A roadmap for how to drive efficiency in offsite construction.
- This article outlines the elements of a Lean supply chain and provides examples of it in action.
- Creating a Lean supply chain sounds like a daunting task, but it can be tackled one item at a time.
- Success is about making smarter, more intentional choices.
Efficiency might not be the flashiest topic, but in offsite construction it’s the secret sauce. Without an efficient supply chain, deadlines turn into wishful thinking, budgets balloon like a helium-filled blimp and production lines grind to a halt faster than you can say “backordered materials.”
Enter the Lean supply chain. It’s not just about trimming fat — it’s about creating a system where every piece of the puzzle fits together perfectly, on time and at the right cost. It’s the kind of efficiency that would make even the most Type-A personalities proud.
This article offers a high-level outline of the principles of Lean supply chain management. It offers practical advice and a few lighthearted examples to keep things interesting. My goal is for you to walk away with ideas on how to streamline your supply chain, how to eliminate waste and how to keep your offsite projects on track — without losing your sanity.
What Toyota Taught Us
Before we jump into the specifics, let’s take a quick pit stop in Japan, circa the 1950s. Toyota was recovering from post-war challenges, and resources were scarcer than parking spots at a construction site. To survive, the company had to rethink how they managed production and materials.
Their solution? The Toyota Production System (TPS), a groundbreaking approach that transformed not just their factories but the manufacturing business worldwide. Key to their success was their Lean supply chain. Here’s what they did:
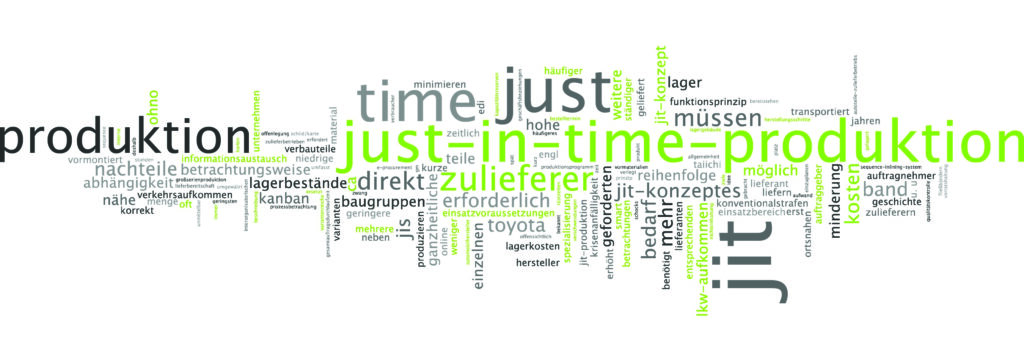
1. Just-in-Time (JIT) Delivery: Instead of stockpiling parts like they were preparing for an apocalypse, Toyota arranged for materials to arrive exactly when needed — no sooner, no later. This saved space, money and headaches.
2. Supplier Collaboration: They didn’t treat suppliers like vending machines. Instead, they built real relationships, sharing production plans and working together to improve efficiency.
3. Standardization: They created standardized parts to make assembly easier and faster. Think of it as choosing pre-cut lumber over trying to saw every piece on-site.
This approach worked so well that Toyota became an efficiency icon. And while you’re not building cars, the lessons apply just as well to offsite construction.
Spotting the Bottlenecks
Before you can streamline anything, you must know where the problems are. Spoiler alert: inefficiencies love to hide in plain sight. Maybe it’s that one supplier who’s always late, or the overstuffed inventory room that looks like a game of Tetris gone wrong.
The following tactics will help you spot supply chain inefficiencies.
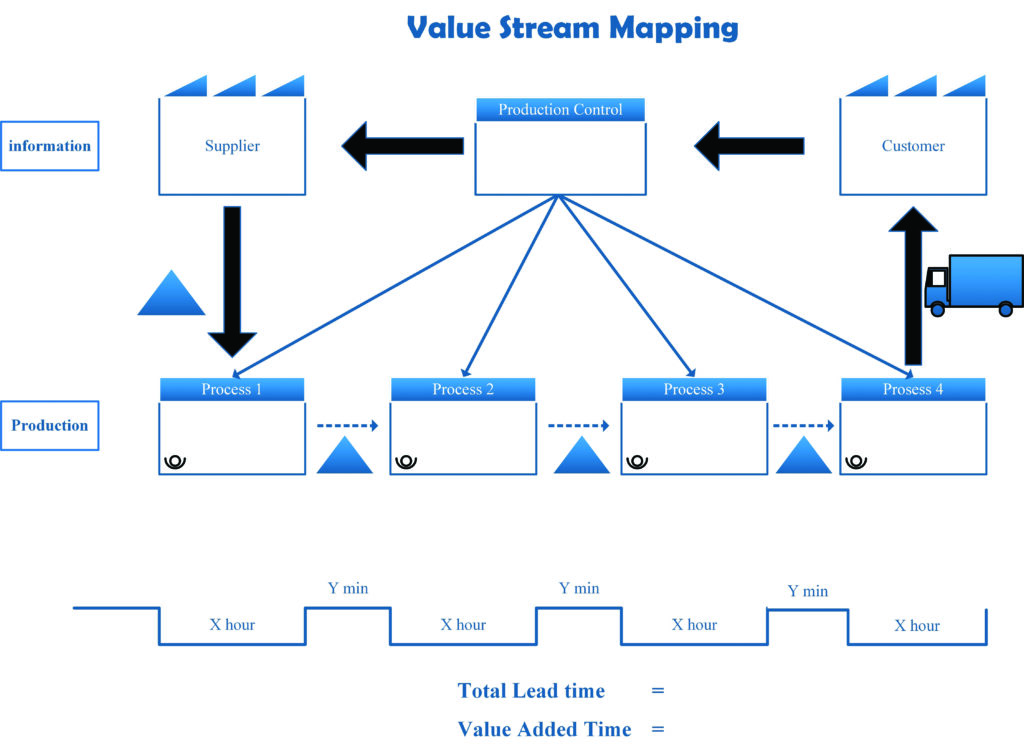
Value Stream Mapping. This fancy term means mapping out every step in your supply chain to see where things slow down. Are materials taking the scenic route to your factory? Is there a bottleneck in procurement? Time to find out.
The “8 Wastes” Audit. Look for the common culprits — like excess inventory, transportation delays, or people waiting around for materials. If your workers have enough downtime to start a book club, you’ve got an issue.
Root Cause Analysis. This is also known as The 5 Whys, an approach in which you ask “Why?” five times to get to the bottom of any recurring problem. For example: Why is the shipment late? Because the supplier didn’t ship on time. Why didn’t they ship on time? Because they ran out of raw materials. Why? And so on.
Example: A modular housing factory realized they were holding a weeks’ worth of window casings because their supplier’s lead times were all over the place. Switching to a reliable, local supplier solved the issue, freeing up floor space and cutting inventory costs by 30%.
Strategic Sourcing
If you want your supply chain to hum along like a well-oiled machine, you need the right suppliers. And no, just picking the cheapest one doesn’t count as “strategic.”
How do you source smartly?
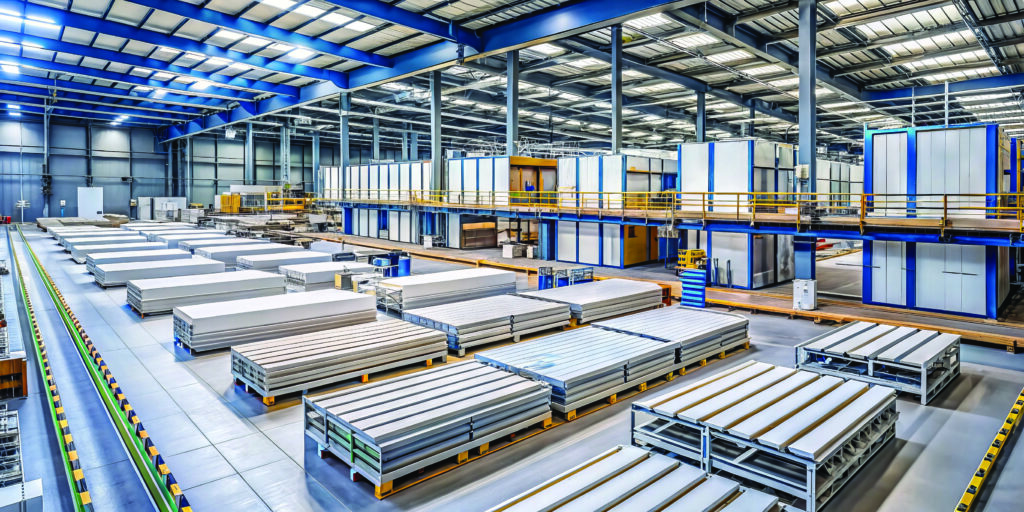
Standardization. Work with suppliers to standardize materials whenever possible. For example, if you can use the same size panels across projects, you’ll simplify procurement and assembly.
Supplier Consolidation. Reduce the chaos by working with fewer, more reliable suppliers who can meet multiple needs.
Local Sourcing. Whenever feasible, choose local suppliers. Not only do you cut down transportation time and costs, but you’re also less likely to end up waiting on a shipment stuck at port.
Example: A modular office pod manufacturer had been juggling three glass suppliers with wildly different lead times. Consolidating to a single supplier with pre-standardized panels cut their lead times in half and reduced procurement headaches.
Just Right Inventory
Inventory follows the Goldilocks principle: too much, and you’re wasting money on storage, too little, and your production line grinds to a halt. The goal? Inventory that’s just right. How do you get that result? Consider these three Lean inventory practices:
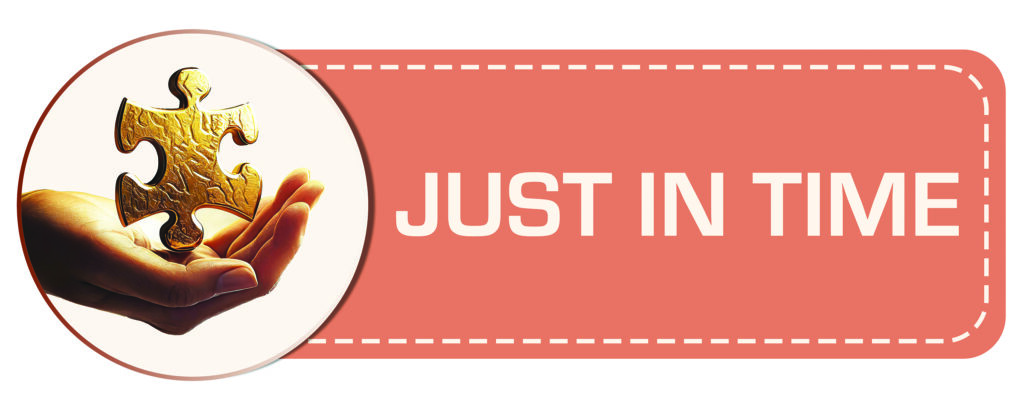
Just-in-Time (JIT). Work with suppliers to synchronize deliveries with production schedules. This avoids overstocking and frees up working capital.
Kanban Systems. Use visual cues or software to signal when it’s time to reorder materials. Think of it as your supply chain’s “low battery” warning.
Cycle Counting. Regularly audit your inventory to make sure you’re not hoarding materials like a squirrel in autumn.
Example: A factory producing modular classrooms switched to a Kanban system for framing materials. Instead of ordering monthly in bulk, they set up weekly deliveries tied to actual production needs. This reduced excess inventory by 20% and made their CFO very happy.
Collaboration Is Key
Your suppliers aren’t just vendors — they’re partners in your success. Treat them well, and they’ll go the extra mile for you. Treat them poorly, and, well, good luck getting that rush shipment. Here are some best practices for supplier collaboration:
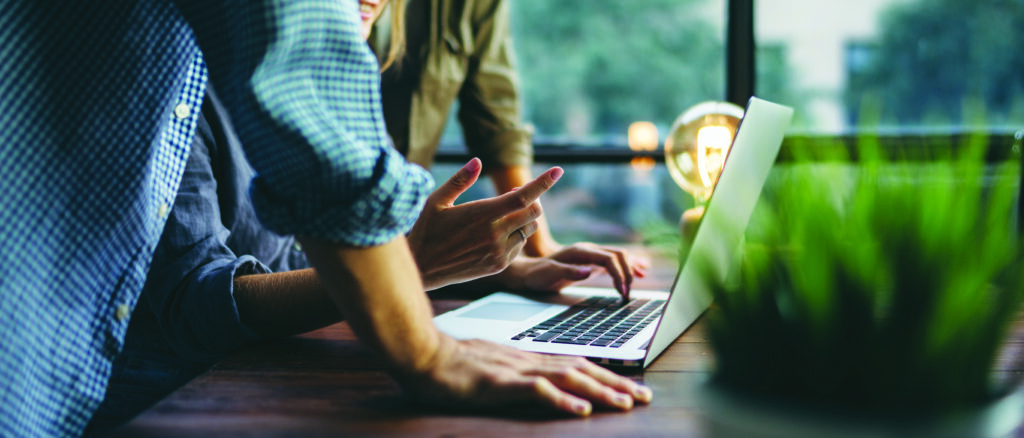
Shared Goals. Align on delivery accuracy, quality standards and cost expectations. Everyone wins when the relationship works.
Joint Planning. Collaborate on demand forecasts and production schedules. It’s easier for suppliers to meet your needs when they know what’s coming.
Continuous Improvement. Work with suppliers to find efficiencies. Maybe they can standardize a component or tweak their delivery schedule to fit yours better.
Example: A modular healthcare builder partnered with its steel supplier to create a shared inventory system. This reduced overordering and improved delivery reliability by 25%.
Technology for the Win
If you’re still managing your supply chain with spreadsheets and hope, it’s time to upgrade. Technology offers tools that make it easier to track, plan and optimize every aspect of your supply chain. Tech tools to consider include:
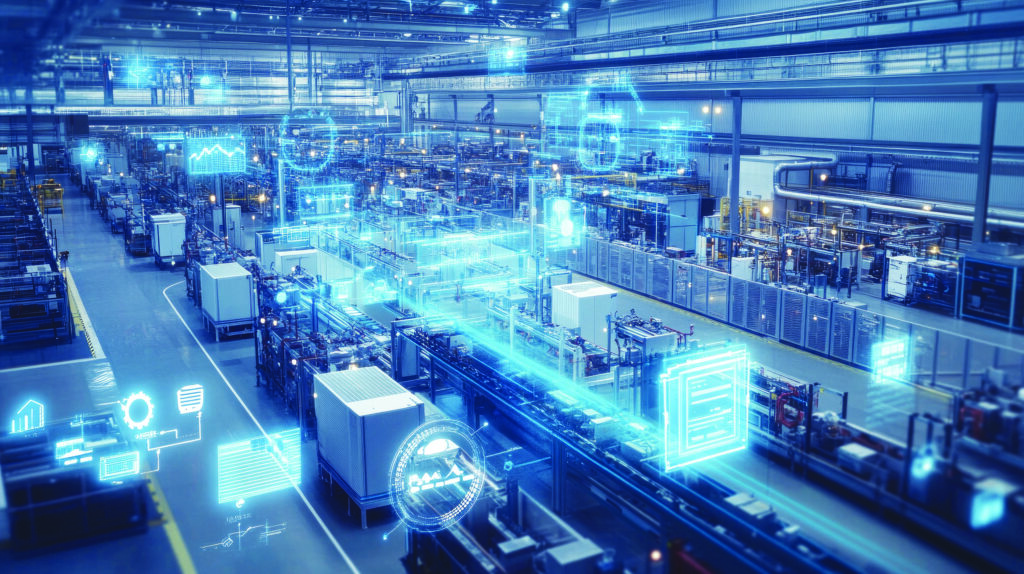
Enterprise Resource Planning (ERP). Integrate production, procurement and inventory data into a single platform for better visibility.
IoT Sensors. Use sensors to monitor shipments or storage conditions, preventing delays or damaged materials.
AI Analytics. Predict demand patterns and optimize ordering to avoid stockouts or excess inventory.
Example: A precast concrete manufacturer used IoT sensors to track material conditions during transit, preventing damage and reducing spoilage by 15%.
Case Studies: Lean Success in Action
Here are a few examples of companies that implemented the above principles and reaped rewards as a result.
Case 1: Collaboration to Reduce Lead Times
A modular homebuilder struggling with inconsistent lumber deliveries worked closely with their supplier to align schedules and improve reliability. Lead times dropped by 30%, and project delays became a thing of the past.
Case 2: JIT for HVAC
A volumetric modular factory introduced just-in-time delivery for HVAC components. This cut inventory holding costs by 25% and ensured materials were available exactly when needed.
Case 3: Simplified Sourcing
A modular housing manufacturer standardized its window designs, allowing them to consolidate suppliers and negotiate better terms. The result? Faster procurement and lower material costs.
It’s About Choices
Creating a Lean supply chain might sound like a daunting task, but it’s really about making smarter, more intentional choices. By following Toyota’s example and applying principles like just-in-time delivery, strategic sourcing and supplier collaboration, you can transform your supply chain into a model of efficiency.
Remember, you don’t need to overhaul everything overnight. Start with small changes — switching suppliers, streamlining inventory, or adopting new tech — and build from there. In the end, a Lean supply chain isn’t just about saving money or meeting deadlines. It’s about creating a system that works for you, your team and your clients.
And hey, if Toyota can do it with cars, you can do it with modular buildings. Go forth and get Lean!
Daniel Small helps offsite manufacturers increase factory throughput and eliminate waste using Lean strategies. As a specialist in Lean for offsite construction, he optimizes offsite production for scalability and efficiency. Let’s improve your process. Contact him at 719-321-1953 or [email protected], or visit www.DaVinciConsulting.co.