Some advice for architects and designers new to this way of building.
- The size of the project will help determine the best approach: full modular, hybrid, or stick-built with kitchen and bath pods.
- The modular process requires a great deal of collaboration between the designer, the fabricator and the general contractor.
- The process of designing around modules can be seen as an evolution of the way designers already work, just on a different scale.
When working on their first project with major offsite components, what should architects and designers do differently from when they are designing a conventional project? To get some insight, we talked with two experienced designers at Gensler, an architecture, design and planning firm with 53 locations across North and South America, Europe, Asia and the Middle East.
Our interviewees are Michael Hendershot, the South-Central Region Practice Area Leader for Senior Living and Brooks Howell, the Global Residential Leader.
Their modular experience includes work on citizenM hotels, multifamily apartments and student accommodations. In addition to designing volumetric modular projects, they’ve also worked on projects that incorporate pods, like restrooms in hotel conference centers.
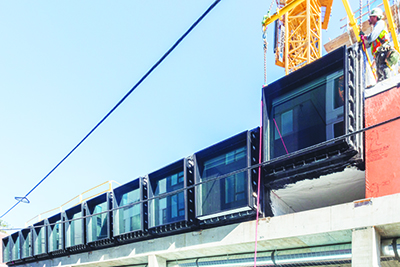
Photo credit: Heywood Chan
Understand the Market Trends
The first piece of advice applies to any project, modular or conventional: know the trends in the market where the building will be located. Some trends are nationwide and include bigger spaces. “There’s currently a trend in multifamily apartments, including senior housing, towards larger units,” Hendershot says.
In fact, apartments targeting seniors will have to compete with aging-in-place remodelling. Aging in place is when seniors find a way to continue living in their own home (often a single-family house), perhaps by remodelling or by installing things like ramps and stairlifts. “Those seniors aren’t looking to go into a smaller space,” according to Hendershot. That’s one reason senior apartments have gotten larger, but smaller spaces can be acceptable to this population if the building offers other compelling benefits, such as great amenities.
Another piece of advice is to consider using modules for some of the building. Modular construction naturally lends itself to small, repeatable units, so if the project doesn’t call for volumetric modules, designers might still consider using kitchen or bathroom pods that slot into place. Designing a building that incorporates pods can reduce project time and the pods are repeatable products so there are potential cost savings, Hendershot says.
The next step up from pods might be to consider a hybrid building. “You could design, say, a bedroom-bathroom module, so you can get repeatability and economies of scale. But you could still have stick-built living rooms and kitchen areas, which tend to be larger and more open,” Hendershot says. This is actually a common approach: the large common areas and amenity spaces in modular multifamily projects — such as fitness rooms and event spaces — are typically stick-built.
Despite the general trend towards larger living spaces, Hendershot points out that there is still a market for smaller units. For example, affordable apartments are typically smaller and come in more standardized unit types. The location of the building also makes a difference. “In more urban environments, there’s a trend towards smaller — even micro — units,” Hendershot says.
Specialty markets may also be a good place to consider small modular units. An example is “Memory care” apartments, which are designed for people experiencing cognitive decline due to Alzheimer’s disease and other conditions. “Memory care isn’t in competition with other multifamily buildings or with aging in place,” Hendershot explains. “The residents just need a space for a bed, bathroom and a small general living area, mainly because the point of memory care is to get residents out into the common areas, socializing with other people, to avoid further cognitive decline.”
The point is that the size of the living units, as well as of the other spaces in the building, are factors in how much sense it makes to use modules or pods. Size also influences how the offsite components should be used in the building — for entire living units or just for parts of units.
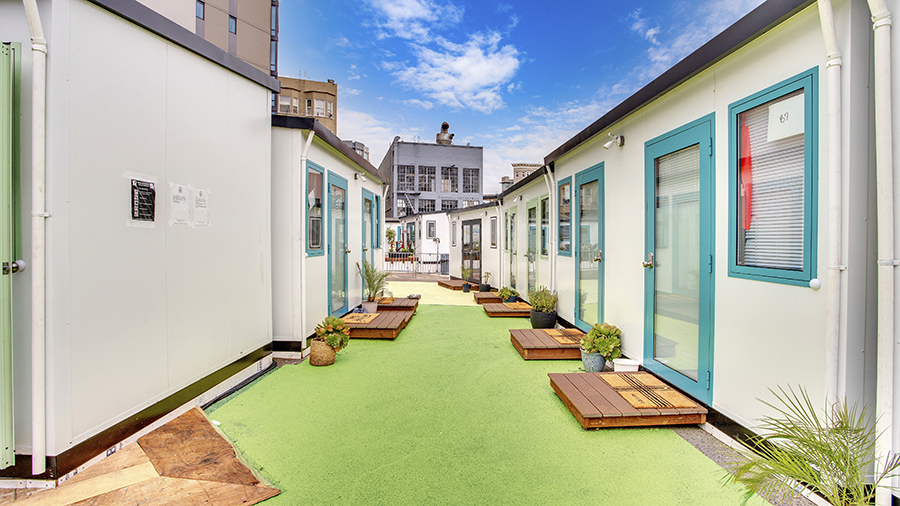
Photo credit: Gensler
Working with the Fabricator
When using offsite components in a building, a major difference for a designer, when compared to conventional construction, is the need to collaborate with the component manufacturer.
“When you’re designing for modular, you work alongside the fabricator. First, the fabricator will give the designer information about tolerances, where plumbing lines and electrical outlets go. You shouldn’t make assumptions about those things,” Hendershot says.
“After the designer has drawn the module, area, or room using the data from the fabricator, that drawing goes back to the fabricator so they can generate their shop drawings. The shop drawings are sent to the designer and the general contractor for review,” Hendershot explains. If the drawings are acceptable, the manufacturer uses them to fabricate the modules or pods.
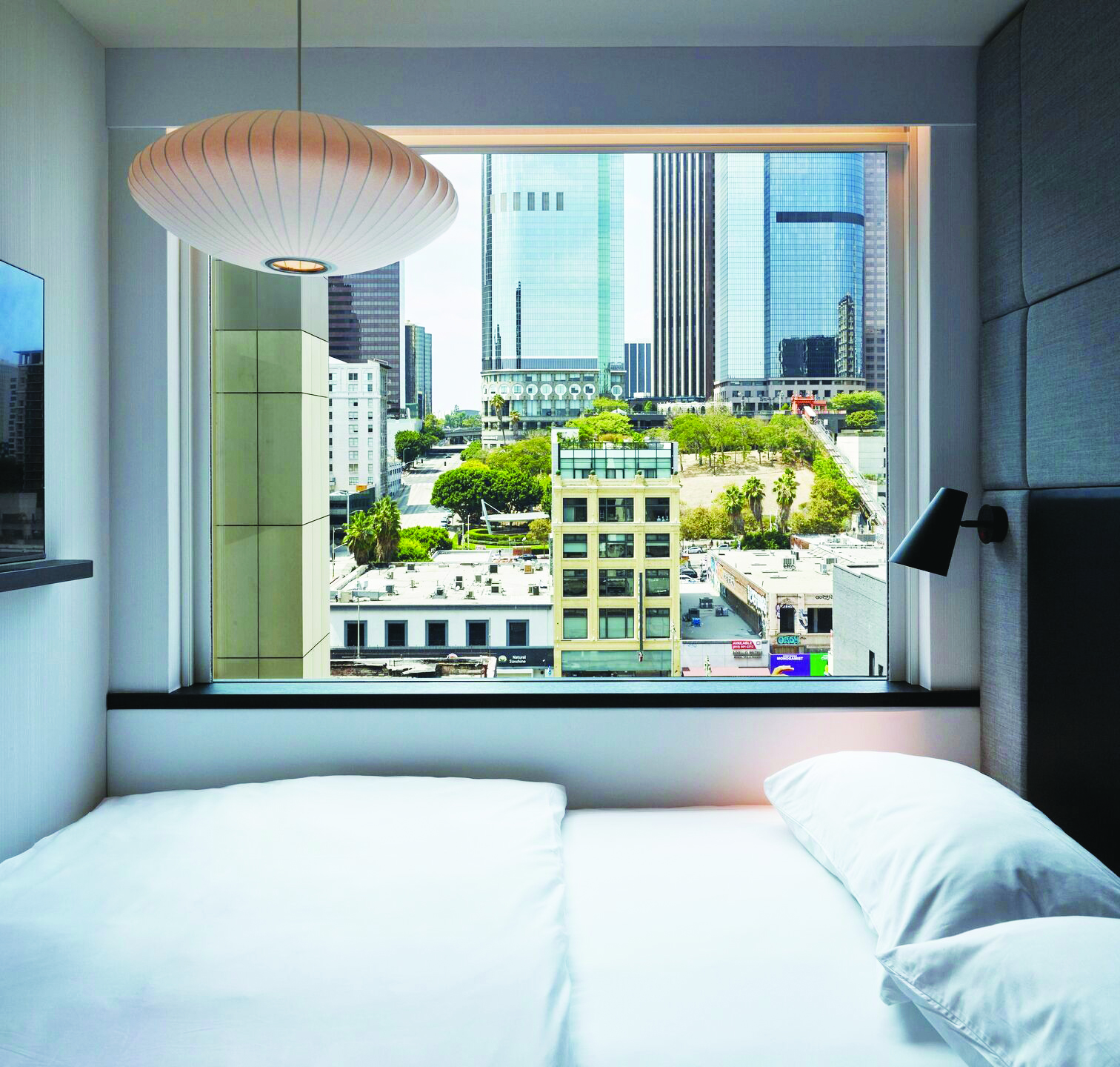
Photo credit: Richard Power, courtesy of citizenM
One way to make a design more efficient is to limit customization. “Multifamily projects are typically over-customized. It’s not uncommon to see a project with 350 units have 35 or 40 different unit types. That causes a lot of problems in the field and adds cost to the project,” Howell says. “This is even more crucial with modules or pods. Get really disciplined in having, say, only three kitchen types.”
Of course, some designers balk at having to tailor the building design to the needs of the modules or pods. But according to Hendershot, this is simply an evolution of existing practices. Just as designers are used to designing around small components like plumbing fixtures, modules and kitchen or bathroom pods become objects around which the designer designs — they’re just bigger objects.
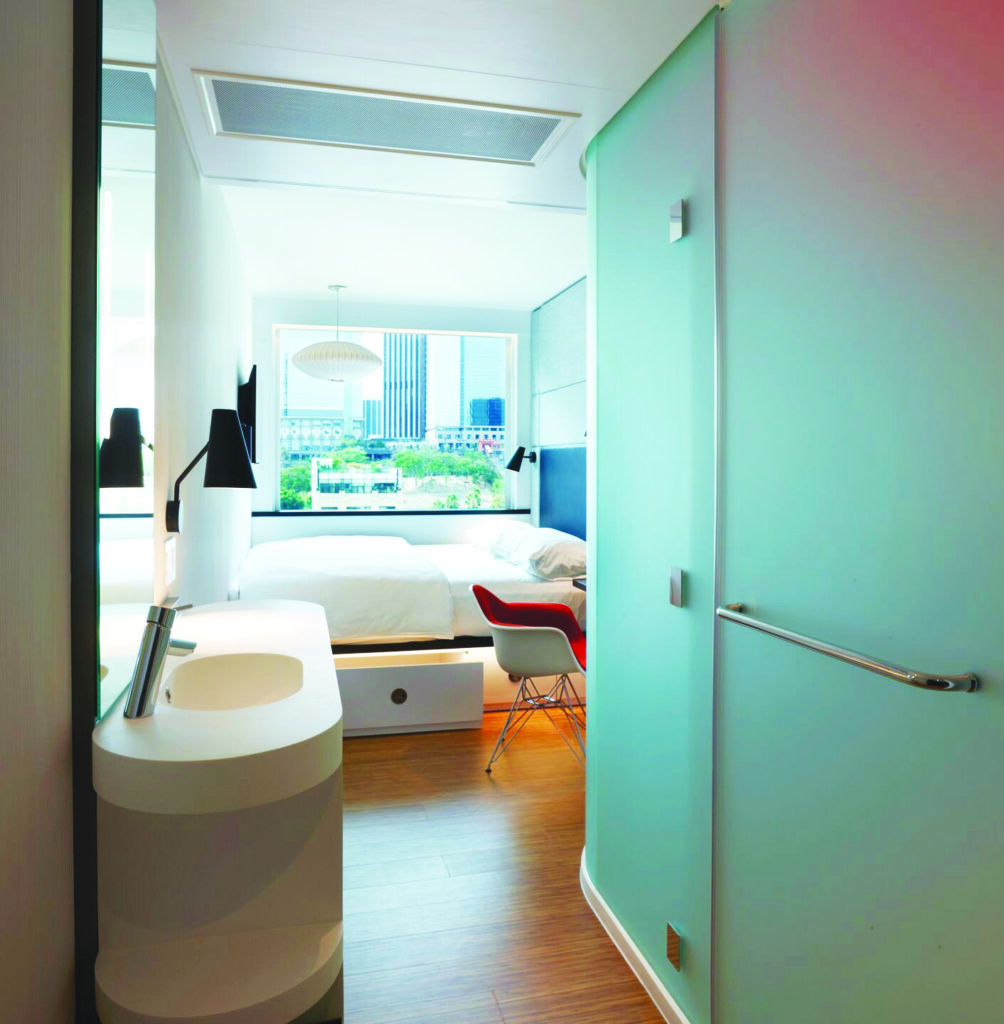
Photo credit: Richard Power, courtesy of citizenM
Installation
Perhaps one of the most obvious ways that using pods or modules differs from conventional construction is that the offsite components are very big. This means that getting them into place in the building isn’t trivial.
For volumetric modules that also form the structure of the building, sequencing is determined by the order in which the modules need to be stacked. For pods or modules that go inside the building’s structure, “You have to think about how the module or pod is going to get into the building,” Hendershot says.
In a conventionally built building, the bathroom and kitchen fixtures would be carried up the stairs or in the elevator. “But if you’re designing with pods and modules, you need to think about how that whole module is going to get into the building in one piece. That means thinking about floor-to-floor heights, openings on the exterior walls, and the need to leave room to roll or slide the unit around into its final position,” Hendershot explains.
In addition, he notes that “unlike with conventional bathroom installation, if you’re installing bathroom pods, the building will likely be open to the elements in some way so you can get the pods into the building. So weatherproofing needs to be considered, too.”
Although the general contractor will determine the sequencing of any construction project, “the GC and the design team need to work together to understand how the modules affect sequencing and how best to facilitate that. An example would be designing window or balcony door openings large enough to accommodate the delivery and installation of a kitchen pod in an apartment,” Hendershot says. “A good design will reflect the GC’s input.”
So, be prepared for lots of collaboration throughout the project schedule.
Zena Ryder writes about construction and robotics for businesses, magazines, and websites. Find her at zenafreelancewriter.com.