Recruiting and training the workers we need will be a collaborative effort. Everyone must be involved.
For years, the average age of construction workers has been rising, and over the next ten years, 40% of this aging workforce will retire. This represents a significant loss of talent and wisdom. Construction has long been dominated by the “learn-by-doing” model and our current workforce has spent decades attaining and honing their skills.
As the industry continues to lose skilled workers, we need to find more efficient ways of leveraging a smaller construction workforce. Offsite manufacturing represents one excellent solution. Therefore, it is in our collective interest to grow our offsite manufacturing capabilities as an industry, to build more advanced housing manufacturing facilities, to create manufacturing-friendly product demand, and to upskill workers so they can operate advanced manufacturing equipment.
There is a lot of room for growth. The Modular Building Institute’s 2024 Permanent Modular Construction Report estimates that the modular market share of new construction building starts in 2023 was only 6.64% — just a half a percent better than the previous year. We need to accelerate the adoption of modular construction and other prefabricated technologies, and we need to start now.
This challenge creates a unique opportunity for the building industry as a whole to not only build faster, better and more efficiently, but also to find and train its next generation of leaders. However, we must first overcome the numerous misperceptions not only about what an industrialized construction future looks like, but also what opportunities offsite construction can offer to young people.
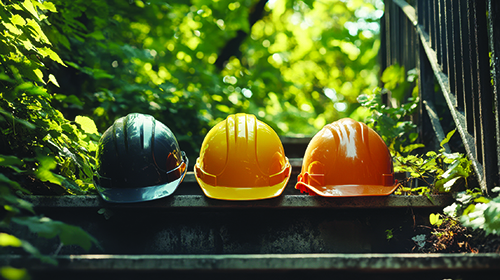
Stanley Black & Decker’s inaugural 2022 Makers Index polled 801 high school sophomores, juniors and seniors and found that 23% disagreed that skilled trades work with cutting-edge technology and 19% doubted the work [was] in demand. The report also found that young people believed trades to be physically demanding (81%), dangerous (73%), and dirty (62%).
The results from the Stanley Black & Decker report should come as no surprise though. Most of the construction training delivered in middle and high school revolves around traditional on-site building methods. Offsite construction education is mostly nonexistent. At the college level, education surrounding offsite methods is fragmented, at best, with only a handful of colleges around the country offering an introductory class or two.
This must change. Early exposure to our industry is imperative if we want young people to think about careers in offsite construction, and you can’t get excited about something you know nothing about.
To successfully recruit and train the next generation of workforce for modern industrialized offsite construction we need to take a wider view than that of traditional trades. We need workers for all areas of our industry: real estate development, product design, engineering and supply chain, technology and manufacturing, transport, and on-site assembly.
This will require involvement from a wide variety of stakeholders. In fact, there’s an incredible opportunity for government, education and industry to collaborate and help move the needle.
The State of Colorado has been leading the way in its support of offsite construction with their governor’s public endorsement of modular methods. In addition, the City of Boulder and Boulder Valley School District have collaborated to build a 30,000 sq. ft. factory where students will learn to construct energy-efficient modular homes. Although that’s a great start, more government support and funding nationwide is necessary for exponential growth.
More broadly, many manufacturing facilities are now offering open houses and tours to students, teachers, parents and community members to not only increase exposure to our industry, but also to inspire future employees, introduce career pathways and help the next generation discover a passion to participate — whether that’s on a production line, in HR, architecture, or engineering. In fact, Momentum Innovation Group has been collaboratively developing offsite curricula for middle schools and high schools to increase exposure and interest in the industry.
If you aren’t already collaborating with schools, industry, and/or government to increase the education, engagement, and training of our future workforce, I encourage you to get involved: hold an open house or conduct tours, send your most engaging employees to speak at local schools, offer internships for high school and college students, etc.
Many of us are currently competitors and will continue to be into the future. But the reality is that without everyone’s participation in developing our future workforce, none of us will go anywhere fast, and we definitely won’t go far.
What innovative collaboration have you seen that is helping to drive our industry forward? Let’s talk.
Colby Swanson is an innovation strategist and construction technologist who has spent 23 years working with developers, production homebuilders, building material suppliers, offsite manufacturers, insurers and federal government agencies. His recent focus is on the market adoption of industrialized building. Colby earned his Biochemistry degree from Arizona State University.