Fading West has worked with the State of Colorado to make financing available for modular affordable housing. It’s an effort that manufacturers in other states could emulate.
Over the past two years (2023 and 2024) Fading West, a development and offsite manufacturing firm based in Buena Vista, Colorado, was awarded a total of $3.4 million from the State of Colorado to help it provide affordable housing to state residents. How did they win these awards? And how might their efforts be replicated by offsite construction companies in other states?
We asked Eric Schaefer, the company’s Chief Business Development Officer, about the application process for these funds.
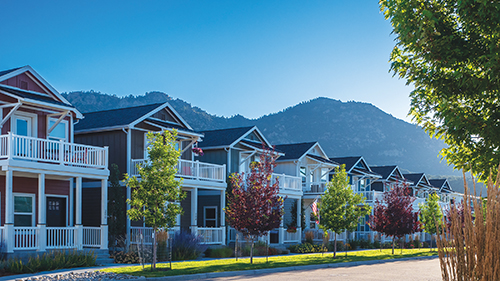
Q: What funds did Fading West receive from the State of Colorado?
A: We were awarded a $1.4 million grant from the Innovative Housing Incentive Program, or IHIP. We got $175,000 in 2023 for working capital and the rest is based on the units produced in our factory. We get between $1500 and $5000 per house, depending on which affordability and energy efficiency criteria each one meets. [Note: Under IHIP, a Colorado business with 500 or fewer employees that manufactures certain types of housing may apply for loans or grants for operating expenses, or for setting up or expanding a factory. The business must be producing units that meet certain criteria (e.g. affordability, location, energy efficiency, etc.)]
Under Proposition 123, we were awarded a $2 million low-interest loan for working capital in 2024. [Note: Proposition 123 was approved by Colorado voters in 2022 and came into effect in 2023. Through grants and loans, it supports affordable housing investment, including in land, low/middle income multifamily rental development, and offsite construction factories.]
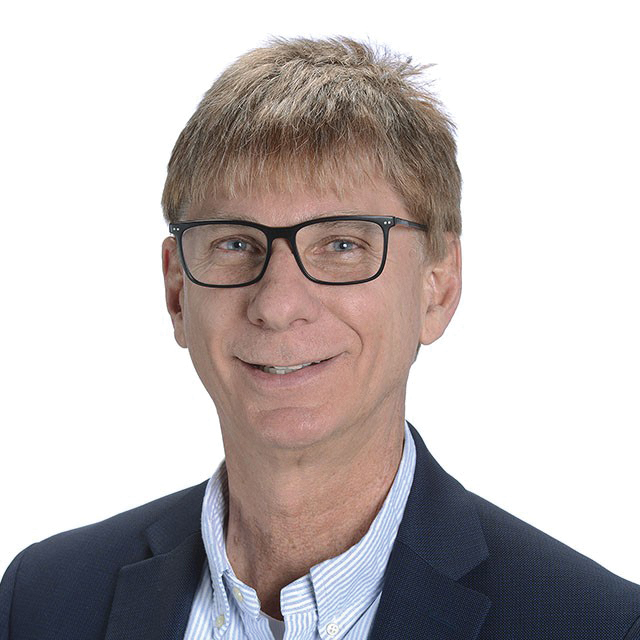
Q: Why were these funds needed?
A: When building affordable housing, there’s always a gap in funding on every single project, so state funds are needed as a bridge. We never just straightforwardly sell affordable housing to developers.
The Governor’s priority has been to get affordable housing built in our state, but it’s important to fund the supply side, not just the demand side. This means helping to build new factories, rather than just funding projects.
For example, there was a $15 million affordable housing project of 40 units in the small town of Lyons. Everybody cheered and 40 families moved in, but if we had been given $15 million, we could’ve built a factory or leased a pre-existing one that was able to manufacture 300-500 homes a year for the next decade. This factory would give the State a steady supply of affordable homes for ten plus years. Wouldn’t that be a better use of state funds than just one project?
Q: What counts as affordable?
A: An example is The Farm in Buena Vista, Colorado [a Fading West development that contains a mix of affordable and market-rate homes]. It’s for residents with 80% to 120% of AMI [average median income]. AMI in Buena Vista is, I think, around $65,000. Some of the two-bedroom 80% AMI homes were purchased by the Chafee Housing Land Trust who then sold them to families at 60% AMI. State funds were used to bridge the gap.
Q: How does one find funding opportunities? And what is the application process like?
A: Applicants give a presentation to the staff at the funding agency. If there’s anything the applicant doesn’t understand, there are people who can answer questions and walk applicants through the process. The agency will help the applicant fill out the forms properly. The agency wants to get good applications, and they’re willing to help with that.
Nonprofits and developers can also apply for funding under Proposition 123, but in that case, it’s for a specific project. For example, the town of Craig, near Steamboat Springs, Colorado, applied for four five-plexes of workforce housing. The town acted as the developer, and they were awarded some money from the State. Although Fading West built the boxes, we didn’t make that application. Craig got the funds and bought the homes from us. So that’s another approach to accessing this money.
The application is like a sophisticated pro forma. And there are various groups that can help applicants put together these packages, such as Tributary Development, a real estate investment firm in Buena Vista, Colorado.
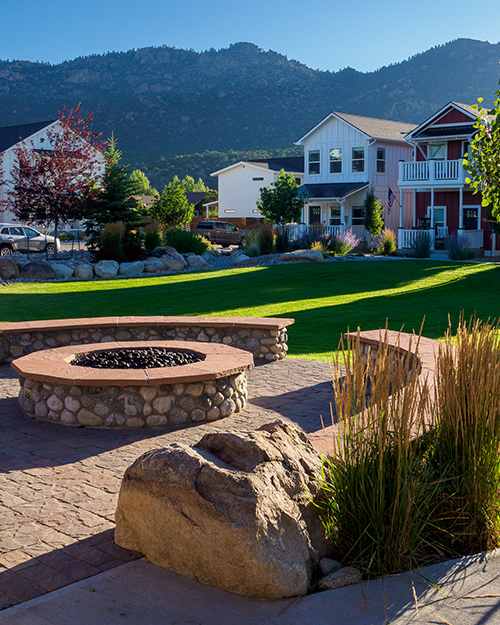
Q: What should applicants be aware of that they might not be?
A: This is all very relational. A major part of my job is forming partnerships throughout the state. Fading West has built relationships with the Governor, and I’m in frequent contact with OEDIT [the State’s Office of Economic Development and International Trade] and CHFA [the Colorado Housing and Finance Authority].
We’ve also worked to build relationships with municipalities across the state, because of a lack of understanding about how offsite construction works. We found there was a negative bias against modular. People wrongly assume that it’s lower quality, that the payment schedule doesn’t work, and that it’s not architecturally pleasing. So, for the first couple of years of getting to know people, a lot of what I did was education.
State agencies are helping factories like ours make sure we’re applying for funding in a timely way, filling out the forms properly, and so on. It’s not adversarial at all. We came into business to help solve the affordable housing crisis in this state, and they see us as helping them reach their goals.
Q: Are there benefits to these sorts of relationships?
A: Besides trying to get funds for affordable housing, we’re also trying to make the entitlement process easier and quicker. We’ve worked with the State government and local municipalities to speed up the processes. We let them know all the pain points we’ve experienced trying to do modular in Colorado.
We want to make sure that when we submit designs to the State, approval takes two weeks, not three months. We have a third-party inspection agency, ICC-NTA, who are in our factory almost every day, stamping boxes for the State.
The State has worked closely with modular factories to shorten the time to get projects and designs approved. Their staff has been very receptive to feedback, and they have implemented new procedures to speed up the State design approval process.
There are over 300 building codes in our state. You don’t want local municipalities ripping out drywall to do inspections when your modules show up on-site. We’ve been bringing local inspectors out to the factory so they can see our process, letting them know they can come any time.
Q: What difference did the funding make to Fading West?
A: We have 150 employees, and there may be months when we have less output, or we don’t have contracts that line up nicely. The typical factory will start hemorrhaging money if it doesn’t have a full pipeline. So, working capital helps start-ups and factories not go under if there is a slow week or month.
Most of the costs for the boxes must be paid before the boxes are built. Developers need to put a deposit down so we can hold their place in line. The State money acts almost like a bridge loan so it can cover deposits if the deposit schedule is different than when money is released by a bank for the developer.
Bear in mind that even if you’re awarded the money, it’s just one piece in a much bigger, more complicated, funding puzzle that might include working capital from a local bank, or possibly a construction loan. For example, we recently worked with nine different groups, including non-profits and State agencies, to get 60 affordable rental housing units built in Buena Vista: the Midland Apartments and Childcare Facility, which is scheduled to be completed in March 2025.
Q: What advice would you give to offsite manufacturers in other states?
A: Don’t try to cook something up on your own. Call the appropriate agencies and tell them what you’re trying to do and ask for their help. They want successful projects. Of course, you still may not be awarded the funds — there are limited funds and more applications than can win awards — but the agencies aren’t there to weed out applications.
State agencies also need to be educated on construction innovation, and they need to take a leap of faith to get involved with innovation in providing housing. That education is something manufacturers can get involved with.
Zena Ryder writes about construction and robotics for businesses, magazines, and websites. Find her at zenafreelancewriter.com. All images courtesy Fading West.