The Benefits for Developers and GCs
- Advantages include more predictable scheduling and budgeting for the developer, and more predictability for the lender. Contractors will also be less impacted by site variability.
- Some factories will have concerns about commoditization, but there are strategies to address that and maintain profit margins.
- One design firm is developing modular plans that can be manufactured by a wide range of companies. Such efforts will be a big factor in helping offsite grow its market share.
Past articles in this magazine have discussed the idea of offsite manufacturers using standardized designs — both within a single project and across multiple projects — to gain efficiencies through repetition. Those articles assumed all projects being delivered from a single factory.
Of course, even greater efficiency can be gained by the sharing of standardized designs across multiple factories. A developer — a hotel chain, for example — could have different factories manufacturing the same modules in California, Colorado and Connecticut, with adjustments made to accommodate local conditions such a seismic activity, snow and wind.
In this article, we talk with four industry pros on how this model can benefit general developers, general contractors and manufacturers, and how this can lead more developers to make use of modular construction.
We also look at the efforts one of them is making to move the industry in this direction.
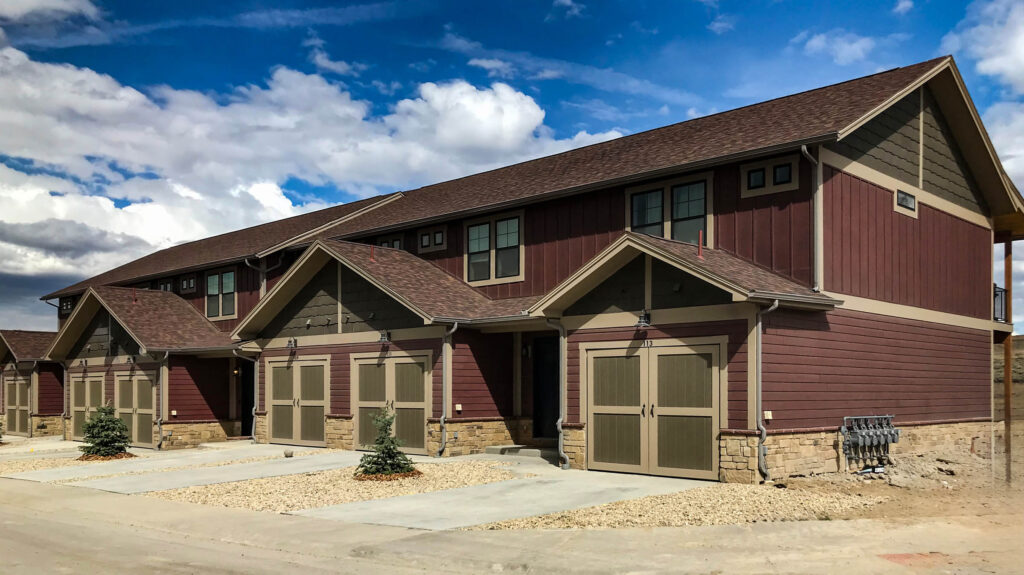
Photo credit: Heritage Homes of Nebraska
Developer Benefits
The benefits of standardizing designs across the modular industry include streamlined scheduling, faster production, better ability to work in multiple markets, more trust in the product, the ability to bid multiple factories, easier financing and shorter permitting times.
Standardization would make it easier for developers to use modular construction for their regional or national programs. If the same design could be manufactured in factories across the country, the industry would be in a better position to grow.
Scheduling. Standardization makes it easier for developers to meet timelines. “A hotel chain is going to be at the mercy of the capacity of their factory of choice,” says Dean Dalvit, an architect, engineer, and Founding Principal of EVstudio, a design firm based in Austin, Texas.
Of course, if one factory is too busy, the hotel chain can ask another factory to build it instead. “But in that case, the plans will likely need to be adjusted, perhaps to a degree that requires re-permitting,” he adds.
Speed. CJ Myrick, an owners’ representative based in Bozeman, Montana, mentions speed as a big advantage for developers. “The developer I was working with for the last four years built 4,000 beds of workforce housing in Big Sky, Montana. The timelines could definitely have been reduced (if we’d had more standardization than we did), providing housing to the community sooner.”
Market access. Standardization makes it easier to build in multiple markets. Take the example of a hotel chain that wants to put the same hotel in four different states, such as California, Texas, New York and Florida.
It’s not feasible to use the same factory for all four hotels: long distances between the factory and the jobsite can cause problems, including high transportation costs. “But if all, or most, factories across the US were capable of building the same thing, then we could design a set of plans that were factory-agnostic,” says Dalvit. That would make it possible for the hotel developer to have a national development program.
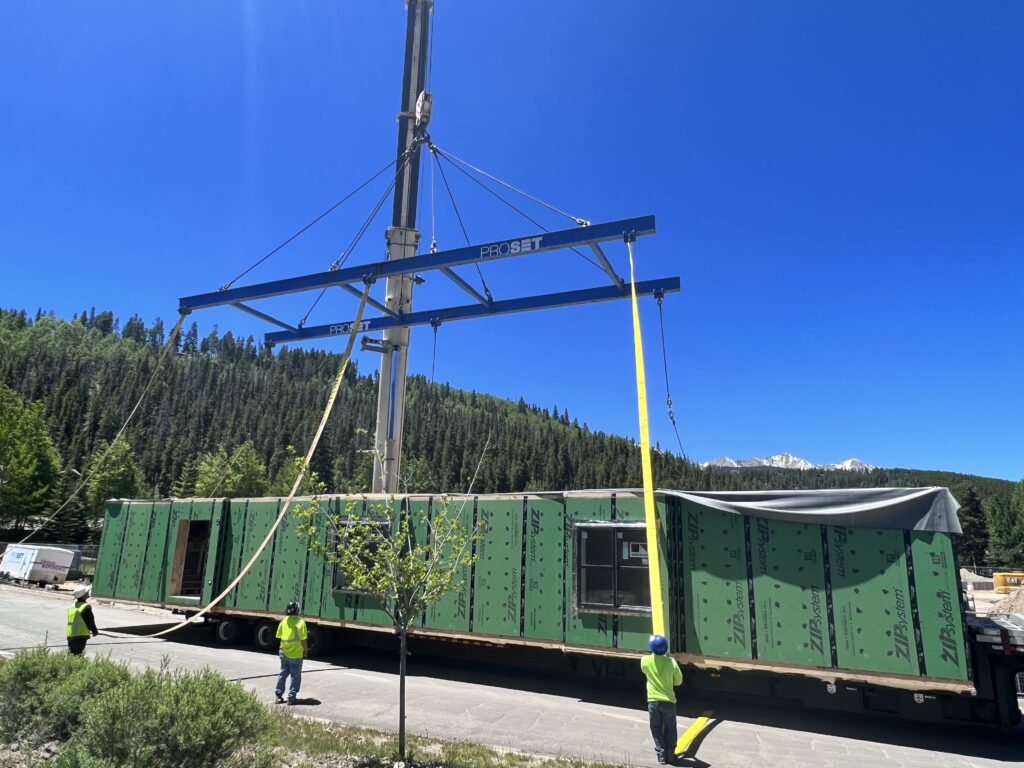
Photo credit: Flatirons Pro Media
In his view, the lack of this type of standardization is why national developers don’t use more offsite construction. “Some are dabbling here and there, but for a national development program, you would need a design that’s constructible by lots of different manufacturers,” he says.
Trust. Myrick says that another advantage of standardized designs is that they strengthen developers’ trust in the product. When they see that four or six buildings have been built to this design, they have more confidence in predicting budget and timetable. Of course, the developer could still change details like countertops or façades but showing them a core building with “proven efficiencies and cost savings in a design” would ease their concerns.
Multiple bids. Another benefit for developers of factory-agnostic designs is that they would no longer be restricted to a specific manufacturer. Instead, they could bid their project to multiple manufacturers.
At the moment, Dalvit says, “There’s no common language across factories. So, a developer or owner is always going to be restricted when selecting a manufacturer.” In addition, “the design team must have intimate knowledge of how that specific manufacturer operates, what their tooling is, what equipment they have, what materials they use and so on.”
In the short term, having the developer locked in and unable to choose between competing factories on price can sound like a good deal to manufacturers. Long term, however, Dalvit maintains that by opening up the opportunity for competitive bidding, standardized designs would lead to “a hundred times more work for every offsite manufacturer than there is today.”
Financing. “Standardization would help with financing big time,” says to C.J. McCray, the VP of Strategic Growth & Development and Partner at Symmetry Builders, based in Dacono, Colorado. At the moment, every factory does things a bit differently, so they’re not interchangeable. “A building’s design is created based on one factory’s capabilities,” he says. Standardization would add predictability and build lender confidence in the space.
Standardization would also reassure lenders that there’s a back-up factory that could take over manufacturing if the first goes out of business or runs into any other problem — natural disaster, hacking, etc. — that halts production.
“Standardization de-risks a project,” explains Dalvit. “Bankers love when things are repeatable.”
Permitting. Nathan Peterson is the Founder and CEO of Vederra, a modular manufacturer headquartered in Evergreen, Colo. with a manufacturing facility in Aurora, Colo. He says that the land entitlement process in Colorado can take two years.
“If you had standardized designs, once they were approved in the factory at the State level, they would be easy to amend for local conditions — for different snow and wind loads, for example. That would speed up the overall process.”
Not having to get new State-level approvals on every unique project also saves money.
For General Contractors
Doing the same thing across multiple projects is also beneficial for the GC in charge of on-site assembly and finishing. The main benefits are increased efficiency and lower risk.
Efficiency gains. With conventional construction, every building is a custom product, McCray says. “The learning curve on each building is steep because there are unique elements every time. Not to mention the time and effort that goes into design, procurement, hiring people with the right skills, and so on — all for one project,” he says.
By contrast, when you move towards standardization, erecting buildings gets faster and easier every time. “I use the analogy of putting together night-stands from Ikea,” McCray says. “The first one might take an hour. The second one takes 45 minutes. By the third one, you’re cruising, and you can put it together in half the time of the first one.”
Dalvit says a GC “could build multifamily buildings from Guerdon, then from Nashua, then from Fading West — and if they were all based on the same standardized design, the GC wouldn’t have to learn each manufacturer’s special way of doing things,” helping their team to get more efficient each time.
Myrick illustrates this point with a project he’s been working on in Big Sky, Montana. “The project consists of three, dorm-type buildings. On the first of those buildings, the crew set a maximum of 15 modules a day. By the time they got to the third building, they hit 26 mods in a day.”
On which aspects of a design would standardization make the most difference to GCs? Structure is an obvious one.
At the moment, each factory has a different way of building the structure, he says. “By standardizing those systems, we can eliminate a lot of head scratching about how things come together on-site.” The more familiar GCs are with a system, the less risk there is of delays and mistakes.
Other elements can benefit from standardization as well. For instance, although electrical systems don’t vary substantially from project to project, “the extent of work done in the factory versus on-site varies a lot,” says McCray. “Drawing the line in the same place between factory work and on-site work would help greatly.”
He adds that plumbing and mechanical systems are also quite variable. For instance, “we haven’t standardized how the connections are made, or what products are used to make the connections. Everything is kind of unique to each project right now. More standardization would be really helpful.”
Less site variability. Some might object that every site is different, and so every project is different. “While there’s some truth to that,” says Peterson, “there’s still room for standardization. There are enough sites that a standardized product could fit onto.”
McCray agrees. “There are always building elements that are repeatable. Maybe one project has to have subterranean parking or a podium of some sort. That is customized to the site,” he says. “The foundation system will also be customized to the site, because of variability in the soil and topography. But above the foundation, we can certainly eliminate a lot of customization.”
He also notes there are other variables, such as “local jurisdictional requirements, seismic requirements and other design criteria that are specific to a geography.” But such requirements still leave a lot of room for standardization.
Myrick notes that, as a developer, he wouldn’t care if his tenants in Montana are in the same unit as somebody in California. He says that tenants don’t care, either. “We provide high-quality, functional spaces. If we were charging them too much, then that would be a problem. That’s what most tenants care about.”
Myrick also says that, even with standardization, there’s room for variation. “I’ve worked with architects that have designed standard box types that they can configure different ways.” They can also accommodate different architectural features. “For instance, maybe one building has a truss roof and the other has a flat roof with parapets.”
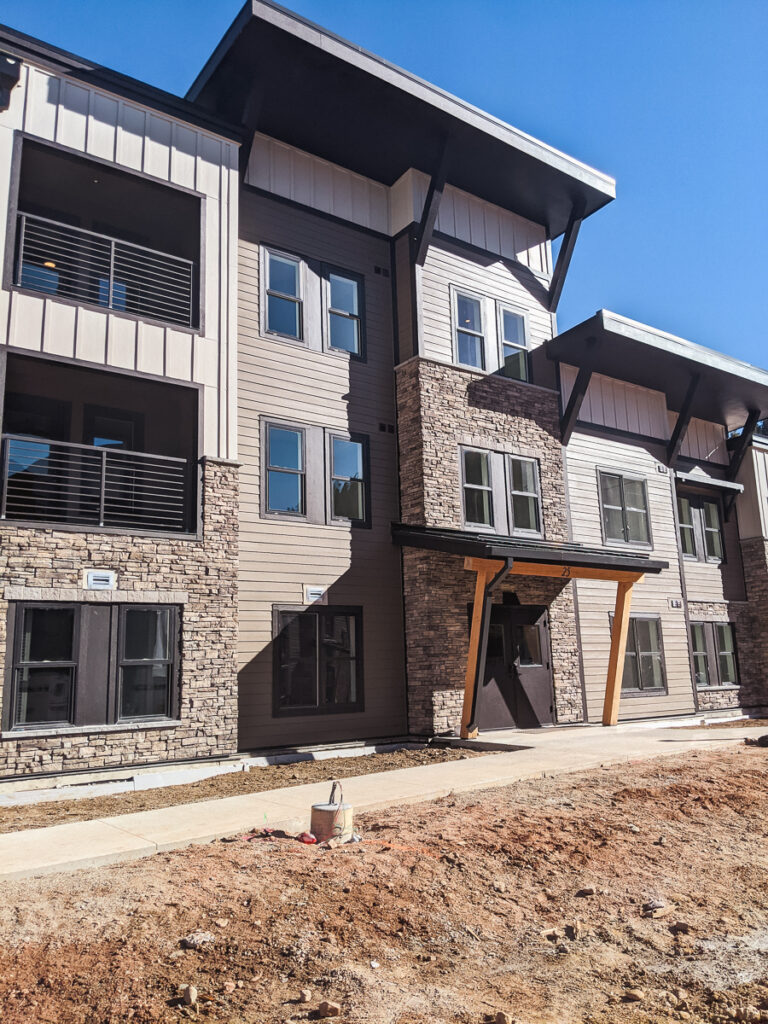
Photo credit: Flatirons Pro Media
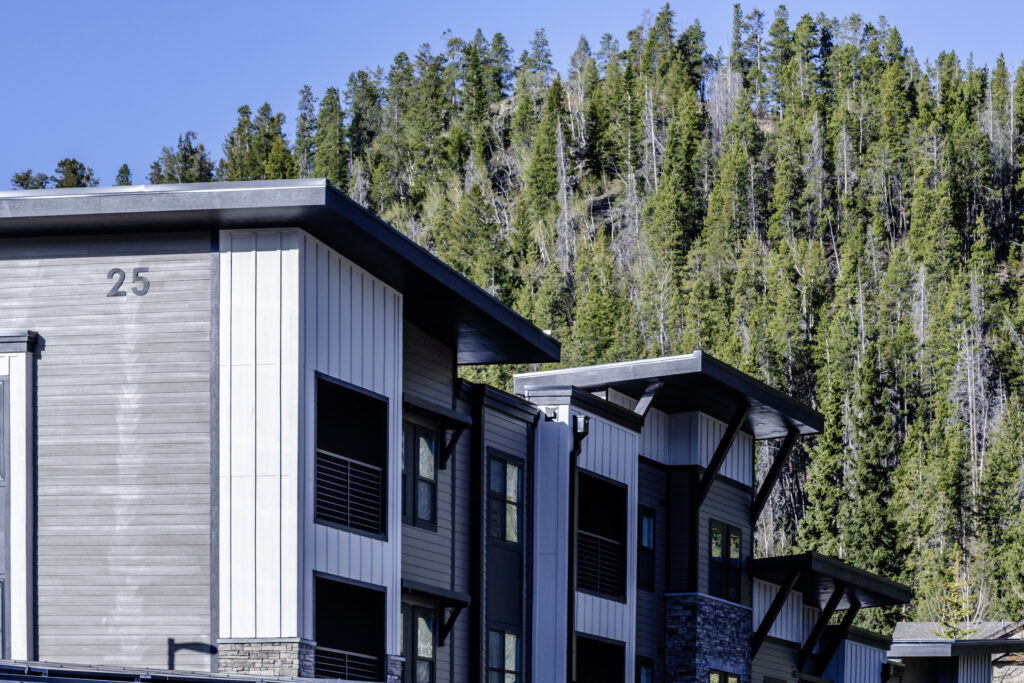
Manufacturers and Design Firms
Of course, some manufacturers will object that standardized designs would require them to change their processes and material choices. And some factories are limited with respect to the module size they can manufacture. Peterson counters that, details aside, there are some designs, such as a 16 ft. by 30 ft. box “that pretty much every factory would be able to produce to the same specs.”
Another risk is commoditization. If different factories can build the same design equally well, that could cause prices and profits to fall over time.
Another issue is that some factories have proprietary designs they don’t want to share with competitors. A solution proposed by Dalvit is for factories to monetize their designs by “patenting their intellectual property and licensing it to peers.”
There’s also room for design firms to create standardized designs. Dalvit’s design firm, EVstudio, is pursuing this route by developing a library of modular plans — including multifamily, hospitality, and single-family homes (both attached and detached) — that are manufacturable by “a wide variety of manufacturers.” They’re encouraging others in the design community to do the same.
He believes that when offsite construction has at least a “10% share of the construction market, standardization will open the door to broader scalability and manufacturers will ultimately benefit tremendously.” It’s also beneficial for manufacturers not to “get bound up in design, where they often struggle due to wild variations in jurisdictions, codes and client needs.”
McCray says that sharing designs will also help factories fill lulls in production and would allow them to offer work to other factories when they can’t keep up.
Peterson believes that standardization could lead to more factories getting set up, thus growing the industry. “During an economic slowdown, if a manufacturer is asked if they want to produce a standardized product for which orders are already lined up, the response will be, ‘Absolutely, let’s do that.’”
Zena Ryder writes about construction and robotics for businesses, magazines, and websites. Find her at zenafreelancewriter.com.