article on the topic in the October 2023 issue of this magazine). Now imagine extending that process beyond the factory, using it to analyze diverse data sources, from supply chain metrics to employee productivity statistics.
Integrating this mosaic of information is about connecting the dots to reveal patterns, correlations and opportunities for improvement. Do it right, and you will be rewarded with a panoramic view of your factory’s ecosystem, allowing you to make decisions grounded in integrated data.
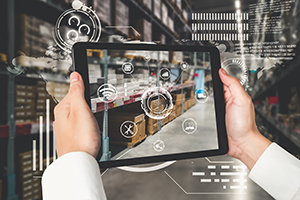
Consider the analogy of a modular construction project. Just as each module seamlessly fits into the grand design of a building, each piece of data helps form the backbone of your decision-making architecture, ensuring that every part of your factory works in harmony with every other part.
Analytics Tools and Techniques
You can think of analytics tools as the architects of efficiency in your factory’s blueprint. From Business Intelligence (BI) tools that help you visualize data to Machine Learning algorithms that facilitate data analysis, these tools transform raw data into actionable insights. It’s not merely about numbers; it’s also about understanding the story they tell.
This is the process by which we refine decision-making. An example would be BI-generated dashboards that enable real-time KPI tracking, thus increasing the speed and accuracy of decisions. By providing meaningful insights about each part of the operation, analytics become your factory’s superpower.
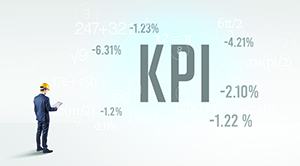
Let’s delve a bit deeper into this toolbox. BI tools, like Tableau or Power BI, serve as the lens through which you view your factory’s performance. They translate complex data into visually digestible information, empowering decision-makers at every level.
Machine Learning algorithms analyze historical data to identify trends and predict future outcomes. For instance, neural networks mimic the human brain, performing tasks like image and speech recognition, natural language processing and complex pattern recognition. They’re the silent architects behind proactive decision-making, foreseeing challenges before they emerge.
Predictive Analytics
What are these challenges? Common ones in an offsite factory include inventory management, inconsistency of demand, and more. Predictive analytics uses historical data to predict potential bottlenecks, to optimize resource allocation and even to foresee market trends. It serves as your factory’s compass when navigating these challenges
This isn’t about seeing the future in a crystal ball; rather it’s about strategically shaping your factory’s destiny. It’s the difference between reacting to issues and proactively steering your factory through them towards success.
Predictive analytics is the weather forecast for your factory. Just as you wouldn’t set sail without knowing the weather conditions, predictive analytics ensures your factory is prepared for whatever challenges the industry climate is likely to throw your way.
Continuous Monitoring
Imagine having a constant pulse check on your factory’s well-being. Continuous monitoring of everything from inventory levels to labor demand, coupled with the real-time analytics discussed above, is your safeguard against unforeseen challenges. It’s about staying attuned to the needs of your factory, ensuring that every part of the production process is in sync.
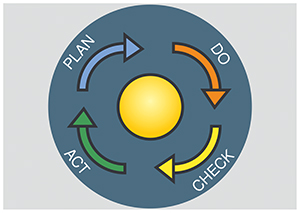
As mentioned above, this type of continuous monitoring is like having a constant, real-time Gemba experience applied to your data. Just as a Gemba walk can catch issues on the shop floor before they become serious, with frequent data monitoring, a slight deviation in output in any part of the operation will trigger an immediate response, preventing potential setbacks from escalating into major issues.
Think of it as a live dashboard for your factory. Just as a ship’s captain monitors various instruments during a voyage, continuous monitoring allows decision-makers to keep their fingers on the pulse of production metrics, supply chain movements and employee performance in real time.
Training for Data Literacy
As we embark on this data-driven odyssey, it’s imperative to equip your team with the skills to navigate it. Data literacy is not a luxury; it’s a necessity for every player.
Drawing inspiration from the insights shared in “Building a Lean Culture,” which I wrote for the June 2023 issue, instilling a culture of data literacy is akin to embedding Lean principles into the fabric of your organization. It’s about fostering an environment where every employee is fluent in the language of data and where every employee can contribute to the continuous improvement journey.
Providing comprehensive training programs ensures that every decision-maker, from the factory floor to the executive suite, can harness the power of data. This democratization of data empowers everyone to contribute to the collective intelligence of the factory.
Front-line workers can benefit from a basic understanding of the metrics being used to track their production, such as throughput, labor efficiency, defects per unit produced, etc. Purchasing teams should understand the data behind inventory turns, SKU portfolio management, etc.
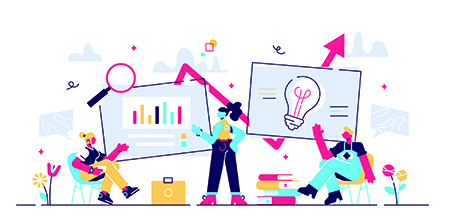
This training provides a toolkit to each team member. Just as a skilled navigator needs the right skills to get the ship to its destination, your employees need the skills to wield data effectively in their respective roles. For most employees, a couple of hours of basic data training will go a long way toward improving their effectiveness at their respective jobs.
Case Studies
The theory becomes reality when we witness the success stories of those who have embraced data-driven decision-making. Let’s delve into a compelling case study that highlights the transformative power of analytics in offsite manufacturing.
Consider a hypothetical modular factory that has integrated data analytics into its processes. By continuously monitoring production metrics, identifying bottlenecks and predicting material shortages, management has achieved a remarkable 30% increase in overall labor efficiency (labor hours per unit produced). This not only streamlined their operations, but also significantly improved customer satisfaction.
This case study serves as a beacon, illuminating the path for others to follow. It demonstrates that data-driven decision-making isn’t a theoretical concept, but a tangible reality that can revolutionize the way we run our factories.
Conclusion
Your offsite construction facility is a vessel sailing through a vast sea of data. Data-driven decision-making is not just a trend, but a strategic imperative for those aiming for continuous improvement. It transforms your factory into an agile, responsive entity, ready to navigate the challenges of modern offsite construction.
Embrace the power of analytics, make informed decisions and watch as your offsite construction facility sets sail into a future of unparalleled excellence.
Daniel Small is COO of Stack Homes, a modular manufacturer in Salt Lake City, Utah. As a renowned expert, thought leader, and consultant in Lean process optimization and innovation in offsite construction, he has transformed the productivity and efficiency of many offsite factories over his 22+year career in the industry.