Recent changes reflect a better understanding of this material’s unique properties.
- Historically, building codes equated mass timber with stick framing in terms of structural strength and fire resistance. That led to unnecessary restrictions.
- Structural and fire testing has helped update the code requirements. Mass timber structures can now be built taller, and most have lower encapsulation requirements.
- Some projects can even exceed the current code limits if the engineers and architects can prove they’re safe. The code includes an alternative process to help them make that case.
If you’re considering building with mass timber [MT] for the first time, you might not be aware of how codes have been updated in recent years to better accommodate this material. Newer code versions reflect a better understanding of MT’s strength and fire resistance. This article looks at some recent developments.
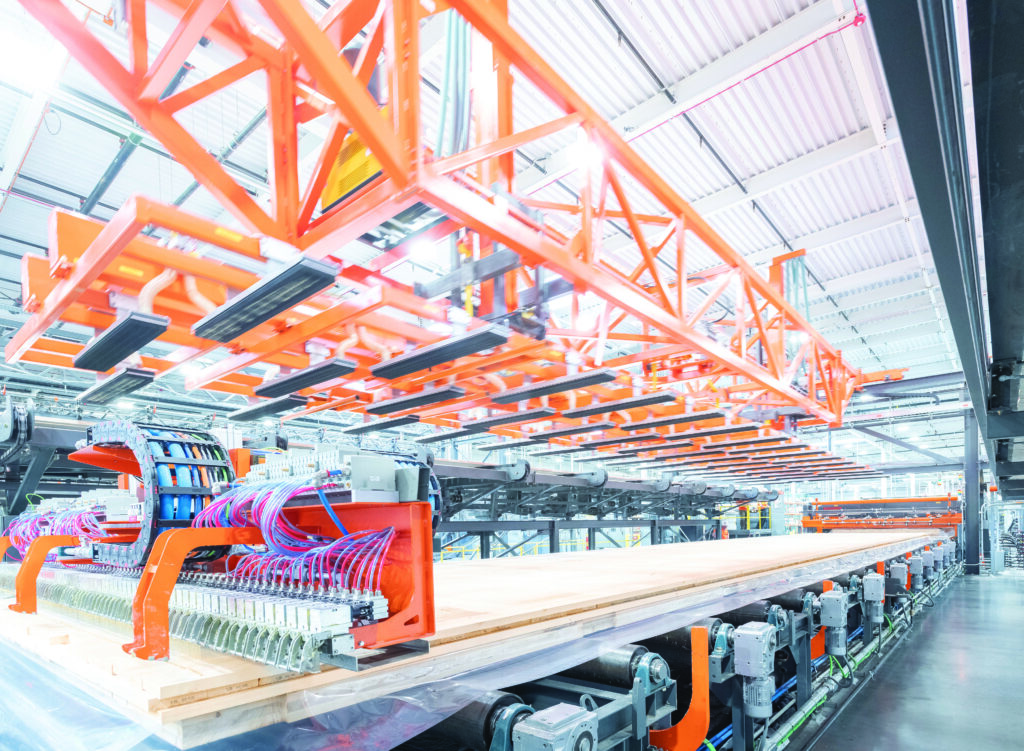
Photo courtesy of: Mercer Mass Timber
Early Code Requirements
Katherine Setterlund is the Senior Mass Timber Engineer at Mercer Mass Timber, a company with manufacturing facilities in Arkansas, Washington and British Columbia. She says that a simple description of mass timber is “big timber made up of little pieces of timber glued together.” MT comes in the form of beams, columns and panels for walls or floors. Technically, the term can include standard glulam beams, but it most often refers to cross-laminated timber, or CLT, which is made by cross laminating several layers of wood perpendicular to one another (like plywood).
Building code requirements for MT buildings include how many stories are allowed in specific circumstances, and how many sprinklers will be needed in a given space. They also include nitty-gritty details such as “how many screws you need to have,” Setterlund adds.
Codes used to assume that MT was more like traditional wood than it actually is, Setterlund explains. However, it’s actually quite different in terms of fire resistance and structural strength.
“Conventional stick framing burns very fast, and its strength is quite limited because the supporting members are so small and skinny,” she says. “The codes assume that you’re using the worst studs available, which is why stick-framed buildings can go up to only six or seven stories.”
Equating MT with stick framing resulted in codes that were quite conservative. “Mass timber used to be capped at six stories,” says Ed Lisinski, Midwest Regional Manager at the American Wood Council [AWC]. That’s no longer the case. “Mass timber columns can, in fact, support much larger loads and much taller buildings, more in line with concrete and steel,” Setterlund says.
Mass timber is also more fire resistant than stick framing, largely because of the size of the members. When MT elements such as beams and columns burn, “you get what’s called the char layer around the outside, which gives almost a self-extinguishing effect, protecting the inner wood,” says Setterlund. “When we design, we take the char layer into account, to make sure the inside portion of the element will be enough to maintain the load.”
In the past, a misunderstanding of the char effect led to fire regulations that imposed unwarranted encapsulation requirements on MT. “It was a shame so much mass timber had to be covered up for fire reasons — because many developers wanted to use mass timber so they could expose it and sell at a premium,” Setterlund says. “Encapsulation killed a lot of projects.”
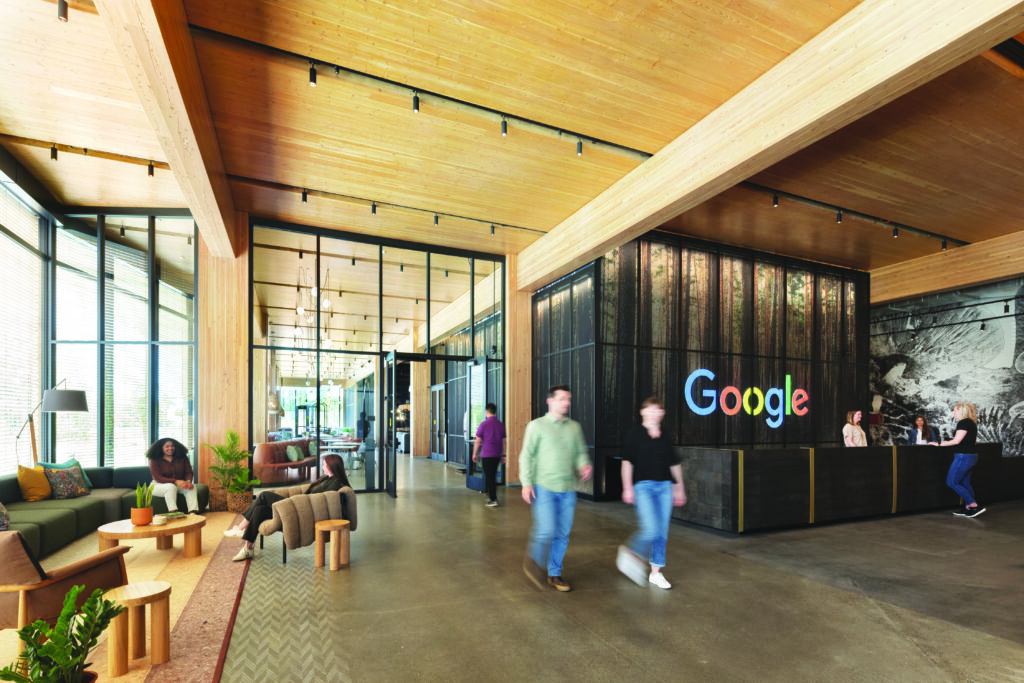
Photo courtesy of: Ema Peter
What Has Changed
Codes have caught up with reality in recent years. “CLT was added to the IBC [International Building Code] in 2015. Then in the 2021 version of the code, a lot of new mass timber stuff came in,” says Lisinski.
Setterlund says that “there are now whole sections for glulam and CLT, and all the common connectors used with those materials. The IBC is now really good at giving engineers — even an engineer who’s never designed with mass timber before — the information needed to design a mass timber building to code.”
These changes have resulted from a lot of testing. “Through testing, we kept expanding how mass timber could be used,” Lisinski says. In the 2024 code, this testing has led to changes in encapsulation requirements, which specify how much of the mass timber must be covered with a fire-resistant topping — usually gypsum board — and how much of it can be left exposed.
The IBC classifies MT buildings into three Types with the following encapsulation requirements:
- IV-A: The tallest buildings, up to 18 stories or 270 feet tall. All MT must be covered with at least two, and sometimes three, layers of gypsum.
- IV-B: Up to 12 stories or 180 feet tall. Most MT will be covered with one or two layers of gypsum, but it can be exposed on either the ceilings or the walls, or a combination of those.
- IV-C: Up to nine stories and 85 feet tall. Nearly all MT can be exposed, except for exit shafts, elevator shafts, the exterior sides of exterior walls and the inside of concealed spaces — such as mechanical chases or shafts, soffits, plenums, or the space above a suspended ceiling.
Typically, firewalls in MT buildings must be built from non-combustible materials, such as steel, concrete, or masonry, Lisinski explains.
Lisinski also explains a change in the 2024 codes that clarifies when the fire-resistant topping needs to be installed. During construction, it needs to be installed four stories below the level being worked on, so if a crew is working on the seventh floor, the gypsum needs to be installed on the first, second and third floors.
The exception is non-combustible floor toppings. “The 2024 code clarifies that the topping isn’t required until the building is complete,” says Lisinski. Floor toppings had been getting damaged during construction and had to be replaced at a significant extra cost. When updating this requirement, the nature of the fire hazard was considered. “Fire burns up, not down,” says Lisinski. “The underside of each floor is protected, and it doesn’t also need protection on the top side.”
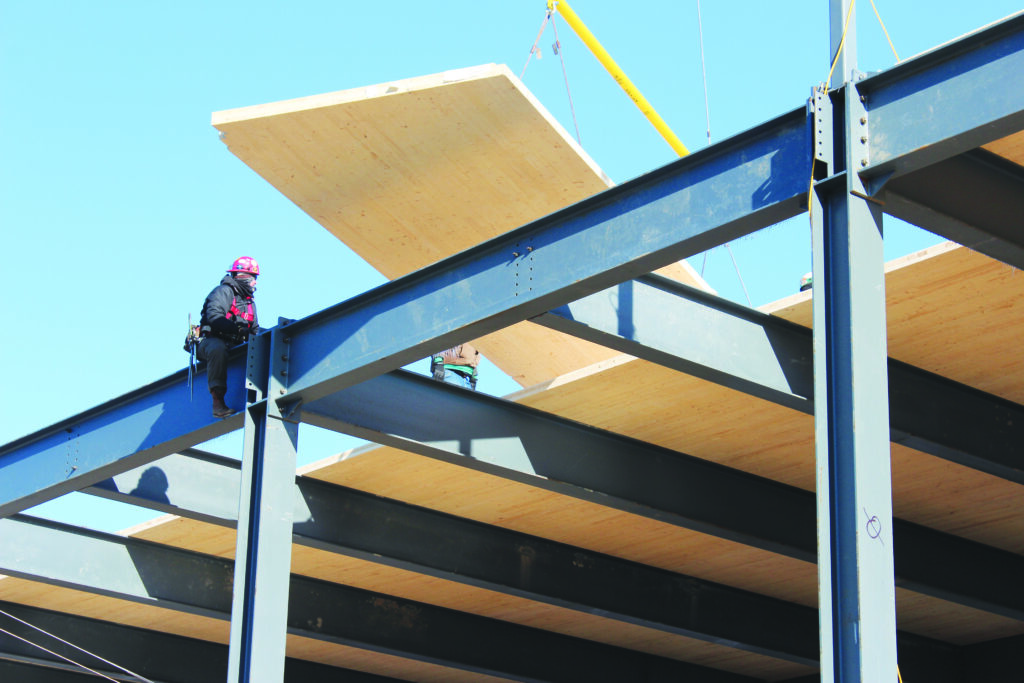
Photo courtesy of: AWC
How Codes Get Changed
As mentioned above, code changes are based on testing. “Each manufacturer will put every single size of mass timber they produce through an independent testing facility,” Setterlund says. “So, we’ll know exactly what load capacity a beam of specific dimensions will have, or how much of a char layer a column will get. The building codes are, in part, based on test data provided by suppliers.” Mock-ups of whole buildings can also go through fire or seismic testing to inform the codes.
There’s also an alternative mechanism that can allow a specific project to exceed the code’s limits. It’s called the Alternative Means and Materials process, and it “allows buildings to be constructed differently from the code specifications, so long as the alternatives can be demonstrated to meet or exceed the same structural and safety standards,” Lisinski explains. For example, “You might have research showing that a little more mass timber can be exposed if you upgrade the sprinkler system to compensate.”
One example is the Ascent tower in Milwaukee, Wisconsin where Lisinski is based. It’s the world’s tallest MT building and was completed in 2022. Although at 25 stories tall it exceeds the 18-story limit for Type IV-A buildings, the Alternative Means and Materials process allowed it to go higher. “There were compensations in that building, which allowed for the additional height and satisfied the local building and fire officials,” Lisinski explains.
The Alternative Means and Materials process can also help architects, engineers and manufacturers advocate for code changes. The downside of this route is that it can extend the code change process, Lisinski says. If pursuing this route, he advises “engaging with building officials and fire officials early and answering all of their questions. This usually will alleviate any surprises at the end.”
The AWC has completed a guide for building officials in Florida on this issue. “Building officials in Florida can use it to make sure all fire and safety regulations are being addressed by [Alternative Means and Materials] proposals,” says Lisinski. They are also working on a guide to help other states and jurisdictions.
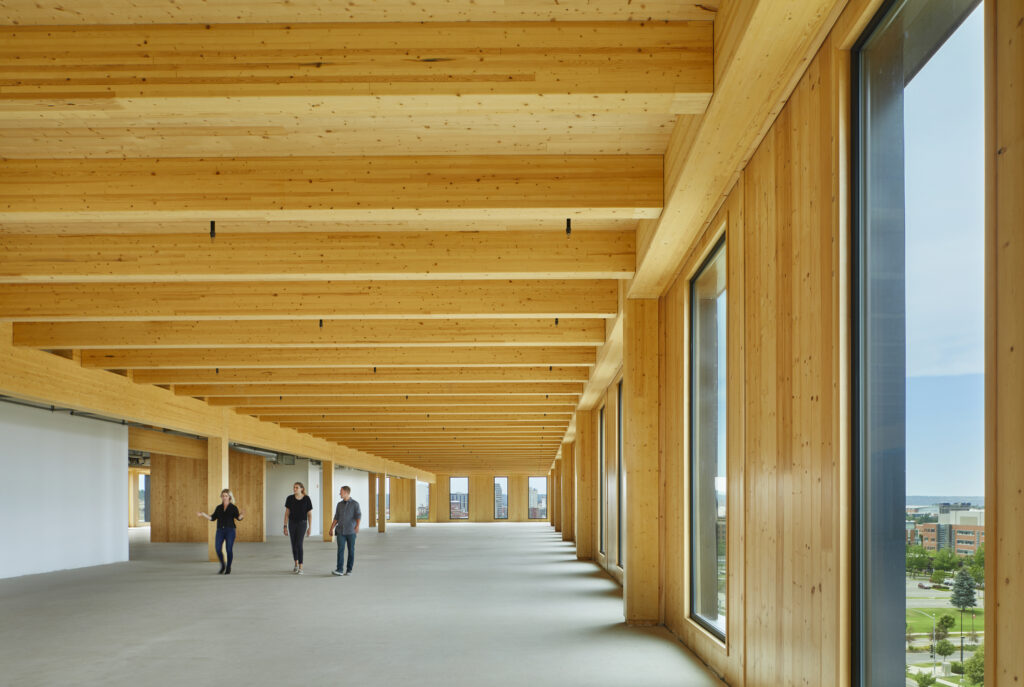
Photo courtesy of: Benjamin Benschneider
What’s Next?
“Codes are always evolving,” Lisinski says. He gives an example from the 2024 code. “Any time a mass timber element meets another mass timber element, or any other structural element, a sealant or adhesive is needed to prevent hot gases seeping through the gap.” This makes sense when, say, a wall meets a ceiling and a sealant would prevent hot gases from seeping into the next room.
However, there are places in which this requirement doesn’t make sense. For example, suppose MT beams are supporting a MT ceiling and the space beneath is wide open. In that case, it’s pointless to put sealant where the beams and the ceiling meet because any hot gases would be swirling all around in the space in a fire anyway. Furthermore, Lisinski says, “If you’ve installed a fire resistive joint system, adding additional adhesives or sealants can actually make that joint system not work properly.”
That detail may be changed in the 2027 code.
Zena Ryder writes about construction and robotics for businesses, magazines, and websites. Find her at zenafreelancewriter.com.
Note: This article is not meant as code advice but is for informational purposes only. Consult the code and your local code official for the relevant requirements.