It won’t be the best choice for all jobs, but where it is, it’s a real problem-solver.
The current state of modular construction is confusing. Advocates praise it as the future of construction, but there are also signs that show otherwise. I see an ever-expanding list of modular factory closings, while at the same time I see modular factories operating into their fifth decade with the third generation of family ownership. What is going on?
Modular has been and continues to be touted as a big part of the solution to a long list of construction and housing problems. One does not have to search very hard on social media platforms to find it hailed as the answer to the housing shortage, to construction inefficiencies and even to homelessness.
Although advocates position modular as a broad-based solution to an inefficient industry, it has seen only limited gains as a percentage of projects built. Why is this?
To address the question of limited gains, it is helpful to first define what we mean by modular construction. As someone who builds modular homes, I view it as a construction methodology. In other words, it is simply a set of tasks that lead to the completion of a structure. Traditional on-site stick building is also a construction methodology, but with a different set of tasks. Both can get you to the same result and, depending on what is being built, modular may or may not be the best one to use.
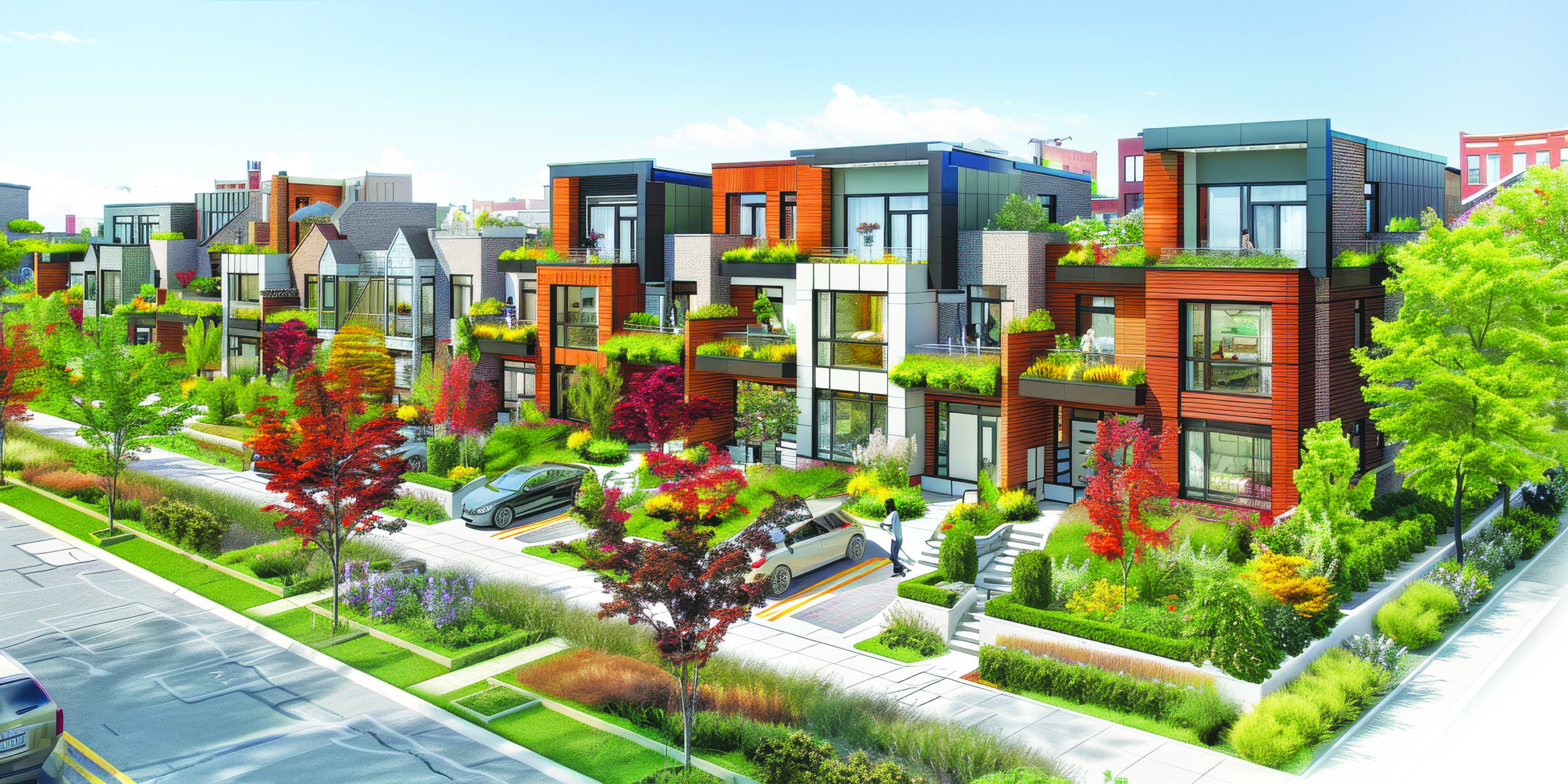
As a homebuilder, I have a variety of construction methodologies to choose from, and I have to pick the right method for each job. Just as trying to use a screwdriver to hammer in a nail isn’t very smart, using the wrong construction method on a project can make the process less efficient, while adding unnecessary time and money.
This gets us to the big question: When is it best to use modular? When, as a builder, do I reach into my metaphorical tool bag and decide modular is the best practice? I submit that, frequently, the deciding factor is labor availability. Is my project located in a geographic area that has access to qualified labor at an affordable price?
If a builder does not have access to qualified, affordable workers, the job will be best suited to modular methods that centralize labor in a factory. The fruits of that labor can then be transported to the building site. I call this labor arbitrage.
Here are three areas where modular construction methods are most prevalent and offer the highest value.
1. Scattered site single-family homes. This is especially true in rural areas, where qualified, affordable labor is not available due to the random locations of jobsites.
New construction trades in these areas tend to congregate in and around new housing developments. They can price their labor/services at more affordable prices because they get high-volume work from the developer. They can move from lot to lot, doing fairly repetitive work in what’s essentially an outdoor factory line. Scattered site builders don’t have access to this ecosystem, so it makes sense for them to turn to a modular factory that pools the labor and transports mostly finished units to the jobsite.
2. Urban infill homes. Builders of these homes have the same problem of pooled access to qualified, affordable labor at their jobsites. The demand for housing is there, but the labor is not. Modular factories offer a good solution.
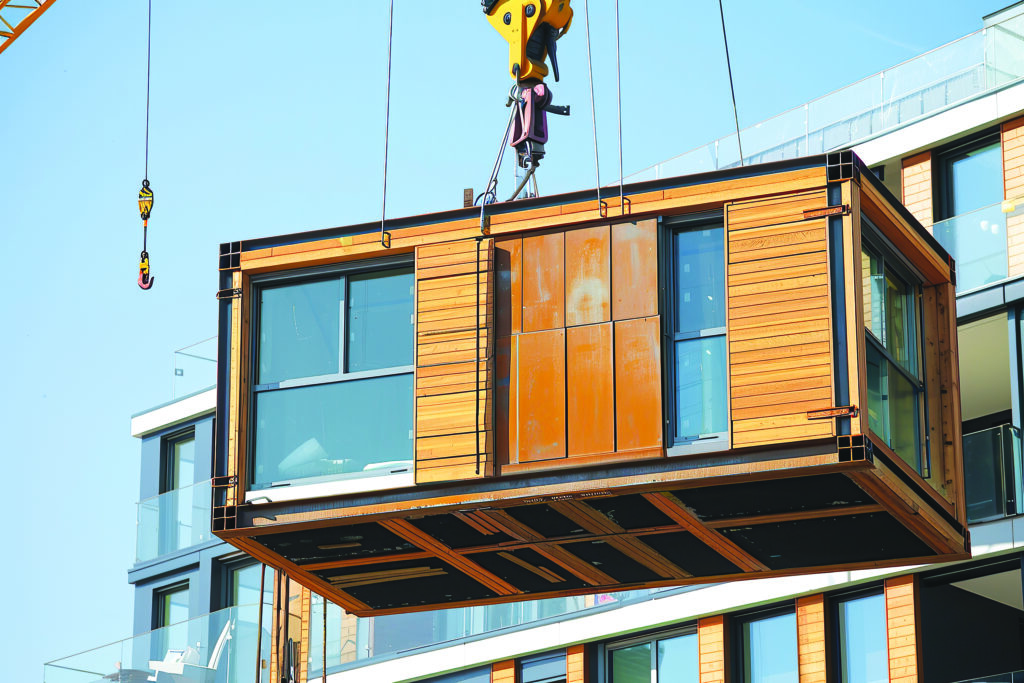
3. Multifamily/Hotel Construction. These are typically 3+ story hotels and apartment buildings. When they are built, there is often a requirement for unionized labor that comes at relatively high cost. This leads developers to turn to modular manufacturers, which employ lower-priced factory workers. The time value of money also plays a role here: in cases where the builder only pays for the modular units when they are ready for delivery to the site, that lessens the time working capital needs to be deployed. The project becomes less expensive to build.
The answer to why modular hasn’t seen significant gains is because the areas where modular flourishes make up only a small part of the overall new construction market. This is not a criticism of modular construction. It is simply a realistic assessment of which market conditions modular is best suited for.
Shawn Corkrean is the owner of Griffith Homebuilders. They sell and build modular homes in Iowa and Nebraska. www.GriffithHomeBuilders.com Shawn has experience as a real estate agent, land developer, factory sales manager, and 20 years as a home builder (stick and modular). He can be reached at [email protected]