How applying Lean and DMAIC principles brought super-rapid results to a modular factory.
- A Kaizen Blitz is a short-term assault on a particular problem or process, with the goal of getting immediate results.
- The author describes how he orchestrated two-day Blitzes for each of the factory’s sub-processes.
- He details the specific improvements that were realized as a result of these efforts.
Imagine stepping onto the factory floor of a modular construction company, one tasked with delivering faster, more affordable housing solutions. Instead of a streamlined, efficient operation, you encounter bottlenecks at every turn. Workers wait idly for materials, tools are scattered without organization and delays pile up as each task waits for the next. The entire operation feels a step behind, far from its goal of becoming efficient and productive.
This was the challenge facing one of my clients. Despite skilled workers, advanced equipment and a growing demand for their modular units, they were bogged down by inefficiencies that sapped productivity and jeopardized the bottom line. It was clear they needed to make changes — quickly.
Challenges like these aren’t unique. Across the modular industry, companies are scaling up to meet global housing demands, but often face common bottlenecks. Modular construction promises a faster, more scalable way to build, yet hidden wastes can significantly hinder these promises. When delays impact the production line, even minor inefficiencies compound into significant losses of time, money and output.
This is where Lean manufacturing principles and the DMAIC framework can be transformative. Lean focuses on eliminating waste, while DMAIC — Define, Measure, Analyze, Improve and Control — provides a structured approach for tackling inefficiencies. Together, they offer a roadmap for transforming sluggish production into efficient, high-performing operations.
The best part? These improvements don’t require massive overhauls. As I discovered in this engagement, substantial change can happen quickly with the right focus and tools.
Modular Manufacturing Challenge
When I arrived at the factory, the bottlenecks were evident right away.
And as I walked through the factory, I noticed signs of what I call “The 9 Offsite Wastes.” These consist of inefficiencies in the following areas:
- Planning
- Transportation
- Preparation
- Tool Administration
- Movement
- Inspection
- Cleaning
- Waiting
- Rework
Each waste type added unnecessary time to the production cycle. In one area, for instance, workers spent too much time transporting materials across the floor, highlighting a Transportation waste. In another, they frequently searched for tools, a clear example of Tool Administration waste. Every step of the process took longer than necessary because these inefficiencies had not been addressed.
It was clear to me that tackling these issues would require a focused, methodical approach.
Focused Application of Lean and DMAIC
To address the challenges faced in the factory, we adopted a focused two-day Kaizen “blitz” for each subprocess, leveraging Lean and DMAIC principles.
Kaizen is a Japanese term that means “change for the better” or “continuous improvement.” A blitz is just what it sounds like: a quickly executed attack. A Kaizen blitz is an intensive attack on a specific problem, with the goal of improving the entire process as well as solving the specific problem.
In this case the goal of the blitz strategy was clear: eliminate waste, reduce cycle times and integrate lasting improvements into the factory’s day-to-day operations.
Day 1: Observation and Analysis
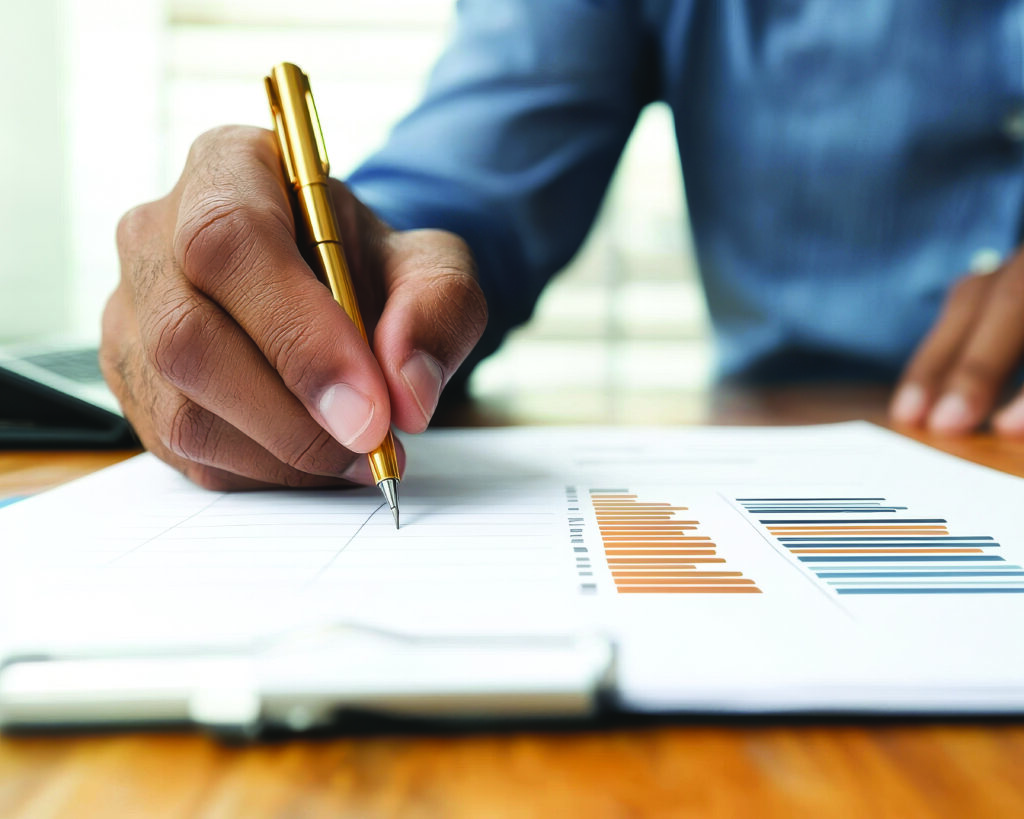
On the first day, I focused on observing each subprocess directly on the factory floor, using only a stopwatch, a set of questions and an eye for inefficiencies. I timed the steps involved in each subprocess, asked workers about their routines, and noted areas where delays and bottlenecks occurred. Armed with this real-time data, I gathered the area manager and team leads to discuss the findings.
We analyzed the wastes I observed — like unnecessary movement or poor tool setup — and discussed potential root causes. We drilled down into the issues using Lean tools such as The 5 Whys (see box). By the end of the day, we had brainstormed high-impact solutions and outlined an implementation plan for Day 2.
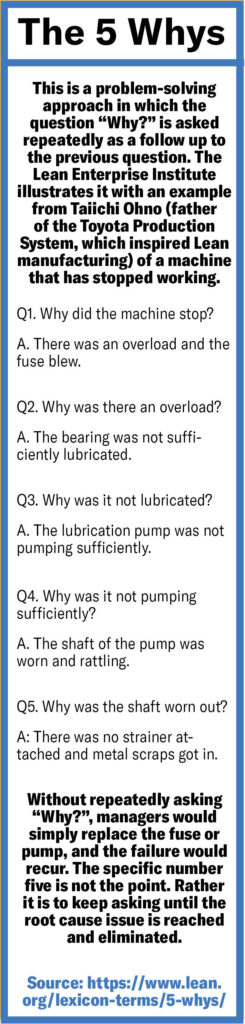
Day 2: Implementation and Validation
On Day 2, we moved into action. The first step was to prepare the necessary tools and materials for the changes we had decided upon. Next, I trained the crews on the updated procedures, ensuring that everyone understood the new process and their roles within it.
As the crews put the new processes into action, I carefully observed the revised subprocesses and took post-implementation cycle time measurements. These new measurements allowed us to validate the improvements, showing how much time had been shaved off each task. The reductions were clear and measurable, with crews adapting quickly to the more streamlined methods.
Once the improvements were confirmed, I developed Standard Operating Procedures (SOPs) to document the new processes. These updated SOPs provided the factory with a framework for maintaining control over the subprocesses and ensuring that the efficiency gains would be sustained.
Faster Throughput
The results from our Kaizen blitzes were immediate and substantial. By concentrating on the most significant sources of waste, we achieved measurable cycle time reductions across various subprocesses.
For instance, one of the most time-intensive areas — the gluing process — saw its cycle time reduced from 65 minutes to just 21 minutes, reflecting a 68% improvement. This was accomplished by refining the workflow to support parallel tasks and eliminating non-essential steps that previously hindered progress.
Similarly, we overhauled the electrical wiring process, initially bogged down by idle time as workers waited for materials or an electrician’s availability. By cross-training other team members to handle simpler wiring tasks, we cut this cycle time from 35 minutes to 13 minutes — a 63% improvement. These improvements weren’t just isolated wins; they contributed to a smoother, more efficient production flow, allowing the factory to boost throughput without increasing labor or equipment costs.
The cumulative effect of these cycle time reductions transformed the entire production line. By shortening each task, we created a more fluid process, increasing overall throughput and enabling the factory to meet higher demand.
Moreover, the changes empowered the workforce by eliminating unnecessary tasks and reducing idle time. Workers were more engaged and productive, as they had the tools and processes needed to perform their jobs more effectively. When employees experience firsthand how Lean principles make their jobs easier, they are more likely to support continuous improvement, helping sustain the gains over time.
Scaling Across the Factory
The success of these Kaizen blitzes shows how Lean and DMAIC principles can very quickly transform productivity in modular construction. The 9 Offsite Wastes — Planning, Transportation, Preparation, Tool Administration, Movement, Inspection, Cleaning, Waiting and Rework — are common challenges that affect all modular construction factories. By systematically identifying and eliminating these wastes, any modular facility can streamline operations, reduce costs and significantly boost throughput.
While scaling across multiple facilities isn’t always relevant for modular companies, the beauty of Lean principles lies in their adaptability within individual factories. The methods applied in one part of a facility can be applied across other sections or processes to achieve similar benefits. For instance, reducing tool administration waste in a framing area can inspire similar improvements in other parts of the production line, like electrical wiring or interior finishing. This allows a company to maximize gains and establish a cohesive approach to efficiency across all production stages.
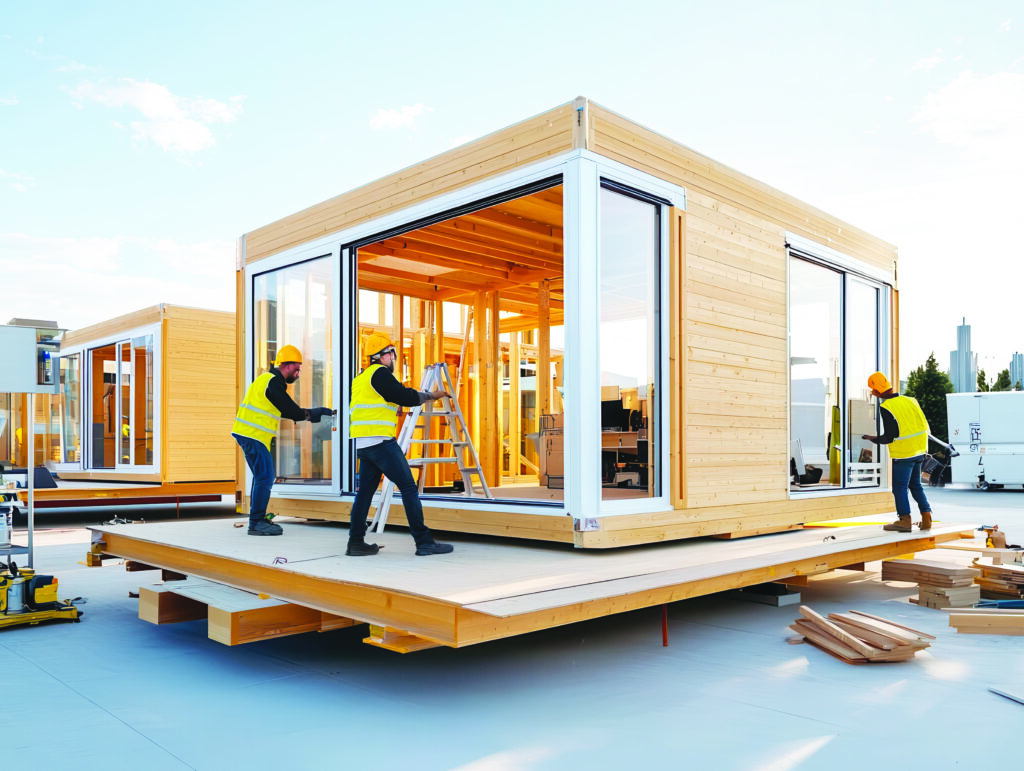
Additionally, Lean and DMAIC principles help factories adapt more effectively to fluctuating demand. In modular construction, where demand can shift rapidly based on market trends or specific project requirements, a Lean operation can scale output up or down without losing efficiency. This makes it easier to respond to changes in the market without overhauling processes or hiring additional staff.
Lean principles also contribute to higher quality across the board. By reducing errors, rework and unnecessary handling, Lean helps ensure that every module meets high standards. For modular construction companies, building a reputation for consistently high-quality units can be a major competitive advantage, especially when each factory serves a distinct region or market.
Financial and Operational Efficiencies
Lean and DMAIC principles directly translate into financial and operational benefits, making them indispensable tools for modular factories. By reducing inefficiencies, factories can accelerate production cycles, thereby lowering labor costs and allowing teams to accomplish more within the same timeframe. Streamlined operations also minimize costly rework and unnecessary resource use, freeing up capital for other investments.
Moreover, by cutting down cycle times, Lean principles enable factories to meet tight deadlines and improve overall throughput. Faster project completion means that factories can take on additional jobs, improving revenue potential without the need for significant increases in staffing or equipment. This kind of scalability is essential for modular construction, where demand can fluctuate based on market needs.
For modular factories, one of the most immediate and tangible benefits of Lean improvements is in waste reduction. Waste elimination not only cuts costs, but also leads to smoother operations with fewer bottlenecks.
The focus on continuous improvement helps ensure that even minor issues are addressed promptly, preventing them from escalating into costly delays. Factories that adopt Lean become more agile and responsive, with the ability to adapt quickly to changing requirements and maximize productivity.
In an industry where margins can be tight, these financial and operational efficiencies are game changers. Modular factories that embrace Lean are better equipped to handle the demands of the market, delivering high-quality projects on time and on budget.
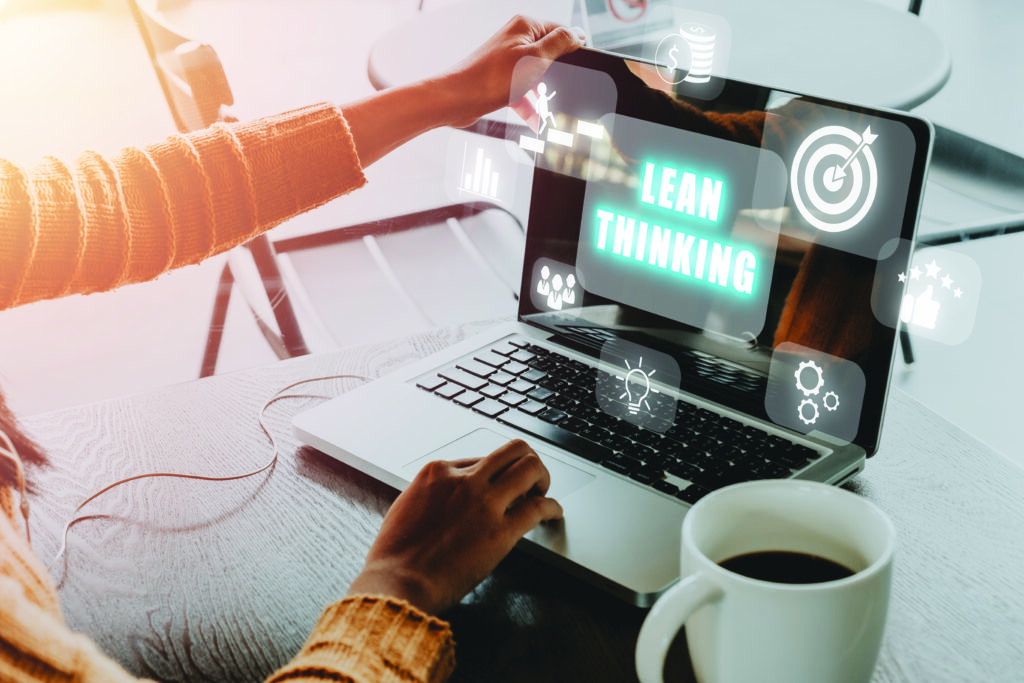
Lean is a Way of Thinking
The modular construction industry stands at a pivotal moment. With demand for fast, affordable housing and other buildings increasing, modular factories must evolve to produce more units efficiently, with fewer resources.
Our Kaizen blitzes show that meaningful improvements can be achieved in days, not months. By applying Lean and DMAIC principles, we transformed a production line weighed down by inefficiencies into a streamlined operation capable of meeting ambitious production targets.
What makes Lean particularly powerful is that it’s not just a one-time project — it’s a mindset of continuous improvement. By updating standard operating procedures (SOPs) and embedding Lean practices into daily operations, companies can foster a culture that prioritizes efficiency and adaptability. This foundation enables factories to not only meet today’s demands, but also to stay prepared for tomorrow’s challenges.
Embracing Lean, eliminating waste and maximizing throughput will position your operation as a leader in the industry, ready to set new standards for speed, cost-effectiveness and quality. That’s because Lean is more than a methodology; it’s a path to sustained operational excellence. The question is, are you ready to take it?
Daniel Small is a Denver, Colo.-based management consultant to the offsite construction industry. He specializes in Lean Construction and Manufacturing and Six Sigma methodologies. For assistance with improving your offsite manufacturing process, contact him at 719-321-1953 or [email protected] or visit www.LeanOffsite.com