Builders who have switched to Structural Insulated Panels say that more builders would use them if they understood the benefits.
- The panels can make it easier to meet strict energy codes, thanks to a lack of thermal bridging and Passive House-level airtightness.
- The reduction in jobsite waste has been documented at up to 75% when compared to a typical stick frame.
- Proper sealing is crucial to avoid moisture problems. It takes a couple of projects for crews to become proficient with this system.
Although Structural Insulated Panels, or SIPs, have proven themselves over decades, they’re still not considered mainstream construction. There are no hard stats on the percentage of homes built with them, but it seems to be in the single digits. However, builders who use SIPs seem sold on the method; in fact, many made the switch from stick framing and never looked back.
For this article we interviewed three senior managers from residential construction companies in the western United States. They use SIPs for all of their homes, and all said that doing so has allowed them to build more homes in less time and with less waste when compared to stick framing. The completed homes are also draft-free and use less energy than conventional builds.
SIPs consist of two exterior layers of oriented strand board with a layer of expanded polystyrene (EPS) foam sandwiched between them. The foam is relatively environmentally benign.
There is a learning curve when starting out with this building system. For example, construction teams need to pay more attention to how electrical wires are routed and the sealing of joints between panels. Asking an experienced builder to provide training can help flatten the learning curve.
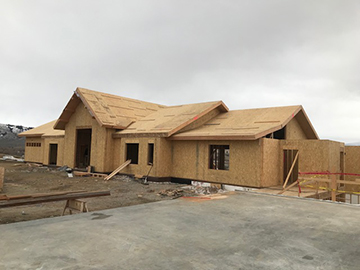
Credit: Paul Wilson
Path to Zero
Energy savings is SIPs’ most obvious benefit. “If you know you want to meet the energy codes, SIPs are the way to do it,” says Paul Wilson, Owner of Tamarack Construction Company, which is based in Victor, Montana. “It’s getting harder for stick-frame builders to meet energy codes, but when building with SIPs, I can [easily] meet or surpass the code requirements.”
Tamarack has been using SIPs since 1992. Wilson was sold on them after using them on one job and seeing their benefits. The company builds five to 15 homes per year.
The reason SIPs make it easier to meet energy codes is because they eliminate many issues with thermal bridging and air infiltration, Wilson says. “SIPs have very little thermal bridging; stick-framed homes have a lot of it. To mitigate thermal bridging in a stick-framed home, you must build expensive assemblies such as double-wall construction, or you have to wrap the house entirely with foam board. Both add expense.” He adds that stick-framed homes with truss roofs tend to have more air infiltration.
Another SIPs convert is Clifton View Homes in Coupeville, Washington. Every house that Clifton has completed since 2003 has been zero-energy-ready, according to Ted Clifton, President and CEO. (He is also the President, CEO and Chief Designer at Zero Energy Plans, which is headquartered in the same town.)
Clifton says the company switched to using SIPs exclusively in 2000, because “it just made better sense.” The company builds four houses per year, on average. Dozens of their homes have been featured in the US Department of Energy’s Tour of Zero, which offers virtual tours of energy-efficient homes in which renewable energy (usually solar) offsets all or most of the annual energy consumption.
In New Mexico, Spiegel Kinsley Construction, based in Albuquerque, has been using SIPs since it was founded in 2021. It received awards for energy savings in 2022 and 2023 from PNM, a major utility.
“We were at around 5,000 kWh savings for each home,” says company President Evan Kinsley. “We took first in the state of New Mexico [in the PNM awards] two years in a row as well. So, it’s kind of a cool way to see, okay, we’re building high-performance, energy-efficient homes, and we’re doing [it] at a really high level.”
According to Kinsley, “The highest kWh savings refers to how efficient the home is compared to a standard construction home. The baseline would be a code-compliant home without a prescriptive model or high-performance build.”
The company builds an average of three homes per year, ranging from around 2,500 to 3,000 sq. ft.
He chose to use SIPs because the technology “checked off all the boxes in terms of how to build a high-performance home.”
Wilson says that a local utility, Ravalli Electric Cooperative, has audited the heating and cooling costs of several houses his team has constructed. The audit was for a 1 ½-year period and costs were around half of what the utility estimated, with some homes using as little as 33% of the estimates. The Cooperative used energy-modeling software and compared Tamarack’s homes to those built using typical construction methods.
Besides thermal bridging, according to Wilson, another reason for SIP homes’ low energy use is that they’re quite airtight, and can easily have less than one air change per hour. Building codes in western Montana allow up to four air changes per hour at a maximum. The results have been measured with blower door tests.
In fact, most of Clifton’s buildings meet Passive House requirements for airtightness, he says. The standard is 0.6 air changes per hour at a 50-pascal pressure.
There are also weatherproofing benefits. If builders use SIPs, moisture cannot get into the building easily and condense, Clifton explains.
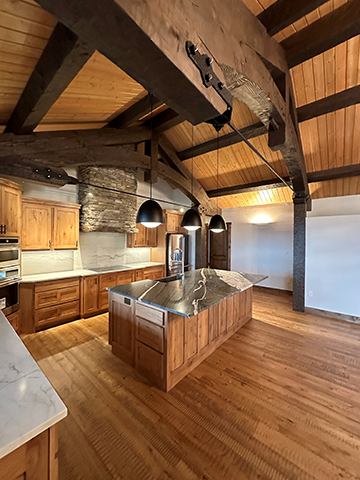
Credit: Tamarack Construction
Waste Reduction
Efficient use of materials is another advantage. All three builders agreed that using SIPs results in much lower jobsite waste.
Built Green Washington, a green home certification program, found that using SIPs easily eliminated over three quarters of jobsite waste, Clifton says. “Studies showed that the average new home generated about 2,400 pounds of construction waste, or roughly one pound per square foot of construction. We reduced that by more than 75% by building with SIPs and by being careful to recycle other products.”
His construction team re-used some cutoff pieces of 2x4s and 2x6s to create bases for shower handholds inside walls. These were designed to support the future installation of grab bars for people with disabilities.
Wilson provided a similar ballpark figure, which is that over 70% less wood waste is generated by the SIPs projects.
“I probably averaged two fewer dumpsters per home,” Kinsley estimates. “We’re able to keep our jobsites really clean. At the last build, I had a pile of cutoff lumber, including OSB [roof and SIP] sheathing for the entire build, that was about the size of a desk and about a foot tall. One of my framers took it home for a small project.”
The builders interviewed for this article all agreed that SIPs do not have significant issues with attracting pests or being flammable.
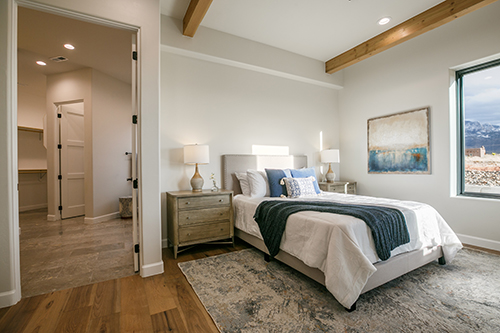
Credit: Real Estate Marketing Service
Building New Skills
In terms of disadvantages, there is a learning curve involved with using SIPs that may cause initial losses in time and profit.
“The only difficulty that we have with SIPs is working with electricians who have to think differently about how they’re going to wire a house,” Clifton says. “You have to plan ahead for where you’re going to pull wires. If you find that you need one more wire, you’ve got to pull them all back out and pull them back through together. Once the electricians have done a few homes, it’s actually faster to wire a SIPs house than a stick-frame.”
In fact, wiring a SIP building is relatively straightforward, according to a YouTube video from SIP Systems Hawai’i. (Search for “How to Run Electrical Wiring with SIPs.”) Wiring chases (drilled through the EPS at the factory) come down every four to five feet from the top to the bottom of the panel; workers use a four-inch hole saw to cut outlet and switch locations. Then they insert an electrical box into the hole and attach it to the panel with screws.
Builders who use SIPs also must pay close attention to sealing panel joints, especially on roofs, Wilson says. “During the installation, all wood members and panel joints are sealed with a heavy bead of mastic supplied by the SIPs manufacturer. After installation, SIP tape is applied to all joints of the SIP panels, providing a seal [preventing] heated inside air from meeting cooler outside air.”
Sealing is also a crucial moisture-proofing step. According to the Structural Insulated Panel Association, there was moisture damage to around 20 multifamily SIPs buildings in Juneau, Alaska. An investigation of the problem concluded that the cause was improper panel installation.
Some construction-related considerations change when a company starts using SIPs. Changing the sizes of windows or doors is more difficult with SIPs buildings than it is with stick-framed ones, Kinsley says. This is due to the dimensions of the SIPs.
Educating people who are new to the technology is also important, Kinsley adds. Builders using SIPs should be prepared to educate inspectors and homeowners about them.
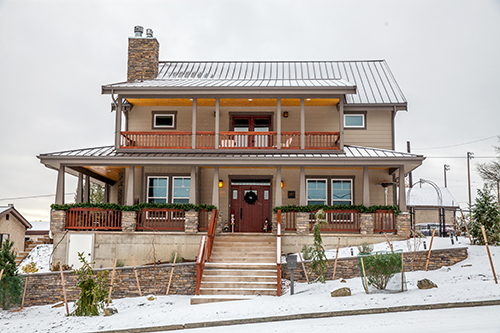
Credit: Ted Clifton
“Not a lot of homeowners know what SIPs are,” Kinsley says. “That’s typically the start of the conversation. I focus a lot on education throughout the process with my homeowners. What SIPs are, their benefits, why I use SIPs, and why I build high-performance homes.”
He says that some inspectors on his jobs are also seeing a SIPs structure in person for the first time. “So I walk them through all our connections and I take a lot of photos during framing so I can explain to the inspector the build process and the connection points.”
Tamarack Construction produced a YouTube video (search for “SIP Construction Process and Benefits -Tamarack Construction – Stevensville, MT”) that Wilson says is “extremely helpful for clients” and has been very well received. “A lot of what we do with our clients is educate them on how an energy-efficient building is different in construction and function.”
The builders all found that their framing crews were fully up to speed with using SIPs after completing two houses with them. Clifton brought in an experienced builder to teach his crew how to use SIPs, and has since coached other crews on how to use them.
“I tell them, ‘Just count on losing money on the first one you do,’” Clifton says.
Although it costs more per sq. ft. in materials to create a SIPs wall than a stick-framed one, this savings is more than made up for by reduced time and lower labor costs, Clifton says.
“When you add up the cost of each of the components of a stick-framed wall, it costs less for materials than for a similar sized SIPs wall,” Clifton says. “When you add in the labor and include the fact that the wall is ‘complete’ as soon as it is installed, the SIPs wall becomes about the same price as the stick-framed wall. And when you add in the value of time saved, and the value of the extra space inside the building envelope, the SIPs structure costs less than the stick-framed structure.”
“What is your time worth? How much money can you make in that extra two weeks? At the end of the year, maybe you build five houses instead of four. And if you’re making $25,000 a house, that’s a big deal,” he says.
Kinsley estimates that he has shaved about a week from the framing process. “I’m adding probably two days of [electrical work] since we needed to cut in and find those chase ways and do that sort of thing for running all of our electrical.” He figures that, over an entire project, using SIPs saves him four to six weeks in on-site construction time.
There are also other cost advantages. Building SIPs roofs makes attics warm and dry, which means they become usable indoor space, Clifton says. Depending on the local wildfire-related building codes, it may not be necessary to add structural vents to them. Omitting these vents saves money as well.
HVAC costs can also be lowered. “You can downsize your heating and cooling system because of the energy efficiency of the SIPs,” Wilson says. “I think building with SIPs is something we should be going towards.”
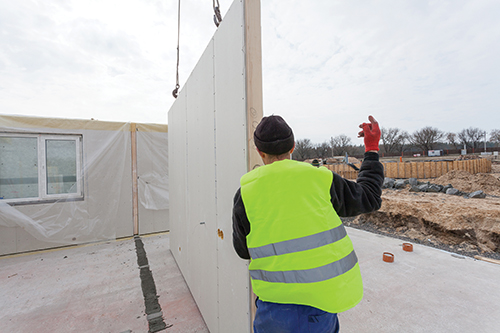
Kat Friedrich writes about energy, engineering, physics and technology. She is a graduate of the University of Wisconsin-Madison College of Engineering and is the editor in chief of Solar Today.