These companies make a compelling case for standardization as a means of enhancing budget management.
- Challenges such as the labor shortage and high material prices demand a disciplined approach to budget management.
- Modular/prefab housing has been found to be more cost effective, with time savings that make a convincing argument for offsite building.
- The more vertically integrated the company, the more control it has over costs.
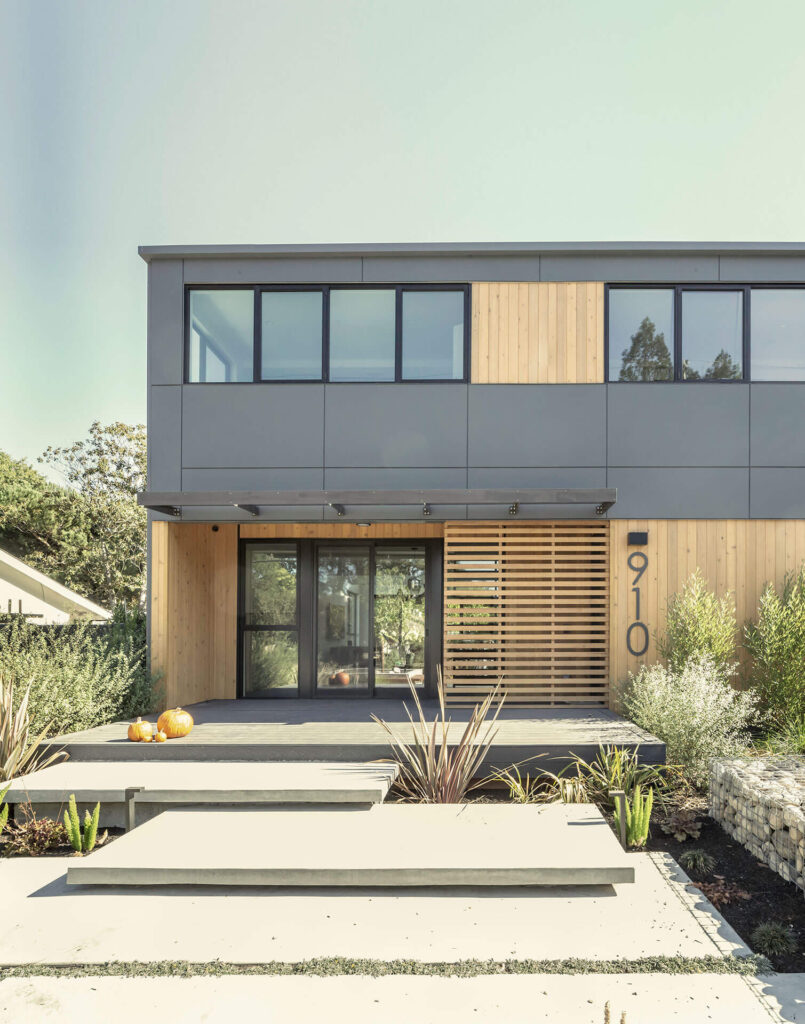
Credit: Connect Homes
Architect Toby Long, AIA, has been utilizing a combination of modular and prefabricated technologies for 24 years. Prior to that, Long worked on diverse construction projects both on-site and offsite. Regardless of the project or the scale, he says, cost control is always an issue.
“Whether it’s a [tiny] house in a backyard or a new suspension bridge across a river, [cost control] issues are always part of building projects,” says Long, whose company, CleverHomes, is based in Oakland, California.
Managing a construction project budget requires discipline, he says. Modular homes are “rigorously detailed and very complete in their nature; [therefore,] you really need to understand every part of them from the beginning,” Long comments. This discipline spreads across every budget category, from the building itself to the site work and infrastructure.
Steve Sudeth, Executive Vice President of Sales and Marketing for modular company Connect Homes in Mesa, Ariz., has heard industry wide that site construction is taking longer and is less predictable because the available labor force is tighter. “You get a lot of hurry up and wait and again, time is money,” he says. “So, if you’re relying on skilled tradespeople to complete your projects, you might have a lot of gaps in productivity on-site.”
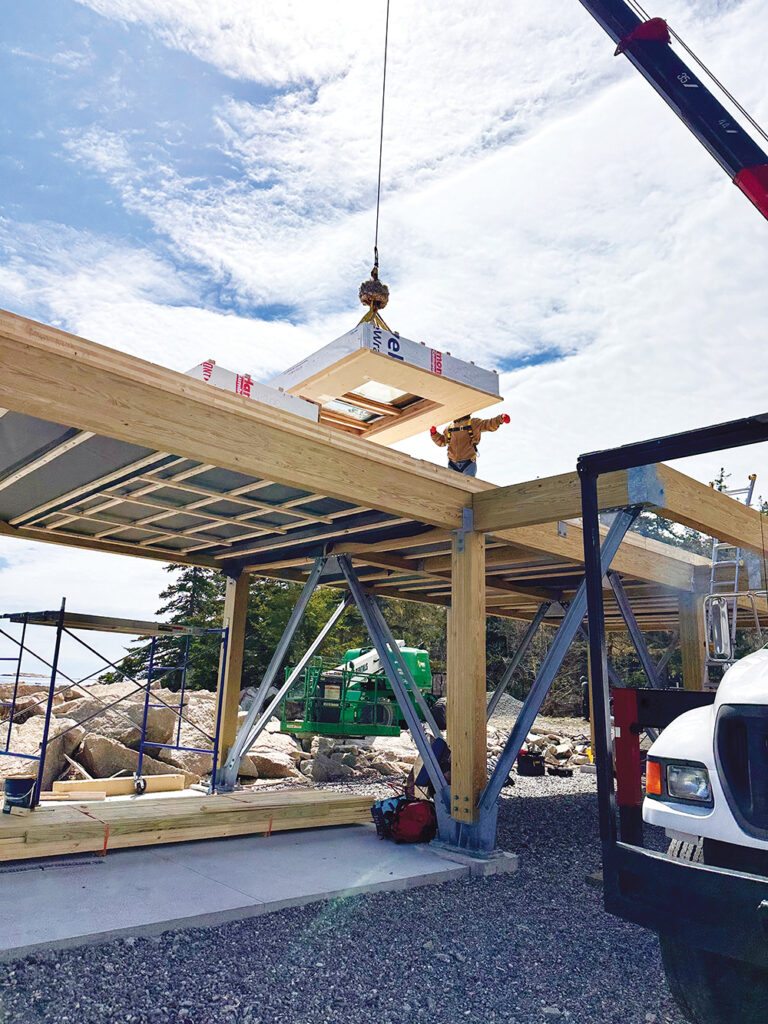
Credit: OPAL Shelter
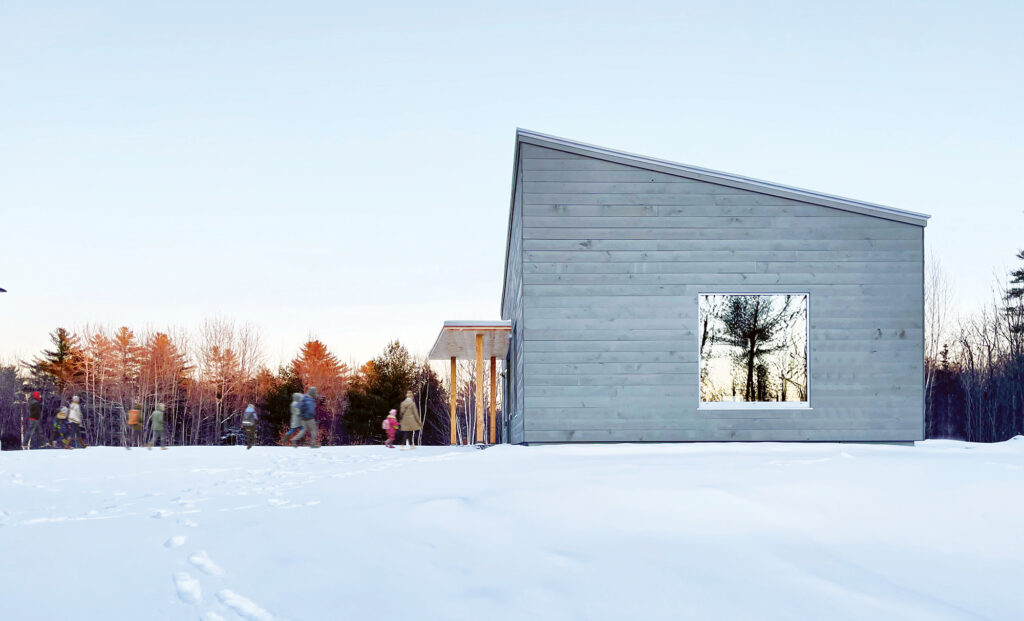
Credit: OPAL Shelter
Pricing Predictability
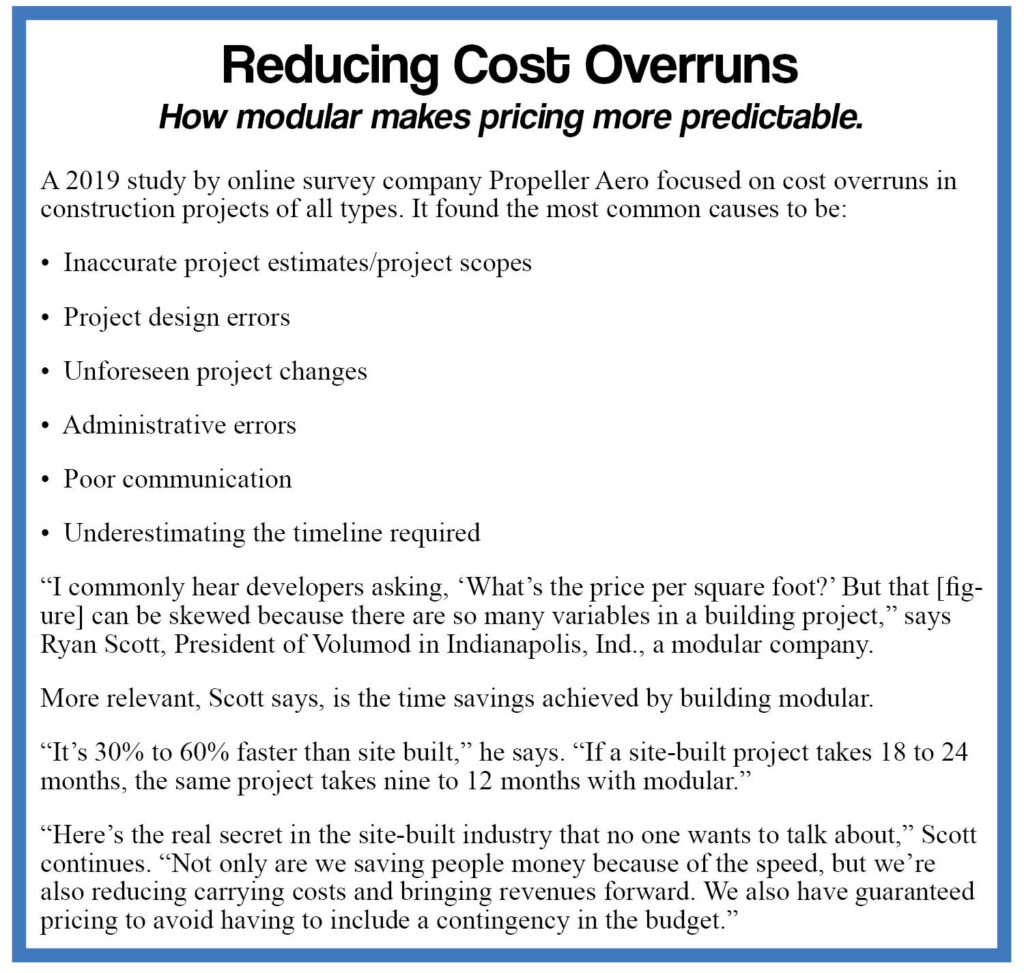
Modular construction, on the other hand, provides a toolkit for alleviating budget unknowns, says Long.
“With modular, there’s a lot of predictability,” he says. “A single line item called ‘Modular house’ includes the rough-in, the finish work, and all the parts and pieces that go into the house.”
OPAL Shelter (OPAL) in Belfast, Maine, utilizes a hybrid system of panelized and modular components to build modern, energy-efficient homes made with cross laminated timber (CLT) and wood fiber insulation.
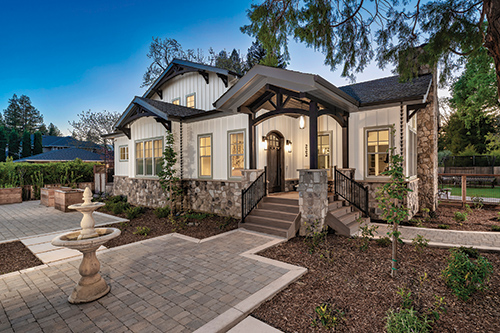
Credit: CleverHomes by Toby Long Design
“The scope of work that we build offsite includes the CLT panels; the windows; the wood fiber insulation; the modular kitchens and bathrooms; and the mechanical, electrical, and plumbing (MEP) pods,” says Matthew O’Malia, Executive Partner of OPAL. “That represents, typically, 60% of the project value, so we’ve been feeling a higher level of confidence about predictability on the cost side. The majority is CLT, which can be pretty price stable, and we have several vendors for windows, which allows us to be competitive.”
Modular methodologies can also be used to help instill a discipline, Long says.
“When you get organized right away and manage an ongoing process that distills the house down to one metric, it captures a lot of the project,” he says. “Builders don’t have to project themselves onto the discretionary elements; they can speak to and support the things that might be more in their comfort zone. One can harness or leverage information into an early and ongoing analysis of costs or do a budget.”
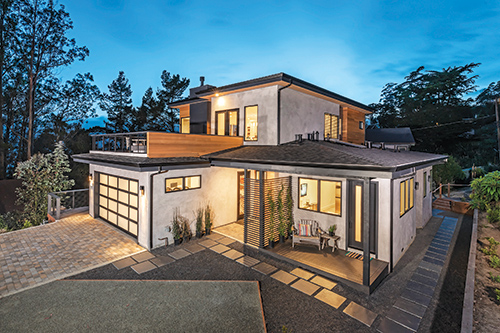
Credit: CleverHomes by Toby Long Design
CleverHomes’ process of budget review and cost planning emerges from collaboration among all team members. “It’s not just the contractor and the local subs; it’s the factory and their team, the local contractor and their team, the design team and the engineers, and everybody needs to come together around the work to be performed,” says Long.
Sorting out scopes of work builds a discipline for budgeting among building teams, and allows the process to track through design, development and so on until project completion.
“If the cost of concrete is going up, we should be able to monitor the increase in the cost of the foundation,” he says. “We’re not going to wait until we’re ready to build only to discover that the cost is twice what we thought it was going to be.”
OPAL chose a hybrid panelized/modular system due to the cost of shipping higher-value elements such as kitchens and baths. “Kitchen and bath modules and MEP pods travel well because they fit the standard shipping dimensions of a tractor trailer, just like the CLT panels do,” O’Malia says. “The mix of panels and [modules] gives us a lot more predictability when we have a long lead time to order materials in the factory. Then we use our own internally sourced labor to install them.”
This gives OPAL more control not only over the products, but also over the supply chain and how and when the products are installed, allowing a small buffer if there is a supply issue.
O’Malia says the company is focused on replicability. “CLT has some specific design criteria which, if you work within it, can be very cost competitive,” he says. “But we have to be very clear with customers when CLT might not be the best choice for their particular design.”
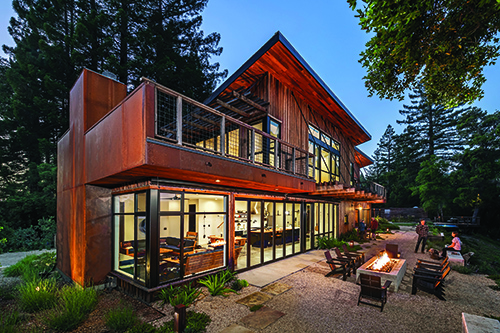
Credit: CleverHomes by Toby Long Design
Time Is Money
Connect Homes builds a volumetric modular product. “We’ve learned that with a lot of the high-touch areas like bathrooms and kitchens, you get the most efficiency by completing them in the plant,” says Sudeth. “All of our homes and townhomes are designed specifically for our manufacturing process so we can complete up to 90% of them in the factory. When it gets to the site, there are only connections to do across modules, drywall patching and flooring.”
Customers can personalize the homes, but not customize them. “We’re flexible on finishes,” says Sudeth. “We don’t want to move anything structural or with mechanical, electrical, plumbing or HVAC.”
Design, materials and labor, he says, “are the three main drivers to everything. You want to limit the number of questions from design to manufacturing to delivery and installation. Every time you pause to ask a question, [remember that] time is money. The integration of design and manufacturing is critical for cost predictability, because you don’t spend as much time stopping and asking questions.”
Sudeth says Building Information Modeling (BIM) software has helped cut down on time-consuming queries by providing a complete digital model of every component: “You don’t have to worry about the interpretation of drawings as much. The information is much more accurate with BIM.”
For cost control in modular construction, a company’s vertical integration is key. “When you have your own in-house design, manufacturing, delivery and installation teams, you’re all pulling on the same rope of success, if you will,” he says. “You’re eliminating all the exterior noise and designing to your capabilities instead of trying to adapt someone else’s design to your manufacturing capabilities.”
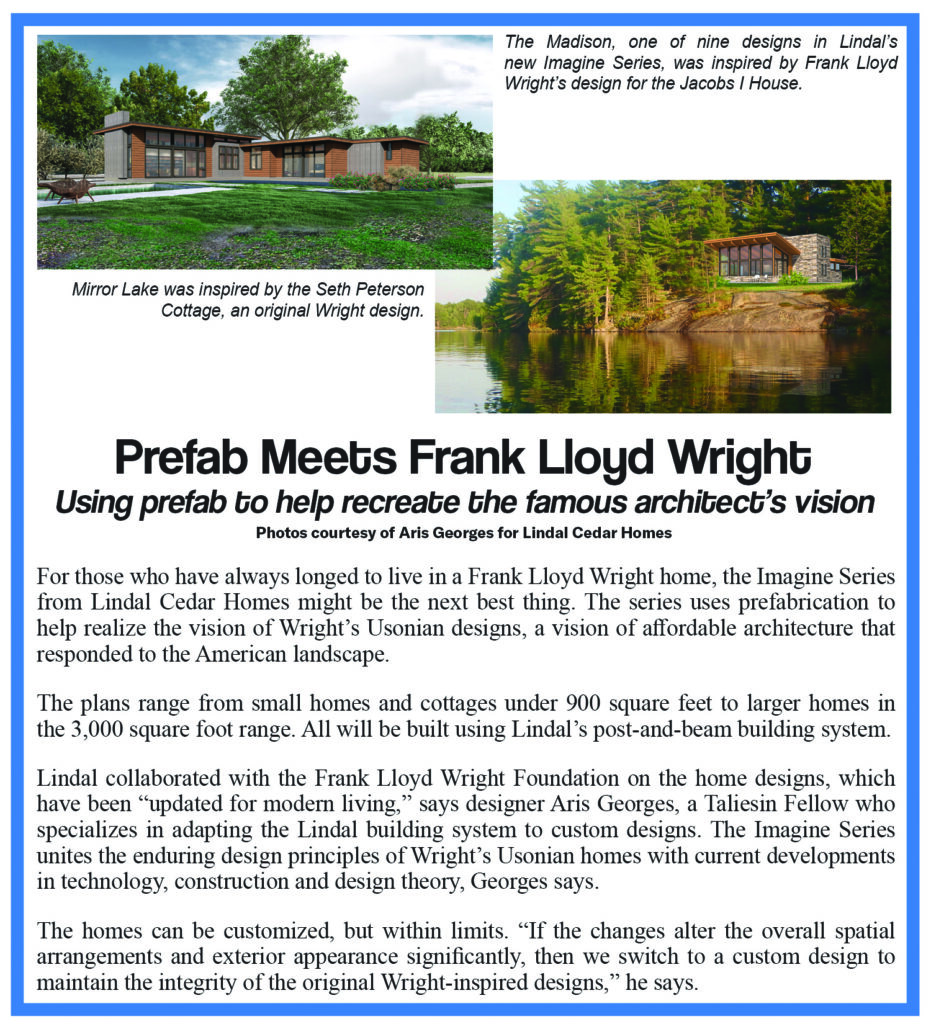
Susan Bady is a freelance writer based in Chicago, Ill., who focuses on residential and commercial design and construction topics including sustainability and building technology.