With predictive analytics, you can mitigate problems caused by delays before they happen.
- This AI technology can analyze historical and site-collected data to predict whether a project will run into scheduling problems.
- When a potential delay is identified far enough in advance, the factory or the builder can make a plan to avoid it.
- The technology is already in use by larger companies, but solutions are also available for smaller builders.
Delays in the factory and on the construction site are a notorious source of cost overruns and unmet deadlines. They can result from a multitude of factors: weather, supply chain disruptions, labor shortages, equipment failures, regulatory issues, and more.
Is it possible to predict delays before they occur? This is where AI-driven predictive analytics comes into play. Leveraging advanced data-driven techniques, predictive analytics can forecast potential delays — or issues that might cause delays — allowing for proactive mitigation and smoother project execution.
This technology is already proving itself. The construction management software systems I know if that incorporate predictive capabilities are Procore, Autodesk, Oracle, Trimble, Buildots, Dodge, Fieldwire and Merlin AI. There are likely more.
Not all systems perform the same functions, and the right solution will be different for each builder or factory depending on variables that include production, what other software or systems are currently in place, technical resources, staff and more.
Several large builders, and at least one major modular company, have incorporated this technology into their operations. But you need not be a big player to take advantage of this innovation; Merlin AI, for example, is priced so that a builder with $5 to $10 million in annual revenue can afford it.
How Predictive Analytics Works
The value of predictive analytics is that it offers a powerful way to identify potential risks in advance. By using historical data, real-time information, and sophisticated algorithms it can forecast where and when delays are most likely to happen. By making predictions early, you can implement contingency plans before problems arise.
It’s about turning data into actionable insights. The process of doing so typically involves several steps.
Data Collection. The first step is to gather relevant historical and real-time data from online and in-house sources. Data can include previous project timelines, local weather patterns, supply chain information, equipment performance records, labor availability, financial reports and even communication logs.
Queries that use this data are complicated to set up, but easy to use. A service provider (BuilderChain, for example) will typically write the query, but then the company can run it as often as needed.
Other types of data can be gathered by sensors, some of which are wearable while others are wall mounted throughout the factory. For instance, telemetry pendants (by Limitless and others) can be worn by employees and contractors and collect many types of data, from conversation to body movement to environmental data.
How is this data used in predictive modeling? Conversations between employees can reveal problems or record discussed issues, like drywall cracking. (If privacy is a concern, it’s easy to turn on and off the pendant’s voice recording feature.) Body movements can show the potential for injuries. If you notice someone lifting incorrectly, you need to correct that or soon, you will have a labor shortage for that person.
Sensors that collect electrical data (such as voltage and current) and physical data (such as temperature and pressure) can be used to monitor machines and reveal current or potential problems.
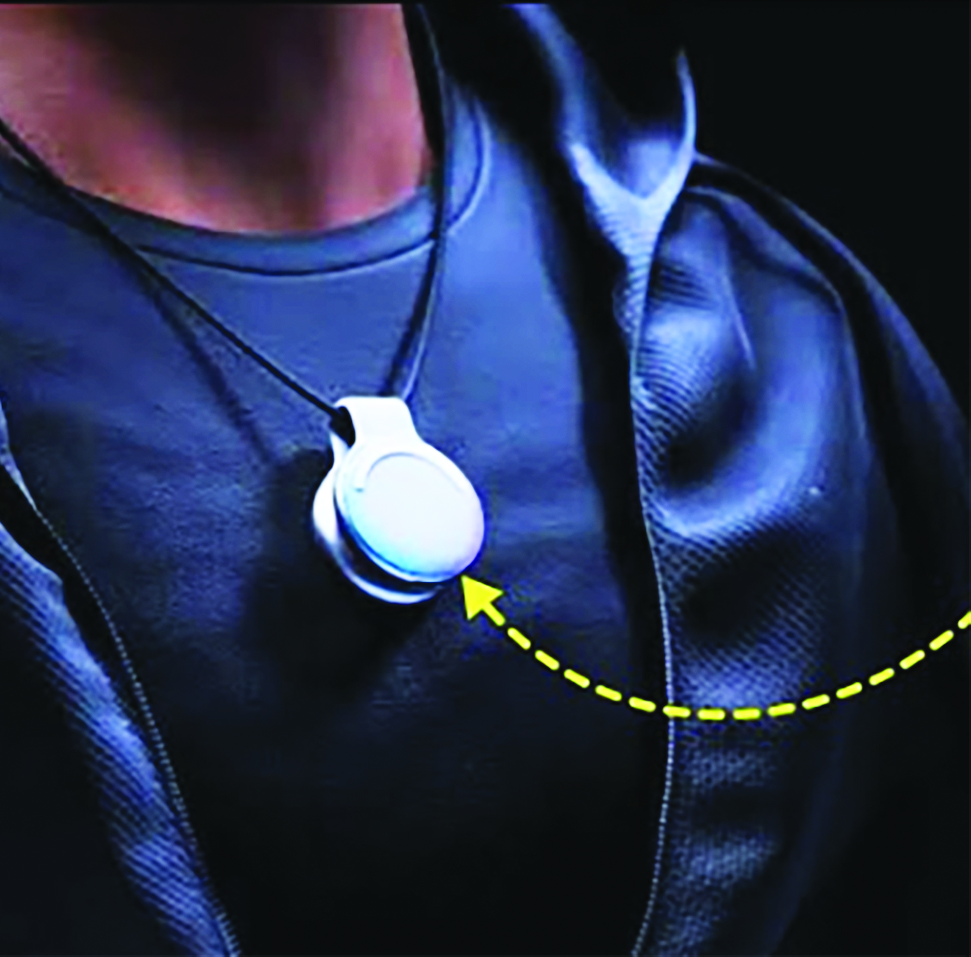
A search for “AI Wearables” returns a rapidly growing list of items, brands and uses, including smart glasses, smart gloves, smart helmets, and more. The more data the factory tracks, the better they can analyze it when workers run into challenges or machines are not operating efficiently. The sooner the factory sees an issue, the sooner it can be resolved or circumvented. Preventing safety failures is part of predicting, and preventing, delays.
Data Analysis. Once data is collected, advanced analytics tools and machine learning algorithms identify patterns, correlations and anomalies. An easy example might be past projects showing construction slowing down 10% in response to specific weather conditions, such as during snow days. If you can expect 27 snow days, on average, during the timetable of a specific project, the AI can estimate the likely delay and even do the math to estimate the lost production and revenue.
The technology can also analyze patterns in supply chain disruptions such as diesel fuel price hikes in winter, a supply shortage of certain chemicals during the spring growing season, etc. This analysis can help anticipate material shortages.
When issues arise, such as material shortages from one supplier, the sooner the factory knows they need to find another supplier, or choose another similar product material or part, the better. If there are other constraints that are going to curtail delivery, all parties can be made aware of that in advance.
Real-Time Monitoring. Once predictive models are in place, they can be integrated into an AI-enabled construction management system, to provide real-time monitoring of projects.
As new data flows in, the system can dynamically adjust predictions and alert project managers to emerging risks. For example, if a supplier reports a delay in material delivery, the system can immediately predict the potential impact on the project timeline. It might also be able to recommend alternative courses of action, even alternative products. (For instance, if the specs call for a Kohler 121 fixture but it’s not available, then maybe Kohler 122 could work.)
Actionable Insights. The ultimate goal of predictive analytics is to generate actionable insights to circumvent problems in advance to prevent profit loss. These insights allow project managers to make informed decisions, such as accelerating certain tasks to mitigate anticipated delays. Responses could include, ordering certain materials earlier than planned, or reassigning workers to avoid labor shortages.
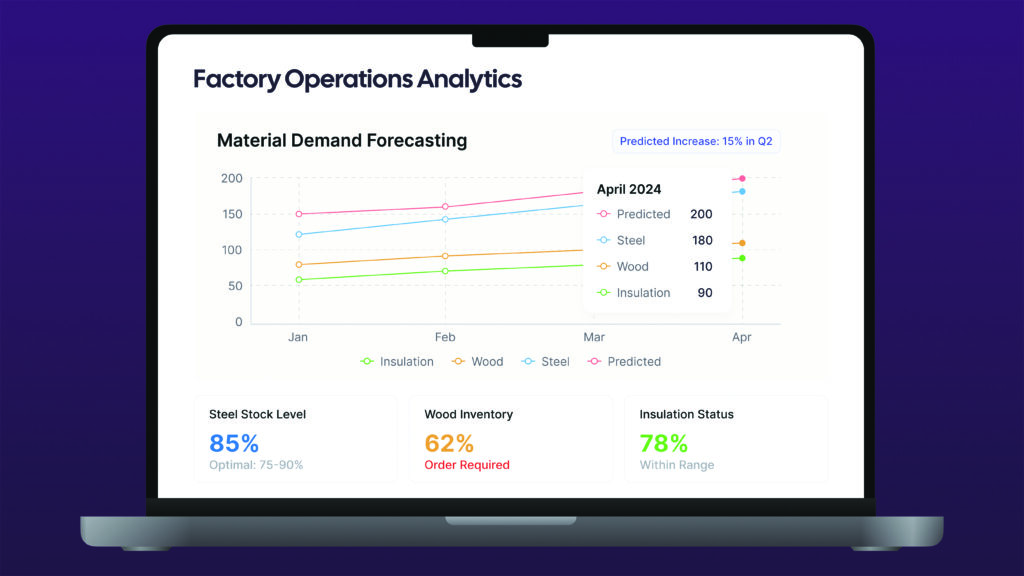
Companies Using This Technology
The use of predictive analytics offers several advantages to the construction industry, including improved project efficiency, cost savings, enhanced risk management and increased stakeholder confidence, just to name a few.
Some notable companies using predictive analytics include PCL Construction, Skanska USA, Lennar Corporation, DPR Construction, Bechtel, Clayton Homes (Berkshire Hathaway) and Turner Construction.
Clayton Homes, a manufacturer of modular and manufactured homes, utilizes data analytics to streamline its production and project delivery. Predictive analytics helps them to manage supply chains, anticipate construction delays and improve the efficiency of building processes.
Predictive analytics can even earn its keep supporting marketing efforts. For instance, it might work with the CRM system to determine the best time to send an email based on an individual user’s email habits.
Conclusion
In an industry where unforeseen delays can lead to financial losses and reputational damage, predictive analytics provides a game-changing solution.
By leveraging data and machine learning, construction companies can forecast potential disruptions before they happen, giving them the opportunity to take proactive measures. As the construction industry continues to embrace digital transformation, predictive analytics is poised to become a critical tool in driving efficiency, reducing costs and delivering projects on time.
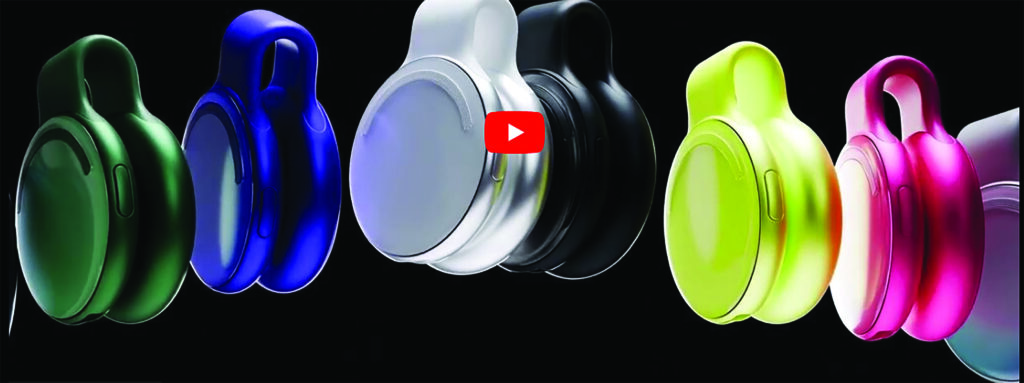
Erik Cofield, VP of Strategy at Merlin AI, has nearly 30 years of experience helping companies in residential construction. A member of NAHB, he specializes in AI, Sales and Marketing Strategy, Business Management, and leveraging technology in the sales process. Erik has provided consulting services to builders, developers, remodelers, and construction companies of all sizes and types. He can be reached at [email protected].