New research is a first step in quantifying its thermal performance.
- Oak Ridge National Laboratory tested mass timber wall assemblies in three simulated climatic zones. The research is timely given the growing use of this building system.
- Total annual energy savings for the relatively mild climate of Los Angeles, Calif. was good, but the walls didn’t perform as well in the hot and cold climates of Golden, Colo. and Houston, Texas.
- The financial implications will depend on energy costs and on time-of-day rates.
Proponents of solid mass wood walls often claim that this type of construction creates a thermally-efficient building envelope. Is there any proof to support that claim? A recent research project is the first step toward answering that question.
In June 2022, the US Department of Energy (DOE) published a report called Impact of Mass Wood Walls on Building Energy Use, Peak Demand, and Thermal Comfort. It summarizes research on solid mass wood walls conducted at Oak Ridge National Laboratory (ORNL) and funded by the DOE’s Building Technologies Office.
According to the report, only 1.5% of all new homes in the US, and 7% of custom homes, are built with solid mass wood walls, but demand is increasing. In 2019, the US mass wood wall market was over $170 million and is projected to reach nearly $400 million by 2025.
Mass wood framing involves the use of large, solid wood panels for wall, floor and roof construction. They include logs, glulams (glue-laminated timbers), laminated strand lumber, CLT (cross-laminated timber) and other large structural composite lumber products.
In this research, only CLTs were tested. They were compared to ordinary walls with lightweight framing.
Why This Research?
According to the researchers, current designs for CLT buildings focus on structural and fire issues. There’s no guidance on how to make the best use of the thermal mass offered by solid wood walls. This research is a step towards assembling data that can be used by CLT producers to market their products and by code officials to gauge performance statistics.
The research results show that there is a benefit from improved energy efficiency by building with CLT, but that the amount will vary with the local climate.
Why Now?
This research is timely because the International Code Council (ICC) recently approved a set of proposals to allow taller wood buildings as part of the 2021 International Building Code (IBC). The code sets fire safety requirements, as well as allowable heights, areas and number of stories for tall mass timber buildings.
The ICC also published the most recent version of the IECC (International Energy Conservation Code) in 2021. This research was intended to determine whether the tested walls met its requirements. At present, three state codes — California, Vermont and Washington — meet the requirements of this code.
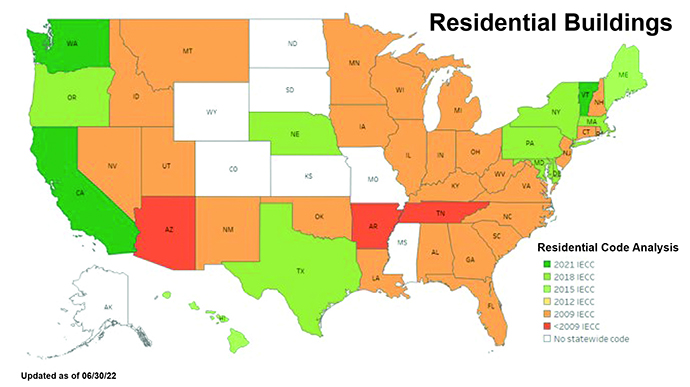
How Was the Research Conducted?
First, the researchers did lab tests to confirm the accuracy of a computer simulation model, EnergyPlus. They also conducted a review of the relevant scientific literature and noted that it confirms the accuracy of EnergyPlus.
They tested four wall assemblies: two lightweight walls and two CLT walls.
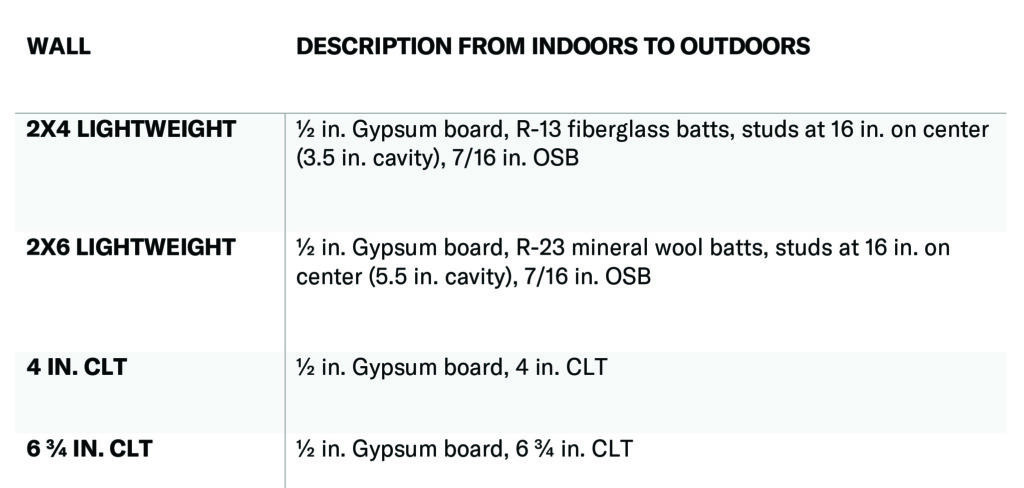
Temperature sensors and heat flux sensors were placed on specific locations on each wall. (Heat flux is the rate of heat energy passing through a surface.)
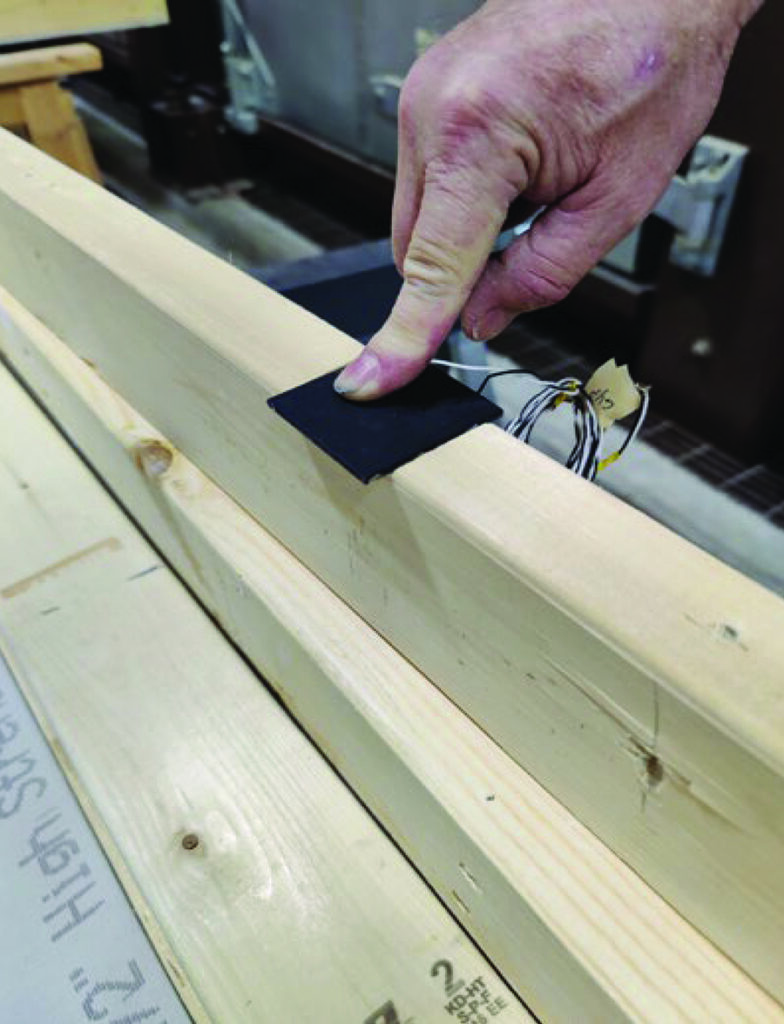
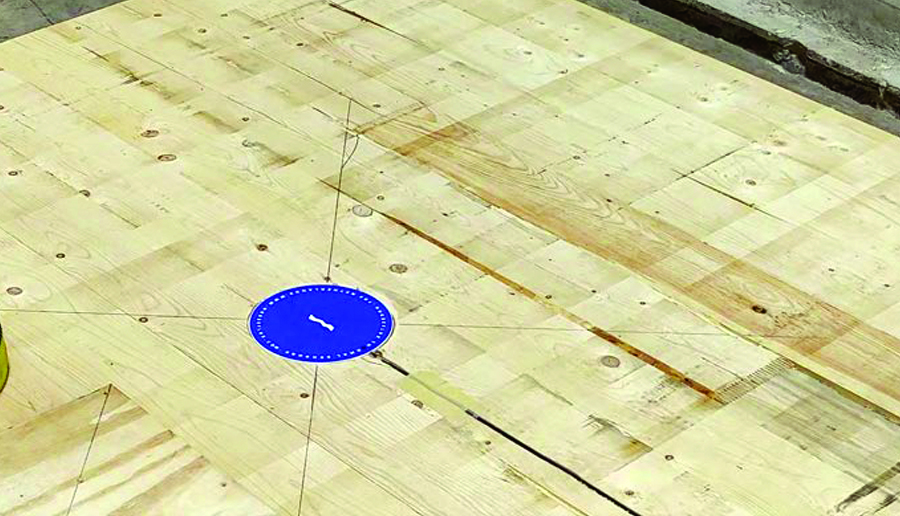
The walls were placed in a climate simulator at ORNL, where researchers used heat lamps to simultaneously expose them to artificially-created outdoor winter temperatures, then to outdoor summer temperatures (with a rest period in between).
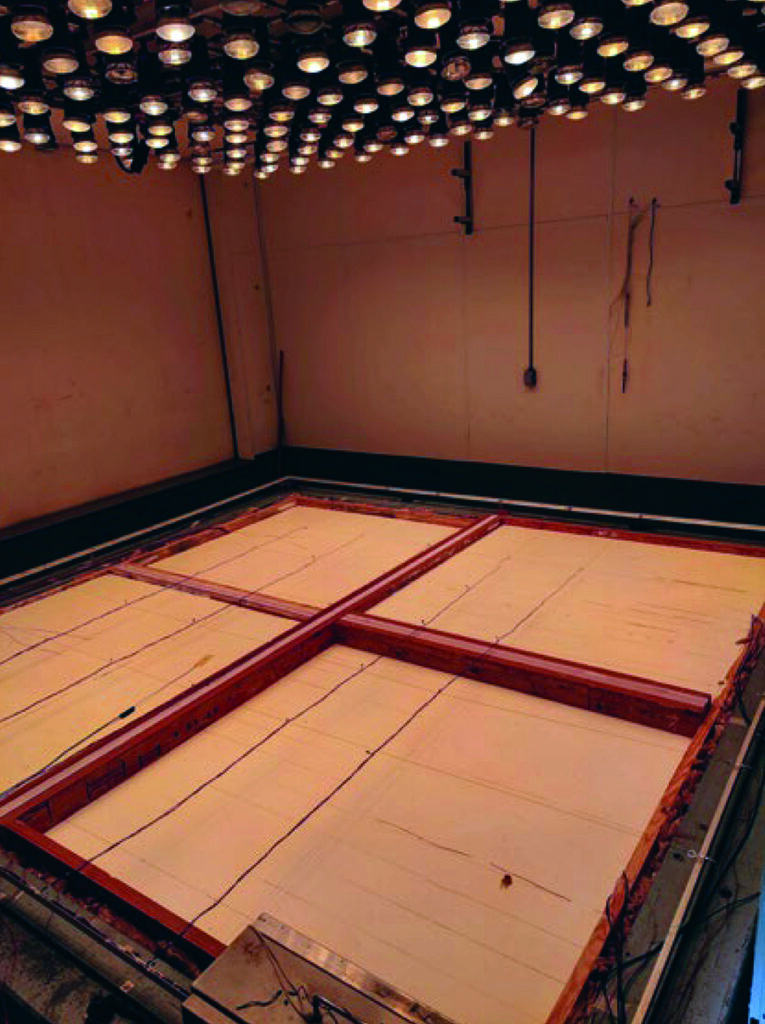
The temperature on the ‘inside’ of the wall panels was maintained at a steady 69°F.
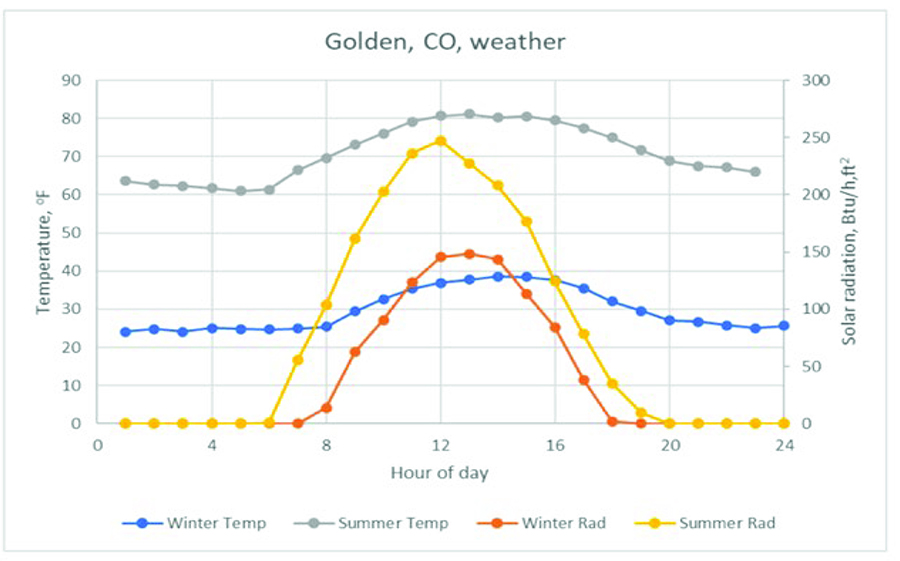
The first step was to confirm the accuracy of EnergyPlus. This was done using temperatures for Golden, Colorado, which has “cold winters and sunny days, providing large temperature swings on walls between night and day.” After validating the computer model, the researchers used the model to evaluate the impact of mass timber on peak demand and energy use of a one-story home.
Computer Model Tests
To compare CLT construction with ordinary lightweight walls (the baseline for comparison), the researchers used the US Department of Energy’s prototype single-family detached home. This is a computer model that can simulate the energy performance of a house in a given climate.
The prototype house was specified to have two stories, a heat pump for space conditioning, a concrete slab foundation and a heated/cooled area of 2,377 sq. ft. It met IECC 2021 and IRC (International Residential Code) 2021 requirements for walls. The model can take airtightness into consideration, but Mikael Salonvaara, Senior R&D Staff at ORNL, explained that the researchers “compared the buildings using the same airtightness.” This made it possible to isolate the mass effects.
For comparison purposes, the researchers also simulated a hypothetical set of walls that were the same as the baseline walls, but with R-100 continuous insulation. This created “an extreme case where walls would have no heat loss or gain.”
Simulations were carried out for specific cities in three different US climate zones: Houston, Texas (2A), Los Angeles, California (3B), and Golden, Colorado (5B). Salonvaara said, “We chose the climates in this study so we’d have one hot and humid, one cold and dry and one mild climate.” The results in Houston, for example, will be largely applicable to other locations in zone 2A.
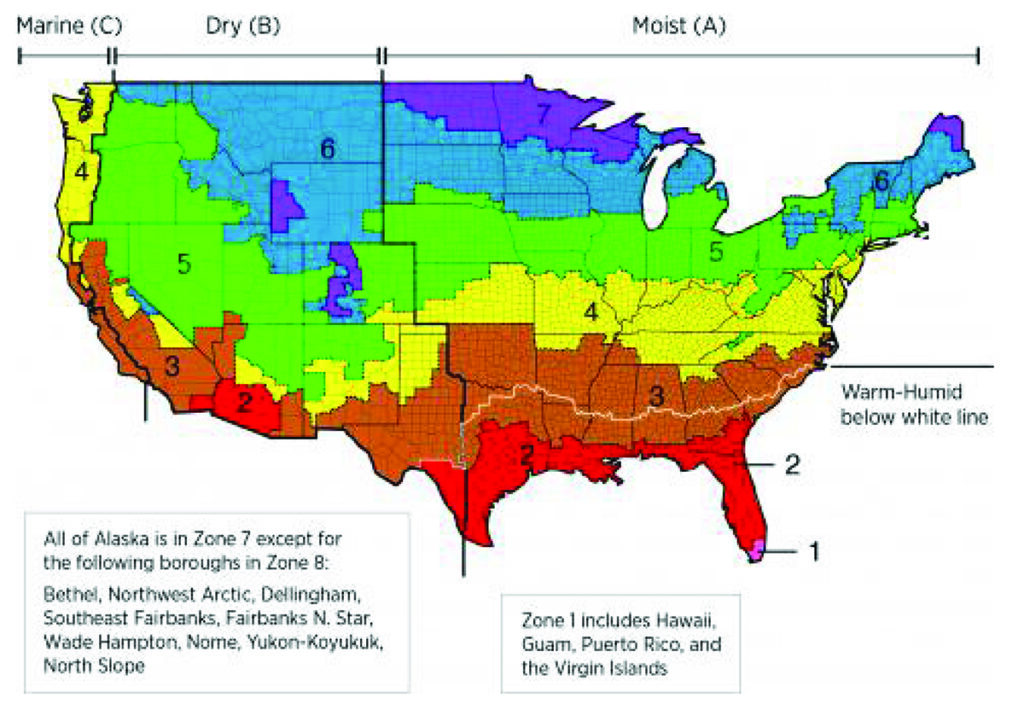
What Did They Discover About Energy Usage?
Energy savings results are summarized in the following table. Note that even if total energy used is the same as, or more than, for ordinary walls, energy costs may be lower if a greater proportion of the energy is used at non-peak times. That’s because non-peak energy typically costs less than energy used during peak hours. (More on that below.)
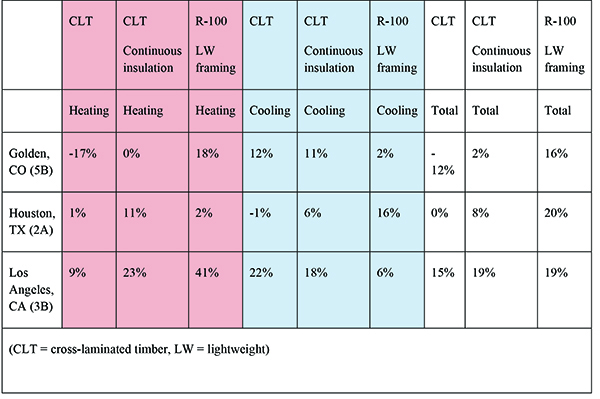
Golden, Colorado (Cool, Dry)
Let’s first look at the results in Golden. When considering energy use for heating, a bare CLT wall uses 17% more energy than baseline for heating. With continuous insulation, it performs the same as baseline.
For cooling in this climate, bare CLT uses 12% less energy than baseline. With continuous insulation, it uses 11% less energy.
For overall energy use (i.e., both heating and cooling), CLT uses 12% more than baseline. With continuous insulation it uses 2% less energy than baseline.
It appears that in a climate like Golden’s, CLT without continuous insulation appears not to have energy savings at all. (Of course, CLTs may have other benefits over ordinary walls that aren’t discussed here, such as earthquake resilience.)
Houston, Texas (Hot, Humid)
Now let’s turn to Houston. For energy savings on heating, CLT with continuous insulation uses 11% less energy than baseline in Houston — better than both CLT by itself and lightweight framing with extreme insulation.
CLT by itself was slightly worse than baseline for cooling energy, while CLT with continuous insulation had cooling energy savings of 6% compared to baseline. It wasn’t as good as the hypothetical lightweight framing with extreme insulation, which was 16% better than baseline.
Total energy usage with CLT by itself was the same as baseline. With continuous insulation, it had annual savings of 8%. (Lightweight framing with R-100 had 20% energy savings compared to baseline.)
Los Angeles, California (Warm, Costal)
In L.A.’s mild climate, a CLT wall with no insulation saved 9% on heating energy and, with continuous insulation, it saved 23% compared to baseline. (The lightweight framing with extreme insulation saved 41% in heating energy.)

For energy savings on cooling, CLT by itself performed 22% better than baseline. With continuous insulation, CLT didn’t save quite as much — 18% compared to baseline. In both cases, CLT performed better than the hypothetical R-100 scenario, which had cooling energy savings of 6%.
For total year-round energy savings, CLT with continuous insulation was equivalent to lightweight framing with extreme insulation. Both had energy savings of 19% compared to baseline. Without continuous insulation, CLT saved 15%.
Summary of the Three Climates
In Golden’s cold climate, mass timber without continuous insulation performed poorly, compared to baseline. With continuous insulation, there were modest energy savings. In this climate, to determine whether using mass timber would result in financial benefits for the building owner, it would be necessary to know both the difference in cost between peak hours energy and non-peak hours and, also, how much more CLT walls cost to build when compared to ordinary walls.
The researchers acknowledge that “In more extreme climates, such as the hot climate of Houston, Texas and the cold climate of Golden, Colorado, the savings are lower because of longer, steady hot or cold weather periods during which the thermal mass effects cannot balance the heat gains and losses as effectively as in milder climates.”
CLT excelled in the mild L.A. climate. Total annual energy savings were significant compared to ordinary walls — and, with continuous insulation, savings were as much as the hypothetical extreme insulation case.
Peak Demand
It’s an established fact that thermal mass helps reduce daily temperature fluctuations. In fact, one of the results of this research is that:
“Mass timber walls efficiently shifted heating and cooling energy demand to other hours away from the peak demand hour. As a result, the peak demand for heating and cooling was 30% to 50% lower with mass timber depending on the month and location.”
In places like California, where utility customers pay more for electricity during peak demand hours, reducing peak demand or shifting demand away from peak hours would reduce energy costs. Of course, the extent of the cost savings would depend on the difference in price between peak and non-peak energy.
This research shows that the energy savings one can expect from CLT depends upon local climate. And whether CLT is financially beneficial will depend upon local costs for construction and the difference between peak and non-peak energy costs.
Of course, there are many other factors to consider when deciding how to build, such as aesthetics, speed of construction, earthquake resilience and so on. But here we’re focusing on energy savings.
The Take Home Message
The bottom line is that energy savings will depend on location. L.A.’s climate is an example of where the use of CLT appears to significantly reduce energy usage. Other places in climate zone 3B would likely see similar benefits.
In the other climate zones tested, total energy usage wasn’t as drastically reduced, but depending on the local energy costs, using CLT may still reduce energy costs by shifting energy usage away from peak hours to cheaper non-peak hours.