This builder is exploiting the full potential of SIPs construction
- This St. Louis, Mo. builder is proving that Structural Insulated Panels (SIPs) earn their keep not only for new construction and additions but also for remodeling, where they can enhance performance while maintaining the home’s architecture.
- In a deep energy retrofit, steel-framed panels are added to the inner face of existing walls, but the contractor has to pay close attention to air sealing and moisture management.
- The company carefully pre-plans its work, using input from all trade contractors. This saves time and money by making for a more efficient job site.
- Most contractors sell deep energy retrofits based on the monthly reduction in utility costs. This is important, but more consumers will be interested if the work also raises the home’s appraised value. Fortunately, appraisers are getting on board.
Enhanced Building Systems in St. Louis, Missouri uses high-performance panels for both new construction and retrofits. Here, we share some of the details of how they do that. We’ll also dig into how to sell ‘green’ while at the same time running a profitable business.
Company founder and Chief Operating Officer Matt Belcher says that the company builds new custom homes and does major home retrofits – all high-performance and panelized. They also work on light commercial and agricultural buildings.
They use various kinds of panels—wood-framed, steel-framed, and SIPs— with a variety of R-values. The panel chosen for a specific project (new build or retrofit) depends on the scope and the installed cost.
The company has plans to start manufacturing its own panels, which will consist of galvanized steel studs, carbon fiberglass sheathing, and expanded polystyrene (EPS) foam insulation treated with a borate solution to inhibit mold and resist fire, insects and rodents.
The panels will have an R-value of between 22 and 60, depending on the foam density and the wall thickness. “Except for door and window openings, these panels provide nearly continuous insulation. They provide a far more effective thermal envelope than traditional construction methods,” Belcher says.
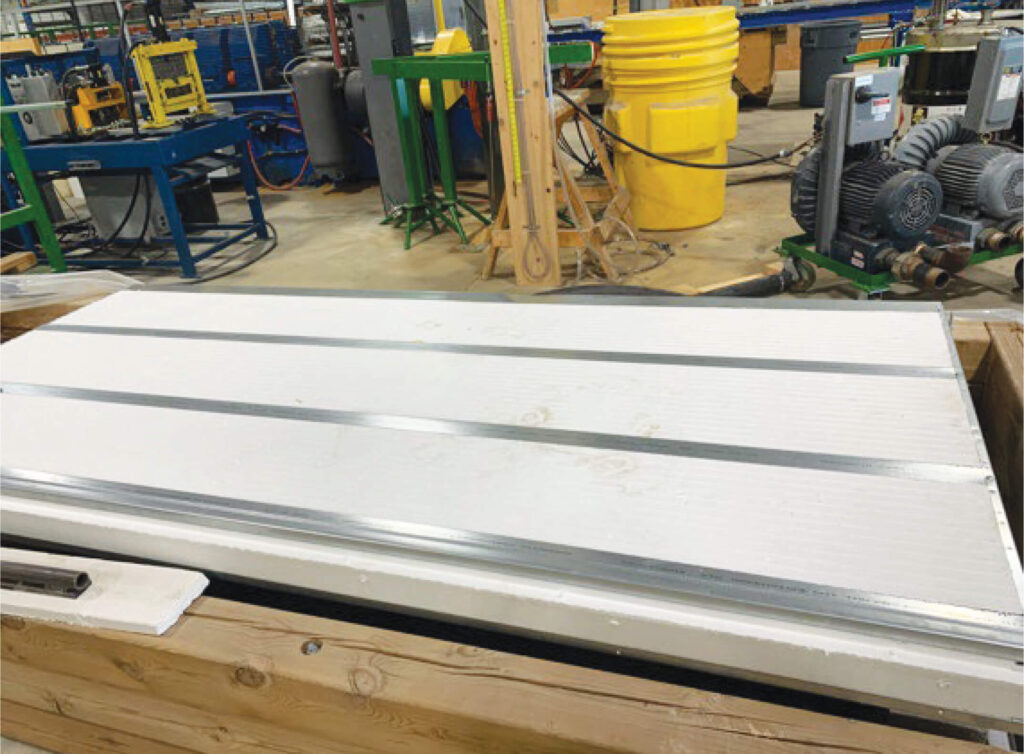
New Construction
It’s easy for engineers to convert plans for a stick-built structure into plans for panelized construction. After the first draft of the design is done, the construction team sits around the table, “usually at the architect’s office because they have the nicest conference rooms,” Belcher jokes. The design is finalized based on input from the tradespeople who’ll be working on the project — carpenters, plumbers, electricians and HVAC installers.
Plumbing is minimized or eliminated in exterior walls. Major electrical home runs are located in interior walls. Input from the trades ensures that plumbing chases and electrical raceways are placed in panels where needed.
This pre-planning makes for a more efficient jobsite. “Trades don’t have to figure out how to keep out of each other’s way and how to avoid conflicts between the ductwork and the plumbing because that’s already been figured out,” Belcher says.
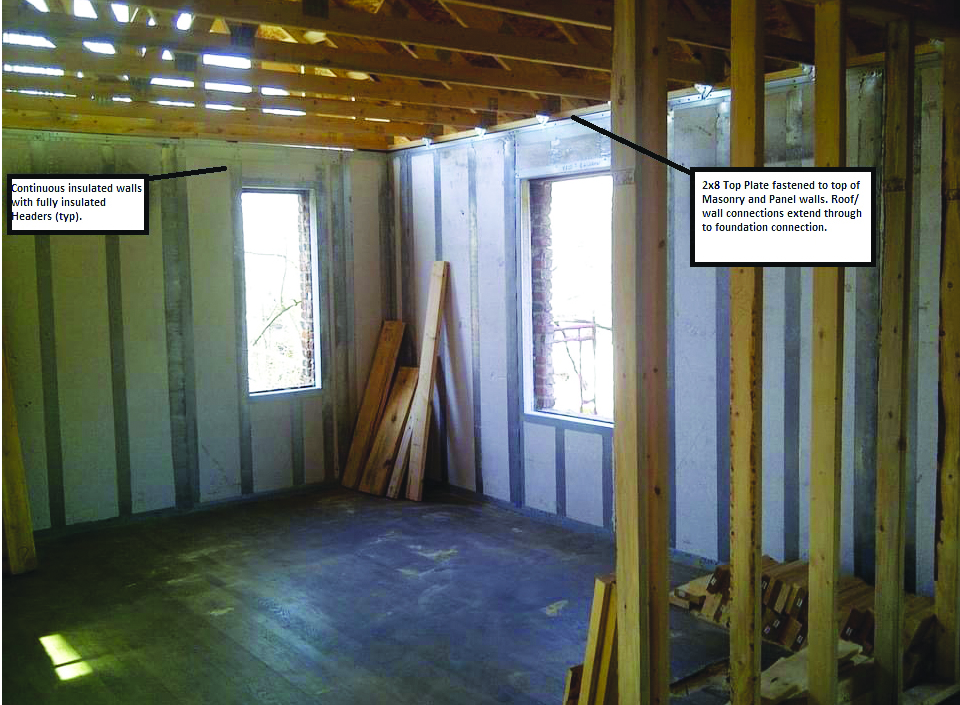
Retrofit Work
Panels can also be used to improve the energy performance of an existing building, usually by installing them on the inside of the existing walls.
The first task in a retrofit is to collect data to figure out if it makes financial sense to improve thermal performance. For this purpose, the company does a blower door test to measure air leakage. If the amount of leakage justifies the cost of the improvements, the company can perform what Belcher calls a “deep energy retrofit.”
Panels for retrofits can maintain the home’s look while improving performance. For example one of Enhanced Building Systems’ projects was an abandoned structural masonry home built in 1930, which hadn’t been maintained. His clients “bought it for a song” and wanted to make it livable, while keeping its classic architecture.
Much of the rear upper level of the home was originally wood framed and had been heavily damaged by moisture and squirrels. Belcher’s team removed that and rebuilt it with panels.
They removed the remaining lath and plaster on the inside of the walls, too. On the outside, they removed ivy and did a lot of tuckpointing to replace old, deteriorated mortar with new mortar.
The steel frame wall panels the company used were light enough to be carried by hand. They were shiplap-joined at the vertical seams, then “attached to the existing masonry with screws and anchored to a 2 ft. x 8 ft. plate at the top,” Belcher explains.
Sealant was applied to the joints with a caulking gun. More clips and straps were used to secure the panels to each other for additional resilience to wind and seismic activity, a practice Belcher notes is recommended by FEMA. “The insulation is continuous and the tight face of the panel is the moisture/vapor barrier,” Belcher says. Where additional structural support was needed in specific locations, the gauge of the steel studs inside the panels was increased accordingly. (Most panels had 24-gauge steel studs, but in the rear of the home, where the panels support the second floor, the gauge was increased to 18.)
To help manage moisture, a one-inch airspace was left between the brick and the new panels. “Older masonry can be very porous,” explains Belcher, “so we made sure the airspace could dry out by adding weeps at the bottom of the wall and protecting the extended window and door jambs as they penetrated that plane.”
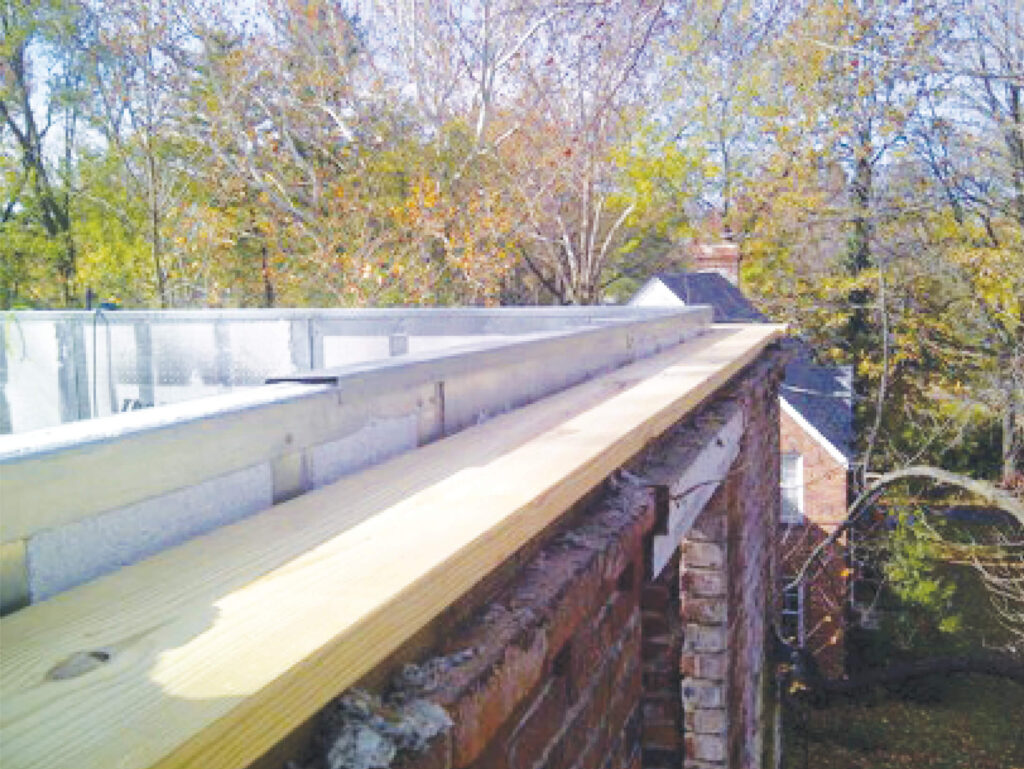
Belcher says that the performance of a retrofitted wall and a new panel wall is very similar. The biggest difference is that retrofits mean “dealing with very fixed existing dimensions: wall length and height, window and door openings.”
Another example retrofit project was a 40+-year-old home in St. Louis, Mo. that Belcher’s client had inherited from his grandparents. It was a 2400 sq. ft. rancher with concrete block walls, brick cladding and a lath and plaster interior.
The owner wanted to maintain the architecture, but increase the size and improve the performance of the home. So Belcher’s team lined the existing first-floor masonry walls with panels, removed the roof, and added prefabricated trusses and panels to create a new second floor with three bedrooms and two baths.
The financial benefits of the retrofit were very quickly apparent to the owners. “The square footage of the home was doubled. But the utility bills were less than half of what the old house was,” Belcher says.
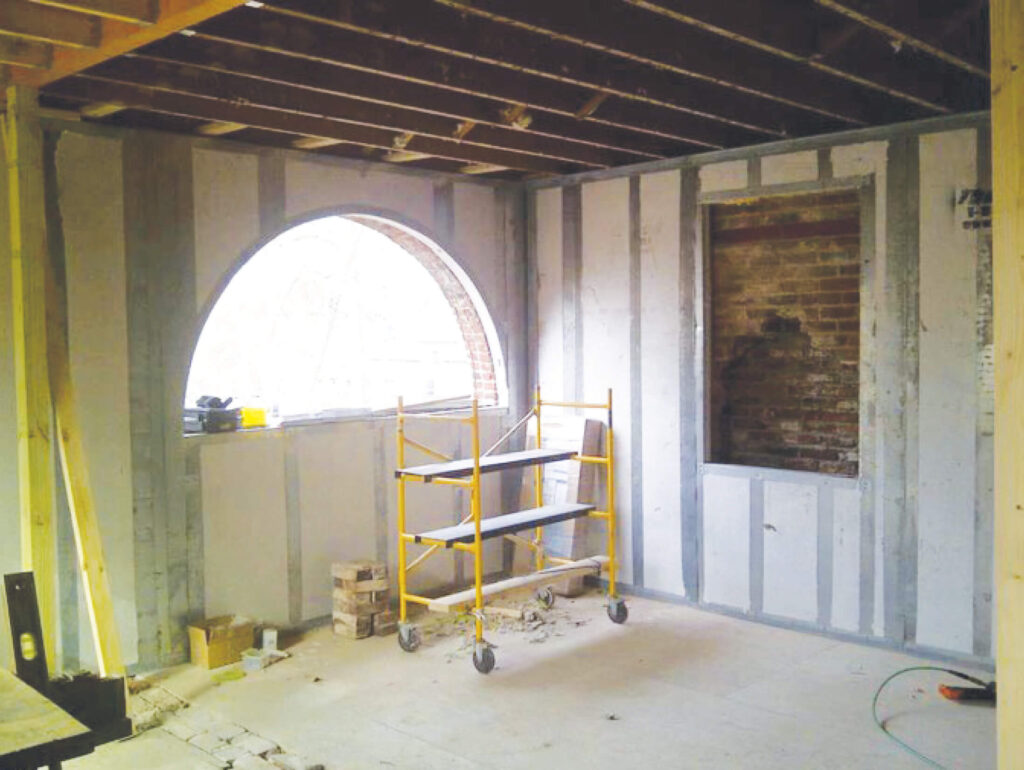
The Key to Selling Green
Belcher has learned that, to make sales, environmentally beneficial products must be financially beneficial, too — for the business and its customers. “It’s not just about making the building efficient; it’s about making the construction process and the business more efficient too.”
The company markets the performance of its above-code homes in financial terms. “The comfort level, the air quality and the durability are all higher. They have lower maintenance costs and use less energy,” Belcher says.
These homes cost more to build than a code-minimum house, but all-in costs can be lower. “Our costs for utilities, maintenance and so on are usually half that of traditional construction. We can also whittle it away further with things like solar panels,” Belcher says. “The lenders we work with include the amount saved on operational costs as part of the clients’ debt-to-income and expense ratio. This strengthens their borrowing power,” Belcher explains.
Whether the lower costs will completely offset the higher mortgage payment depends on many factors— the size and scope of the project, the local housing market, interest rates, and the fluctuating costs of materials, energy and labor. All these factors are considered when helping a client choose the materials and details that will be used.
It’s also crucial that the homeowner’s increased investment be reflected in the dollar value of the building. “We used to have issues with appraisers who didn’t recognize the value of what we were building.” However, ever since the Appraisal Institute launched its green appraisers’ training, this has been less of a problem and homeowners’ investments are being reflected in their valuations.
Belcher says that Fannie Mae and Freddie Mac now require that the energy-efficient features in the home be identified and valued.
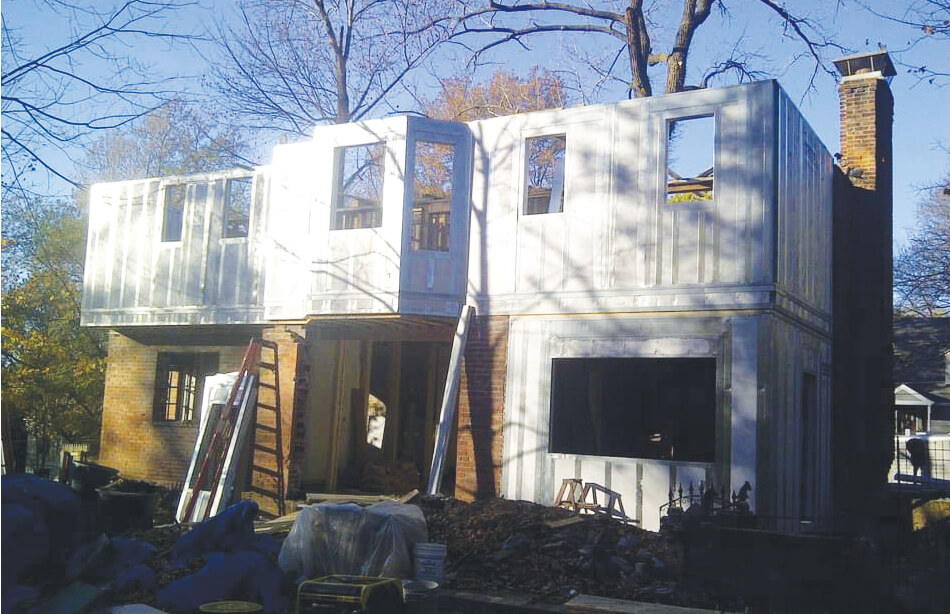
“Appraisers need to be familiar with whatever they’re appraising. For instance, an agricultural appraiser has to understand the value of agricultural buildings, land and crops,” Belcher explains. “Similarly, when we build a LEED Platinum home, we need an appraiser who understands the value of that certification.”
To ensure accurate appraisals, Belcher provides lenders with a specification that lays out the requirements for appraisers. The specification notes that the building has been constructed or renovated to standards higher than the local prevailing code and that the lender shall choose an appraiser who is educated in valuing the specialized buildings — preferably one who holds a professional appraisal designation certifying that they’ve had the relevant education.
“It’s still a little unusual for appraisers to have this training and for lenders to be aware of it. But it’s growing rapidly. People who are building and selling high-performance homes need to recommend appraisers who have had the proper training.”
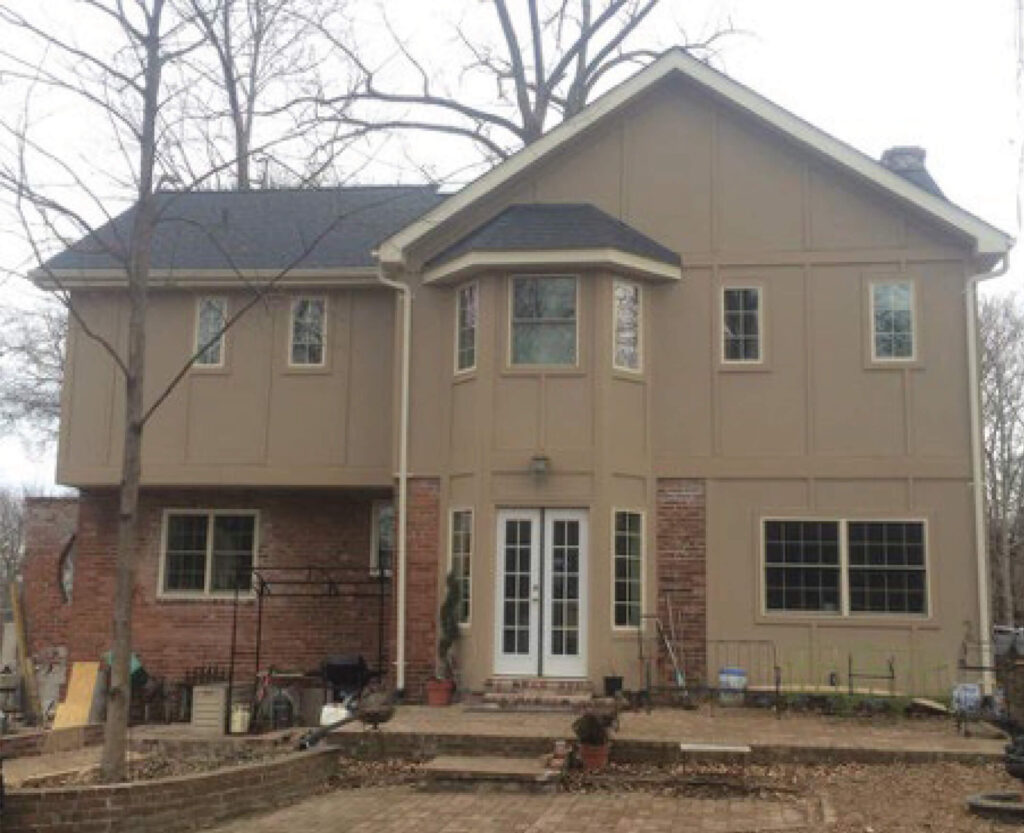
From Builder to Manufacturer
Thanks to recent supply chain issues, the company has decided to begin manufacturing its own panels. “We’ve completed the factory plans, the financials are done, the operating agreements are finalized, the corporations are set up, and we have a great team of experienced pros for both panel fabrication and modular and pod assembly,” Belcher says.
The 100,000 sq. ft. factory they purchased in New Madrid, Missouri, came with gantry cranes already installed, and soon the team will be ordering more equipment, such as steel roll forming machines. In the meantime, they’ve acquired a manufacturing plant in Canada (Belcher isn’t yet able to disclose the location), which will make panels and ship them to New Madrid. The panels will be used to make kits for prefabricated buildings. They already committed 200 new houses.
Eventually, they plan to sell panels to other builders and to manufacture pods and complete modules. They’re also looking at producing mass timber components.
One major advantage of the new facility is its location in the center of the country. “Our distribution area is from the Rockies to the Smoky Mountains. There’s also a barge port on the Mississippi right in New Madrid,” Belcher says.
The basic design of the panels they’ll be manufacturing has been used for about 40 years, with tweaked improvements, Belcher says. A 4 ft. x 12 ft. panel, with typical 24-gauge steel studs weighs about 75 pounds. They don’t need special equipment to install and each one can be lifted and set in place by one person.
“If the same size panel was made in wood, it would probably weigh a couple of hundred pounds,” Belcher says.
Despite the lightweight, these panels are very strong. They’re frequently used for their thermal properties in cold regions like Alaska and Russia, and for their resiliency in the hurricane-prone areas of the southern United States. The New Madrid factory is in Tornado Alley and in the New Madrid Seismic Zone.
Says Belcher, “if there was a fourth little pig, he would have built his home out of these panels.”
Photos courtesy of Enhanced Building Systems.