This panel manufacturer has embraced factory automation and a design-build approach
- Blueprint Robotics builds multi-unit residential projects with floor, wall and roof panels that include the wiring and plumbing runs. They chose panels over modules because they offered more architectural flexibility and had fewer shipping issues.
- Before they begin manufacturing, the company uses 3D software to create a digital twin of the. It specifies the exact number and size of every detail, from structural members to fasteners. This provides customers with a high level of certainty.
- The 200,000-square-foot factory makes extensive use of automation. Machines do the cutting, nailing, and drilling, while employees rough in the MEP and sprinklers.
After spending more than 40 years in construction and real estate development, Jerome Smalley knew there needed to be a better way to build. In 2015, he partnered with entrepreneurs Karim Sahyoun and Sascha Bopp to create Blueprint Robotics, an advanced off-site building system that combines Building Information Modeling (BIM) technology with robotic machinery to create precision building components for wood-framed construction.
Blueprint is one of only a handful of companies in North America using machines in this way for industrialized construction. “There just aren’t a lot of companies [doing this] in the US and certainly not a lot that has the scale of a facility that we have,” says William Grothmann, Director of Sales for Blueprint.
The timing couldn’t be better; the Rubik’s Cube of concerns that plague the building industry right now seems almost unsolvable. A labor shortage of 650,000, the need for more housing, material shortages, supply chain disruptions and inflation. No matter the contortions, the puzzle won’t come together in a nice, neat cube. But Blueprint Robotics’ methodology and value proposition offer a pathway that others might emulate.
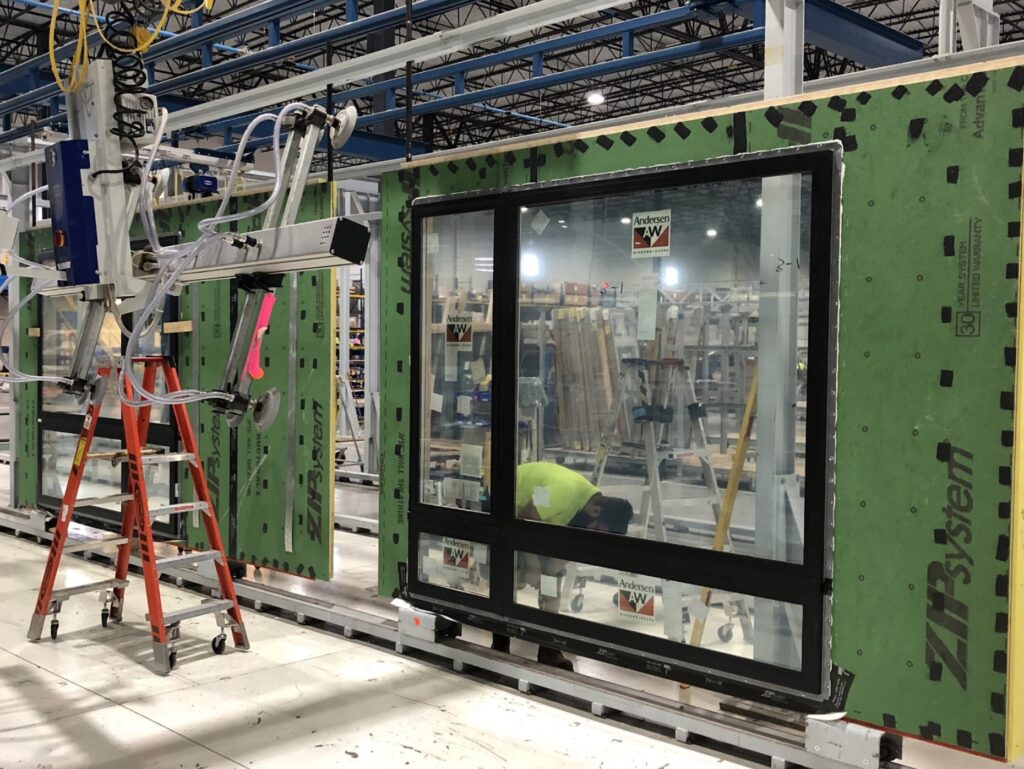
The Set Up
Investors at Invus, a private equity group with offices in New York, Paris and Hong Kong, provided Blueprint’s initial start-up capital. Blueprint had a factory built to their specifications in an industrial park in Baltimore, Md. Weinmann, a leading manufacturer of machines and plants for timber construction (part of the Homag Group and headquartered in Schopfloch, Germany), and Stiles Machinery, based in Grand Rapids, Mich. (also a subsidiary of Homag), assisted with factory planning and development.
Blueprint’s founders and executives traveled to Germany to visit facilities that employ the same, or similar, machines and technologies. They purchased numerous multi-function bridges (a versatile machine that can be outfitted with various tools from nail or screw guns, to saws, routers, drills and other tools), carpentry machines (which process top and bottom plate material, studs and beams), framing stations (which nail the walls together), pack-out machines (which assist the employees with loading the heavy walls onto a pallet), and trolleys (which transfer the wall from one station to the next). It took about a year to build the 200,000 sq. ft. facility, which was ready for move-in in April 2016.
Blueprint began by creating panels for single-family residential structures, but by 2019 they switched to focusing solely on multi-unit residential, including apartments, student housing and senior living. “We made the switch because of scale and repeatability of design,” Grothmann says. “There are efficiencies in creating machine files, manufacturing and assembly. When we can do that at scale, we can fill the factory.”
The factory produces wood-framed structures in a panelized format: floors, walls, and roofs. Machines do all of the cutting, nailing, and drilling. Panels include all the mechanical, electric and plumbing pathways, and Blueprint employees install the rough-in for MEP and sprinklers. “When we do vertical with assembly on-site we follow behind with MEP installers to make the inter-panel connections,” Grothmann says. “That’s a lot of scope of work and where much of the schedule compression occurs.”
The company takes things further, however. “We’re set up much like a general contractor when it comes to project management and we’re managing the procurement of all the materials involved with our scopes of work very closely,” Grothmann says. “It’s one way we stay on top of our supply chain, which can be difficult to navigate these days.”
Blueprint works with architects and designers and other building stakeholders, such as general contractors, owners, or consultants, from pre-construction to project completion. Blueprint has chosen this route based on the value proposition it offers builders. “We’re delivering a higher level of cost certainty and higher quality and doing it faster. There’s a need for this because of the labor market,” Grothmann says.

Pre-construction Coordination
Using a coordinated approach similar to design-build, Blueprint looks at projects holistically. Their scope of work includes the creation of a digital twin, virtually constructing the building with Dietrich’s 3D production engineering software. The digital twin is then converted to machine files, which means the final model is extremely precise. “Every structural member, stud, joist, everything, is the exact size it will be,” Grothmann says. Knowing the exact number of every nail, for example, raises the level of cost certainty.
And working with BIM, they have a clear way to coordinate and resolve the “clash” (where two building elements might interfere with one another), for example, between “MEP and the structure,” says Grothmann. “We refer to it as a ‘real-time shop drawing’ process because we include the project team as a member.”
All the upfront considerations lead to a reduction in risk for the ultimate builder or owner.
Less Labor Needed
Blueprint pulls permits, does the required site work under the slab and makes a return trip to trim out the MEP scope. They hang lights, plumbing fixtures and HVAC registers.
“When it comes to the rough carpentry package — all the wood structure, with sheathing, weather-resistant barrier and windows installed — we do all the assembly in the field ourselves and we bring the material-handling equipment like the cranes. We handle logistics, transportation — everything involved with that scope of work,” Grothmann says. “We’re striving for the general contractor to be able to cross out five to seven trades on their current estimate and then plug our lump sum, have all of the same scope covered, and be able to easily compare cost.”
The method is particularly appealing to builders of multi-unit projects because the quicker a project is ready, the quicker units can be sold and rented. “On a four-story building on slab, Blueprint Robotics’ scope could be 60% of the building’s construction. To have that locked in with no change orders is significant to an owner,” Grothmann says. “Because of the time savings, it could be finished several months earlier.” This allows an owner to get their first month’s rent earlier, and to convert their loan from construction to permanent earlier as well.

Panel Decision
Blueprint has chosen to focus on panel creation and not produce volumetric modules (although they will build modules as pods, such as bathrooms and mechanical rooms).
For one, the company has flexibility in architecture. Grothmann points out that they can build off a permit set and construction documents and get involved in a project at any time. “With modular, a project needs to be designed for volumetric modular from the beginning.” He adds, “The fact that we’re building in a panel format means we essentially have no design limitations and can build any architecture.”
Also, in producing panels, as opposed to modules, transportation is less of an issue; they don’t ship permitted loads and can go through bridges and tunnels without a problem. “We’re not shipping air,” (which you would be doing with a volumetric modular) Grothmann says, which keeps down transportation costs. The company now has its own trucks and trailers.
Although the company was launched in 2015, it didn’t begin production until about 2017 when it began with single-family attached and detached homes. Only two years ago did they find their niche of multi-unit housing, and then as it did for everyone, the pandemic slowed them down. Blueprint had its largest revenue year in 2021. Their projects average around $7 million and they’re gearing up for about 15 projects in 2022 in and around Maryland, Washington DC, Virginia, Pennsylvania, New York and New Jersey.
Now the company employs about 100 people, including production engineers working from the company’s two satellite offices: one outside of Munich, Germany, and another outside of London, England. They’re planning a second facility in the Northeast, which will be online in the first quarter of 2024. Plans call for an over 400,000-square-foot facility with the capabilities of processing cross-laminated timber and mass timber so they can build tall post-and-beam glulam structures with CLT decks. Says Grothmann, “We plan to continue to refine and expand our scope of work and footprint across the US with new factories every one to two years.”
Wood If They Could
Being environmentally friendly is part of Blueprint Robotics’ ethos. The company has chosen to use wood and not steel because, as William Grothmann, Director of Sales, says, “Steel is a very carbon-heavy product. Wood is a renewable resource and a lot of the projects that we’re on have requirements for environmental and social governance. Projects may get additional funding for meeting Passive House, Net Zero or carbon neutrality goals, for example, and wood is how you get there.” The factory itself produces little wood waste and what there is goes back into producing energy.
About one-third of their projects meet Passive House standards. Walls are insulated in the factory with an ISO blow machine that’s on one of their Weinmann multi-function bridges. The product has a super-insulated envelope, is airtight and includes high-performance windows.