Some of the inefficiencies of site-building are duplicated in the factory. This company claims to have eliminated them.
- Veev manufactures steel-framed panels with integrated plumbing and wiring
- Their central factory can feed smaller satellite plants located closer to job sites
- Efficiency is enhanced by extensive use of digital technology and automation
This magazine often talks about offsite’s speed and quality of production as a way to address the national housing shortage and many offsite startup founders are exploring different ways to accomplish that goal. One of these is Amit Haller, co-founder and CEO of the San Francisco Bay Area-based Veev, which manufactures steel-framed panelized walls with integrated plumbing and wiring.
Started in 2008, Veev was initially envisioned by Haller and his partners — Ami Avrahami and Dafna Akiva —as a real estate investment and development company. Haller had built two businesses before beginning Veev, including one related to Bluetooth core technology, which he sold to Texas Instruments. “I thought I was retiring when I sold that business,” he laughs.
Instead, as the serial entrepreneur dug into the fundamentals and value chain of real estate and construction, he began to recognize it as an old-fashioned business with many complications and inefficiencies.
Veev’s transformation to an offsite manufacturer began taking shape in 2016. Haller had learned how very labor-intensive the construction industry is and how many construction workers had left the trade during the housing crisis of 2008, thereby creating the protracted labor shortage the industry is currently grappling with.
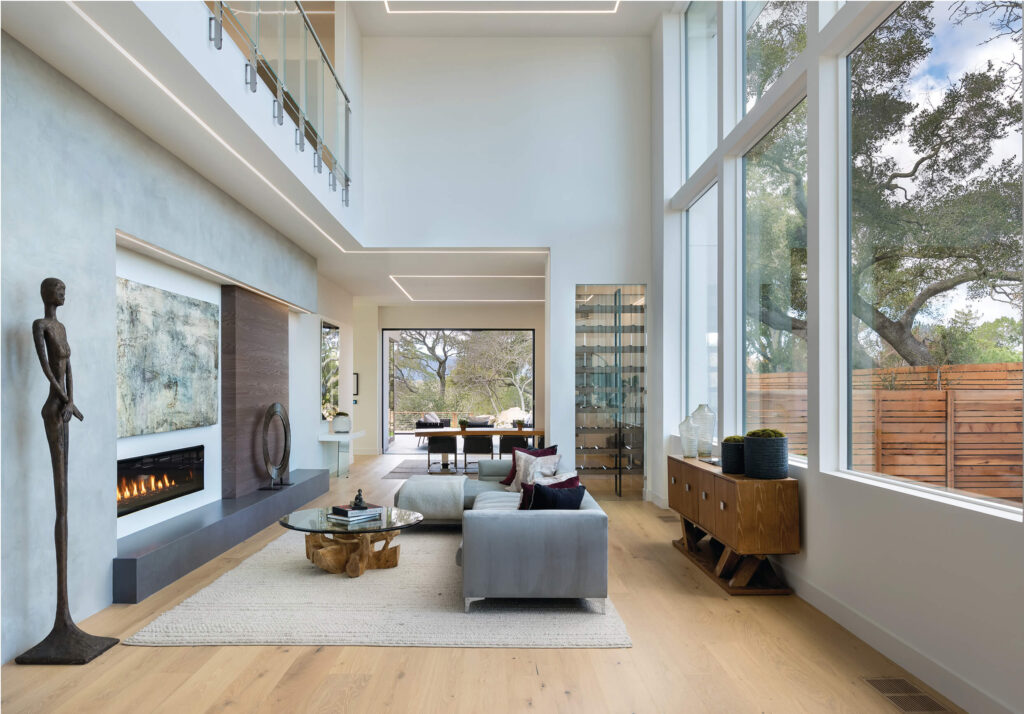
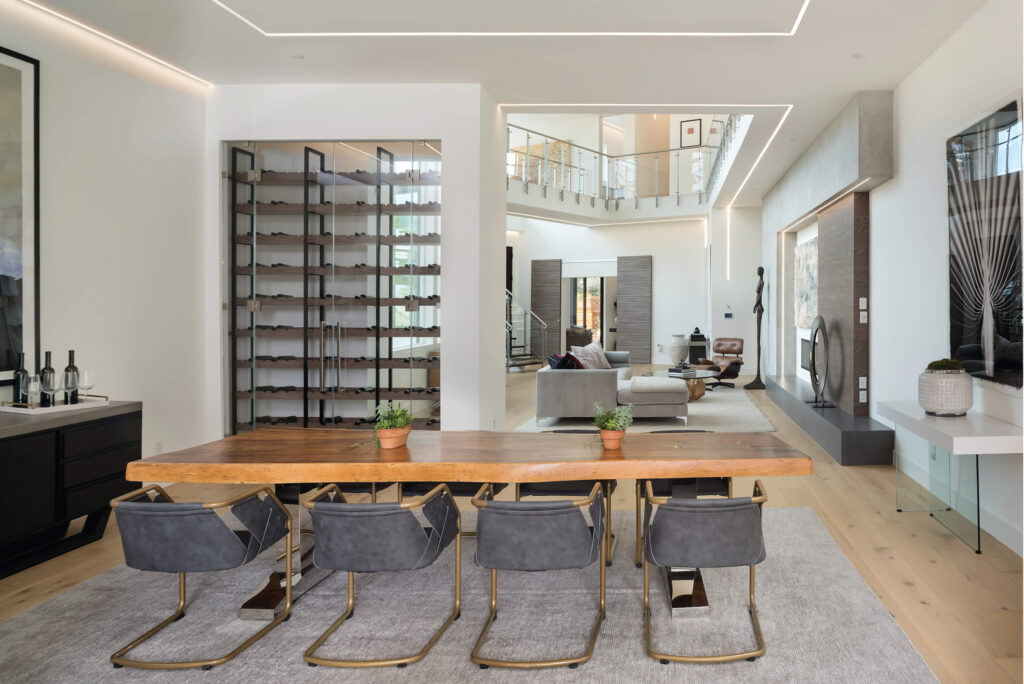
To his mind, this was irrational. “At the end of the day, 99% of a home can be built right, but if you are missing one trade or material, you can’t sell it,” Haller says. His team began examining the steps involved in building to figure out how to construct a home for the 21st century, given the reduced availability of labor.
Growing Offsite
Offsite/prefab/modular building has existed for years. Everyone knows it has benefits, so why isn’t it used more?
Haller has multiple answers, but the primary one is that many approaches are not scalable. “The same inefficiencies are moved into the manufacturing facility.” In many factories, projects compete for floor space.
Veev has addressed this with a hub-and-spoke manufacturing model. They’ve built a 50,000-square-foot manufacturing facility in the Bay area and have an office in Tel Aviv, Israel for their back-end employees (primarily engineers). But as operations scale, they can also locate smaller facilities in proximity to demand areas to reduce the time and costs associated with moving components. “This enables us to meet housing demand where it’s most prevalent and to make construction far more efficient compared to a large, centralized facility that ships all over a state or region,” Haller says.
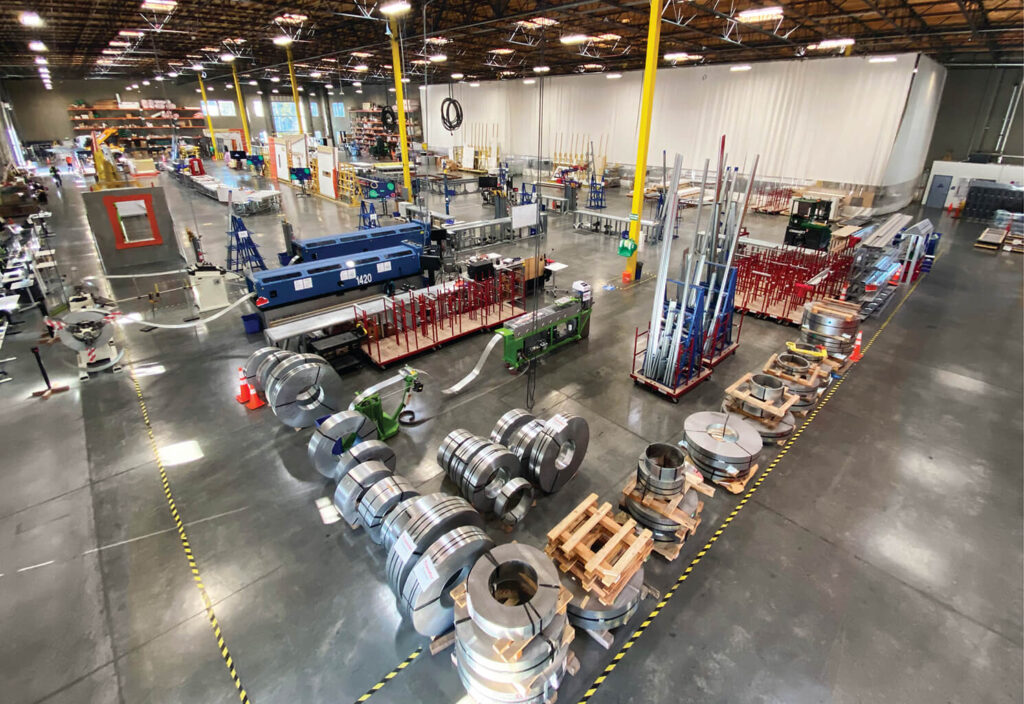
The company can complete a 78-unit development in 90 days – 4 times faster than the industry standard. Their on-the-ground team of only five team members was able to erect 50 walls per week or about one every 30 minutes.
Veev’s team came up with its system by thinking of homes as products. Questions they asked included: what’s the product made of and are there better ways to make it than what everyone else is doing? They focused on interior and exterior walls and were determined to figure out how to build the most efficient walls that could be mass-produced.
Their answer was a wall constructed from light-gauge steel. It’s a closed wall system: covered on the inside with a high-performance surface—a multi-faceted material that’s certified hygienic and mold resistant, ultra-smooth to the touch and possesses incredible strength. Comparatively, drywall, favored by most builders, is rigid and prone to mold.
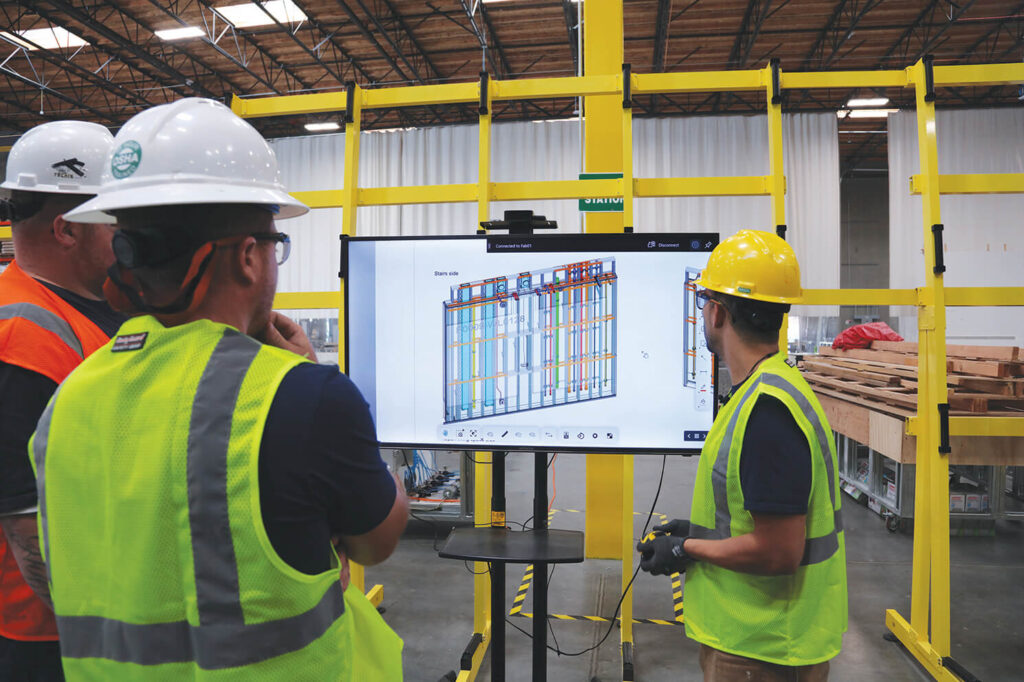
To assist in the production of the walls and other elements of the home, the company has pioneered its own in-house Building Information Modeling (BIM) technology, in which a digital twin of the home is made before any manufacturing begins. It maps every piece of a home down to the finest details, from mechanical, electrical, and plumbing (MEP), to smart home capabilities, to complex design features.
Production Capabilities
Because Veev wall panels are produced in a highly-automated factory, design changes are made through digital files rather than waste on the production floor.
“We no longer need specialists to build the walls,” says Haller. “We can mass-produce walls and floors to any shape, size and look.” He says the walls are pre-inspected and built to be long-lasting.
Over the past five years, Veev has built 140 homes. With its current system, Haller says they’re able to produce up to 800 to 1,000 houses per year.
In partnership with Lennar, Veev recently announced an agreement to build a new Northern California community of 102 attached homes that broke ground this year. Other projects have included townhomes, single-family homes and multi-family homes, demonstrating how their system is adaptable to a range of housing types. “We view this flexibility as one of the core strengths of our approach — we can produce high-quality and modern homes that are adapted to developers’ varied needs,” Haller says.
So far, all of Veev’s projects have been in Northern California, but the company has plans to expand into Southern California and Texas in the next year. Ultimately, Haller aims to serve the entire US and beyond.
Meeting Challenges
Material shortages and inconsistent supply chains are challenges everyone is facing. Veev is confident that its approach to building is faster, more efficient and less reliant on the supply chain.
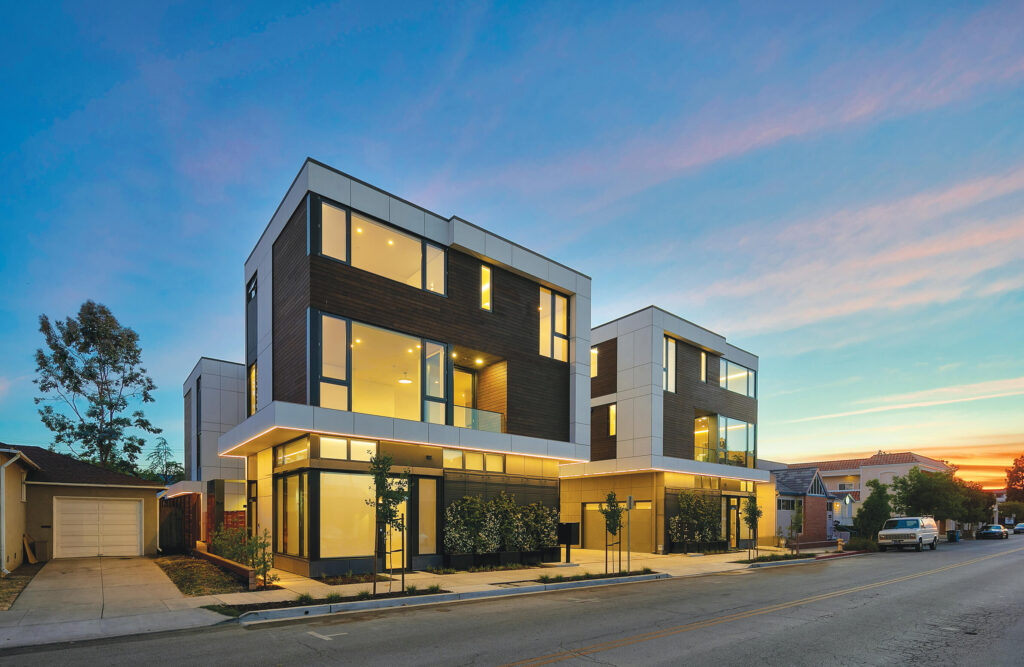
A traditional home construction project has a bill of materials of around 10,000 SKUs. Veev claims that its streamlined material use and pre-project mapping with digital twin technology allows them to significantly reduce the number of materials and parts needed for a build. This means they are less dependent on supply chain fragmentation, resulting in lower production costs and reducing the time it takes to complete a project.
Other challenges go beyond time and costs. The construction industry has been moving towards a future of reducing wasteful practices and Veev aims to put sustainability front and center. For instance, they rely upon vendors who supply recycled steel. They also joined the World Green Building Council’s Net Zero Carbon Buildings Commitment.
No one company can solve the housing crisis. Instead, the entire industry needs to join in and drive innovation and tech-forward approaches to building. Haller and Veev are determined to be part of the solution and believe their homes go above and beyond.
“In light of the housing crisis, our mission is pressing,” Haller says. “By vertically integrating the homebuilding process from start to finish, we have managed to produce homes at a quality, speed, value and sustainability unseen in the industry – until now.”