The results could help streamline the manufacturing of modular apartment buildings and optimize hot water demand.
- Test module data was compared to that gathered from an established modular apartment building.
- The researchers looked at air infiltration, as well as electrical loads and the cost-effectiveness of solar.
- Results have been used to produce two reports, and the team is planning a follow-up project.
If you could install a modular apartment in a research lab and run tests on it, what might you learn? Answering this question has been the goal of an ongoing research project running at the National Renewable Energy Laboratory (NREL) in Golden, Colorado.
NREL’s staff have been taking sophisticated measurements of a modular apartment and comparing the results to data collected from the Eliot Flats modular apartment building in Denver, Colo. Both were produced by Champion Home Builders, a manufacturer based in Troy, Michigan.
Eliot Flats’ developer was Brice Leconte of iUnit, an Ashburn, Virginia-based company that builds high-performance modular communities. At the time of its completion, it was the highest-rated ENERGY STAR multifamily project in Colorado, and was also the first modular apartment complex built in Denver. Champion is Leconte’s manufacturing partner and he worked with them to build the NREL module.
Leconte says that the idea for the testing was sparked by a conversation he had with Chuck Kutscher, who was then the Director of NREL’s Buildings and Thermal Sciences Center.
Kutscher asked Leconte what his mission was. Leconte answered that it was “to build sustainable and attainable modular housing communities, from apartments to cottages.” He hoped that lessons learned from the prototype lab tests could be applied to future iUnit communities, as well as to those built by other builders and developers.
“It’s been a great relationship,” Leconte says of the NREL collaboration. “We’ve been able to test so many things.”
The laboratory staff did encounter some technical challenges in the beginning. “A modular apartment is something that’s normally not trucked down our driveway or trucked down our access road,” says Shanti Pless, Senior Energy Efficiency Research Engineer at NREL . “We had to closely coordinate the physical size of the unit so that it would actually fit into the high bay… in the Energy Systems Integration Facility laboratory.”
The design team also took steps to protect the apartment from the elements so that it could sit on an outdoor testing pad safely, Pless says. They used custom siding and custom sealants. The biggest challenge they encountered was figuring out how to add sealants and insulation underneath the floor, where the floor plumbing and the racking system for the trailer are.
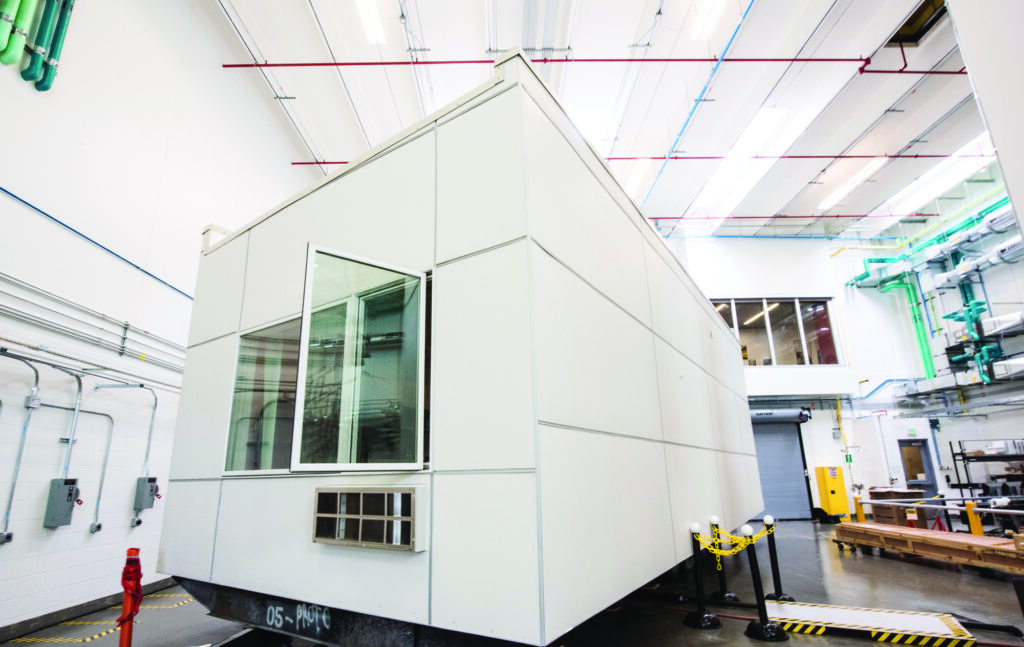
Infiltration Measures
The testing has included “technology integration opportunities around all-electric heating and cooling systems, around high-efficiency hot water integration into the unit, and a range of smart apartment control and engagement applications and demonstrations,” says Pless.
“The biggest value in this work was learning how to design these systems to be fully installed in the factory vs. on-site,” Pless says. “This looks like a classic design for manufacturing and assembly product-design exercise but applied to all-electric and high-efficiency systems in modular apartments.”
Pless’s team placed the six-sided volumetric modular box containing the apartment on an outdoor testing pad. They measured the air infiltration continuously to determine airtightness under different weather conditions.
“This work is ongoing, so [there are] no published results yet,” Pless says. “We have completed a year’s worth of data collection measuring the infiltration for a range of weather and wind conditions, which we will be able to then compare to the typical single measurement and calculation approach to quantifying annual energy savings for air tightness. Typical site-built homes do a single test and extrapolate infiltration over the course of a year based on calculations and energy-model predictions.”
Ordinarily, Pless says, airtightness tests involve creating a pressure difference between the inside of a building and its outside and then measuring the air flows through the cracks.
However, this doesn’t lead to extensive insight about pressurization, depressurization, wind profiles and temperature profiles. To learn more, Pless says, the NREL team made use of tracer gases, in which they injected the gasses into the space and measured the airtightness of the apartment. One example of a tracer gas would be concentrated carbon dioxide.
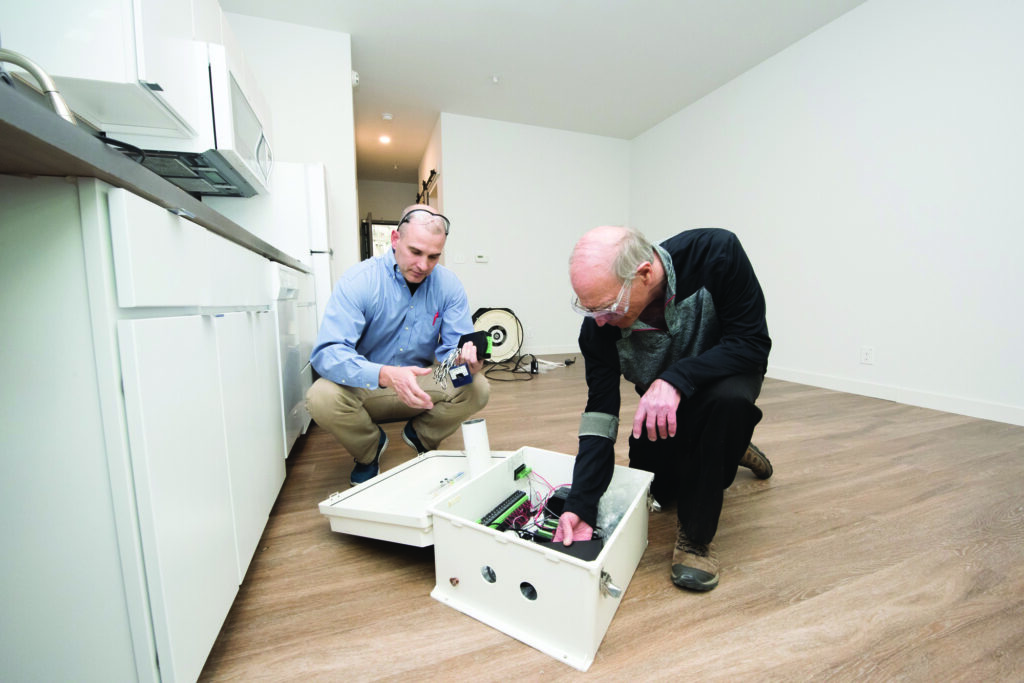
Electrical Testing
Electrical measurements were key to assessing the performance of the apartment and the apartment building. For Eliot Flats, Pless says NREL tracked the energy use of each apartment, including heating, cooling, lighting, appliances and hot water.
“We’ve done a lot of electrical subpanels, outlet-level metering at the circuit-breaker level using minute-by-minute power data, [and] current data for specific loads,” Pless says. “We also measure apartment-level electric data at the minute level.”
Measuring complex profiles for electrical equipment allows NREL to use fewer sensors for each apartment. “We can install one sensor for the whole apartment and disaggregate individual loads,” Pless says. “When the hot-water tank turns on, we know exactly what that load profile looks like.”
Data from the tests helped NREL produce a publication on submetering hot water in modular apartments with the (pithy) title “Meter-based synthesis of equipment schedules for improved models of electrical demand in multifamily buildings.” It’s posted at tandfonline.com.
According to Pless, the authors developed a new method for “using electrical-meter data to synthesize realistic equipment-use schedules that can improve models of electrical demand in buildings, with specific applications for domestic hot water use.” The results include “actual hot-water-draw profile variations across 40 different modular apartments.”
NREL has also created a series of computer models of the year-round performance of the apartments in typical Colorado weather, Pless says. These models will allow NREL to explore the effects of reducing the cost of an apartment or improving its efficiency.
Solar Cost Data
One research question that NREL wanted to answer, Pless says, relates to the cost of residential solar. The Eliot Flats apartment building included solar power.
“As we know, the cost of residential solar is still pretty high compared to… large commercial utility-scale or community solar,” Pless says. “Oftentimes, installation time and soft costs and permitting are higher than the hardware itself in the residential market in the United States. Those installation costs can be partly addressed by how it gets installed.”
Soft costs are defined as expenses that do not directly relate to construction. The team at NREL is also investigating what would be involved in installing solar power on a modular building unit in a factory, Pless says.
The team found that factory installation of energy efficiency and renewable energy technologies had many coordination and cost benefits. They used factory information modeling and a case study to analyze an approach for constructing factory-installed solar+storage that resulted in a 27% total cost reduction compared to on-site installation.
The results have been published in a paper through the US Department of Housing and Urban Development. The paper, Exploring the Potential of Factory Installed Solar + Storage for Homebuilding, is available at huduser.gov and jstor.org.
“We identified both potential barriers (for example, first cost, permitting, utility interconnection, finished module transportation and future battery replacement) and value (such as resiliency benefits, opportunities for utilities, clean energy equity for affordable housing and new markets for modular factories) of incorporating solar and storage into factory-built housing,” Pless wrote.
“Using the cost-reduction results from the case study, the team evaluated the homeowner economics and duration of backup power using the NREL System Advisor Model in six locations in the United States. Results showed that in five locations, homeowner net present value (NPV) is positive with long-term, low-interest financing through a mortgage.
The SAM analysis showed that, in almost all cases, the solar+storage system could power 25% of the electricity needed in a home for four days, and under some scenarios, up to 100% of the load for four days.”
This question about cost savings also applies to other energy and sustainability features for affordable housing such as heat pumps, air barriers and smart apartment controls, Pless says. Factory construction of buildings can reduce the cost of the installation of these features.

Follow-Up Research
After the success of this initial collaboration, NREL and iUnit are looking to continue their work together by building a net-zero, modular small house that would be sited and tested at the laboratory. This project is in its initial design phase, Leconte says. With this house, Leconte plans to include solar power.
“Eliot Flats had solar installed on-site after construction,” Pless says. “We hope to install solar in the modular factor, gaining the time, cost, quality and integration benefits that are inherent in modular factory construction processes.”
Pless says NREL chose to collaborate with iUnit because LeConte was willing to spend time and resources to “partner on answering questions around affordability and decarbonization.” Most developers don’t choose to participate in research to this extent.
Reflecting on the value of this first project, Pless says, “We’re not inventing new technologies for modular, we’re inventing new ways that the existing technologies can be best packaged into the modular form to be as cheap as possible when installed.”
Other companies can learn from the lessons of this project by discussing the research results with Pless and Leconte.
“We do plan to publish our broader learnings with our partners, such as iUnit,” Pless says. “We have many modular partners and use specific partners’ projects to inform our broader industry publications.”
“[The] partnership is not just for Champion and iUnit, but it’s also really to share that information with the rest of the industry,” Leconte says. “The goal with iUnit has been to be on the cutting edge and push the limit on these different initiatives that other developers and other practitioners can follow.”
Kat Friedrich writes about energy, engineering, space and technology. She is a graduate of the University of Wisconsin-Madison College of Engineering and is the editor in chief of Solar Today. Photos by Dennis Schroeder/NREL.