We look at the misconceptions some builders have about prefabricated components, and how to handle and install them the right way.
- Trusses and other components are code compliant and more adaptable than a lot of builders realize. However, some decisions can’t be reversed.
- Cost comparisons to stick framing are only meaningful if you look at whole costs: including the cost of labor used on the jobsite, the amount of waste generated and comparative construction schedules.
- With panels, more care must be taken when forming and pouring foundations. In addition, trusses must be properly braced for structural and worker safety.
Despite roof trusses being commonplace in otherwise stick-built homes, misconceptions about them and other prefabricated structural components persist, even among builders.
To learn more about these misconceptions — as well as about the benefits and best practices when using prefab structural components — we talked with two people at the Structural Building Components Association (SBCA): Sean Shields, Director of Marketing and Jess Lohse, Executive Director.
They shared statistics that, according to Home Innovation Research Labs’ 2023 Annual Builder Practices Report on Structural Systems, 70% of single-family detached homes and 79% of multifamily units used roof trusses in 2022. The use of wall and floor panels is much less widespread. For example, in 2022, only 3% of single-family detached homes used wall panels.
Builders’ Reservations
Reservations that builders have about components have to do with change orders, code requirements, their ability to accommodate complex designs and shipping issues.
Can we make changes? According to Shields, a common misconception is that that roof trusses don’t allow changes to the floor plan after work begins, for instance when the homeowners walk through the framed space and decide they want to take out a wall to make a bigger kitchen. He points out that it’s easy for a truss manufacturer to design long-span trusses that go from one exterior load-bearing wall to the other, “so there are no load-bearing walls in the interior at all, which means they can be moved around however you like.”
However, there are decisions that do need to be locked in at a certain point, such as the location of exterior walls, doors and windows. “If a builder doesn’t like the idea of even that [level of fixed decisions], then offsite componentization is not a good fit for them. But that’s a very small part of the market.”
Do they meet code? Builders also worry about the use of components because local codes vary so much, Shields says. However, this isn’t an issue. He explains that varying codes aren’t a problem because the component manufacturer “looks at each job as a custom job that has to be designed to the local codes” that apply at the site of the building.
Can they handle complexity? Some builders who don’t normally use trusses worry that they can’t accommodate complex roof planes. Actually, the opposite is true.
“The greater the roof complexity, the more the design software for truss manufacturing shines because it makes all those things pretty easy to accomplish,” Shields says. “You could actually argue that the more complex the roof, the more efficient and cost effective it is to use trusses, instead of hand cutting and trying to figure it all out in the field.”
He notes that much of the residential construction industry is unaware of “how much advancement has occurred in the design software and the fabrication process, and how much more capable component manufacturers are than just a few years ago.”
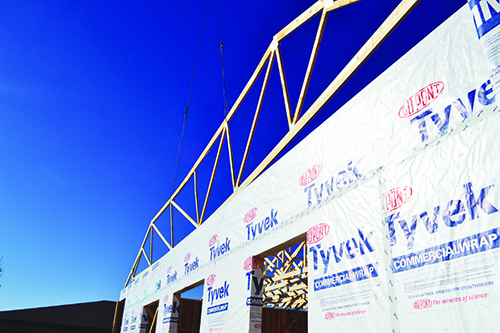
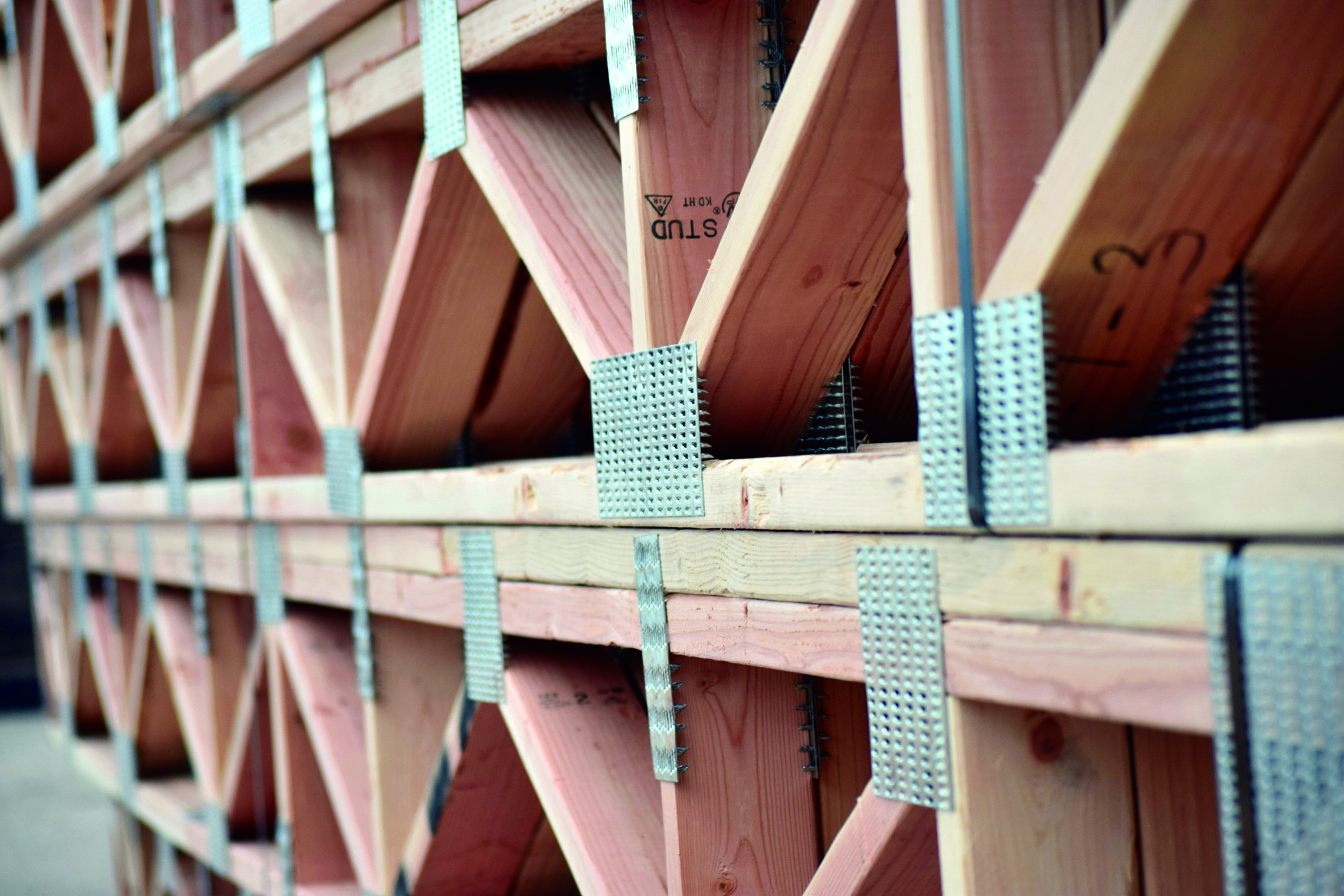
Will shipping add cost? Shields says that another common objection is that, when transporting wall and floor panels, “you’re shipping a lot of air, which builders assume isn’t cost-effective.” He says that builders who make such comments haven’t done a cost comparison that factors in the reduction in cycle time that components make possible.
“A driver and truck are less expensive than a framing crew taking three extra days to frame up a house because they’re building conventionally, rather than using wall and floor panels,” Shields says. The cost of shipping air is negligible compared to the efficiency prefab panels provide framing crews in the field.
Advantages of Components
Perhaps the main advantage of using structural components is the reduced time spent on framing compared to traditional on-site stick-built homes.
For the last two years, SBCA has participated in the Innovative Housing Showcase, hosted by the US Department of Housing and Urban Development (HUD) at the National Mall in Washington, DC. This year, it teamed up with 84 Lumber to frame a 2400 sq. ft. house in less than eight hours with components. (For more on this home, see Christine Wagner’s Op-Ed in this issue.)
SBCA also illustrated the speed of prefab components with their Framing the American Dream project. In 2015, two identical 2900 sq. ft. ranch-style houses, each with a walk-out basement, were framed side-by-side. One house was entirely stick-framed, and the other used prefab structural components including wall panels, floor panels and roof trusses. The stick-framed house took 375.5 man-hours to erect, and the one using components took 152.1.
(The Framing the American Dream project was held in 1995 as well as 2015, and the next iteration is planned for 2025.)
Framing the American Dream also illustrates Lohse’s point that, compared to stick-building, framing with components requires less on-site labor, uses less material and generates less on-site waste.
According to the SBCA website: “A crew can frame two and a half homes with structural components in the time it takes to stick frame one house.”
The stick-framed house used 20,643 board feet of lumber and EWP [engineered wood products] while the component-framed house used 15,052 board feet of lumber and EWP. That means the component-framed house used 25% less wood product.
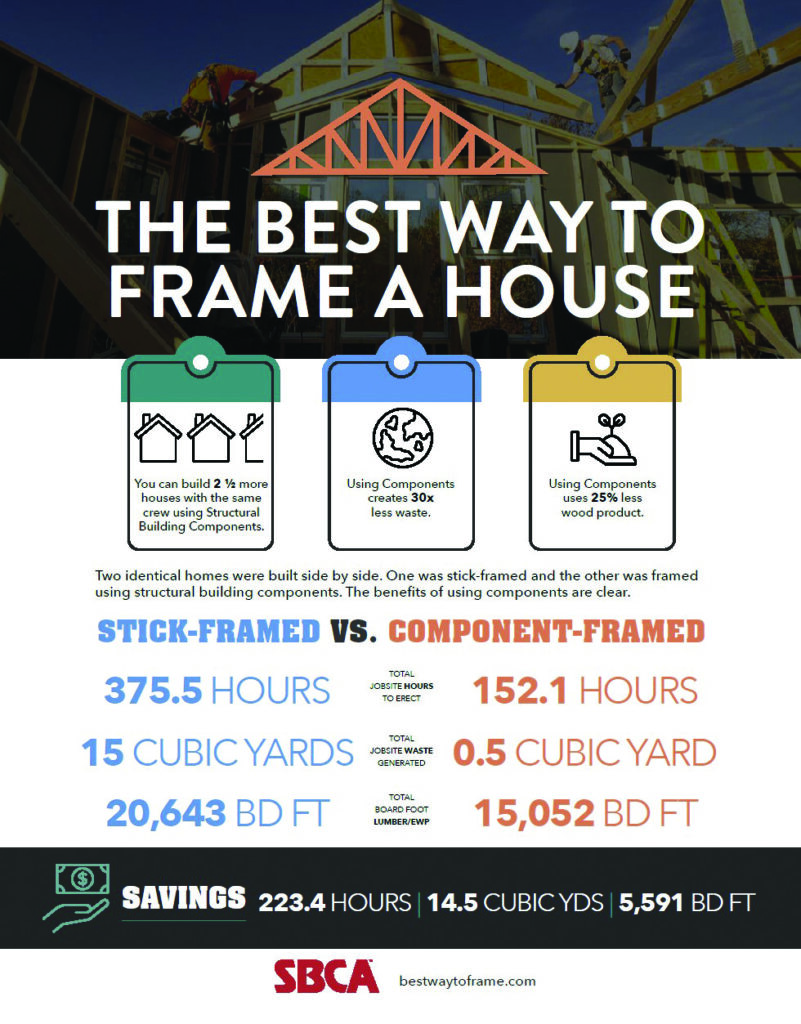
The upshot for builders of using less wood and less labor are cost savings that can be passed along to homebuyers. The following table is based on SBCA’s 2024 house at the HUD Showcase.
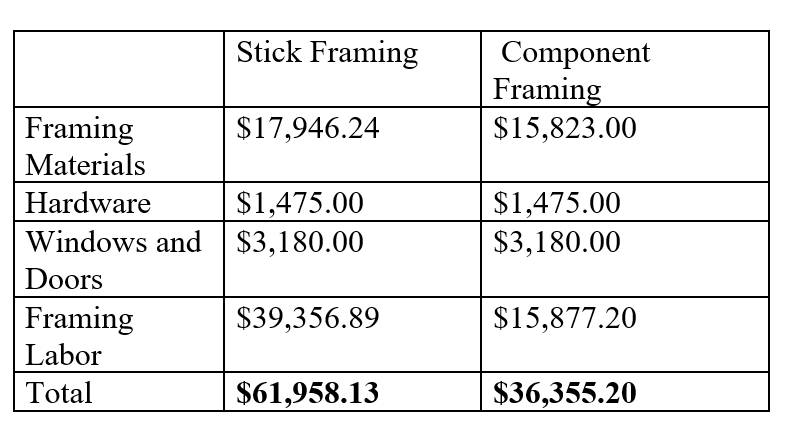
Lohse says, “You don’t see dumpsters outside of component-built homes that are full of wood and other materials.” In fact, Framing the American Dream showed that, “stick framing a house generates 30 times more jobsite waste than framing a house with structural components,” according to the SBCA website. In that comparison, the component-framed house generated half a cubic yard of jobsite waste, while the stick-framed house resulted in about 15 cubic yards (roughly 102 standard 32-gallon trash cans).
Ensuring Good Results
Perfect foundations are needed. Shields notes that wall panels are manufactured on the assumption that they’ll be set on a level foundation. When stick-framing walls, if a foundation isn’t perfectly level, he says, “You can accommodate that by cutting one piece a little shorter, cutting another a little longer, or adding a shim here, and so on. With on-site improvisation, you can make sure you have a level wall top plate for the roof trusses to rest on.” With pre-manufactured wall panels, however, it’s much harder to accommodate imperfections on-the-fly.
Good communication with the foundation contractor is a must. Any builder or framer who’s using a wall panel system must ask the foundation contractor to ensure that certain tolerances are met. “Particularly for setting exterior walls, the outside foot of the foundation really needs to be level and square,” Lohse says. These days, getting foundations level is easier than in the past. “Scanning technology can show imperfections while the concrete is still wet,” so that they can be evened out, he explains.
Furthermore, after the concrete’s cured and set, it can be scanned so the wall panel manufacturer can know the details of the surface the panels will be set on.
Careful storage and staging. Particularly with long-span trusses, a storage and staging location needs to be carefully chosen, Lohse says. If a crane will be used to lift the trusses, they should be stored and staged close enough to the building site that they need to be lifted only once — when they’re set into place.
Lifting trusses twice (or more) not only wastes time, but it also increases the chances they’ll be damaged or installed out of order or in the wrong orientation. Typically, trusses are bundled for transportation in the order they should be installed. Lifting and re-stacking can reverse (or completely disrupt) the stacking order, increasing the risk of installation mistakes.
The stacks of trusses should also be stored as flat as possible — with block installed where necessary — to minimize the risk of bending.

Use proper bracing. For success with roof trusses, “understanding the bracing requirements is critical,” Lohse says. “It’s not a linear relationship, in which a 20-ft truss requires double the bracing of a 10-ft truss. Instead, it’s an exponential curve.”
In particular, the builder must provide substantial temporary ground bracing for the first truss erected because the rest of the first set of trusses rely on that first one for stability. Similarly, after the first set of trusses are braced, the remaining sets will rely on that set for stability. Insufficient bracing can cause trusses to buckle out of plane, potentially causing damage that might not be immediately apparent. Catastrophic collapse can also occur.

It’s also important to understand the permanent lateral bracing required for the roof trusses on each building. Sheathing may not provide sufficient lateral resistance, and the builder must follow the designer’s requirements for truss stability.
The Building Code Safety Information booklet produced by SBCA warns that:
“Disregarding Permanent Individual Truss Member Restraint and Permanent Building Stability Bracing (PBSB) recommendations is a major cause of truss field performance problems and has been known to lead to collapsed roof and/or floor systems. Failure to install the proper restraint and bracing will greatly increase the probability of truss performance problems or an accident resulting in property damage, personal injury or death.”
Lohse recommends that builders pick up a copy of this booklet if they’re unfamiliar with using building components. It can be purchased on the SBCA website (www.sbcacomponents.com).
Zena Ryder writes about construction and robotics for businesses, magazines, and websites. Find her at zenafreelancewriter.com.
Images are courtesy of SBCA except where noted.