This fast-growing startup uses panels made from a new type of material as the basis for affordable modular homes.
Vantem, a North Carolina-based manufacturer of affordable, energy-efficient modular homes, intends to build 15 factories across the United States over the next seven years. But they won’t be making the same modules that most others make. Vantem has developed a unique building system.
The core of their system is a structural insulated panel (SIP) made from a proprietary cementitious material in the ceramic family. The material is similar to that used for the nose of a space shuttle.
CEO Chris Anderson says the company has traveled a long road to get to this point.
Better Building
Anderson co-founded his first entrepreneurial endeavor, SIMEX International, in 1993. The company manufactured construction products such as windows, doors and flooring made from sustainably-harvested hardwoods and its customers included big names like The Home Depot and Lowes. By the time Anderson sold the company in 2007, it had 2000 employees, 90% of whom were plant workers.
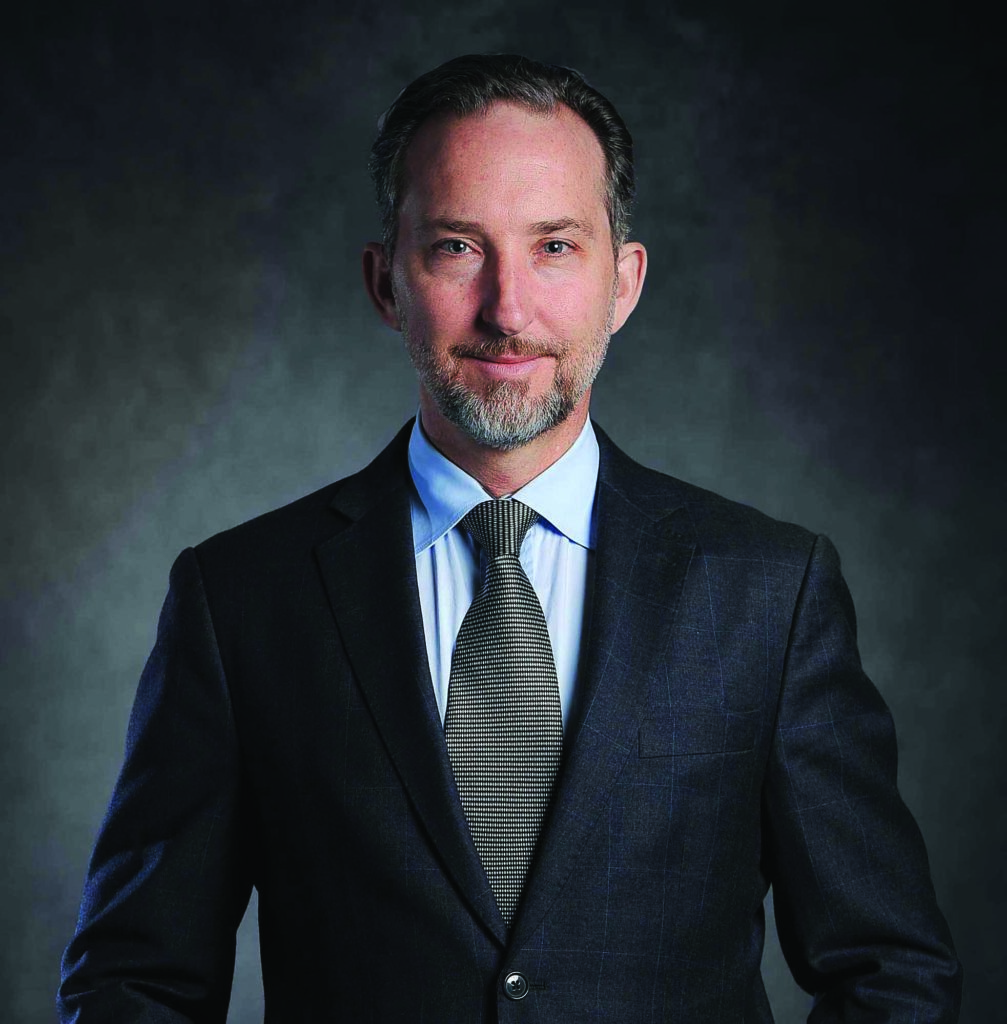
Despite the fantastic success of SIMEX, something about the experience didn’t sit right with Anderson. “We used computerized equipment to make exacting products [produced to tolerances of a thousandth of an inch]. But when we visited jobsites, we saw that the homes our products were being put into were being built using hundred-year-old methods. The structures were very imprecise, with openings that were off by inches.”
He concluded that there had to be a more modern way to build. This frustration sparked the entrepreneur in him, which led to the creation of Vantem.
Another driving factor was Anderson’s interest in sustainability and the environment. SIMEX’s products were produced from sustainably-harvested wood.
His ecological commitment developed during his formative years growing up in Bolivia on the edge of the Amazon. “As I got older, I could see the impact of deforestation and I feel a deep connection with the environment.” He says that connection is what drives him.
New Factories
In 1986, Anderson came to the US to attend Park College in Parkville, Missouri. After graduation, he went on to the University of South Carolina to earn a Masters’s degree in International Studies.
When developing Vantem in 2008, Anderson decided that it was not a good time to start operations in the US, given the housing crash. So he returned to his South American roots where he has a broad network. The company’s main facilities were established in Uruguay, but they set up operations in other countries as well.

For its first two years (2008-2010), Vantem focused its time and money on robust lab testing to get certification and code approval in countries throughout South America. Since 2015, after completing some demonstration products and getting the necessary approvals, Vantem has built three million square feet of housing and schools in Uruguay, Brazil, Bolivia, Chile, Colombia and the Caribbean.
In 2021, Vantem began lab testing for code approvals in the United States. “When you build with a new material, you need to have reliable information about its structural characteristics, acoustics, fire rating, etc.,” Anderson notes. The company completed this testing in early 2022. The system complies with all the IBC and IRC code requirements, which are documented by the International Code Council.
Vantem’s US operations will focus exclusively on affordable housing. The focus is due to the huge shortfall of housing the country is facing. “We see an opportunity to build in an important sector and make a difference by creating units that are energy efficient in a market that is barely keeping up with standard growth,” Anderson says. He says the company’s homes can usually be built for 20% less than traditional construction.
The company’s first US-based factory will be in the Dakotas. The exact location has yet to be determined (they are in discussions with various local authorities), but when complete it will serve those states as well as Minnesota.

Vantem plans to open two factories—the Dakota factory and a second factory in Arizona—in 2023. After that, they hope to open factories in Texas and Florida, then move on to other states. Once all 15 factories are up and running, Anderson is confident that Vantem will be able to cover most of the US. Every factory will have the capacity to build one million square feet per year.
Each factory is being developed with local partners and Vantem has already secured financial commitments for the first two. “We look for strong developers in each market and put a factory in their market to produce the homes that they sell and have in their project pipeline,” Anderson says. Ownership of the factory is split 50/50.
To simplify production and reduce costs, Vantem uses an assembly line system that Anderson says incorporates lessons from the auto industry. First, they make the panels; then they assemble the panels into modules. The same system will be used in each factory. Replacing traditional materials— framing and drywall, for instance—with one light structural panel, lowers product costs and simplifies the manufacturing process.
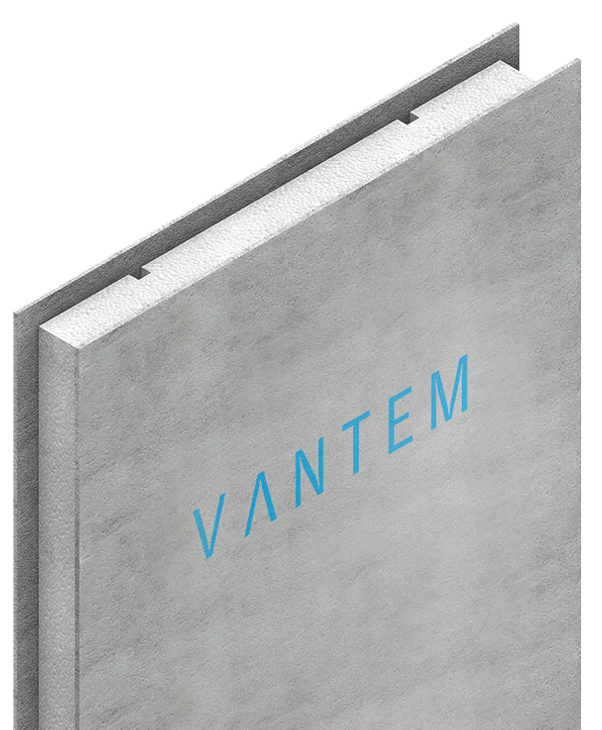
Like other SIPs, Vantem’s panel is a sandwich made from foam insulation and two structural skins, which creates an extremely efficient thermal envelope. Panels are assembled with a special glue and can be used for the walls, floors and roofs of its modules.
Attracting Investors
Vantem’s innovative approach is proving attractive to developers and investors. “Because we can develop our product for less cost and require less investment to make it, we can go to developers and pass along lower costs and get them a better return on investment,” Anderson says.
When Anderson first founded the company, he worked with TEM Capital, which is partly how he came up with the company’s name. Since then, the team has brought on other investors, “who see the potential of what we are doing.” Among the new investors is Breakthrough Energy Ventures, which was founded by Bill Gates.
With capital secured, there is one more challenge that Vantem and the industry as a whole face – attracting talent. However, this is proving less of a challenge than it could be. The simplicity of the product and the streamlined manufacturing system means that Vantem’s facilities require less labor than a conventional modular plant.
Looking to the future, Anderson is bullish not just about Vantem, but also about offsite manufacturing as a whole. “It’s a small share of the housing market now, but it will increase dramatically with time, as people find ways to make it scalable,” he says. He and Vantem are doing their part and are excited to continue to do their part to meet the needs of the housing market in the US and overseas.