Why is it taking the industry so long to adopt offsite components at scale? Because builders don’t understand their true costs.
- Builders cite a variety of reasons why components haven’t taken more market share. According to the author, they miss the big picture.
- This article describes how builders take too narrow a view by overlooking costs that can add up to big money over the course of many projects.
- Future articles will provide detail on a suite of calculators developed to help builders better understand the true cost savings offered by components.
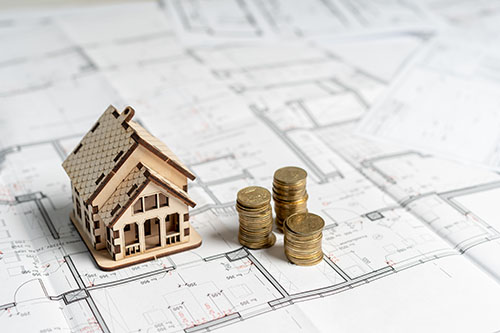
Thirty-five years ago, I sat transfixed in a three-day workshop held by Bill Pulte, Founder and President of Pulte Homes. Among the many memorable moments, one in particular has reached a remarkable level of irony.
Bill was always forward-looking, seeking any edge to improve efficiency. He described how new manufacturing processes and technology had dramatically changed automobiles, electronics and manufacturing of all types, and now it was homebuilding’s turn. Detroit, Michigan-based, Bill was close to many key automotive engineers and executives. He raised his hand up in front of the class with his thumb and forefinger held about one inch apart and proclaimed, “We are about this far from adopting advanced manufacturing methods that will completely revolutionize homebuilding!”
Bill then described how the use of trusses to replace stick-framed roofs was only a beginning, and soon we would see a strong movement toward panelization, the simple “open” type, just 2x4s and some larger sizes for headers. Although no one used the term back then, Bill went on to outline how we would next see closed panels with windows, doors, sheathing and even drywall and siding.
Fast forward nearly three decades to 2018 when I visited Bill a few months prior to his passing. We covered a lot of ground, including Pulte’s many efforts to introduce more manufactured components into their product — all the usual suspects and even panelized foundations. I reminded him of his statement from so many years before and held up my thumb and forefinger an inch apart as he had done and asked him how far we are today from that revolution he predicted.
Bill was quiet for a moment, then raised up his hand with his thumb and forefinger this time less than a ½-inch apart, and with his unmistakable laugh said, “About THIS much!”
As I write this in early 2025, I wonder how Bill would describe how close we are today. A little more progress, I think, but still there would be a gap between his thumb and forefinger, perhaps a ¼-inch. This begs the question, why has it taken so long to adopt offsite components on a large scale?
At least once a month I come across an article or blog post listing the obstacles. I occasionally read advice on how to solve at least some of them.
The opinions I’ve read highlight a variety of issues: inspection authorities, shipping and logistics, trades’ willingness (or not) to adapt, engagement by architects and engineers, customer acceptance, community acceptance (zoning), and builder willingness to embrace change and commit to a learning curve that most believe will hurt profit, at least in the short run. Then there are the supply side issues and the capital needed to invest in plants for a cyclical industry, which has killed innumerable efforts in the past.
The Biggest Hurdle?
No doubt you have read about or experienced other hurdles. But after studying this issue for a couple of decades, I conclude the biggest obstacle of all is one that is never mentioned. It is also the one that, if solved, will overcome many of the other barriers blocking the path to the broad-based adoption of offsite components in production homebuilding. The problem, put simply, is that we don’t know how to measure the true total costs and benefits of on-site versus offsite production.
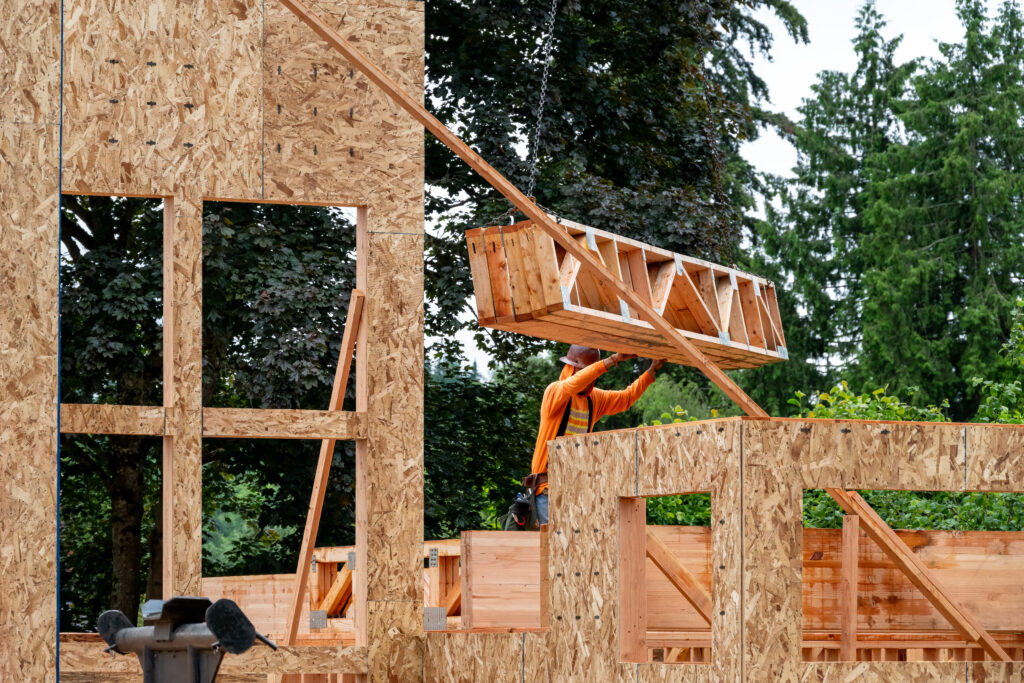
When comparing panels to site framing, for example, the great majority of builders don’t look much beyond material plus labor for both methods. You might also see an addition for crane rental on the panel side, if needed. At that level of analysis, panels lose more often than not.
Yet there are so many other factors to consider. For example, no matter what method of waste removal you employ, the typical home generates three to four high-side dumpsters of trash, costing $400 to $800 each, depending on the market. Let’s call it $600, and assume that using panels will reduce waste by better than half a dumpster on average, saving between $300 and $400 per unit. You’ll save even more if your panels include sheathing and you go past mere trusses to “roof cassettes.” Typically, that’s as far as the analysis goes.
I take a broader view. I have identified more than 20 essential factors required to accurately compare the total costs and total benefits of on-site versus offsite construction methods. In future articles, I will dig into these and present a model for a comprehensive total cost and total benefit comparison. Meanwhile, let’s look at two critical comparison factors.
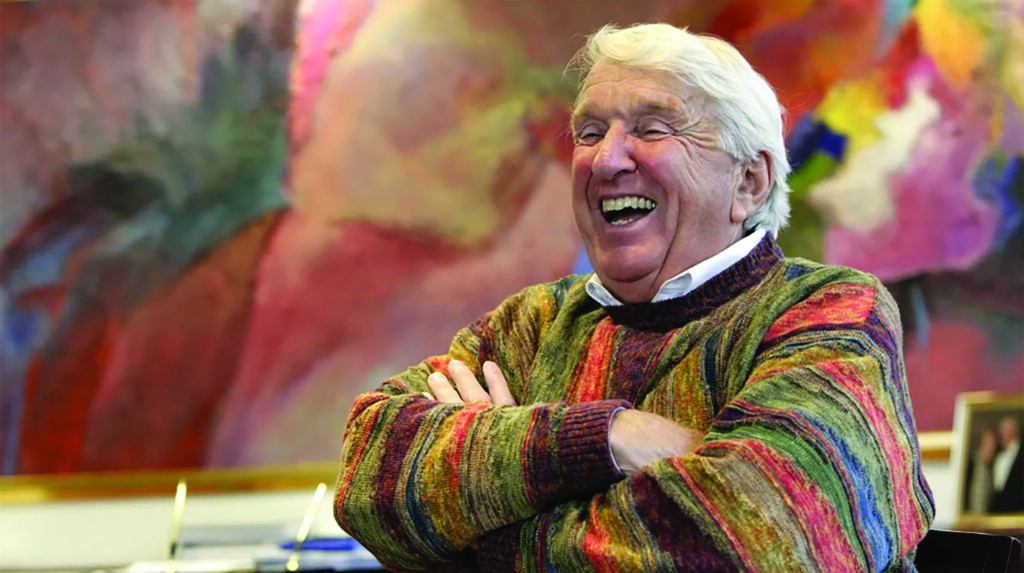
Photo courtesy of Detroit Free Press
The first factor is the cost of wasted or excess trips to the building sites. It’s virtually never measured. The second factor is the value of a saved schedule day, which is sometimes measured, but never accurately.
I developed tools using Excel templates for both factors more than 15 years ago and have captured data from nearly 200 homebuilders and more than 5000 suppliers and trades. The findings from the data are mind-boggling and go a long way to cost-justify the move to the broad application of offsite components over stick-framing.
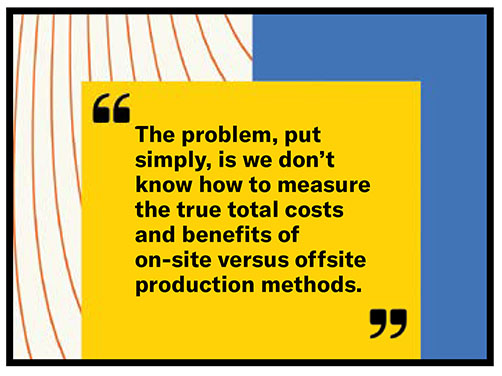
Do the Math
Let’s consider just one example. Recently, a Southeast division of a national builder conducted a trial, building a 2300 sq. ft. two-story home with the extensive application of components. Involved in the project (besides the builder team) was a highly collaborative group including a prominent lumber and truss dealer, framer, HVAC, plumbing, electrical and product design experts from my firm, MiTek.
Planning for the build spread across several months and required adjustments in plan layout for all suppliers and trades involved. The walls and roof sections arrived at the site with exterior sheathing that requiring no house wrap, and with windows and doors pre-installed. The process to dry-in before mechanicals was traditionally planned for 10 schedule days. On the day of install, in a steady drizzle with a crew who had never before erected a house like this, the job was completed in just under eight hours. That’s nine saved days.
Now estimate how many trips to the jobsite were saved by both the framing crew and the lumber dealer, then assign a cost for both. Next consider how just these obvious trip reductions impact the evaluation equation for on-site versus offsite methods. Now run the same exercise for the nine saved schedule days. What are the all-in cost savings?
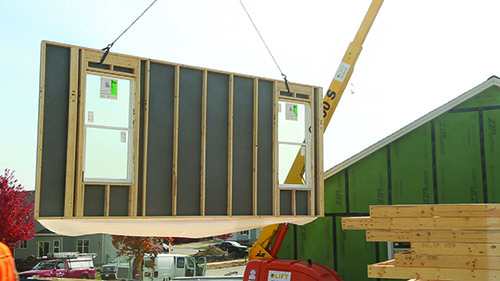
In future articles I will introduce the TrueNorth Trip Cost Calculator to show the true, total costs associated with site trips for each approach. I will also introduce a second tool, the TrueNorth Saved Day Calculator to document the impact of schedule improvement. You’ll be shocked at the numbers and find that the move toward adoption of offsite components becomes more compelling than ever before. Finally, I will pull it all together with our new, On-site vs. Offsite Evaluation Tool, literally six years in the making. This magazine offered a 30,000-foot overview of these calculators in the May 2024 issue (see “Show Me The Money” on OffsiteBuilder.com), but I intend to go into them in more detail.
I am convinced that when you learn to truly understand the true total costs and benefits of the adoption of offsite components, the decision will become quite easy.
Scott Sedam is Principal of True- North Consulting, MiTek Service. Scott founded TrueNorth 26 years ago following nine years as an executive with a top national builder. The TrueNorth team has worked with more than 300 builders in five countries, and Scott is a well-known writer and speaker at conferences and company events.
Interested in learning more? Scott’s 2025 IBS presentation, “Design Lean to Build Lean” is at 8:30 AM at the LVCC – West 230. You can reach him at [email protected]