We interviewed five design professionals who have embraced modular building systems. Here’s what they had to say.
• Modular requires architects to learn new skills, adapt to different timelines, and calculate costs and profits differently.
• Some said that modular lets them be creative while also offering affordable homes that buyers will love. Others said that manufacturers don’t always make that easy.
• The bottom line is that while architects will be essential to expanding modular’s market footprint, there will be hurdles to getting more of them on board.
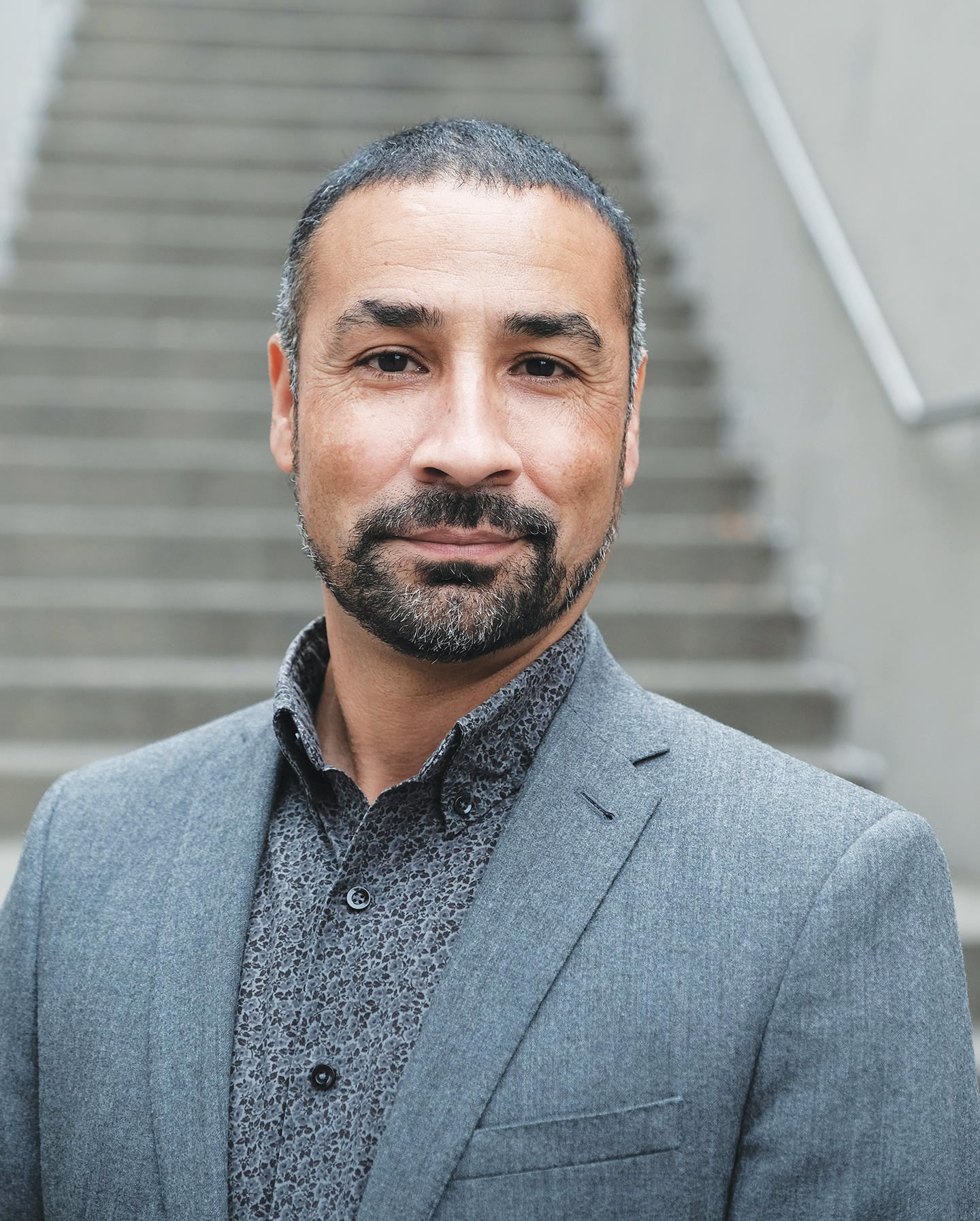
Photo courtesy of AO Architecture
Some architects have caught on to the possibilities of modular building and have designed numerous large-scale projects, while others remain firmly on the sidelines. This article offers insight into the experiences of architects who have used modular in single-family residential and multifamily projects.
A few of the architects interviewed here were relatively new to modular, while others have decades of experience. To understand the role this profession plays now and into the future of modular, we included architects at both large and small firms in different parts of the US. What we found is a tale of two market segments.
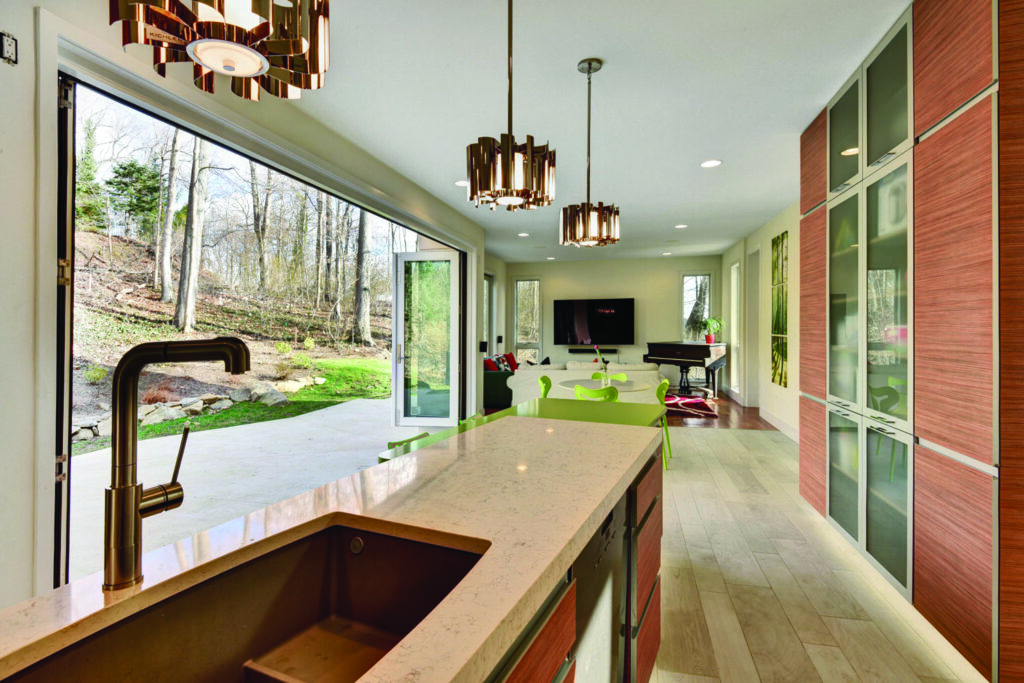
Photo courtesy of Douglas Cutler Architects
Creativity and Efficiency
Architect Nickolos Gomez works at AO Architecture’s Oakland, California office. In addition to being a Principal at AO, he is also the firm’s Director of Modular Design and Construction. AO has completed 18 modular projects, including multifamily apartments, affordable housing and senior living.
An architect since 1999, Gomez’s interest in modular construction predates his arrival at AO by several years, through exposure to multifamily and institutional projects. He credits AO for creating a community around modular construction where people collaborate, and where information is shared for the common good.
Gomez says that, unlike conventional building, modular requires a different skill set when it comes to understanding the details of the construction process. For instance, strict timelines must be adhered to, and every detail of the project must be defined before work starts in the factory. “You run into construction delays if you have gray areas,” he says.
Appropriate submittals to municipalities must take place, and they’re often different from the submittals required for a conventional build. Installation methods are different from the norm. For the project to go smoothly, collaboration and information sharing among all members of the team (the architect, the developer client, the manufacturer and the general contractor) is essential.
However, Gomez doesn’t find modular to be constraining. “You just need to learn the dos and don’ts and you can learn them as you go,” he says. “Every project is a challenge, and I learn something new with each one.”
Modular construction allows Gomez to be creative in his design while also ensuring affordability and efficiency. He expects to see more modular construction in areas such as hospitality, student housing, affordable housing and supportive housing.
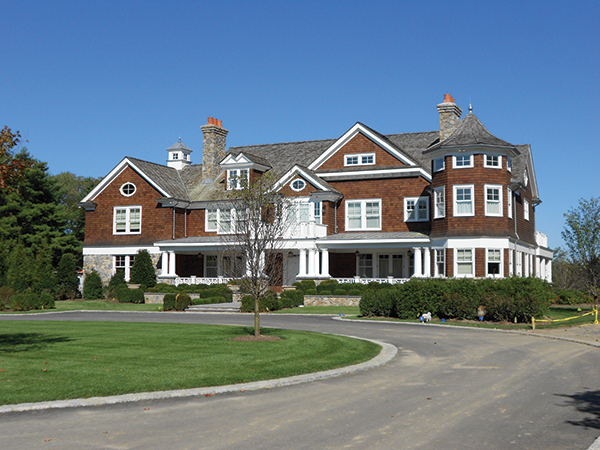
Photo courtesy of Douglas Cutler Architects
Good Design Pays
Douglas Cutler, a Connecticut-based residential and commercial architect, has been involved with modular construction since the 1980s. That experience includes more than four dozen residential, commercial and multifamily projects.
He likens the role of architect to a fashion designer, with the manufacturer providing the basic structure. An architect that understands the possibilities of modular construction can manipulate customer perceptions and create illusions within a home’s design by techniques that include changing box widths, lengths and ceiling heights. A good architect will also know how to up the aesthetic game with interior finishes, such as coffered ceilings.
When it comes to manufacturers, Cutler has met with varying levels of cooperation. Some have treated him in an almost adversarial manner, viewing him as a competitor to a manufacturer’s engineering department. The problem, says Cutler, is that manufacturers don’t put enough emphasis on design quality, or don’t quantify design as a part of the cost of selling.
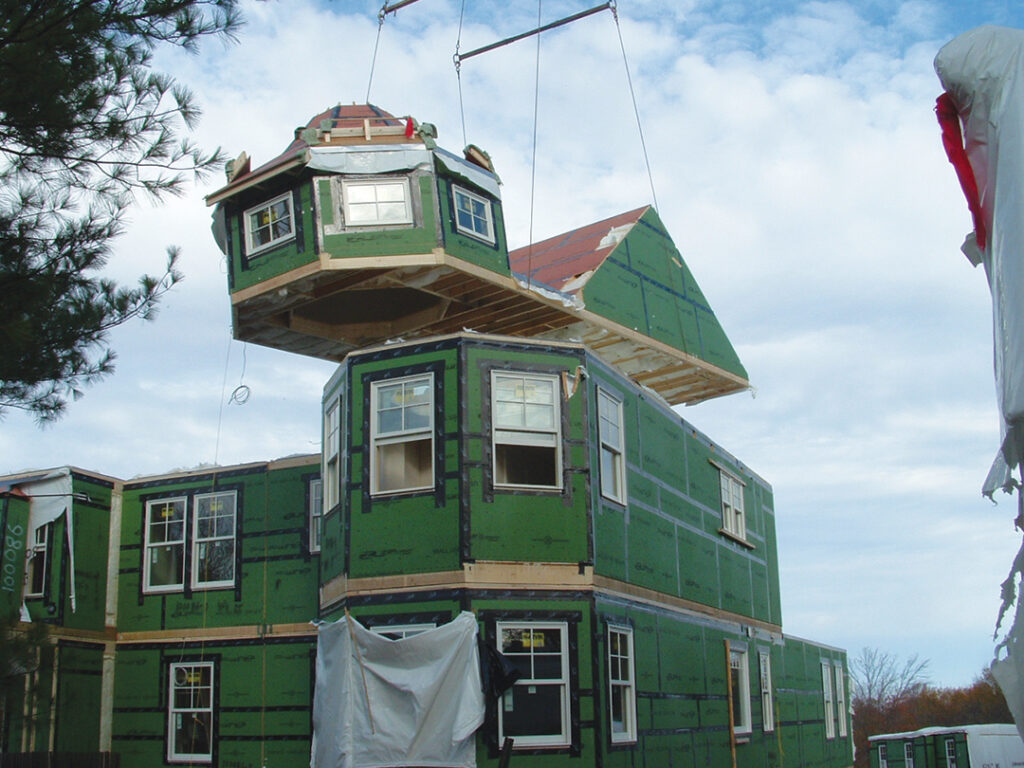
Photo courtesy of Douglas Cutler Architects
The Greater Good
Matt Laase, a Principal of Jackson Main Architecture based in Seattle, Washington, has a career in architecture that spans 30 years. After returning from working abroad, he was struck by the lack of available affordable housing in the US.
Laase first became involved in modular construction through a 2015 work camp housing project in British Columbia, Canada. There, he came to see how it could help provide homes for low and moderate-income people.
“We have built the same type of housing for over 100 years,” he says. “I see modular as an alternative way to deliver value and affordable workforce housing.”
Jackson Main’s vision, according to Laase, is to work toward what he termed as the “greater good.” That includes educating developers, engineers and others about how modular brings value and best practices to construction. His company strives to be an open source of information about their experiences with modular by sharing what they have learned with others.
“Modular building can be more affordable, efficient and faster, but it is complicated,” Laase says, explaining that’s because “it is a different way to do things for everyone involved.”
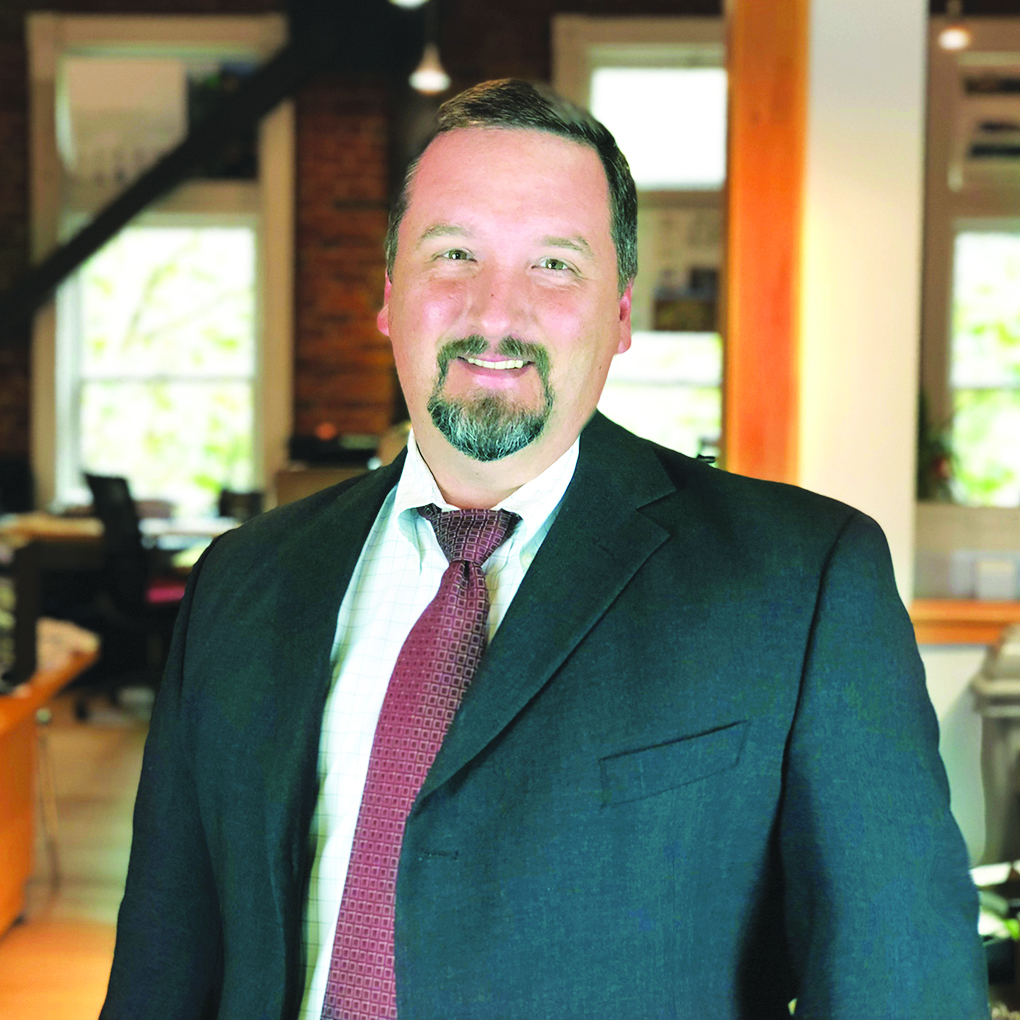
Photo courtesy of Jackson Main Architecture
How to Think About Money
Lasse stresses that decisions must be made upfront, especially when it concerns design and material choices. Also, because a factory must purchase materials in advance, the financing process is different, and a bridge loan might be required to cover 50%, or more, of the costs.
In the end, Laase says the final product is superior in quality to site building, if not cheaper. “It’s always faster, but isn’t necessarily less expensive in the final cost.”
Customers usually come to Laase first, he says, with the notion of trying modular with their next project because of cost savings; however, that could be a misnomer. Savings typically happen in the “speed to market,” he says.
With a shorter construction timeline, leases can be filled sooner. “Just imagine if you were to shorten your occupancy timeline from 24 months to 14 months,” he explains. “Revenues are more immediately realized.”
Successful modular projects begin with careful planning, and defining a schedule is critical, Laase says, adding that it’s important to be aware of local jurisdictions’ ordinances. “You must collaborate with local officials and cannot work in a vacuum.”
Laase recalls that the first 85-unit, multifamily modular project he worked on would have gone more smoothly if communication and education with local officials had taken place before the units arrived. “Seattle had no understanding of modular,” he says. “Inspectors were red flagging everything, and we were having to cut open walls.”
Although modular building still remains a niche, Laase continues to be a passionate supporter of it, especially now as a way to alleviate the nationwide housing shortage.
In terms of what can be done with modular construction Laase says, “You may be limited by unit widths and lengths, but not by your creativity.”
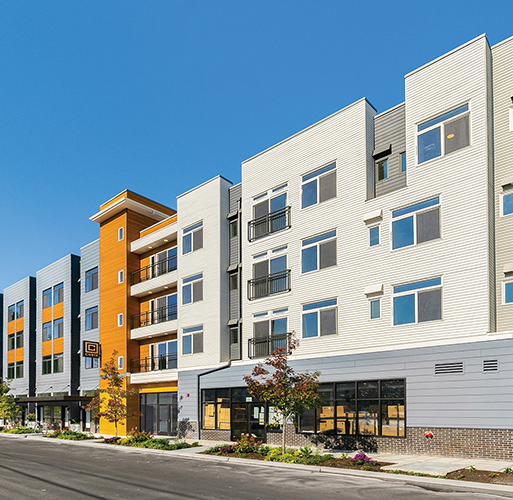
Photo courtesy of Jackson Main Architecture
Urban Micro Homes
As a managing partner at FK Architecture in Winter Park, Florida, architect Gary Badge is a self-described “creative professional,” whose philosophy is “to be proactive and not reactive.”
Badge’s interest in modular construction began unexpectedly during the COVID-19 pandemic. He had ordered a 15-ft. x 30-ft. storage shed from a local home improvement store with the vision of transforming it into a future man cave. A flatbed truck arrived and offloaded pre-built and pre-painted framed panels for the walls, roof and floor. Badge was captivated by the fact that it only took a day to assemble the structure.
It was also during the pandemic that Badge saw his industry shuttered, and started looking for alternative ways to build more efficiently. This led him to join the Modular Housing Institute (MBI), where he learned more about panelized and volumetric modular approaches to building. After attending conferences put on by MBI, he realized modular construction was a key to easing the burden of unaffordable housing.
In July 2022, FK Architecture’s developer client, Wire Development, had an interest in modular micro-housing, and together, the two companies developed a micro-home prototype. A micro-home provides a flexible and economical way to offer affordable housing in smaller, urban infill lots.
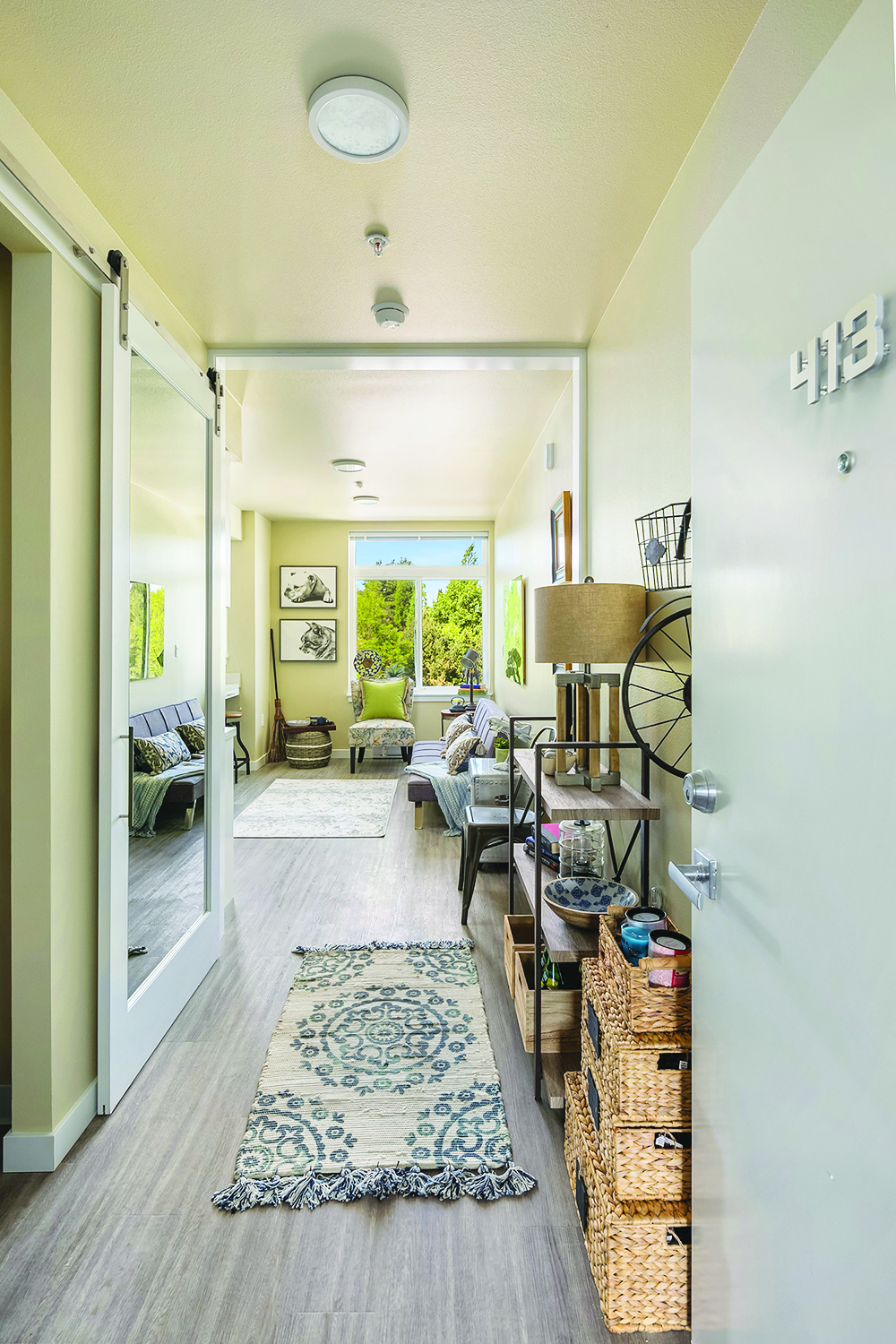
Photo courtesy of Jackson Main Architecture
FK Architecture and Wire Development approached the City of Tampa and the Housing Authority with their idea. The Housing Authority offered some infill lots that the city owned and they were happy enough with the homes that FK and Wire provided that followed up with a request for a proposal to develop a similar site. After presenting their concepts and ideas, FK and Wire were awarded the project.
FK Architecture’s unique approach to micro-home design offers permanent housing in a smaller footprint at a more affordable price than with traditional apartment buildings. The design concept addresses two housing problems at once — getting people to move back into cities post-COVID and revitalizing existing empty spaces that, if left undeveloped, would contribute to urban blight.
Micro-homes range from 450 to 650 sq. ft. in size and offer unique modular furniture options, upgraded appliance packages and upgraded durable finishes.
Seeing the endless possibilities in modular construction, Badge and FK Architecture have been working with other developers in other communities to realize the potential of micro-housing. Badge says it’s exciting to reimagine vacant and underutilized urban spaces for the micro-housing market, and projects like these can help rebuild communities stifled by urban sprawl.
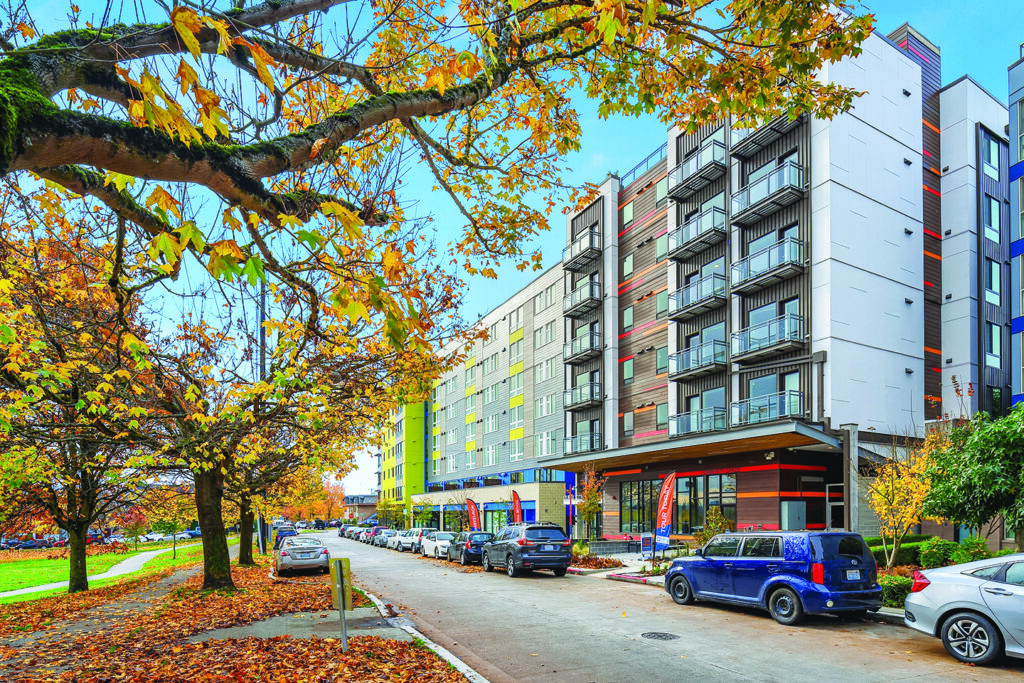
Photo courtesy of Jackson Main Architecture
It Doesn’t Always Work
Modular won’t work for everyone. That’s the experience of residential home designer Dan Scharff, who owns and operates Cheridan Designs in Pleasant Valley, New York.
Scharff “cut his teeth” in the modular industry. In the mid-1990s, after graduating from college, he began working as a draftsman in the engineering department of Westchester Modular, a manufacturer in Wingdale, New York. In 2001, he started Cheridan Designs, designing homes for both modular and site-built residential construction. Over the last decade, he estimates he’s designed about 20 modular homes.
Today, however, nearly every home Scharff designs is site-built.
That’s thanks in part to bureaucracy. He says that, in his market, modular homes are neither faster nor cheaper than site-built ones because of state and third-party approvals and transportation regulations. “It can take up to six months to get drawings to production,” he says, “so the only benefit you have left is quality.”
On average, the homes Scharff designs are in the $2 million to $4 million range with customers wanting custom treatments, such as high ceilings. Sometimes, he says, it is just easier to build those custom features on-site.
He also says that some modular manufacturers are resistant to change. “If they had their way, all they would build would be four-box colonials with 7/12 roofs and gable porches,” he says. “If I were to bring them a custom design, they would try to value engineer it to make it better for their production line to get the best bang for the buck at the expense of the architectural design.”
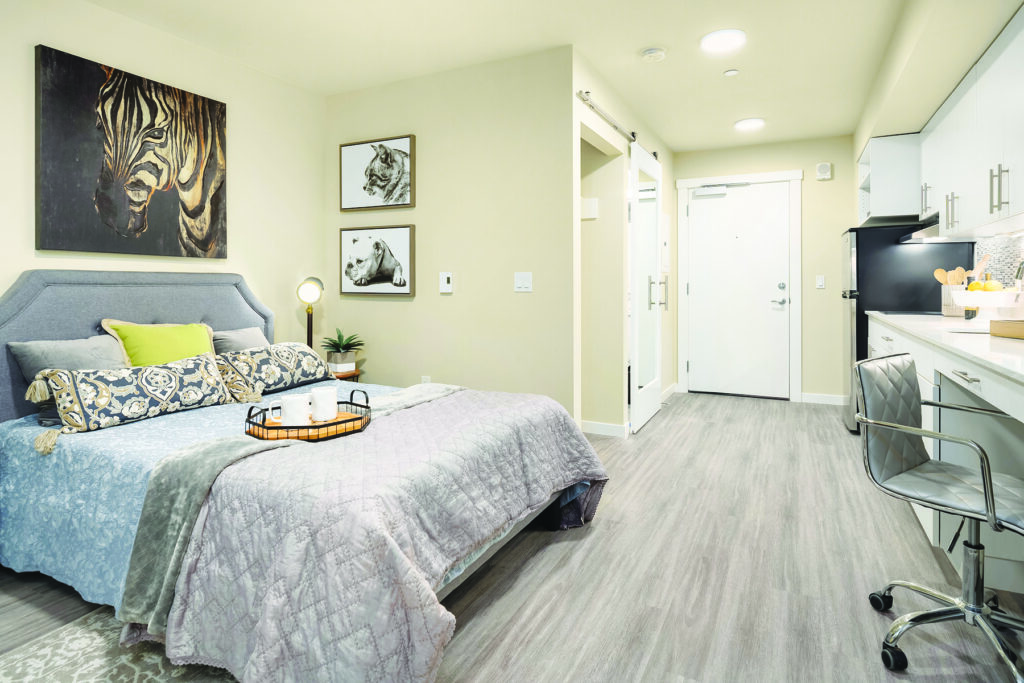
Photo courtesy of Jackson Main Architecture
Hurdles to Overcome
Lessons learned from sampling these conversations reveal a contrast between market segments.
On the one hand, there is a great deal of excitement among architects regarding the possibilities of modular construction in hospitality, multifamily, affordable housing and supportive housing. On the other hand, architects and home designers on the residential side are less enthused and find dealing with modular manufacturers less attractive.
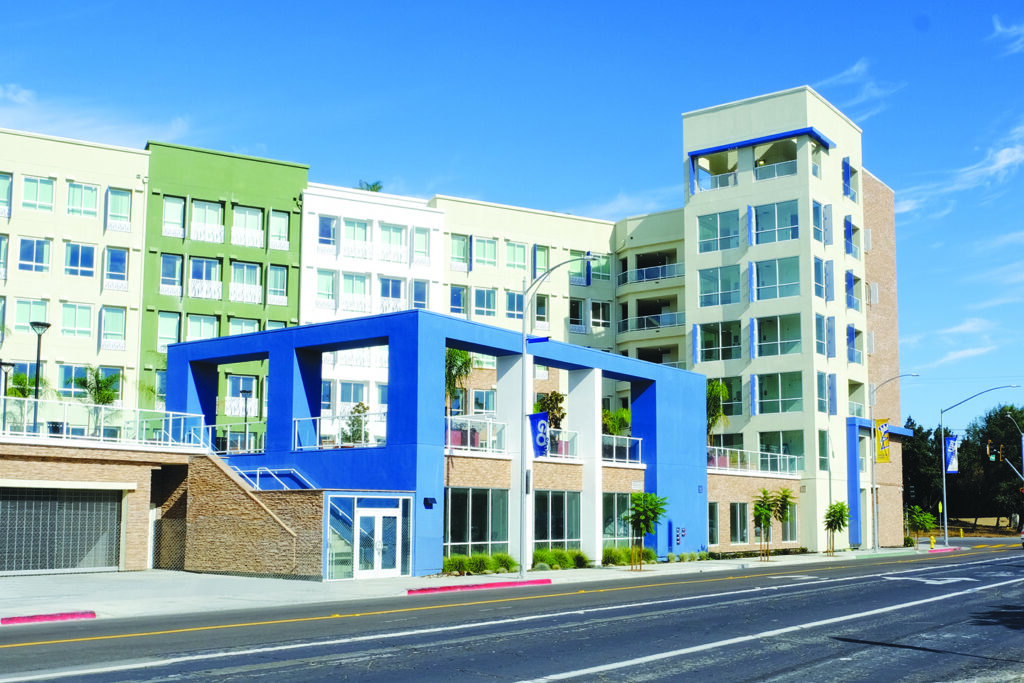
Photo courtesy of AO Architecture
There is also a learning curve for architects when it comes to education about the modular construction requirements and processes. In addition, coordination must take place among jurisdictions, modular companies and architects.
While architects hold one of the keys to expanding modular’s market share there are definitely hurdles to overcome.
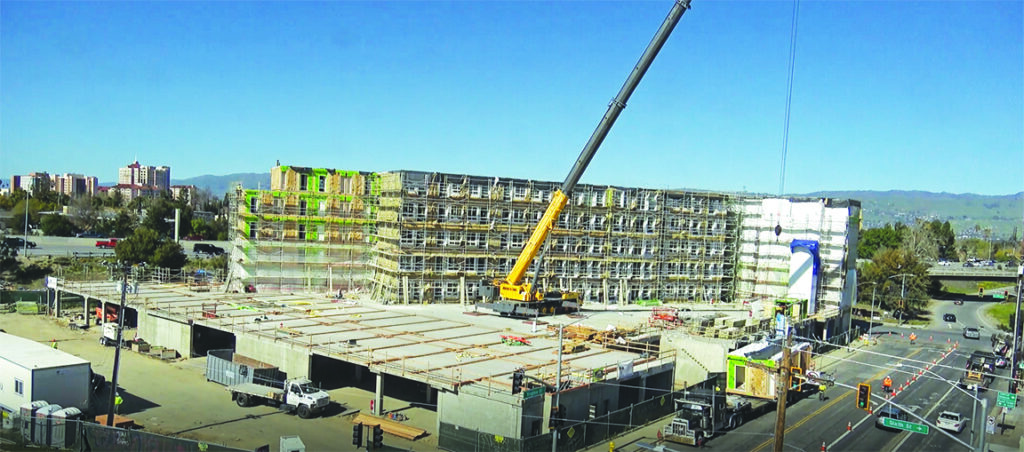
Photo courtesy of AO Architecture
Reed Dillon is a content brand specialist, marketing consultant and freelance writer that focusses on offsite and new construction. He is the owner of Creative Brand Content in Moneta, Virginia. Contact: [email protected].