Its quality and speed make modular housing a worthy partner for urban infill development.
- In urban infill developments, modular construction helps builders and developers set prices that are within reach of a greater number of buyers.
- Modular homes can be constructed quickly, reducing noise and disruption in the neighborhood.
- They can also be designed to fit a variety of lot sizes and with different elevations to fit their surroundings.
Cities like Detroit, Los Angeles and Pittsburgh are experiencing severe shortfalls of all types of housing, from single-family detached to rental apartments. Urban infill development supplies new housing stock in place of vacant, overgrown lots and abandoned homes. By substituting modular housing for stick-built, developers can achieve lower price points and complete projects faster, more efficiently and with less noise and inconvenience for the neighbors.
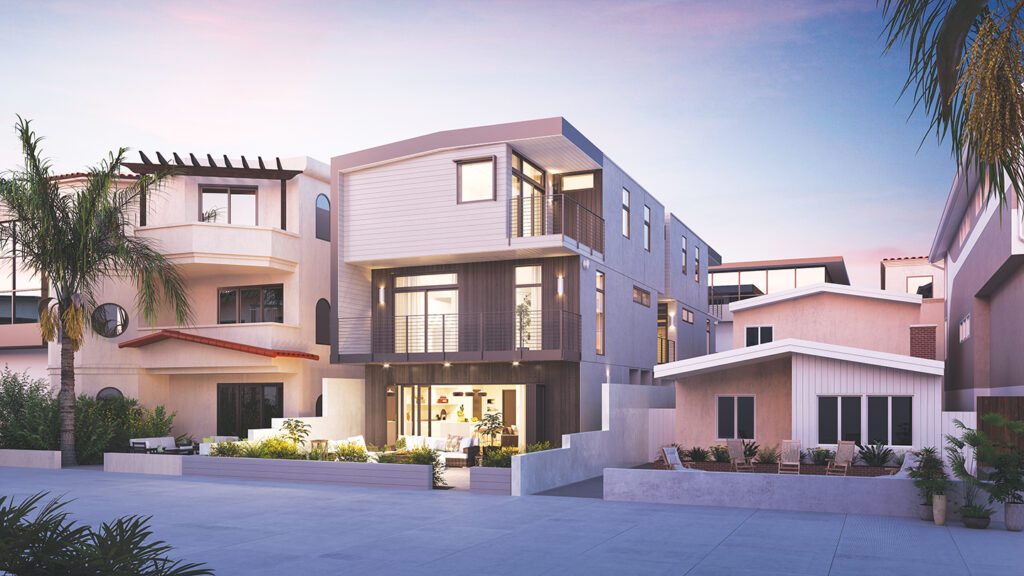
Photo credit: Courtesy of Plant Prefab
Site-Specific Designs
When David Allen, President of InnovaLab Development in Rockford, Michigan, was introduced to modular construction at a trade show in 2017, he loved the designs, but recognized they wouldn’t fit 35-foot-wide city lots. Allen and Roberto Kritzer, Vice President of Corporate Design for Champion Homes in Troy, Michigan, put their heads together and, four months later, produced a pattern book of designs for urban neighborhoods.
Allen, who has 30-plus years of experience as a real estate developer, previously worked for Michigan’s Kent County Land Bank Authority converting foreclosed properties into low- and moderate-income housing. He and a business partner started InnovaLab in 2019 and began introducing the modular concept to nonprofit organizations, municipalities and other nontraditional clients.
InnovaLab’s solution is a timely one, as housing shortages in Michigan are “beyond the pale,” says Allen. “We’re facing a shortage of 14,000 housing units in Grand Rapids, and 50,000 in Kent and Ottawa counties, the two largest counties in West Michigan.” The company was launched in 2019 and by 2020, “we had about $5.8 million worth of contracts in the works,” he says. “Then COVID [happened].”
The company retrofitted its business model for the post-pandemic world. “We’re based out of West Michigan,” says Allen. “If a customer comes to us with a project that’s in our area, we act as the general contractor. We do the modular, the site work, everything. If the project is outside of West Michigan, we help the customer find a local general contractor and we work with that [GC].”
The focus is on design and the quality of fit and finish, which helps ensure the homes are both attractive and attainable to buyers. In the Grand Rapids area, Allen says, the company’s homes are priced from the high $200,000s to the low $300,000s. InnovaLab is building duplexes in Flint, Mich., next spring: “We’re doing three triplexes and two duplexes in historic neighborhoods, so [the homes] have to meet historic standards.”
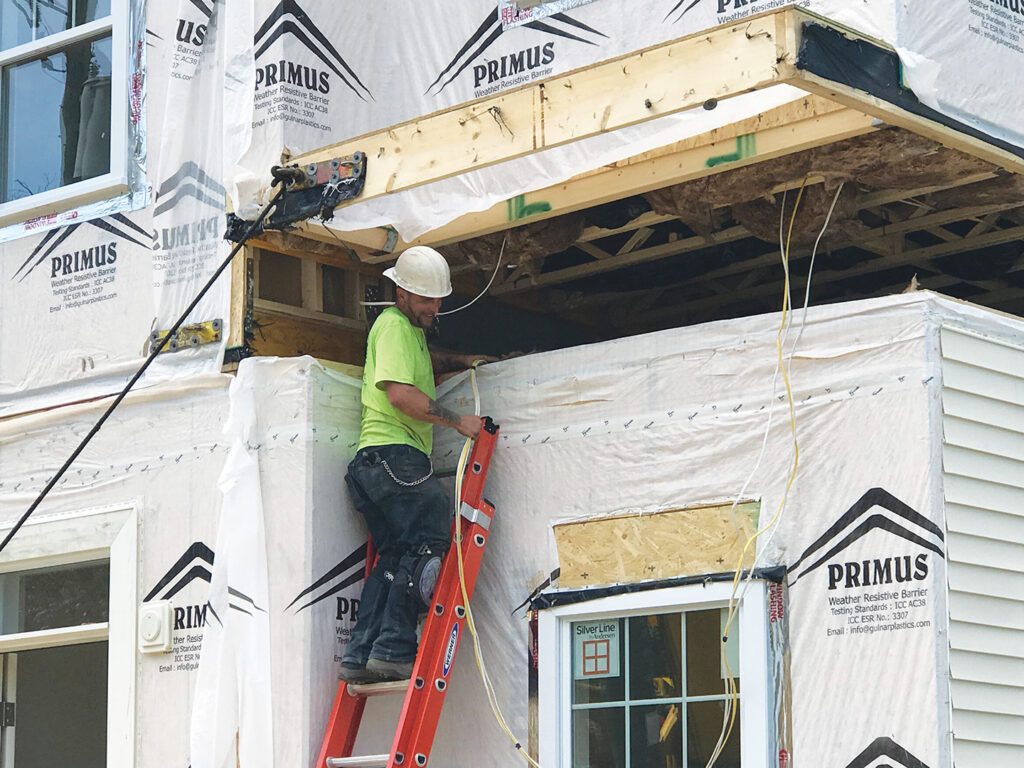
Photo credit: InnovaLab
Streamlined Process
Significant time savings can be realized by constructing modules in tandem with foundation and site work. Moving most of the construction off site minimizes neighborhood parking problems and noise.
“Building in a controlled factory environment also allows for more efficient labor planning and utilization, which is particularly beneficial for infill projects given the limited supply and high cost of labor in urban areas,” says Stephan Jordan, Executive Vice President of Business Development and Marketing for manufacturer Plant Prefab in Rialto, California.
Factory construction offers streamlined material planning and efficiency, Jordan says, resulting in less waste with no jobsite theft or vandalism. Factory manufacturing processes provide a high level of quality assurance and safer working conditions for laborers.
From Allen’s perspective, modularization affords the opportunity to get urban infill projects done right, and to scale, and it also eliminates headaches. “You’re not going to have a lot of change orders once you get locked in at the factory.”
It takes only eight weeks from order placement to delivery of the modules, he says. “And once it’s set on the foundation you can complete it in two months. Your time to market is a heck of a lot quicker and that’s a real advantage.”
Allen emphasizes that there are many issues with city lots that developers wouldn’t normally deal with in a standard modular set. Builders and developers who plan to work with institutional clients on urban infill should practice being patient, because projects don’t happen quickly. “The wheels of government move slowly,” he says.
Multiple logistics are involved in urban infill because each location is different. InnovaLab recently completed a project in Hamtramck, a working-class neighborhood in Detroit, Michigan, where the houses date back to the 1920s and are only five feet apart.
Of course, finding staging areas in urban neighborhoods can take some creativity. “We’re not in a big field where we can just line up modules on trailers,” says Allen. “For the Detroit project, we got permission to use a large empty lot that was a couple of blocks away. Then we walked the route to the site to ensure the trailers would make it. In some instances that meant going underneath an elevated walkway that was 14 ft., 6 in., leaving about six inches of clearance for our boxes.”
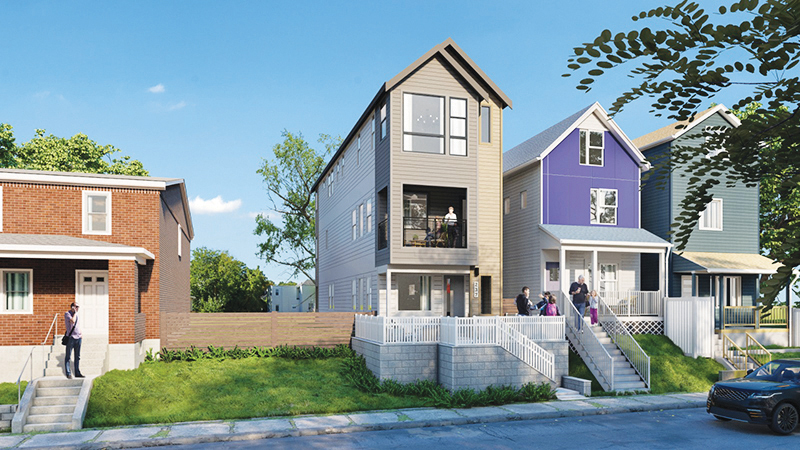
Photo courtesy of DAHLIN Architecture
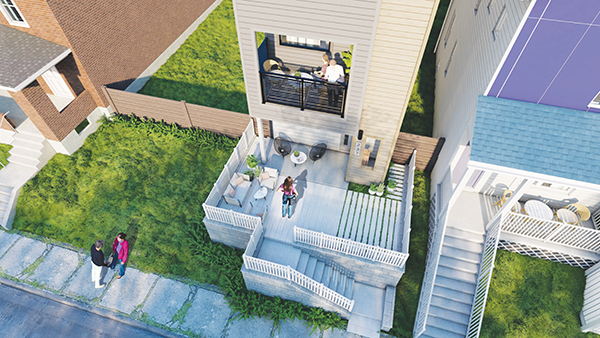
Photo courtesy of DAHLIN Architecture | Planning | Interiors
Replacing Missing Teeth
A startup out of Pittsburgh, Pa., Module is doing its part to fill the gaps left by vacant lots, or what Hallie Dumont calls “missing teeth.” Dumont, Director of Product Development for Module, says, “There has been a resurgence in cities like Pittsburgh, which makes housing a priority. It made a lot of sense for us to use modular construction for infill.”
Module utilizes the constraints set by modular construction for narrow infill sites. The company’s urban designs include 16-, 30-, 36-, and 44-foot-wide models. A 14-foot-wide model is under development. “It’s a perfect fit because most of the lots [we deal with] are about 20 feet wide,” says Dumont.
Module conducts an inventory of its designs once a year. The company typically builds two- and three-story townhomes, but also offers three single-story designs. In addition, there are three multifamily designs: a duplex, a triplex and a sixplex. “We have standard specs for both market-rate and affordable housing, but both have the same building envelope,” she says.
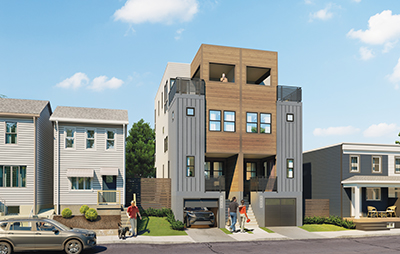
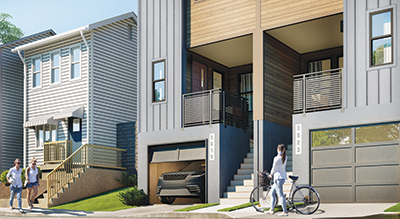
Photo courtesy of DAHLIN Architecture
The company works with both nonprofit and for-profit developers, designing and specifying on-site elements such as stairs and stoops, porches, rear decks, carports, garages and canopies. Two façades are available: a modern elevation and a traditional elevation with three windows across (a good option for historic Pittsburgh neighborhoods, Dumont says). Zero Energy Ready is the standard for all Module homes, which are all electric and solar ready.
At press time, Module was in the process of developing Black Street, its first multifamily project, which includes four units: one affordable, one market rate, and a duplex with a one-bedroom apartment on the first floor and a two-bedroom unit on the second and third floors.
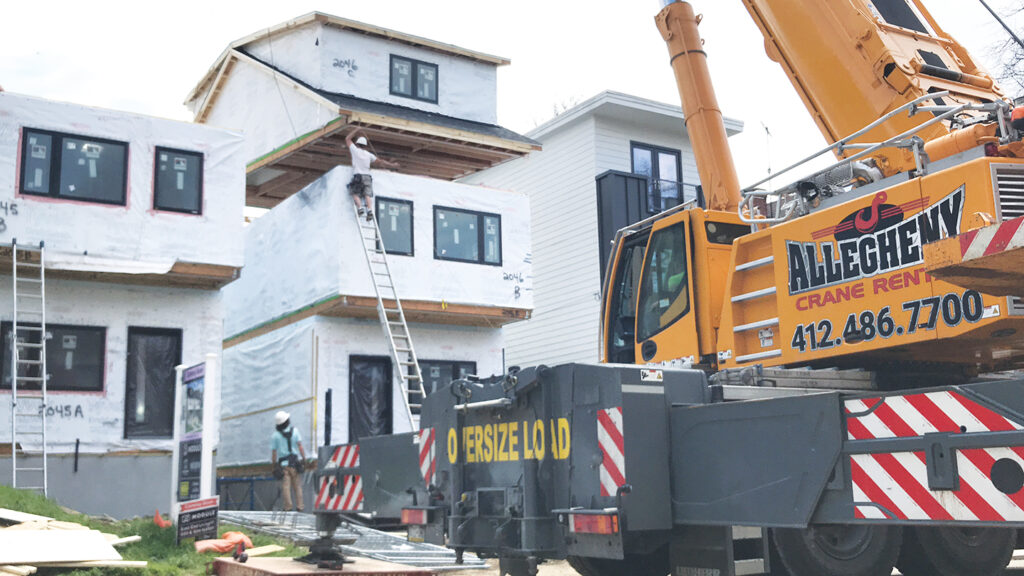
Photo credit: Courtesy of Module
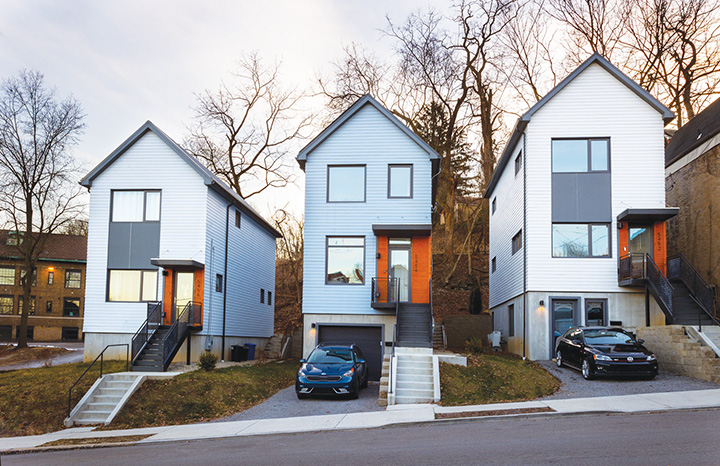
Photo credit: Courtesy of Module
Get It Done Right
More and more, developers are going modular with urban infill housing for reasons of speed, factory quality, efficiency and attainability. Modularization helps keep rents and sale prices within the reach of more renters and buyers. Plus, the designs make the most of quirky site conditions, which are a given with urban infill.
“In cities that have all these vacant lots there are home valuation issues, and in urban infill you have to hit a certain price point,” says Allen. “Modular affords us the opportunity to get these projects done right and to scale.”
Susan Bady is a freelance writer based in Chicago, Ill., who focuses on residential and commercial design and construction topics including sustainability and building technology.