When you switch to building with components, time saved is money earned. This tool helps you quantify that extra profit.
- Once builders understand the true total cost impact of the time required to build a home, it changes many of their assumptions.
- The author’s Saved Day Calculator calculates how the time saved by using components affects the company’s build time, production output and bottom line.
- The ability to input both fixed and variable costs ensures an accurate estimate.
Why is it taking the industry so long to adopt offsite components at scale? This is the third article in a four-part series, and as I detailed in my last two articles (see the February and March 2025 issues), the answer is that builders don’t understand their true costs and how components can reduce those costs.
In Part 1, I laid out the basics of the big picture. In Part 2, I dug deeper into the 25+ elements that must be considered in a True Total Cost (and benefit) comparison of on-site to offsite methods. In this article, I introduce a proven, practical tool that can significantly change your analysis of cycle time savings — The TrueNorth Saved Day Calculator. Once you’ve calculated the true cost/benefit of a saved construction day, you will see how the time-savings from using components makes you more profitable.
The Sausage Line
Early in my career with a large national builder, I spent more than a month with our Southern California division. This group was literally obsessed with the primacy of the build schedule. For them, it was an all-day, every-day focus and any lost day in construction brought cries of anguish and gnashing of teeth.
I confess that I thought them a bit overdramatic. “Okay, so we lost a day, but can’t we make it up? Work late! What about Saturdays? Put a couple more guys on the crew.” “No!” came the emphatic response, “It’s the sausage line!” Totally lost, I didn’t even try to hide my ignorance of what they meant.
The president of that operation, now deceased, was a charismatic guy named Craig who decided that I simply had to understand the concept of the sausage line, and he nominated himself to beat it into my head.
In Craig’s world, each day was an irreplaceable commodity. He kept trying to explain that when you miss a day in the build schedule, no matter what actions you take to try and compensate for it, you never get that day back — it, and the margin associated with it, is gone forever. Being a Detroit, Michigan guy, that clicked for me when I envisioned the building process as an assembly line, whether for components of sausages, vehicles, or homes.
I had toured the Ford F150 assembly line in Dearborn, Michigan, where truck frames came down the line for their components, one after another, with no stops and only enough gap in between for a worker to maneuver. At one point the frames stopped coming, but the line kept right on moving. There was a gap of about 15 minutes during which workers were standing around with nothing to do while the line cranked on by.
Because the plant had a 100-unit per hour production rate, that 15-minute gap amounted to 25 trucks missing from the day’s production. Can Ford ever get them back? Craig would say absolutely not, at least not at the same margin.
That began a decades-long dive into the impact of the schedule on homebuilding. When you begin to view every jobsite where no work is being performed as a loss, it changes your entire outlook. If you learn how to calculate the true total cost impact of the lost time, it changes many of your homebuilding assumptions.
Another way to approach this idea is to look at the impact of the absorption of fixed costs. Variable costs, especially materials, run pretty much the same on a percentage basis, increasing or decreasing with volume at the same rate (leaving volume discounts out of the picture). But what if we can build just one more home with no increase in fixed costs? Generally speaking, the fixed costs of overhead — including salaries, benefits, equipment, support functions, rent, etc. — move very little, if at all. That one extra house is now more profitable.
Can you build 10 more homes without hiring anyone, buying more equipment or renting more space? I pose this question to builder management teams regularly and although the answers vary with their size, most will say they are all good for 10 more houses, sometimes 20, 30, or more. At some point, however, they’ll need to add some fixed cost to support the process. Even so, those extra homes will always generate a higher margin.
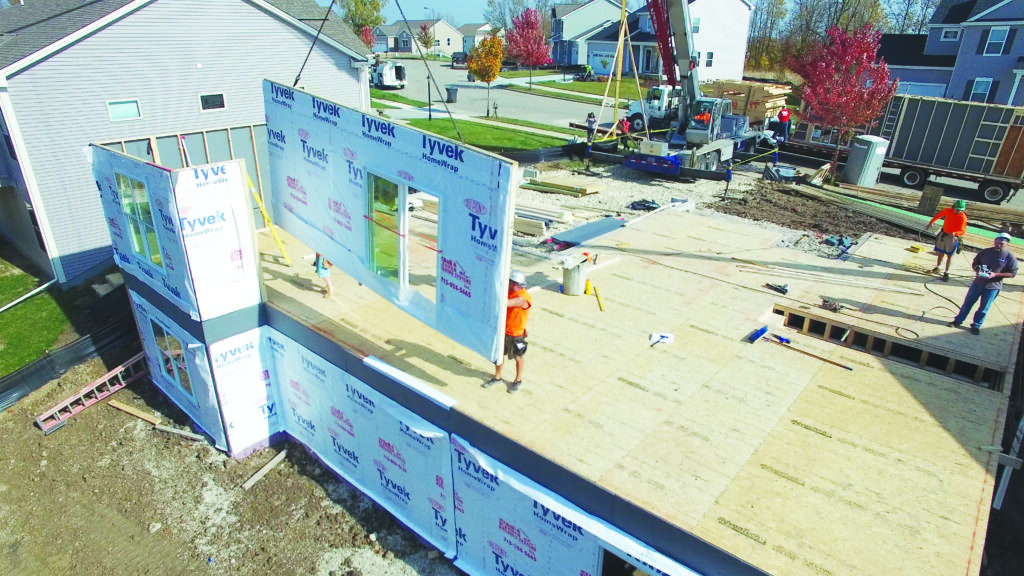
The Saved Day Calculator
As I saw this phenomenon in builders across the country, I became motivated to develop an Excel Template to calculate the true impact of a saved day in the build schedule. I came out with the first version of the TrueNorth Saved Day Calculator more than 15 years ago. It has improved and evolved since then, and has now been used by more than 200 builders in five countries.
Many builders have shared the data from their calculations with me, and that data has been quite revealing. Over the years, I have found builders typically estimate a per-unit cost of a lost schedule day at between $100 and $300. Let’s call that an average of $200/day.
Those estimates are actually quite low. This becomes clear when using the Saved Day Calculator, where, in addition to the costs of labor, material, interest, insurance, taxes and overhead, we also calculate the impact of the absorption of fixed costs. Measured in this more comprehensive, and thus more accurate, way, we typically see numbers between $500 and $900 for the true per-unit cost of a lost day, or two to five times what builders normally count.
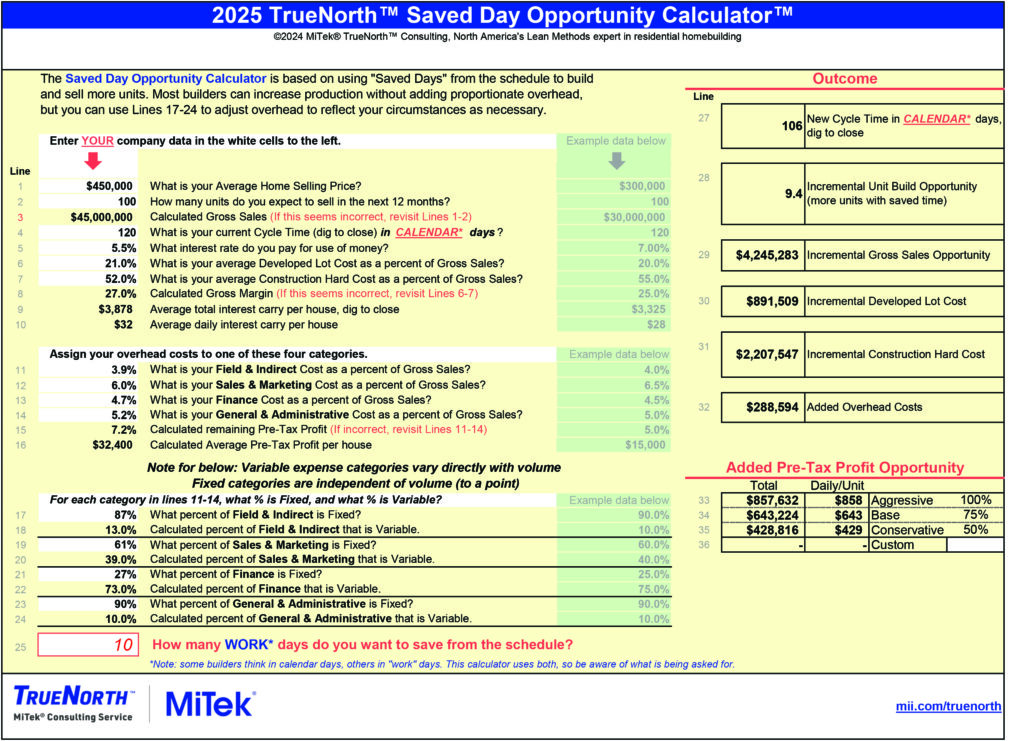
Here is a simple way to understand the phenomenon. Let’s say you’ve been building 100 homes in 100 days, and you estimate that you can shave a day from the framing schedule for all homes by switching to panels. That’s a critical path, which means the time savings will reduce the actual cycle time for the entire build.
Now we’re building 100 units in 99 days, freeing up 100 days total (one saved day per unit) from the original schedule. If we use those 100 days efficiently, we can build one more home for a new total of 101 units, with one day left over on the new schedule of 99 days. We still have our variable cost per unit, of course, but we did not hire anyone, we did not increase fixed costs. Now we are spreading the fixed cost across 101 units instead of 100, and margin increases. That’s called “absorption.”
What if we reduced our cycle time to 90 days? A 10-day reduction is a common goal builders set when coming out of our LeanBuilding Blitz events. That frees up 1000 days from the original schedule (10 days per home x 100 homes). At our new 90-day build schedule, we can build an extra 11 homes. If, and it is a substantial if, we can now build 111 homes in the same overall time frame as our original 100, the absorption of fixed cost goes up substantially and likewise, profit.
The impact has been a genuine eye-opener in our workshops. Most understand this concept intellectually, but when they work through the numbers using the Saved Day Calculator, they really feel it and become motivated to reduce cycle time. Ironically, and contrary to most beliefs, for a good builder, reduced cycle time produces higher, not lower, quality.
As with all good things, there are caveats though. What I described above happens in what the economists call a “perfectly elastic system.” In such a system, the inputs convert to outputs reliably, consistently and with no loss. In real life, this almost never happens, but what if we could get half of that time converted to production, or as some clients have reported, reap 75% or 80% of the opportunity to build additional units through reduced cycle time?
Another caveat is you must sell those extra homes of course, and support their processing through your system. Let’s say to do that sales insists they need more dollars for marketing and purchasing, already beyond their limit.
Both factors will increase costs, and you’ll see how the calculator allows for those and other factors to be manipulated as needed. It also enables you to pick your own conversion percentage, which you can adjust at any time as you gain confidence in your ability to utilize the saved days in your cycle time for additional production.
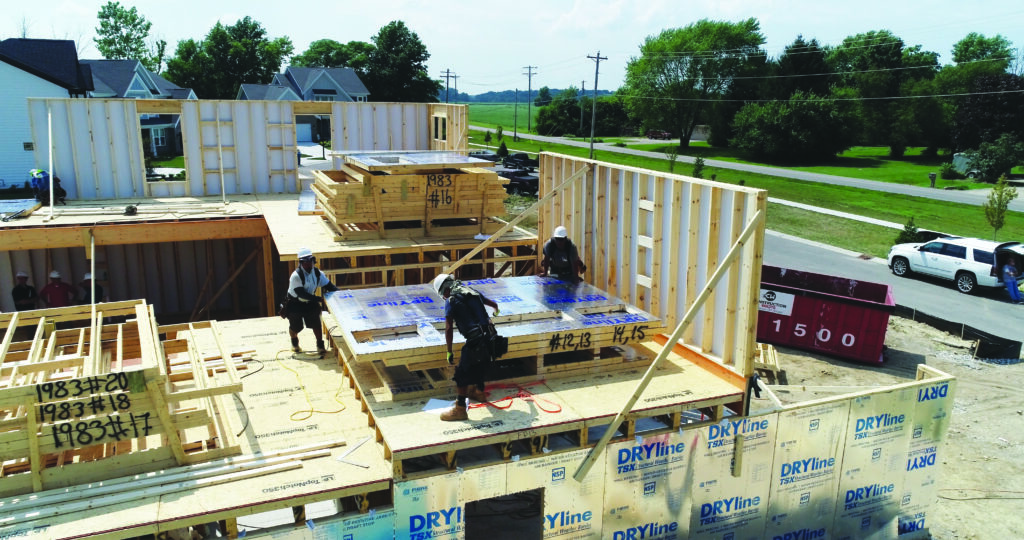
Study the graphic of the Saved Day Calculator for a minute. In the years spent perfecting this model, the biggest breakthrough came when we began to ask for the fixed versus variable percentages in each key cost category. This enabled the capture of the true impact of a lost day’s production on the sausage line. I believe you’ll find the example shown here quite inspiring. It demonstrates how any improvement in the critical path improves margins and, just as importantly, reduces the need and cost of capital, a huge factor in making offsite components more competitive.
In fact, as I said at the outset, measuring the true value of saved days can all by itself provide more than ample justification for converting from traditional stick-built homes to an extensive use of offsite components.
In our final Part 4 of this series, I will present one more practical tool —the TrueNorth Trip Cost Calculator. Every builder, supplier and trade knows that unnecessary trips to the building site are a killer for efficiency and profits. This tool reveals the true total cost of such trips and provides more than enough motivation to reduce and even eliminate them altogether. You will see quickly how offsite components can play a huge role in the elimination of such trips along with, of course, excess build days in your cycle time.
After Part 4 is published, we will offer you a package of these tools with instructions, thereby enabling you to apply them to your own operation.
Scott Sedam is Principal of TrueNorth Consulting, a MiTek Service. Scott founded TrueNorth 27 years ago following nine years as an executive with a top national builder. The TrueNorth team has worked with more than 300 builders in five countries, and Scott is a well-known writer and speaker at conferences and company events. Please join Scott’s “LeanBuilding Group” on LinkedIn and learn more about TrueNorth services at www.mii.truen.com.
Images courtesy of MiTek. Saved Day Calculator and Trip Cost Calculator are Mitek trademarks.