Eight practical quality control strategies for offsite construction.
Quality control (QC) is essential in offsite and modular construction. It’s the key to making sure that buildings come together smoothly and meet high standards. However, when it comes to QC, you don’t need fancy or expensive tools. By focusing on straightforward, cost-effective inspection techniques, you can build a reliable quality control system that catches problems early and ensures consistent results.
In this article, we’ll explore eight simple, lean-friendly QC methods that offsite factories can use to ensure excellence. These ideas aren’t complicated, but they’re powerful, and they align well with the Lean philosophy of minimizing waste and maximizing value.
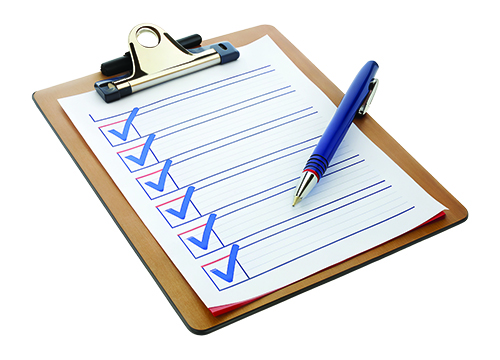
1. Standardized Checklists
Checklists are one of the simplest but most powerful tools for quality control. They ensure that every component and assembly is checked the same way, every time. This consistency is key in offsite construction, where modules and parts need to fit together perfectly when they reach the jobsite.
What It Does: A checklist makes sure that no step is missed in the inspection process. It helps inspectors remember what to look for, whether it’s the placement of electrical outlets, the quality of welds, or the alignment of walls.
How to Use It in Offsite Construction: Break down each stage of production into specific tasks and create a checklist for each. For example, in the framing stage, a checklist could include items like: “Nail patterns are correct,” “Studs are spaced 16 inches apart,” and “Window and door openings meet specified dimensions.” At each stage of production — such as framing, electrical, plumbing, or finishing — the checklist should be reviewed and signed off by a quality inspector.
Standardized checklists ensure that every detail is inspected, reducing the chances of mistakes. Even the most experienced workers can miss something, but a checklist makes sure nothing gets overlooked.
2. Go/No-Go Gauges
A Go/No-Go gauge is a simple tool that allows inspectors to quickly determine if a part or feature meets specific dimensional requirements. It’s commonly used in industries that require precise measurements without complex tools or high-tech equipment. Go/No-Go gauges are particularly helpful in offsite construction, where ensuring that parts fit together accurately is essential.
What It Does: A Go/No-Go gauge checks whether a part’s dimensions fall within acceptable tolerances. The gauge has two ends or two sets of dimensions: The “go” side of the gauge represents the maximum size within tolerance, which is the upper limit. The “no-go” side represents the minimum size, marking the lower limit.
How to Use It in Offsite Construction: Suppose you’re manufacturing wall studs that need to be a precise width to fit within a modular wall frame. To check each stud, an inspector uses a Go/No-Go gauge. If the stud slides smoothly into the “go” side of the gauge, it’s within the maximum allowable width. If it does notfit into the “no-go” side, it meets the minimum size requirement. In other words, an acceptable part/assembly will fit in the “go” side of the gauge, but not in the “no-go” side.
Go/No-Go gauges are quick, easy to use and don’t require advanced training. They ensure that critical dimensions are met with minimal room for human error. Using these gauges saves time compared to measuring with calipers or other more complex tools, and provides a clear, pass/fail result that’s easy to interpret. By catching any parts that fall outside of specifications early, the team can prevent costly rework and delays on the jobsite.
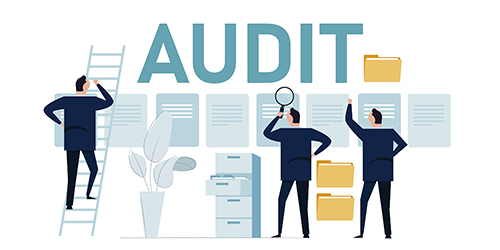
3. Layered Audits
In a layered audit, multiple people inspect components and assemblies at different points in the process. This approach catches mistakes that might be missed in a single inspection.
What It Does: Each layer, or level, of inspection provides an additional check. For instance, the first layer might be production workers checking their own work. The second layer could be the supervisor doing a spot check, and the final layer might be a quality inspector doing a thorough review.
How to Use It in Offsite Construction: During the assembly of a wall module, for example, the person assembling it could inspect the work for correct measurements and secure connections. Next, a supervisor might do a quick check to make sure the frame is square and meets specifications. Finally, a quality inspector could review the wall module before it moves to the next production stage.
Layered audits spread the responsibility for quality across multiple people and steps. This approach increases the chances of catching mistakes early and creates a culture where everyone is accountable for quality.
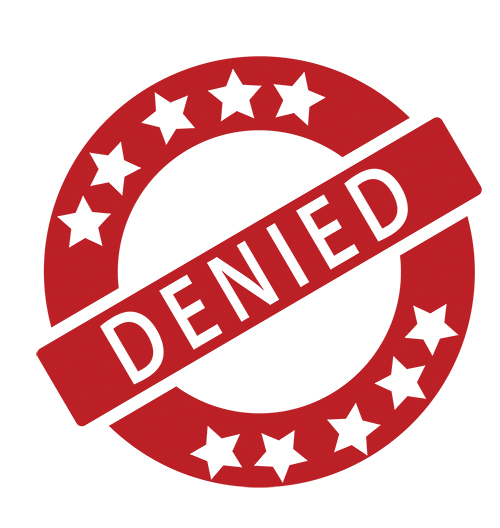
4. Red Tagging
Red tagging is a Lean quality technique that involves tagging items that don’t meet standards with a red label or “tag.” It’s part of the 5S methodology, which is a system to keep workplaces organized and efficient.
What It Does: When something doesn’t meet quality standards, a red tag, sticker, or similar, is attached, signaling it needs rework or corrective action. The tag stays on until the issue is fixed, making it clear to everyone that the item requires attention.
How to Use It in Offsite Construction: Let’s say a modular bathroom pod has a plumbing connection that’s not properly aligned. The inspector places a red tag or sticker on the unit, marking it for correction. This visual signal tells everyone on the floor that the unit needs attention before it can move to the next stage. Red tagging also helps the team prioritize items that need rework.
Red tags are a clear, visual indicator that something needs fixing. This simple method prevents non-conforming products from slipping through the cracks and ensures that only high-quality components move forward in production.
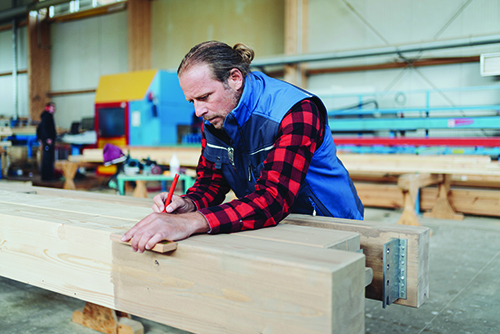
5. First Article Inspection
First Article Inspection (FAI) is an in-depth inspection of the first unit produced in a batch or production run. It ensures that the first item meets all requirements before mass production begins.
What It Does: FAI sets the standard for the rest of the production run. By thoroughly inspecting the first item, QC teams can verify that the design, materials and measurements are correct before the factory starts full-scale production.
How to Use It in Offsite Construction: Imagine you’re building roof trusses for a modular home. After creating the first truss, a quality inspector checks all aspects — dimensions, joints, alignment — to ensure it meets design specifications. If the truss passes inspection, production can continue. If it doesn’t, adjustments are made before additional trusses are built.
FAI allows factories to catch issues early in the process, preventing the production of a whole batch of defective components. It saves time, reduces waste and sets a high standard from the beginning.
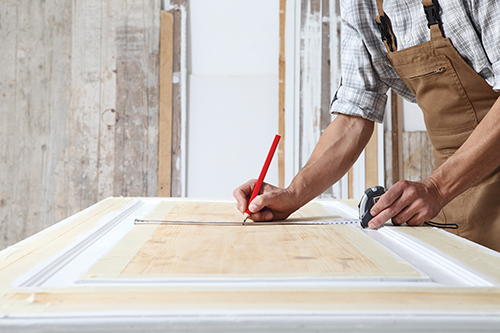
6. Statistical Process Control
Statistical Process Control (SPC) uses simple data analysis to monitor production processes and ensure consistency. This method doesn’t require advanced tools — basic charts and tracking can go a long way.
What It Does: SPC helps detect changes in production quality before they become significant issues. By tracking key measurements over time, SPC can show trends that indicate when adjustments are needed.
How to Use It in Offsite Construction: Let’s say you’re monitoring the dimensions of window openings. You can track these measurements on a control chart that shows acceptable limits. If the measurements start trending outside of these limits, it’s a sign that the process needs adjustment to avoid producing out-of-spec openings.
SPC helps detect quality issues early, reducing rework and ensuring that products remain within acceptable standards. It’s a proactive approach to quality, using simple data to prevent problems before they occur.
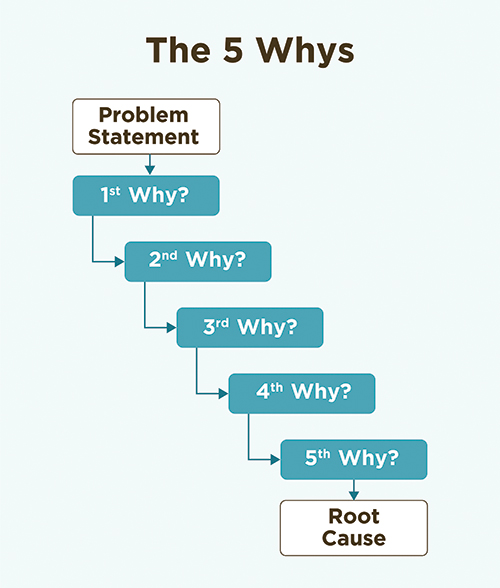
7. Root Cause Analysis
When a defect does arise, Root Cause Analysis (RCA) is essential for understanding why it happened so you can prevent it from happening again. RCA digs into the “why” behind quality issues, identifying the underlying causes.
What It Does: RCA helps identify the root of a problem rather than just treating the symptoms. This approach ensures that any solution addresses the true cause, leading to long-term quality improvements.
How to Use It in Offsite Construction: Suppose a modular unit consistently has alignment issues with its door frames. Using the “5 Whys” method, you could ask, “Why is the frame misaligned?” The answer might be, “Because the support beam isn’t square.” Asking “Why?” multiple times eventually leads you to the root cause, which might be a misalignment in the initial framing.
RCA prevents recurring issues by addressing their true causes. By finding and fixing the root problem, you stop quality issues from happening repeatedly.
8. Training and Skill Development
Even with the best tools and processes, QC is only as effective as the people carrying it out. Well-trained employees make better quality inspectors and contribute more to the continuous improvement process.
What It Does: Training builds employees’ skills, helping them to understand quality standards and learn how to spot defects effectively. It also fosters a sense of responsibility for quality among everyone in the factory.
How to Use It in Offsite Construction: Provide hands-on training sessions where employees learn to use Go/No-Go gauges, apply checklists and perform basic statistical checks. Cross-train employees in different production areas to give them a broader understanding of how their work impacts overall quality.
Skilled employees are better equipped to maintain high standards and identify potential issues. By investing in training, you create a quality-focused team that takes pride in producing excellent products.
Conclusion
Quality control in offsite construction doesn’t need to be high-tech or expensive to be effective. Lean, simple QC methods — like standardized checklists, Go/No-Go gauges, layered audits and red tagging — can deliver remarkable results. By focusing on practical, accessible techniques, offsite manufacturing facilities can achieve consistency, prevent defects and improve quality without a big budget.
Quality control is about more than just tools and techniques. It’s about creating a system and a culture where everyone is responsible for quality. By applying these Lean, affordable QC methods, your factory can ensure reliable, high-quality products that make clients happy and keep your projects on track.
Daniel Small is a Denver, Colorado-based management consultant to the offsite construction industry. He specializes in Lean Construction and Manufacturing and Six Sigma methodologies. For assistance with getting more from your offsite manufacturing process, contact him at 719-321-1953 or [email protected], or visit www.DaVinciConsulting.co.