Which offers better performance? A field study of 25 buildings provides some insight.
Offsite construction is a logical alternative to the inefficiencies of site-building, and the numbers show increasing adoption. In fact, the Modular Building Institute estimates that the market share for volumetric modular doubled from 2.9% to 6% between 2017 and 2022. In large part, this growth was because modular shortens project schedules by 30% to 50%.
However, as everyone in this industry knows, barriers remain to further adoption of volumetric modular. These include costs, logistics and questions about building performance.
Costs
Modular project costs are 5% to 10% less than site-built on average, and shortened project schedules provide owners with cash flow months earlier than with conventional construction. However, developer cash/equity requirements are higher: modular projects often require upfront deposits of 30% or more of the modular contract. The manufacturer needs these deposits to purchase materials and reconfigure production lines for each job. In a previous article (see “Modular’s Cash Flow Challenge” in the May 2024 issue), I detailed this financial challenge and described some industry efforts to address it.

Logistics
In terms of logistics, the main challenge with volumetric modular construction is the expense and liability involved in hauling modules over the road. A recent US Department of Energy study of more than 50 multifamily projects across the US identified panelized as a growing alternative in response to this challenge. (The study referred to it as “non-volumetric modular,” but we’ll use the term “panelized” for clarity.) Panelization involves the offsite prefabrication of building sub-assemblies such as two-dimensional floor, wall and ceiling panels.
Panels can solve some problems. For instance, unlike volumetric modular, in which the manufacturer must absorb the cost and inefficiency of manufacturing a new product for each project, panel manufacturers can produce standardized products that adapt to a wide range of projects and designs. This makes them better able to sustain production between project cycles, to make more efficient use of factory resources and to retain a more stable workforce.
Volumetric modular companies generally use materials such as wood, drywall and batt insulation that are vulnerable to moisture until the modules have been placed and the building dried in. (Modules are wrapped at the factory to protect them from weather, but a tear in the wrap can lead to water intrusion.) In contrast, non-volumetric floor, wall and ceiling assemblies do not use moisture vulnerable materials and are often small enough to be stored under a roof.
Manufacturers of advanced panelized systems also use a wider variety of materials. These include steel studs with built-in thermal breaks, mineral wood insulation and water-resistant composite sheathing products.

Building Performance
Although these advantages are compelling, questions remain about building performance. Specifically, how does panelized construction compare to modular?
This is an important question. Many cities now require commercial buildings to do ENERY STAR benchmarking every year, and if the building does not earn a minimum score, the jurisdiction can force upgrades. Given those requirements, a new building that starts its life with the lowest possible energy use will likely be more attractive to owners and investors.
A 2022 study sponsored by the National Renewable Energy Laboratory (NREL) provides some insight into the energy use question. Researchers looked at 20 site-built, two volumetric modular and three panelized buildings in Seattle, Wash. (The study focused on a single location so that all buildings in the study would face the same climate conditions and be subject to the same code requirements.) All were commercial multifamily buildings with between five and 15 stories above grade, and an average of roughly 110,000 sq. ft. of conditioned floor area.
All buildings in the study performed better than the 2018 Seattle Energy Code (SEC) multifamily energy use target of 35.0kBtu/sf/yr, widely considered among the most stringent energy codes in the US.
But while all buildings met the code, the specific numbers varied by the building system. Panelized construction had better energy performance (23.3 kBtu/sf/yr) when compared to either volumetric modular construction (27.2 kBtu/sf/yr) or site-built construction (32.2 kBtu/sf/yr). Energy performance was determined by ASHRAE 140 compliant building energy modeling and post-occupancy energy use data from the Seattle Energy Benchmarking Portal, which building owners use to certify their energy use.
Building envelopes for site-built and volumetric modular construction consisted primarily of exterior wood wall framing, batt insulation and OSB or CDX sheathing. Roof assemblies were built with conventional or pre-engineered framing, and a combination of batt insulation and rigid roof deck insulation. Despite the similar materials, the quality and airtightness of building envelopes appeared to be better for the modular buildings than for site-built.
The panelized buildings had steel framing, mineral wool insulation and an uninsulated service cavity for piping, wiring and ductwork. Panels were enclosed with exterior-grade fiberglass mat gypsum on either side with a thermal break between the steel framing and interior/exterior finish surfaces of the panels.
Thermal transmittance (U) values for site-built and volumetric modular wall assemblies varied from 0.040 to 0.063Btuh/sf/oF. U-values for non-volumetric modular wall assemblies ranged from 0.030 to 0.040 (lower is better). Similarly, thermal transmittance (U) values for site-built and volumetric modular roof assemblies varied from 0.020 to 0.027. U-values for non-volumetric modular roof assemblies ranged from 0.015 to 0.020.
The modules used for the modular buildings in this study were produced over a period of three to six months and then stored outdoors at the production site, or staging area near the jobsite, until placement. They were made by different manufacturers. Finishes and fixtures were installed for volumetric modular (80% to 90% complete in factory); panelized finishes and fixtures were installed in the field once the building was dried in.

Shared Benefits
Despite the differences in thermal performance, both volumetric and panelized construction offer compelling advantages. Fewer on-site workers are needed, and shortened construction schedules result in safer jobsites and less noise, traffic and other disruptions to the surrounding community. In addition, the manufacturing process for panels and modules includes established quality control protocols in an enclosed, climate-controlled work environment.
Compare that to site-built construction, which depends on a largely transient workforce under the control of multiple trade contractors working in the sun, rain, wind and snow.
The repetitive, less specialized and less physically demanding nature of prefabrication in a factory setting also allows both volumetric and panelized manufacturers to draw on a wider pool of potential workers, often for lower costs.
In summary, the study confirmed what most professionals in the offsite construction industry have long observed: that both volumetric modular and panelized construction benefit from higher labor productivity and safety in a controlled, factory environment. However, panelized construction balances these gains with lower capital investment, greater transportation efficiency and more design flexibility. As a result, panel manufacturers may be better able to scale the production of standardized assemblies rather than to absorb the cost and inefficiency of manufacturing custom volumetric modules for each project.
The study also put numbers to the long-standing question of comparative thermal performance. Of course, this won’t be the final word: it would be helpful to see similar studies of buildings in different climate zones. However, the results show that panelized construction can deliver impressive performance.
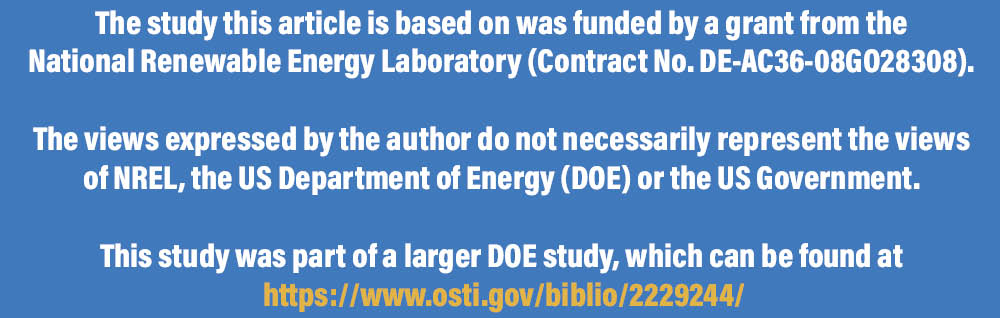
Kevin R. Grosskopf is a Professor at the Charles W. Durham School of Architectural Engineering and Construction at the University of Nebraska. He has a PhD in Architecture, an MS in Construction Engineering, and several years of experience as a construction manager. All photos were provided by the author.