This 100-year-old Swiss company has gone all-in with automation and robotics.
- Renggli uses BIM models to drive a largely automated factory.
- The facility is clean and precise, with very little waste
- By approaching a building as a kit of parts, the company can handle design variations while maintaining an efficient operation.
Nestled in the foothills of the Swiss alps, sits one of the most advanced prefab construction factories in Europe. Renggli, a 100-year-old firm, builds high-performance, energy-efficient, prefabricated panelized structures. They use a variety of machines to automate their manufacturing process, like CNCs, suction cup lifts, robotic saws, tilting tables, gantry cranes and more.
I had a chance to visit Renggli in 2022 and it’s fair to say that I was blown away by the precision of their facility, the high quality of materials used and, of course, the robots in their assembly line. In this article, I walk through the steps of their process and touch on its pros and cons.
Like an Amazon Warehouse
The first machine in Renggli’s process is a platform system adopted from the automotive industry. Forklifts load drywall, timber, sheathing and other large materials onto the base of the machine. They are separated into categories and stored on shelving racks. As material is needed inside the factory, it is automatically retrieved from these shelves and carried down a highway system.
The factory operates like an Amazon warehouse. Every piece of material is tagged with a unique barcode, which allows every component to be tracked, easily located and retrieved by the machines. There is also a huge storage building with tagged lumber and engineered wood waiting to be used.
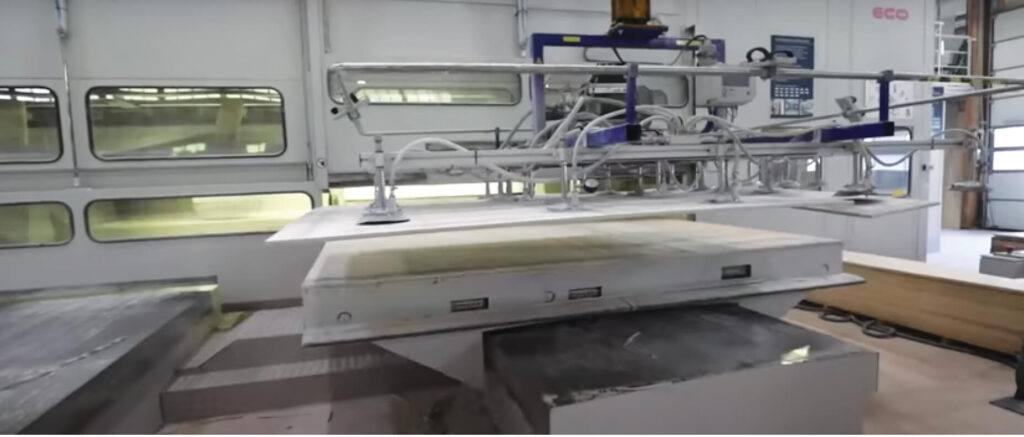
Such an advanced facility needs highly detailed BIM models to drive its processes. As readers of this magazine know, BIM stands for Building Information Modeling, a technology in which digital 3D models are loaded with information, which in this case includes the size and location of every part and piece. Renggli knows how large each wall panel is, how many pieces of lumber go into building it, how many nails are used, where electrical boxes are located and more.
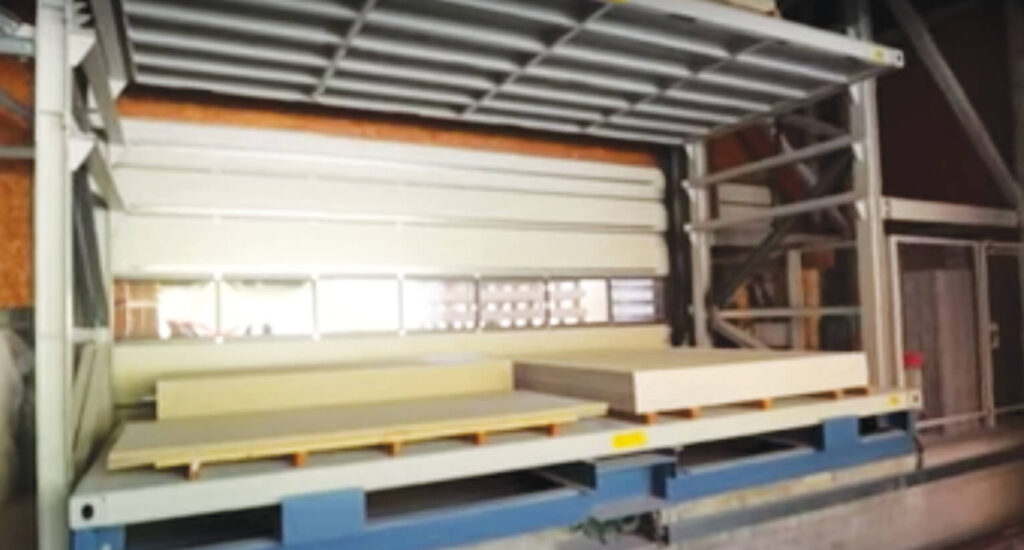
BIM modeling allows them to think of a building as a kit of parts, and to plan the sequence in which the panels are built in the factory and assembled on job sites.
The second robot in the process is a CNC, or computer numerical control, machine. Gypsum boards and wood panels are lifted from the shelving racks and brought to feed tables. From there, they slide into the sealed-off CNC machine, where they are cut with router bits. BIM data dictates the dimensions of each piece and where the cuts for electrical outlets and plumbing are made. When the cuts are complete, the table slides out of the machine. Suction cups carefully lift the pieces to another platform.
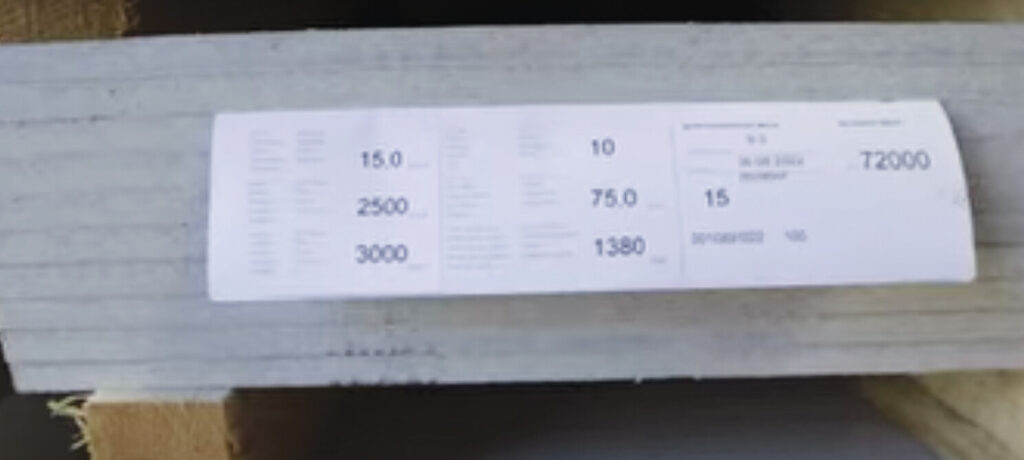
I was shocked by how little waste was generated during this process. Thanks to the BIM models, cuts are optimized for maximum output. Small waste pieces are collected in bins and recycled, if possible.
I was also surprised by how clean and dust-free the factory is. The CNC machine is connected to two exhausts; one for gypsum dust and another for wood dust. Two large tanks outside the factory store this dust until it’s ready to be disposed of. Wood dust is burned in winter and used to heat the office and factory, which reduces landfill waste.
The third machine is an advanced Hundegger saw. Large pieces of wood, some 40 feet in length, are fed into this fully automated machine. It can cut wood in 5 axes and can also drill screw holes, cut notches, mortise and tenon joints, and punctures for electrical and plumbing. Once again, data from the BIM models dictate the cuts. Sawdust is suctioned away, which keeps the factory floor clean.
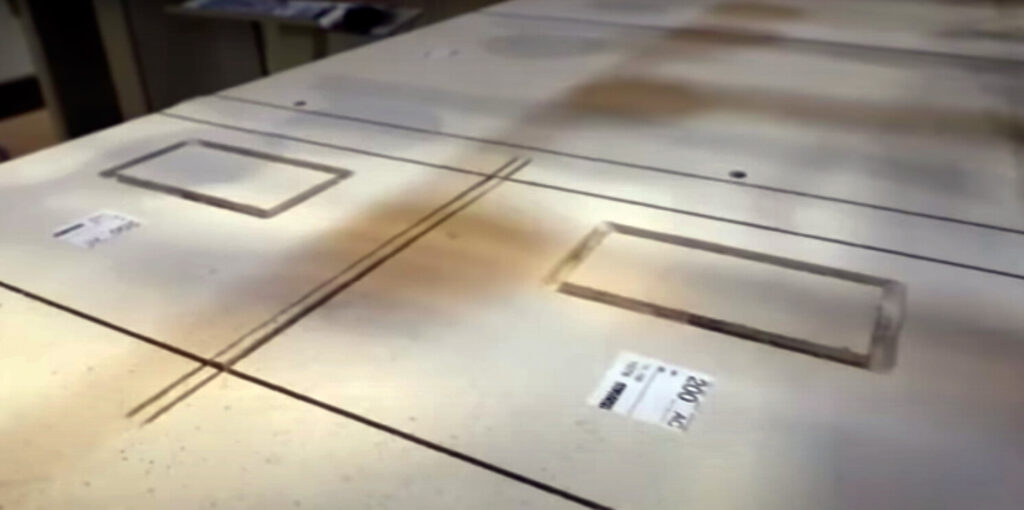
Because precision is so important to offsite construction, Renggli only uses engineered wood like glulam beams. Each piece of lumber needs to be perfectly straight, with consistent widths and thicknesses.
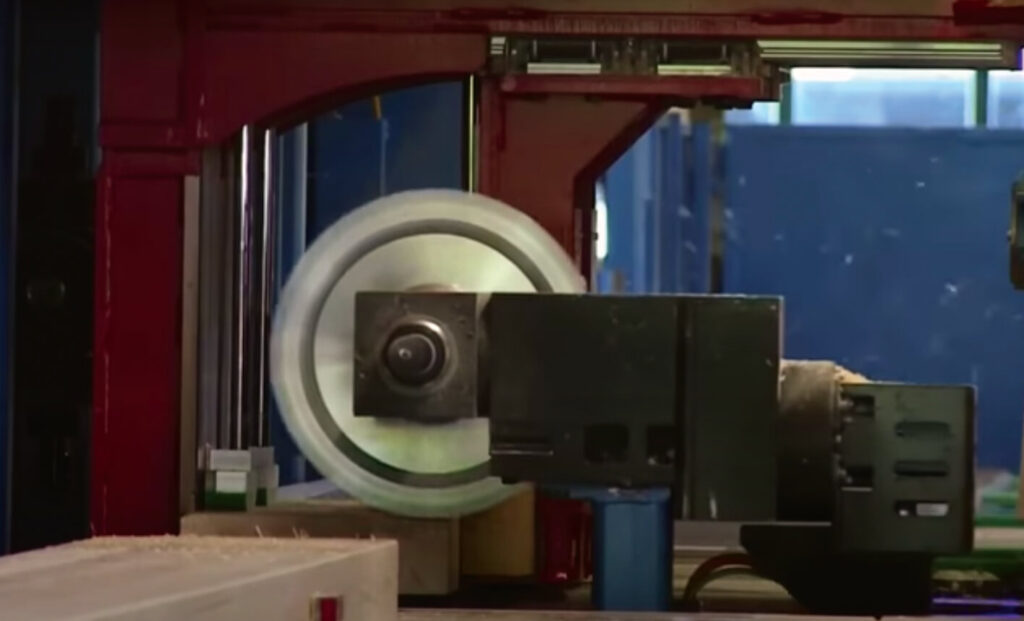
Some Labor Required
The fourth type of machine is a simple, but extremely useful butterfly table. Workers build wall, ceiling and floor panels on these tables using milled glulams, sheathing and drywall. When work is done on one face of a panel and it’s time to work on the opposite face, a hydraulic lift flips the table 90 or 180 degrees and safely lowers, which takes just 90 seconds. Automating the repetitive task of flipping panels this way can prevent any potential injuries. Another cool aspect of these tables is that they have metal pins that act as guides for wood studs by automatically moving to the right positions. This makes assembly easier
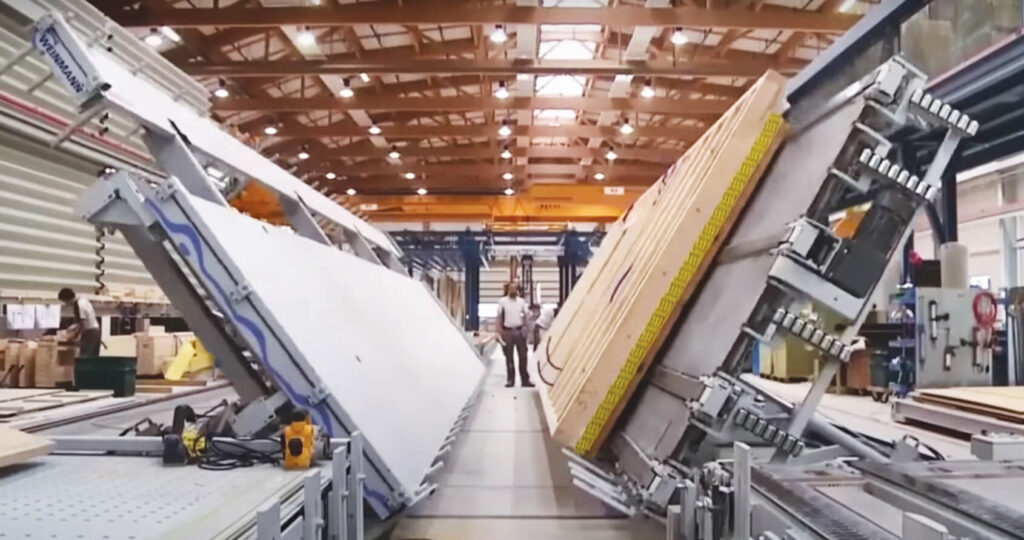
The fifth machine is a gantry crane system that spans the entire length of the factory. It carries building panels from one assembly table to another.
In the final assembly section, workers place thick mineral wool insulation in the stud bays and a place a layer of wood fiber insulation on the exterior faces of the panels. They fasten drywall to the interior faces. Plastic conduit for wires is also installed in the panels.
While most of the factory is automated, final assembly is still reliant on manual labor. But unlike typical job sites, it’s highly organized. Every station has a fully stocked supply cart and dedicated people make sure no one runs out of supplies.
Once the panels are complete, they are lifted by cranes, flipped into the vertical position, stacked on transport platforms, and draped with plastic. The plastic is heat-sealed to protect the panels from moisture. The plastic cannot be reused in the factory, so they send it to a recycling plant.
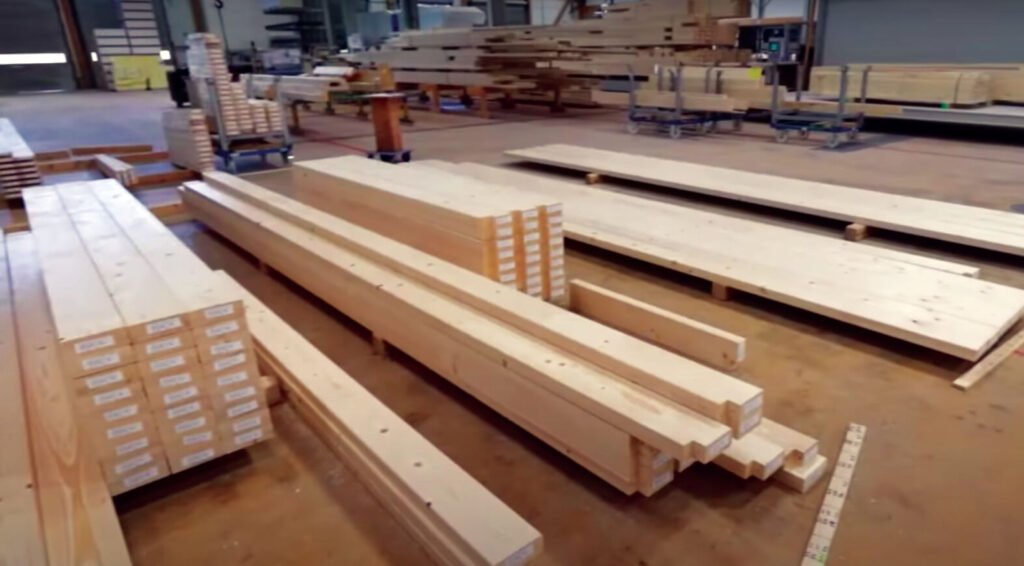
Final Impressions
As you can tell, I was very impressed with the way the factory was run and how the company has successfully managed to rethink buildings as kits of parts.
It’s not easy or cheap to build such an advanced facility, and in order to compete with traditional construction, Renggli has to be extremely efficient. They cannot afford to have people waiting around for materials or instructions. The factory needs to run like a well-oiled machine.
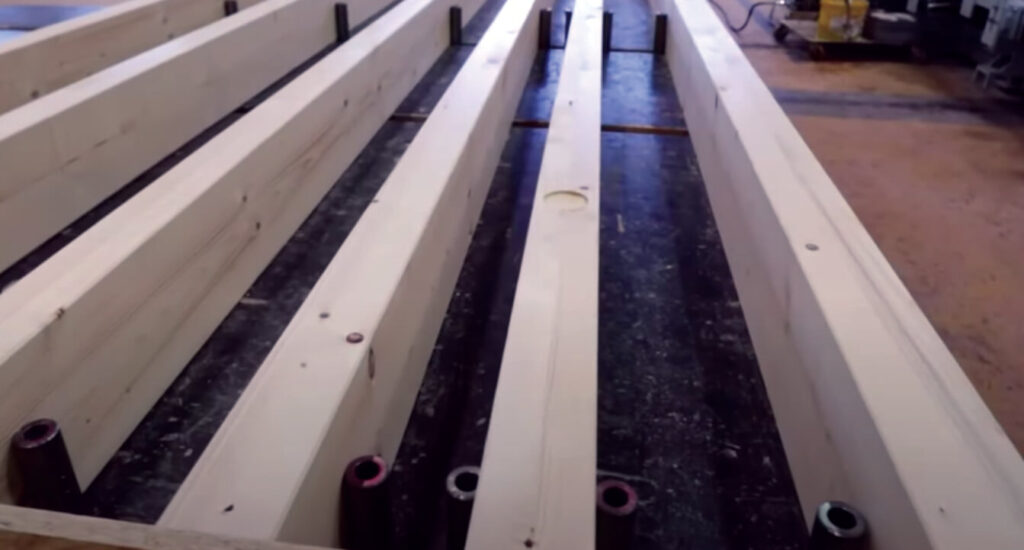
David Renggli, one of the owners of the company, spoke with me about the importance of accurate BIM models, which he referred to as a digital twin. The company uses the models to extract material lists and buy raw materials early, which in turn lets them guarantee customers a certain price.
The factory setting also means Renggli can build panels faster and better. They don’t have to worry about exposure to rain, snow, and other elements, and they can hire older and more experienced workers because indoor working conditions are not as harsh. They are also able to minimize waste because of careful planning and execution.
The final advantage is the sustainability of wood construction. I usually get a lot of flak for saying this, because there’s an unfortunate misunderstanding that wood and mass timber construction equals deforestation. This isn’t true. Renggli only uses sustainably harvested wood, where a tree is planted for every tree cut down. They use rapidly growing softwood and not hardwood. In addition, their factory and office are powered by solar panels almost all year round.
Let’s end this discussion with some of the disadvantages of Renggli’s prefabricated process. They build well-insulated, air-tight buildings with massive walls, floors and ceiling panels. These buildings require less energy to run over their lifetime, but have high initial carbon footprints, thanks in part to their use of stone wool insulation.
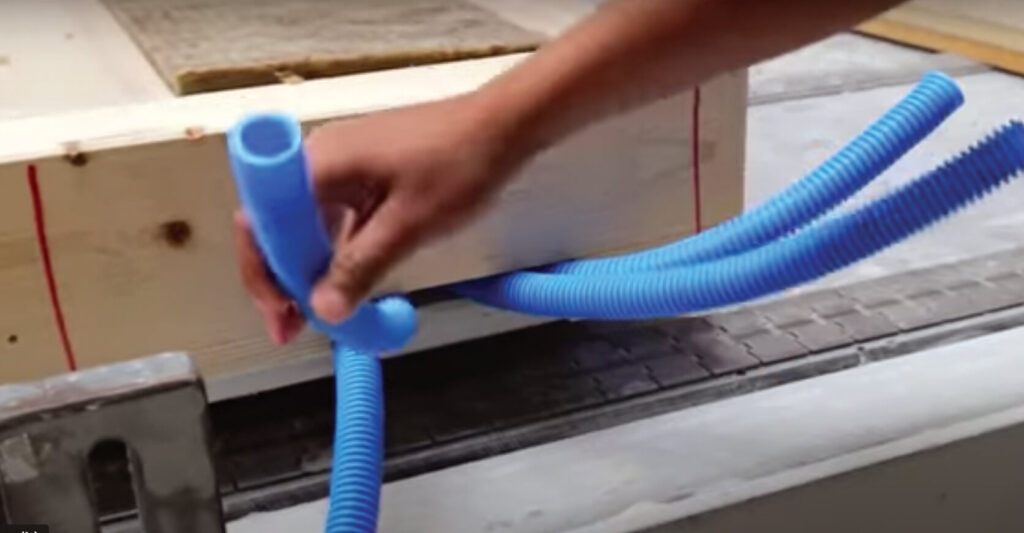
Also, the fact that they use high-quality engineered wood, triple-glazed windows, and 10-inch-thick insulation tends to raise material costs. Finally, as successful as Renggli’s process is, construction is a very difficult industry to automate because every project is so individualized.
I hope our industry embraces prefabricated, off-site construction more and starts thinking of buildings as an assembly of products. It’s going to take a while and it’s going to be messy, but with companies like Renggli proving that it can be done, there’s hope.
If you want to know more about what this very interesting company is doing, there’s a video version of this article on my YouTube channel. You can also check out my full interview with David Renggli in the September 12, 2022 episode of the Belinda Carr podcast on Apple Podcasts.