Does 3D-printed construction for buildings live up to its hype? The answer is complicated.
- Long-term, 3D printing holds real promise for the building of homes and offers great design flexibility. However, some current claims made by its advocates don’t stand up to scrutiny.
- This technology’s radical departure from convention means that training will be needed for architects and engineers, as well as for construction workers.
- Although builders and developers who have worked with 3D printers report lowered construction costs, those savings have yet to be fully quantified.
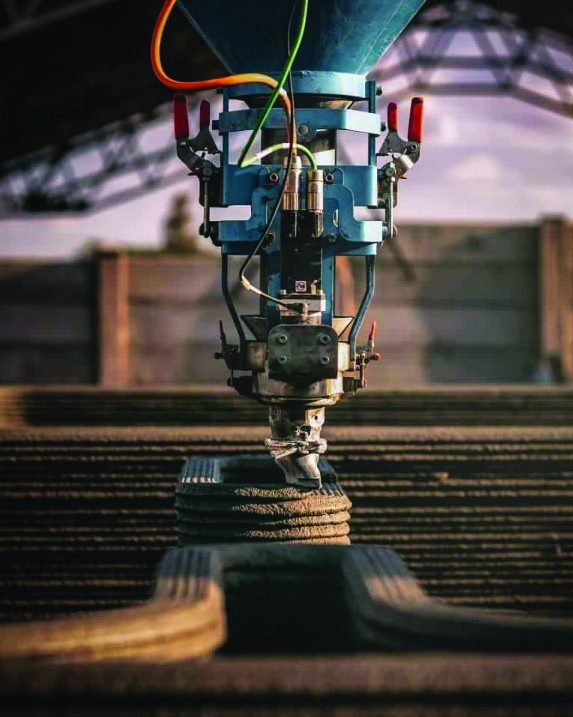
Photo credit: 14 Trees
“The industry has a lot of misconceptions, and those misconceptions are hurting the industry,” says Philip Lund-Nielsen, Co-Founder and Head of Americas at COBOD International, a company that makes the equipment needed to 3D print structures and has offices on six continents.
“Some years ago, you could hear: ‘Oh, you can 3D print a house and it’s going to cost only $4,000 for the full house.’ Or, ‘You can 3D print a skyscraper at half the cost.’ Or, ‘You can 3D print a home in six hours.’ Those claims are baseless. And that’s why COBOD is all about being transparent about the real numbers out there.”
COBOD hasn’t been shy about challenging such claims. According to a 2019 article by Joris Peels for 3DPrint.com titled “Truth in 3D Construction: ‘Nobody 3D Printed an Entire Building,’” COBOD International published a whitepaper that debunked several overinflated marketing claims. These included claims about companies 3D printing entire buildings or printing them very rapidly.
Peels said that a lot of those claims don’t stand up to scrutiny. “At 3DPrint.com, we’ve always been very skeptical about the goings-on in 3D-printed construction,” he wrote. He said that he has seen a lot of claims of houses being 3D printed in 24 hours, but that each time the claimant “conveniently forgot to invite the media” to the event.
Hype aside, what are the real advantages and disadvantages of 3D printing in building construction?
Some of the disadvantages relate to building code changes and professional-education requirements. The advantages include less concrete, lower labor requirements, upskilled jobs and design flexibility. 3D printing can also lead to more rapid, precise and efficient builds. Cost savings is another possible advantage, but it is still too early to quantify that savings.
Code Challenges
According to Russell Varone, founder of the automated construction company Diamond Age, based in Phoenix, Arizona, 3D printing companies are focusing on changing building codes, getting new building codes written, and/or asking the American Concrete Institute to have new classifications for their materials.
“There’s enough difference in what some of my peers and worthy rivals out in the field are building that they don’t line up clearly enough for a building inspector in whatever town, USA,” says Varone. “He opens up his building code and goes, ‘I don’t know what you’re bringing me. I don’t understand this. I don’t know how to read the building code and protect my residents.’”

Credit: PERI
Worker Training
Another challenge is the need for workers with technical skills. Lund-Neilsen points out that the industry in general needs skilled people to operate the equipment necessary for a 3D build — rather than moving bricks around, workers are operating high-tech equipment.
As the industry grows, that need will become an advantage because training is something companies will have to offer. “We’re educating the workforce of the future, which should lead to higher salaries with less backbreaking labor,” he says.
Training isn’t just for factory workers, either. It also extends to the engineering and design team. For instance, it can be a challenge to find a structural engineer who knows how to work with this technology.
When it comes to architecture, “you might not have architects who know how to design for 3D printing,” says Lund-Nielsen. It unlocks more design freedom than they’re used to, and they’re unsure how to take advantage of that.
Embracing Possibilities
Lund-Nielsen believes that, eventually though, the increased design possibilities will have great appeal to architects. “It’s one of the aspects I find most attractive to this technology. Buildings no longer have to be rectangles or squares. The machine can pop out these beautiful buildings that are far more organic, far more tailored to the local community.”
Not everybody has to live in the stereotypical framed house because the technology can create homes that are more stunning to look at for the same cost, he says. “The machine doesn’t care if you’re doing a round building or a rectangle.”
Another advantage of 3D printing is that it uses concrete in a more sustainable way. “The fact that you are only printing what you need can significantly reduce the amount of waste on a construction site, also lowering the carbon dioxide emissions,” says Lund-Nielsen. He compared that to a regular construction site, where “typically the waste factor can reach upwards of 30%.”

Credit: Dar Al Arkan
Lower Costs?
Most people in the construction industry understand that the use of automation can reduce labor costs, improve precision and accelerate the build schedule, and 3D printing is no exception. “As an example, one of our customers in California recently printed [a building] of 1,200 sq. ft. in six workdays,” says Lund-Nielsen. That job only required three people on the site to operate the machine.
But while such results are impressive, he says that because the 3D-printing industry is so young, there’s no reliable data on how much money this technology can save.
Despite the lack of data, he insists that the savings are real. “We have started to hear anecdotally from our customers that it is getting cheaper, that it is getting faster,” he says. “If you do it faster, it’s a quicker return on investment and a bigger return on investment.”
What’s Next?
At this point, the 3D printer typically completes just 8-10% of the value of a home, Varone says. But some industry players believe that’s just the first step, and that we will eventually move towards fully automated construction.
Varone is betting on it. His company, Diamond Age, is gearing up to do 26 different automated operations that include spraying stucco, attaching roofs, spraying paint, cutting door and window openings, and much more. These operations will complete 55% of a house.
He was motivated to develop this automated construction system because of his previous experience working at Tesla. That experience made him familiar with industrial concepts of efficient process optimization such as the Toyota Production System, which aims to eliminate waste in manufacturing.
That includes wasted time caused by inefficient processes. “Diamond Age’s thesis is that you have a labor shortage masking a process problem,” he said. “If everyone in the world woke up tomorrow morning and no one knew how to build a house in a production environment, and there was a Manhattan Project of, ‘oh, let’s collectively figure out how to build homes in this hypothetical scenario,’ you would not design the trade-labor stack that we have today.”
He believes the more likely outcome would be something that looks like a Tesla factory making cars or a Foxconn operation making cell phones, with a lot more design flexibility. That’s the future for the construction industry that he hopes 3D printing will lead to.
Kat Friedrich writes about energy, engineering, physics and technology. She is a graduate of the University of Wisconsin-Madison College of Engineering and is the editor-in-chief of Solar Today.