By Dennis Michaud, Managing Director of CertainTeed Offsite Solutions
In the building industry, where profit margins can be thin, we all know every variable that can be controlled makes a difference. Offsite construction has become a reliable solution for developers and builders aiming to enhance efficiency, shorten construction timelines, and navigate labor shortages, all while meeting the needs and wants of modern homebuyers.
Though the basis of prefabrication dates back centuries, today’s offsite construction solutions have evolved considerably. Leveraging streamlined processes, the latest product technology, customization capabilities, and elevated quality control, offsite construction delivers high-caliber modern homes in a fraction of the time of traditional construction.
Beyond the production line and build site, one of the most compelling benefits of modular and panelized construction is the way they enhance cost predictability. A clearer picture of costs empowers developers, builders, and contractors to approach project budgets and financial forecasts with greater accuracy, stability, transparency, and, ultimately, confidence.
This article delves into the unique advantages of offsite construction that support financial foresight.
Controlled Build Environment
At the heart of offsite construction is a controlled, factory-based assembly process that minimizes exposure to variables that often compromise on-site projects. When building components are assembled in a controlled environment, factors such as weather delays, material damage, and unexpected labor shortages are significantly reduced.
In contrast to traditional builds that are vulnerable to elements beyond the builder’s control, factory-based environments provide greater consistency and adherence to project timelines. This assembly approach not only reduces delays but also supports financial predictability by minimizing the hidden costs that come with unpredictable field conditions.
Unanticipated rain, snow, or extreme temperatures, for example, can stall traditional construction, leading to prolonged timelines and inflated budgets. With offsite construction, developers gain confidence in their scheduling, allowing them to avoid seasonal delays and unplanned expenses.
The predictability of factory assembly is also invaluable for year-over-year financial planning, as it supports reliable forecasting and fewer budget overruns.
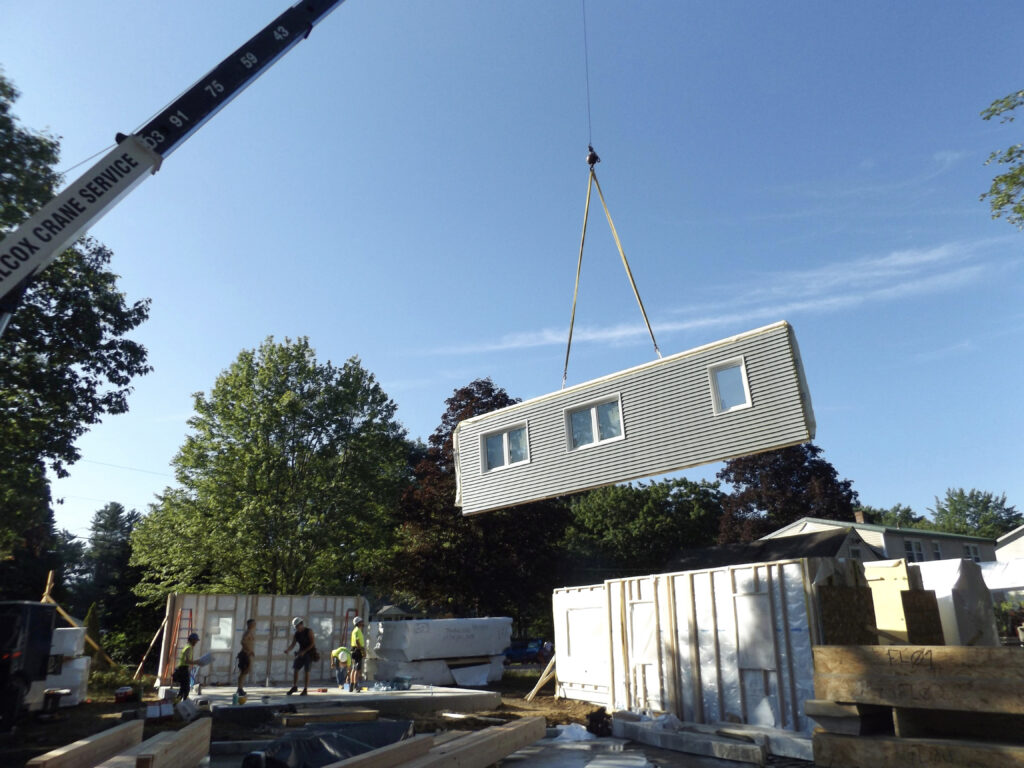
Streamlined Logistics
Weather is one significant variable in the management of project costs. Logistics are another. From supply chain to material delivery to on-site material handling, traditional construction is riddled with logistical hurdles that can stretch timelines and escalate costs. Offsite construction helps take the guesswork out of much of it.
With most of the building materials consolidated in a single factory location during manufacturing, offsite makes material sourcing, volume purchasing agreements, and inventory management more efficient.
Panelized assemblies, in particular, offer significant logistical benefits. Their compact, stackable design allows them to be flat-packed to maximize truckload efficiency, which reduces transportation costs and the number of trips required. Additionally, panelized systems simplify on-site assembly, requiring less heavy equipment and reducing labor costs. These combined benefits ensure tighter budget control, fewer logistical variables, and enhanced financial predictability for developers and contractors.
With fewer logistical variables, developers can allocate resources more accurately and avoid the fluctuating costs of material transportation and storage at multiple sites. This level of predictability not only simplifies budgeting but also allows companies to scale operations, handling multiple projects without the concern of logistical bottlenecks.
By streamlining logistics, offsite construction optimizes not only individual project budgets but also the financial structure of broader, long-term development plans.
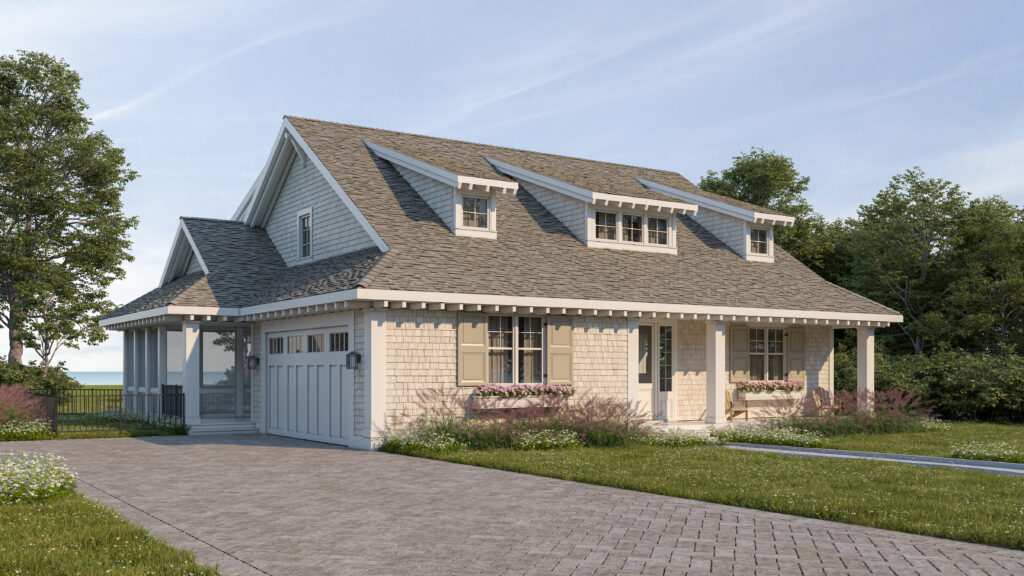
Optimized Workforce Allocation
Significant labor shortages have plagued the construction industry perennially since the Great Recession, and the labor needed to meet demand today remains woefully inadequate.
For traditional construction, grappling with labor challenges poses obvious problems: A dwindling supply of skilled tradespeople complicates staffing projections and leads to project delays, ultimately increasing costs for builders. The bottom line is that fewer workers to complete homes means fewer homes completed, less revenue generated, and slowed growth.
Offsite construction techniques ease these challenges by allowing a core, specialized team to complete much of the work within a factory environment. Since fewer personnel are required on-site, and tasks are standardized, labor expenses become more predictable and manageable, and the risk of delays due to staffing issues is minimized.
A controlled labor environment enables developers to allocate their workforce more effectively, reducing the costs associated with temporary hires or overtime pay. For contractors, the reliance on an optimized workforce leads to predictable, stable labor costs across projects.
By reducing the unpredictability of labor expenses, offsite construction becomes a tool for managing financial performance, ensuring that human resource costs remain stable and predictable from project to project.
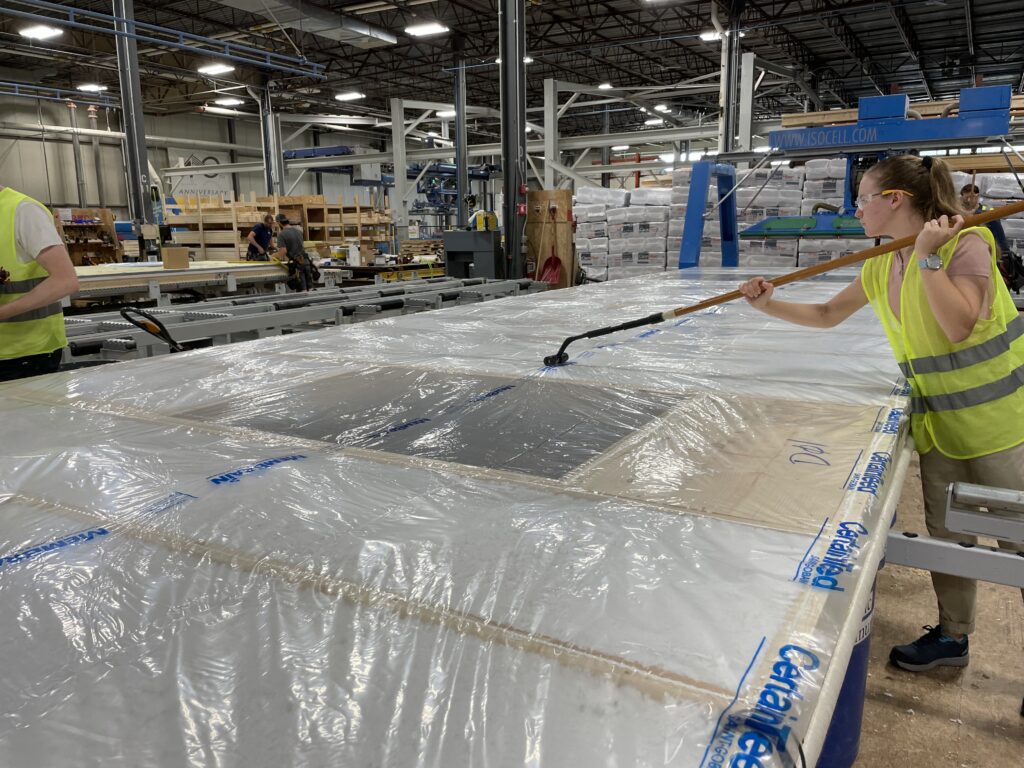
Reduced Material Waste
Waste reduction is another financial benefit inherent to offsite construction.
Traditional construction methods can result in significant material waste due to damage from onsite handling and errors in measurement.
By contrast, offsite construction offers precision in measurements and assembly techniques within a controlled environment, resulting in minimal waste and reduced material costs.
This efficiency not only lowers material expenses but also streamlines waste management costs. For developers, this translates to greater control over resources. For contractors, it means fewer budget surprises related to material overuse.
By improving material efficiency, offsite construction ensures that developers can accurately predict and control their supply expenses, leading to enhanced budget adherence across multiple projects.
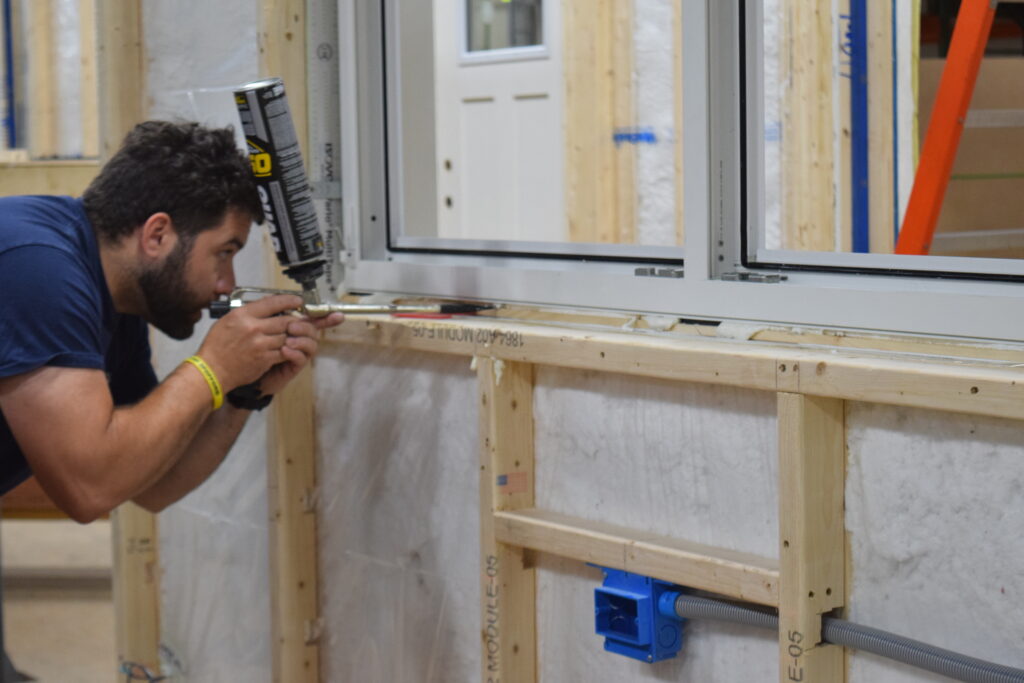
Fewer Unexpected Post-Construction Costs
As a matter of practice, most offsite construction companies engineer, manufacture, and assemble homes to the same standards as traditionally constructed homes. In some cases, the standards are even higher.
But equally important is how companies hold themselves accountable to these standards. With One Precision Assemblies™, for example, CertainTeed relies on high-quality materials for advanced moisture management, minimized opportunities for mold growth, and reduced energy consumption — but we also maintain rigorous quality control standards.
Quality checks ensure high-quality components coming out of the factory are up to standard and delivered undamaged to the site. By managing quality at each stage of the assembly, offsite construction reduces the likelihood of errors, rework, and long-term maintenance issues. This level of quality control reduces warranty costs and post-construction callbacks, providing developers with peace of mind regarding the longevity and reliability of their builds.
In addition to enhancing project predictability, fewer post-construction issues translate to lower costs for maintenance, repairs, and contractor call-backs. These savings benefit not only the current project budget but also future planning, as developers and contractors can expect fewer call-backs. With the ability to control post-construction costs, companies can reinvest savings into new projects, driving profitability and growth.
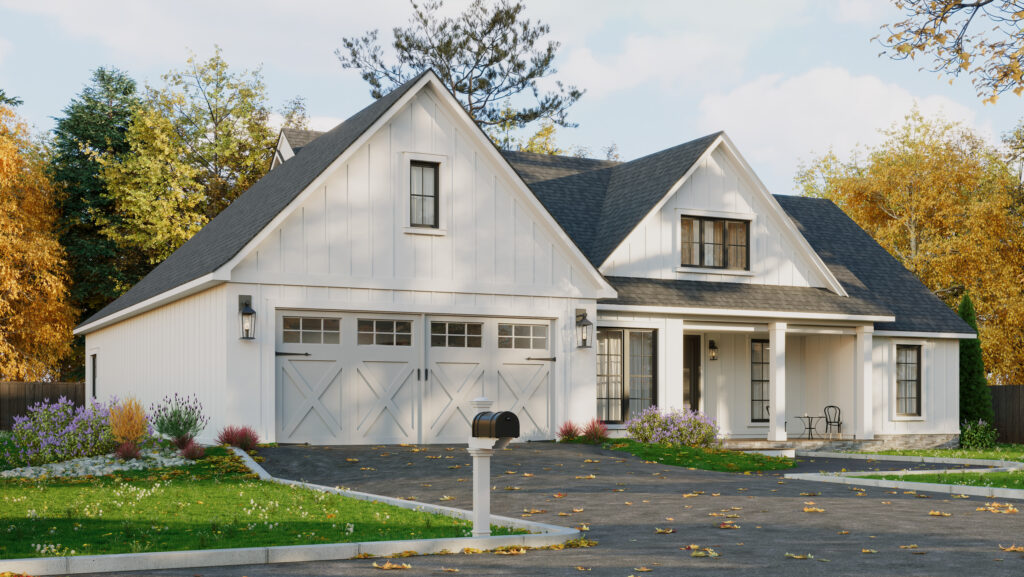
A Future Built on Predictability
Offsite construction isn’t just a solution for individual project savings; it’s a broad strategy that supports the long-term financial health of a construction company. With more predictable costs, fewer delays, optimized labor resources, and streamlined material expenses, offsite construction empowers developers and contractors to approach long-term planning with greater confidence.
As the construction industry continues to evolve, the importance of cost predictability will only increase. Offsite construction offers a unique combination of stability, efficiency, and quality that enhances the financial foresight of developers, builders, and contractors. By controlling costs across multiple areas, from labor and materials to logistics and post-construction expenses, offsite construction provides a solid foundation for sustainable, profitable growth.
By reducing variability in project budgets, offsite construction simplifies financial forecasting, supporting improved cash flow management and budget allocations. This stability is particularly valuable for multi-year projects and large-scale developments where financial planning is paramount. In an industry often characterized by uncertainty, offsite construction provides a path forward for companies looking to enhance their financial stability and minimize risk.
Learn more about how partnering with CertainTeed ONE PRECISION ASSEMBLIES™ can benefit your company: certainteed.com/one-precision-assemblies