This Pacific Northwest company says that offsite is a natural for sustainable development.
- Green Canopy NODE is making and selling CLT modules and flat pack framing kits. Current kits are designed for multifamily construction, but a single-family version is in the works.
- The company also makes a prefabricated utility wall. They use it for their modular and kit homes, as well as selling it to other builders.
- The prototypes they have built have been tested and certified to have low air leakage and to be 20% to 30% more efficient than typical homes.
Green Canopy NODE is based in Seattle, Washington and Portland, Oregon. The company’s predecessor, Green Canopy Homes, was founded in 2010. That company started out doing deep energy retrofits on existing housing stock, but then transitioned to new construction in 2014, building all-electric homes for clients focused on sustainable construction. By 2021, they had built and sold more than 270 homes.
In 2021, the company merged with NODE, a construction technology company. Now, the integrated company does real estate development (including general contracting), real estate fund management, construction technology and manufacturing.
Although Green Canopy NODE continues to use conventional construction on some of its projects, they’re mostly focused on a new direction — selling prefabricated Integrated Building Kits and Utility Kits. Their building kits can be flat packed or delivered as volumetric modules, depending on site accessibility.
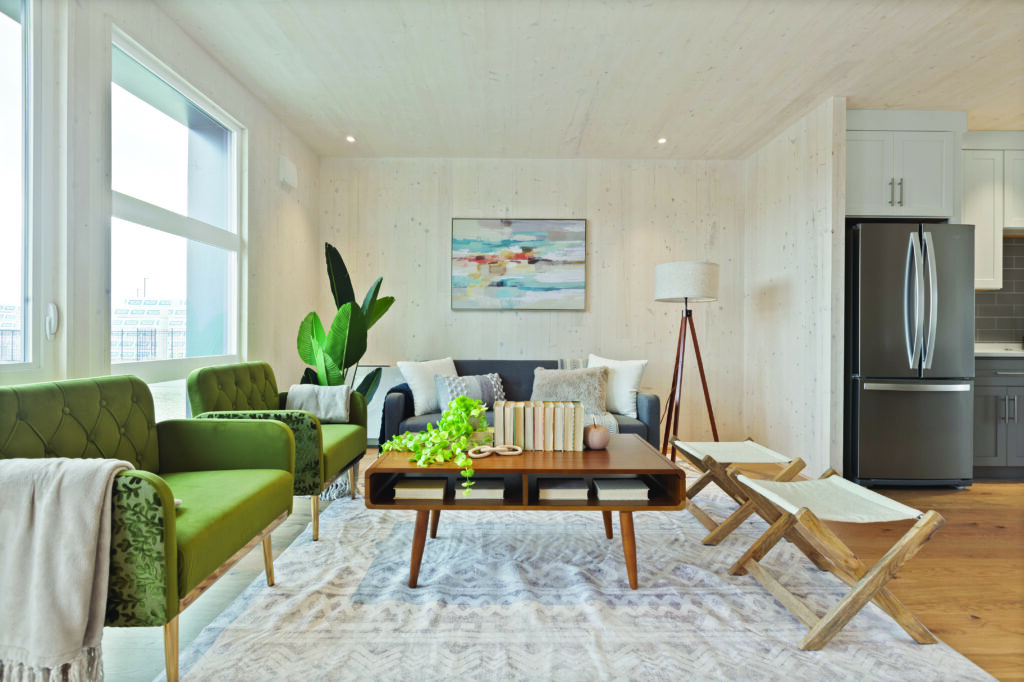
CLT Modular Prototype
In March 2023, the company completed a prototype build of a volumetric modular home in Spokane, Wash. The next iteration will be built in Portland, Ore. The modules were manufactured from CLT, or cross-laminated timber.
Green Canopy NODE’s Spokane prototype has two stories, 1,200 sq. ft. of floor space, two bedrooms, 1.5 bathrooms and a rooftop deck. The interior surfaces of the CLT modules are left exposed. “When you walk into the prototype home, it feels like you’re in nature,” says Mark Grismer, Construction Project Manager. “And eliminating the steps of screwing on drywall and painting over it significantly reduces the on-site construction timeline. It also eliminates the on-site waste typically generated by drywall installation.”
The Spokane prototype home uses both mineral wool and wood fiber insulation on the exterior of the CLT. The cladding is a rain screen system that was installed on-site. The next model home will have even more work completed off-site — including installation of the utility kits, exterior finishes and many interior finishes.
The Integrated Building Kits consist of CLT modules or flat-packed panels, utility walls and a raised flooring system for MEP components. “Our prototype model home was designed for multifamily scenarios. Modules can be placed side by side for rowhouses, or stacked vertically for multifamily apartment applications,” says Grismer.
The Kits are designed to be used in multifamily residential buildings from one to seven stories, from cottages to apartments. In addition, a single-family kit will be released later this year. Grismer says the kits will be similar in cost to their stick-built projects — but will be 44% faster to complete.
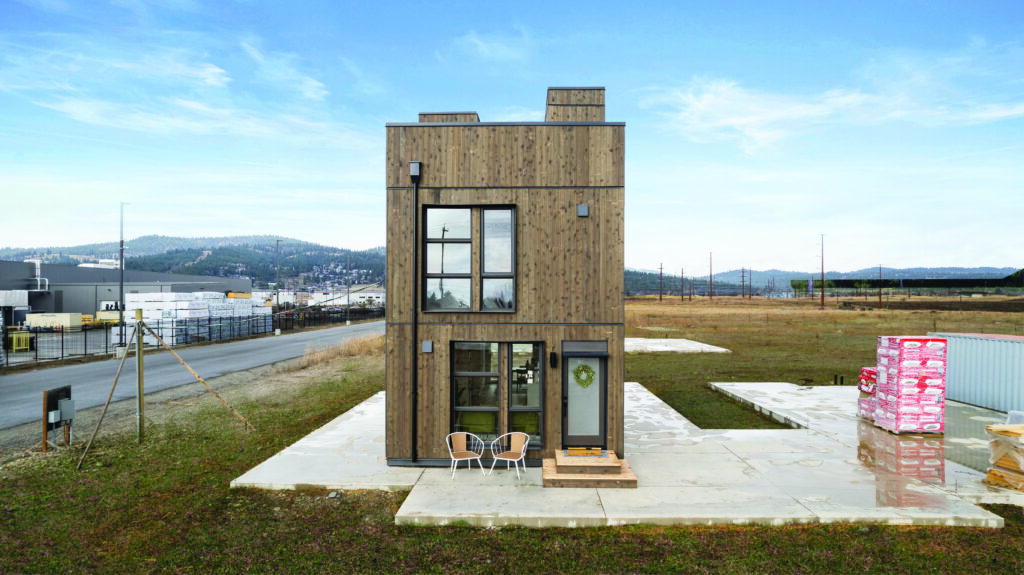
Utility Walls
The company also manufactures utility wall panels with integrated plumbing, HVAC and electrical components. The utility panels form part of Green Canopy NODE’s complete building kit, but they can be used with other manufacturers’ modules, and modular manufacturers can also incorporate them into their own modules.
The panels can even be purchased by developers and builders to install into otherwise conventionally built projects. “Fourteen of them are about to be installed in townhomes in the Grow Community on Bainbridge Island (Wash.),” Grismer says. The Grow Community is an urban net zero development, and the townhomes are the final phase of the project.
Grismer explains that in a single-family home, “Our utility wall would typically be in a mechanical room. On one side would be the mechanical equipment for the systems of the home. The other side might be a bathroom or kitchen. Any other utility walls would be stacked above the first one.”
When the utility walls are used in a multifamily building with multiple modules, “they reduce the number of connections you have to make when installing the modules, which makes installation faster. They also reduce the number of long runs needed in a building, which increases efficiency and reduces the amount of materials needed.”
Energy Savings
All the homes Green Canopy NODE builds are above required energy code. “In Seattle, our homes are third-party certified by Built Green. In Portland, we’re certified by Earth Advantage. In fact, every home we’ve built in Portland has been certified Platinum by Earth Advantage, which is the highest energy efficiency level.” He says the company’s homes are 20% to 30% more energy efficient than ordinary homes built to code.
Energy Trust is a non-profit organization that helps people in Oregon and Southwest Washington reduce housing costs by saving energy. They test new homes and provide an Energy Performance Score (EPS). The EPS allows consumers to compare how similarly sized homes use energy, and to estimate their utility costs before they buy a home. Scores range from 0 (the best) to 200+. As an example, a 2,171 sq. ft. home built by Green Canopy NODE in Portland, Oregon in 2020, received a score of 47; the same home built to code would score 94.
The organization estimated that the average energy cost in the Green Canopy NODE home (which is all for electricity) per month would be $79. For comparison, by extrapolating from data on the US Energy Information Administration’s website, the average monthly energy costs for a 2,000 sq. ft. home in Oregon in 2020 was about $162.
Although the prototype home has had various sensors installed in it, it’s very new and it will be a while before any meaningful data analysis can happen. However, a blower door test was conducted on it during construction, before the the exterior insulation was installed.
The results are in terms of ACH, or air changes per hour. (The official metric is ACH50, which indicates the test was conducted at a pressure of 50 Pascals, the industry standard.) A lower ACH number is better, indicating fewer air leaks and lower energy use. The prototype scored 0.8 ACH, and in future iterations the company aims to get that down to about 0.5 ACH, using passive house principles.
For comparison, Washington’s current (2018) residential energy code requires no higher than 5 ACH for new construction. Oregon’s current (2021) residential energy code requires no higher than 3 ACH for new construction.
Of course, most older homes are even more leaky. According to a report published by the US Department of Energy in November 2022, nearly 70% of residential building stock in the United States was built before 1992, when the Building Energy Codes Program was established. And, of those pre-energy code houses, nearly half have little to no insulation in the walls and have very high air leakage rates of 10 ACH or more.
In Canada, a 2020 research paper in the Journal of Building Engineering reports that more than 900,000 single-family homes had an average airtightness of 5.7 ACH, with older homes generally being more leaky than newer ones.
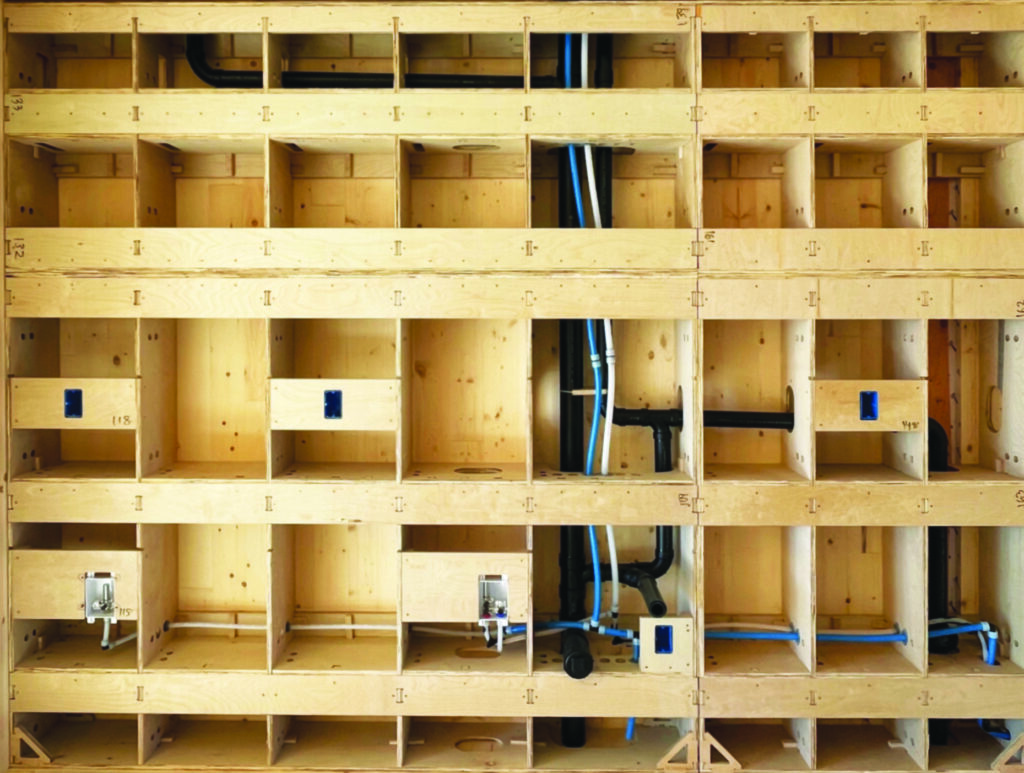
efficient connections.
Is it Affordable?
As well as lowering residents’ energy costs, Green Canopy NODE also insists that sustainable homes should be more affordable for more people. That’s a challenge, given today’s high construction costs.
Green Canopy Homes, the company’s predecessor, says that 16.1% of the homes it delivered were “at affordable price points.” However, by affordable they mean less than $500,000. While that may be a bargain when compared to other homes in the area, it’s still more than what many families can afford.
To be fair, Green Canopy NODE is working with partners to try to deliver more affordable housing in the region they serve. These partners include community land trusts, churches, non-profit organizations and the Washington State Housing Finance Commission.
One upcoming affordable housing project is a 17-unit multifamily development that Green Canopy NODE designed. It’s slated to break ground in Seattle during the spring or summer of 2023. They’re partnering with Habitat for Humanity on this project, which will have one and two-bedroom units to be sold to households making at or below 80% area median income.