Author explains the “Capacity” bubble and how it is affecting onsite and offsite builders, factories, developers and the end consumer
by Offsite Builder Staff
Many housing experts have discussed and even argued over when the housing bubble will burst, but there is another housing bubble occurring where labor shortages, material shortages, and rising costs result in lead times to the completion of projects extending 3 or 4 times longer than they did just 3 years ago.
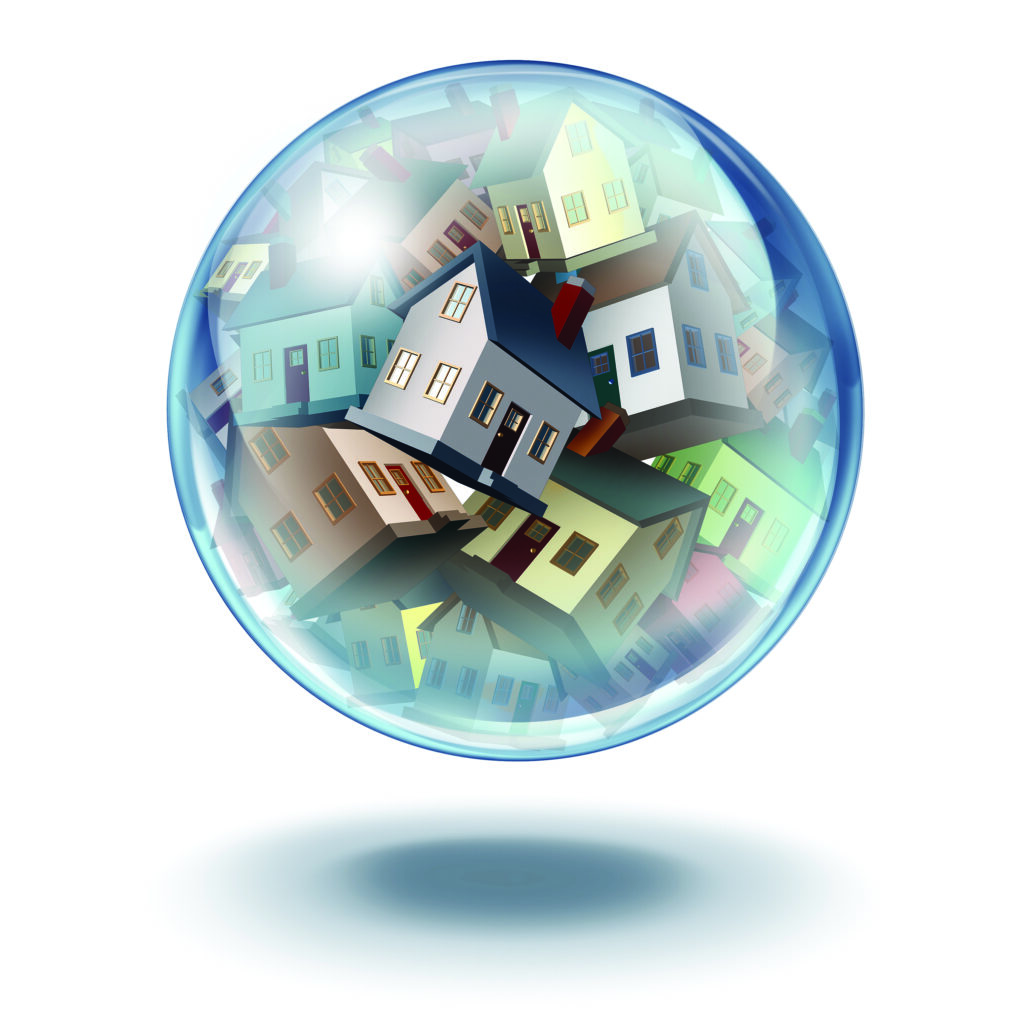
The “Capacity” bubble has been with us for a while now and it is affecting onsite and offsite builders, factories, developers and the end consumer.
Orders for new homes, affordable housing projects, hotels and other commercial projects are pouring in and the capacity to build them is curtailing new construction and those orders keep piling up.
Even when a project is lucky enough to get started, the availability of workers and materials slows down completion times. General Contractors are being sued by developers that can’t get completion dates for their projects. New home builders, both large and small businesses, are sharing that capacity problem. It doesn’t matter if they use onsite, offsite or modular construction methods, this is a situation they all share.
Several modular factory owners have told me they may not be able to survive the fantastic number of orders flooding in their front doors as it means their backlog continues to grow and without enough workers or materials to complete the houses as quickly as they used to, it could mean the return of hundreds of thousands of dollars in deposit as their builder’s customers begin backing out on contracts.
The rental market is once again getting hot as people that were about to build a new home simply can longer afford them and have begun looking at the rental market and “build to rent” developments.
The Capacity bubble won’t bring about housing foreclosures, but it could begin to erode an offsite factory’s profit to the point where closing the doors or selling it are the only options. Modular factories are being pushed to the seams to build more homes and commercial projects but here are some reasons that may not happen this decade. Currently, modular factories produce about 3% of the total construction in the US. To raise that to 20% market share it will require hundreds of new modular factories to be built.
Here are just a few reasons why that won’t happen:
Lack of Capacity.
For modular factories to produce 100,000 modules (the current 3% level) a year which equates to an average of 20 floors a week being produced by the approximately 100 modular factories in the US. That means to reach the goal of modular producing 20% of all new, the number of floors will need to increase 7-fold in existing factories.

Cost to Build a Factory.
Building a new modular home factory consists of three parts. The land, the building, and the equipment. Oh, if only it were as simple as putting up a 100,000 sq ft building at $55 a square foot. But that necessary evil of land is always there and that can run into the millions with excavation, utilities, paving, etc. Now add about $5,000,000 for the production floor equipment, offices, showrooms and maybe a couple of model homes and the total quickly escalates to over $10,000,000. Now multiply that by the additional 230 factories needed and you need an investment of about $2.5 billion.
That type of investment is not going to happen anytime soon in the modular housing industry where even if we could find the money needed for additional factories, there is always a chance the demand for new housing may dry up if inflation and interest rates continue to rise.
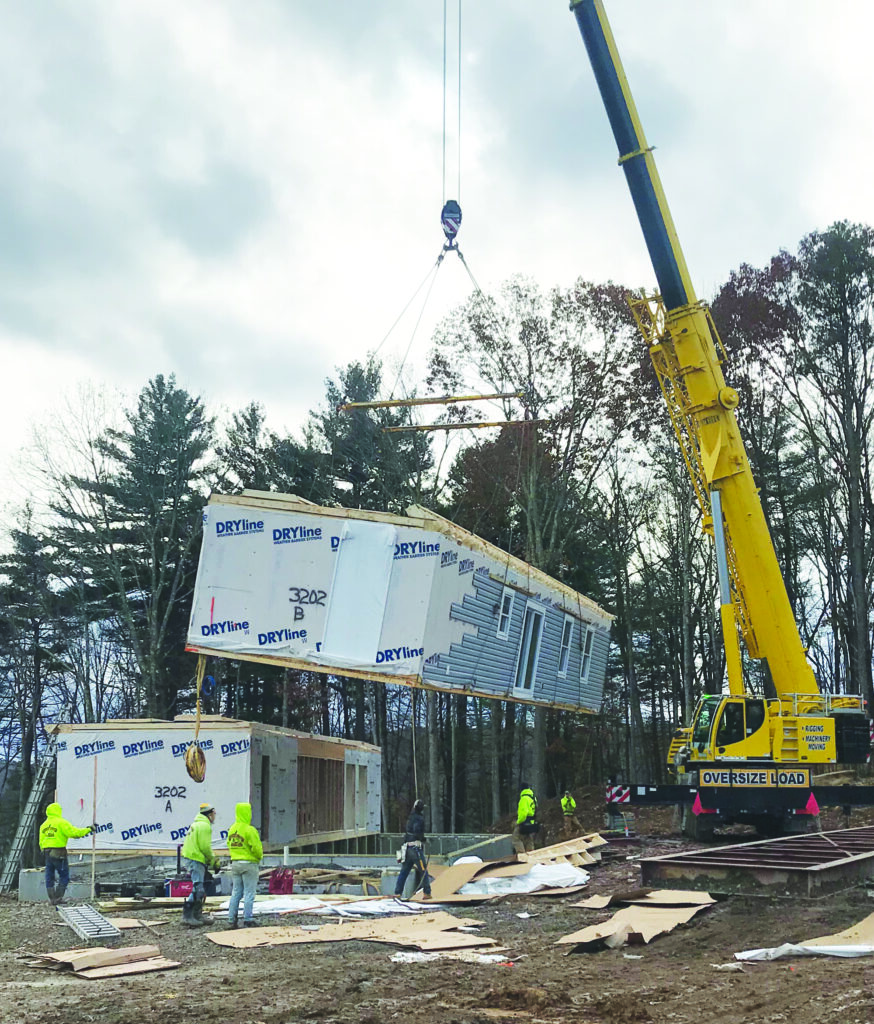
Lack of Builders.
Not only would we need an additional 230 factories, but we would also need 10,000 new home builders each building 12 homes a year to meet the need for these 120,000 increases in new modular housing. With little or no training available to new builders, finding that many and making them productive will never happen. On top of that, young people are not entering the retail trades like they did just 10 years ago. Few want to risk everything they have just to get into a business that forces them to work as hard as a new home builder.
Many of today’s modular home factories are ramping up production of tract homes and high-rise condos and commercial buildings such as hotels. This switch to a much larger pool of potential business than working with the retail new home builder means that the small builder may soon be seeing themselves pushed out by many factories that embrace a more commercial clientele.
Lack of Workers.
Modular home factories are rarely built next to major cities and urban areas that need the affordable housing that modular can bring them. The factories are located up to a hundred miles away and sometimes hundreds of miles from their product’s destination. The extra labor needed for all these additional factories will have to come from somewhere but the displaced worker that lives in the city where the stick building is replaced with modular cannot and will not move hundreds of miles away to work for half what they made in the city.
The local labor pool found near most factories is quickly drying up as easier service jobs are taking a toll on the factory’s production floor. Factories are seeing many more new applicants fail the drug screening test. What good are 230 new factories without enough labor to build all those new modules?
Lack of Transportation.
I can’t even imagine how many more carriers, trucks and drivers will be needed if we increase our market share to 20%. There are already lotteries by some states allowing only a few modulars into their states every day. With the cost of fuel for those trucks climbing higher, additional transportation costs will have to be added to every module leaving the factory.
All this boils down to capacity. While many are worried about a housing bubble crashing the housing market, maybe we should be worried about the Capacity bubble bursting when demand completely frustrates our ability to supply it.