A look at how early adopters are faring with the new ICC/MBI Standards for modular inspections.
- The lack of uniformity across state lines in how inspections are done has hampered offsite’s growth.
- New standards from ICC/MBI promise to streamline the process and make it easier to ship modules from one site to another.
- The states that are embracing these standards are already reaping benefits from them.
Virginia and Utah are the first states to adopt the new standards for offsite inspections, developed by the International Code Council (ICC) and the Modular Building Institute (MBI). The new standards —ICC/MBI Standards 1200 and 1205 — went into effect in Virginia in January 2024 and in Utah in May 2024.
In this article, we’ll look at what adopting these standards means and how other states might follow the lead of Virginia and Utah.
First, however, let’s clarify terms. Building codes specify the requirements buildings must meet for structural safety, fire safety, ventilation, energy efficiency, accessibility, and so on. They apply to both conventionally constructed buildings and those made in factories, including panelized or modular buildings.
The ICC/MBI Standards (which we’ll just call the Standards) specify how offsite inspections are done in the factory. They offer a uniform way to ensure that factory-built components meet code in the jurisdiction where they will be located.
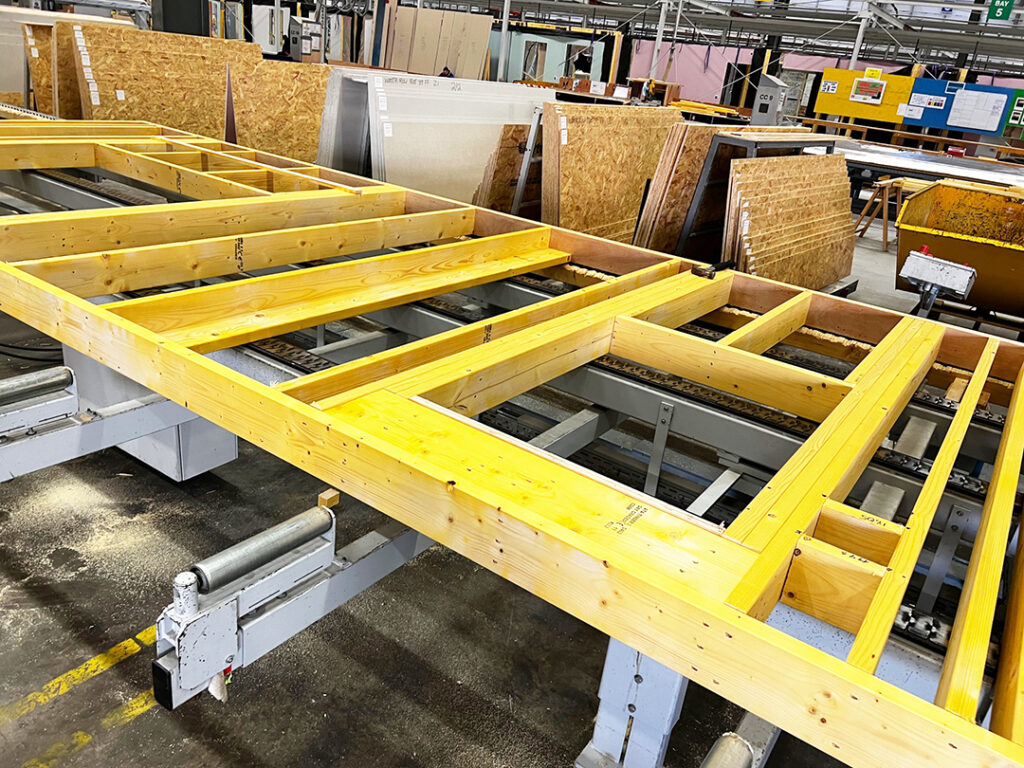
Credit: Virginia State Building Codes Office, Off-site Construction Staff
The Problem with Inspections
What does the current lack of uniformity mean in practice? Colker asks us to suppose a modular factory in Oregon wants to start shipping modules to California. To do so, that factory might have to “re-tool their verification processes,” as Colker puts it. That is, the factory has to adjust to deal with the two states’ different requirements. For example, they might need to have units inspected more or less often, or may have to complete different paperwork, or follow different quality assurance protocols.
However, if California and Oregon both adopt the Standards, then the verification process in the factory will have to follow the same requirements regardless of which state the units are shipping to, Colker explains. That would make things easier for the factory, but it would also streamline things for building officials, who now know that the factory is producing products for their state using a uniform verification process, while also meeting the requirements of their state’s building code.
Colker believes that this is essential to growing offsite construction’s market share. If factories can’t easily ship their products across state lines, it limits the growth of the industry.
In fact, some states even have a patchwork of different standards operating within the state. “Every time a supplier ships to a different county, city, or jurisdiction, there’s a whole new set of rules regarding industrialized buildings,” says Cindy Davis, Deputy Director of Building and Fire Regulations in Virginia’s Department of Housing and Community Development (DHCD). Again, this bureaucracy limits offsite’s growth.
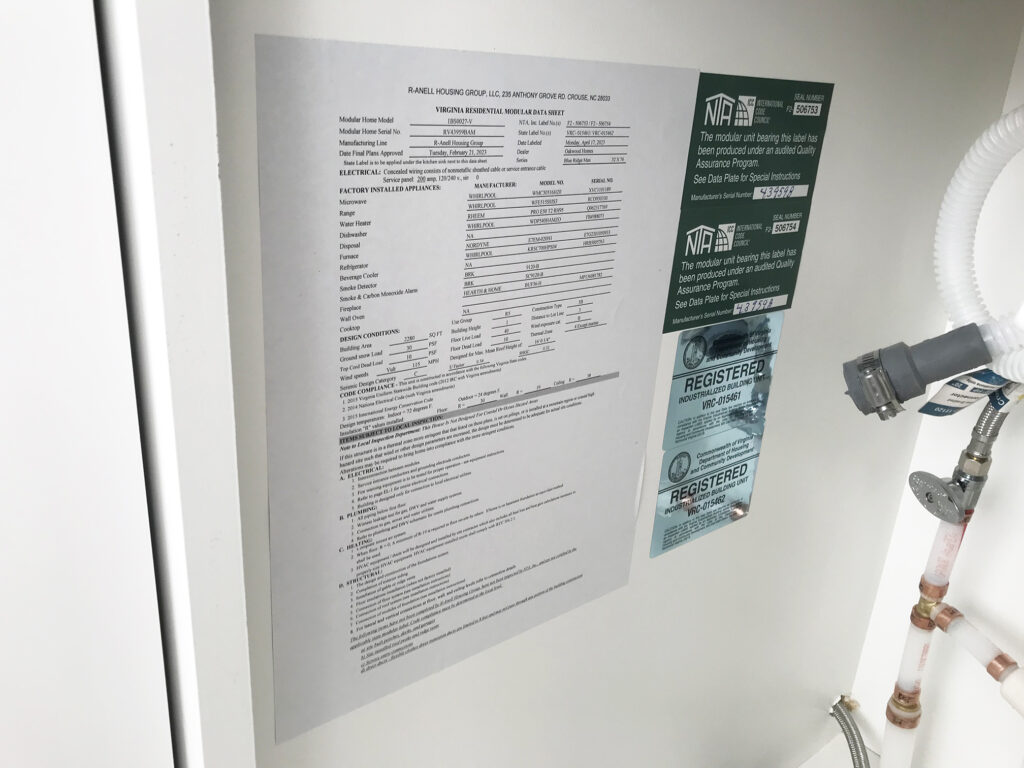
Credit: Virginia State Building Codes Office, Off-site Construction Staff
How the Standards Help
Thirty-nine states have a statewide modular program, which means that offsite construction (not necessarily just modular) is explicitly addressed in amendments to the state building codes. For example, according to the ICC NTA website, North Dakota — which has adopted the 2021 International Residential Code (IRC) — has a statewide modular program that allows for third-party plan review and inspections of offsite-built modules and panels at the factory.
Some states have a statewide modular program, even though they haven’t adopted statewide building codes. Colker says that Texas falls into this category. Although building codes are adopted and enforced at the local level, the modular program sets code requirements for offsite construction projects statewide. This provides consistency for manufacturers.
Before adopting the Standards, Virginia already had a modular program, and it included a lot of the best practices that informed the development of the Standards, such as allowing certified third-party inspections.
Davis says, “When a building is constructed on-site in Virginia, the building department does on-site inspections [to ensure code compliance].” But when modules or closed panels coming into Virginia are manufactured out of state, “our building department doesn’t typically visit the factory. Instead, the state [relies on] state-approved, third-party inspection.” About 10 inspection agencies have been approved in Virginia. How those agencies are approved is set out in the Standards.
“The inspection agency becomes our eyes and ears in the plant, and we count on them and the manufacturer’s quality control program” to ensure code compliance, Davis says. In addition, she says the state employs “about three individuals who periodically audit the manufacturers and the inspection agencies to make sure they’re doing what they’re supposed to be doing on behalf of the State of Virginia.”
Most of the offsite-built units sited in Virginia come from out of state —largely from Pennsylvania, Georgia, and North Carolina. The approved third-party inspection agencies contract directly with the manufacturers in those states, and the agencies are authorized to affix Virginia’s seal to components that have been inspected and approved.
When the unit arrives at the building site in Virginia, Davis explains, “the building department sees that seal and the unit is automatically accepted.” The local jurisdiction still inspects things like the connections between the units and the foundation.
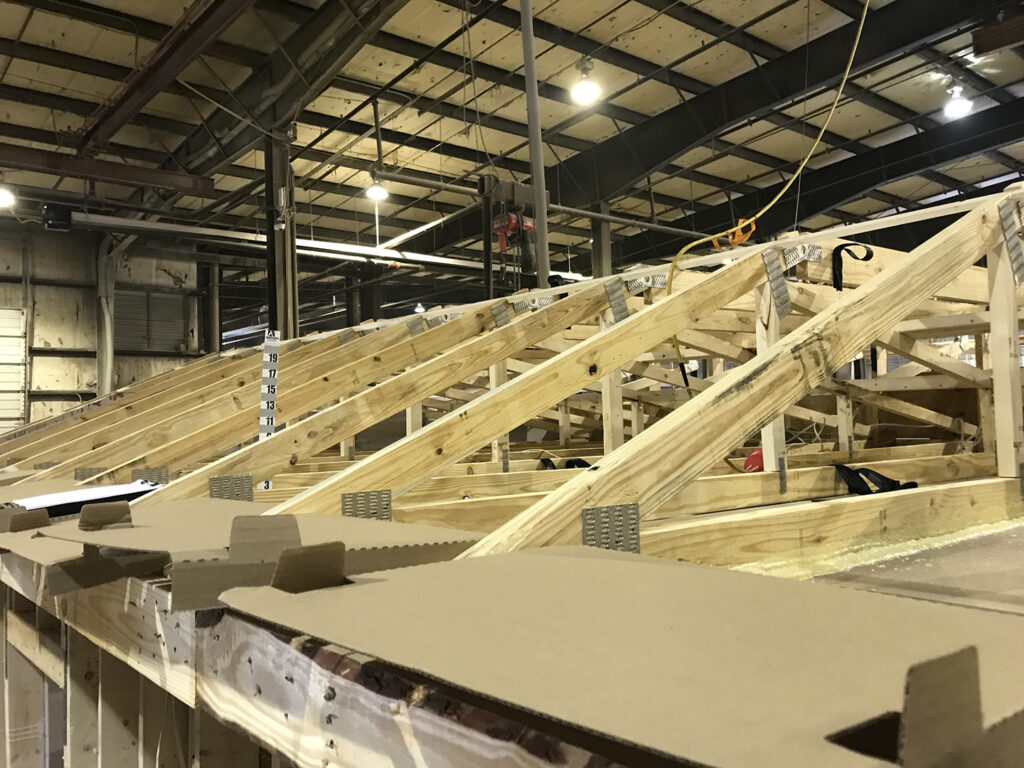
Credit: Virginia State Building Codes Office Off-site Construction Staff
Standards Solve Problem
Adopting the Standards in Virginia didn’t result in a big change. Colker says, “Virginia was already doing most of the best practices identified in the Standards. So, they didn’t necessarily need to adopt them. But doing so sends a strong signal of the importance of having a common basis for inspections.”
Davis concurs. “Our industrialized building program already mirrored the Standards, so adopting them wasn’t a big leap. It didn’t change anything that we do here in Virginia.”
She notes that the system works very well. “We’ve never had to issue a notice of violation to a plant. Problems are very, very rare. Those rare occurrences were just matters of a one-off oversight, and the factory fixed the problem right away.”
The Standards can also earn their keep after hurricane, wildfire, earthquake or other natural disasters. For instance, MIT’s Center for Transportation and Logistics is exploring ways that factory-built housing could help disaster relief efforts. According to MIT Research Associate Lauren Finegan, “If you’re able to bring panels or modular units from another state, you’re able to lessen the load on the local construction industry. You’re also using local labor capacity more efficiently, so the same number of people can build more homes more quickly.”
One state that is using modular for disaster relief is Hawaii. The state doesn’t have a statewide modular program, but is making use of the Standards anyway. In the wake of the August 2023 wildfires “Maui County and FEMA have incorporated the Standards into their request for proposal for recovery housing,” Colker said.
Jon Hannah-Spacagna, Government Affairs Director at MBI, notes that the houses will be built outside of Hawaii using modular construction. They will be built to Hawaii’s state building code and inspected and approved according to the Standards.
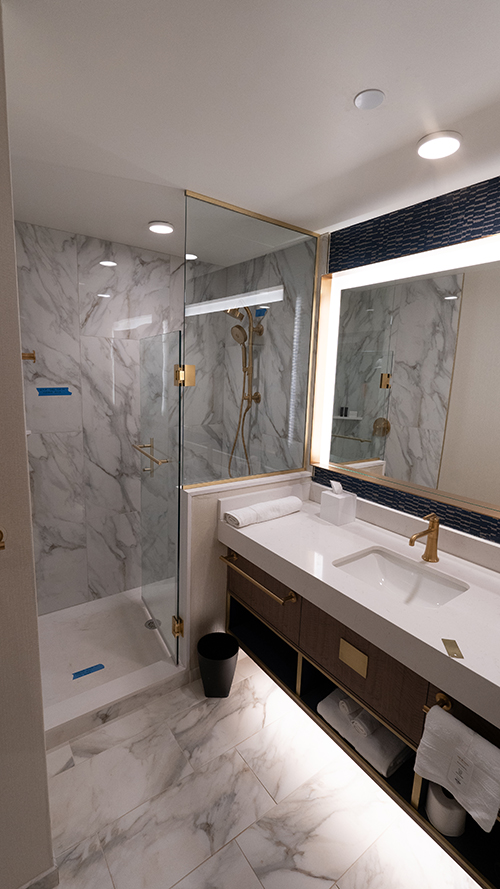
Credit: Bristol, VA Building Department
The Adoption Process
Adopting the Standards in Virginia was easy — because the state already had a statewide modular program and because Virginia goes through an automatic update of the statewide building codes every three years.
As part of that automatic update process, the Building Codes Office in Virginia’s Department of Housing and Community Development (DHCD) put forward the proposal to adopt the Standards at the state level. After discussion, there was consensus on sending the proposal to the governor-appointed DHCD board for approval.
Thing were trickier in Utah. That state didn’t have a statewide modular program and so, Colker says, “they had to pass legislation to establish a statewide modular and offsite construction program, using the Standards as the basis for that new program.” But Salt Lake City had already adopted the Standards, so Utah officials were able to see their value.
Prior to adopting the Standards, “Salt Lake City required every project to be inspected by a local official,” Colker explains. “But local officials couldn’t leave the jurisdiction to inspect projects in factories outside that jurisdiction. Adopting the Standards allowed them to leverage third-party agencies.”
Hannah-Spacagna spent months working with Utah legislators and other state officials to “write the bill language for their new state modular program.” He says the foundation for the state program was laid by Salt Lake City’s adoption of the Standards in 2021, which the city needed “in order to save a multi-million-dollar, multi-family modular project that they had no way to get approval for because [the modules were] built in California.”
Upcoming Adoptions
Hannah-Spacagna says, “As an industry, we’d like all states to adopt the three ICC/MBI published standards: 1200, 1205, and newly published 1210, which is specific to Mechanical, Electrical, and Plumbing for modular. I’m working on a committee with ICC now to have 1200 and 1205 included in the 2027 IBC/IRC.” He explains that states adopting these Standards create consistency across state lines and increase speed and efficiency. That makes it easier for “modular manufacturers to operate across the country.”
Other states are making progress. Colker says, “Ohio is in the process of updating their regulations around offsite construction and a few other states are going through, or will soon be going through, their regular code update process and we’re looking at trying to include the Standards.”
The process of adopting the Standards will vary from state to state, depending on the current situation in each state. Davis recommends reaching out to Jon Hannah-Spacagna at MBI ([email protected]) if you’re interested in getting these codes adopted in your state, because he can help coordinate the necessary parties.
Zena Ryder writes about construction and robotics for businesses, magazines, and websites. Find her at zenafreelancewriter.com.