This technology can virtually optimize products and manufacturing processes. But is it worth the cost?
- In the case of plant equipment, uses range from performance optimization and predictive maintenance of existing machines to the testing and troubleshooting of new machines before they’re built.
- In the case of modules, a manufacturing simulation can be run to ensure that the unit has been appropriately designed, and can be easily produced on the plant’s equipment.
- Costs for a digital twin can range from tens of thousands to hundreds of thousands of dollars, depending on the complexity.
“We have no choice but to implement sound means to make modular construction perfect,” says Jim Dunn, President of Stack Modular, an international manufacturer of large-scale steel frame modular construction projects. The means, in this case, are digital twins. How do digital twins relate to factories and offsite construction, and how do they earn their keep?
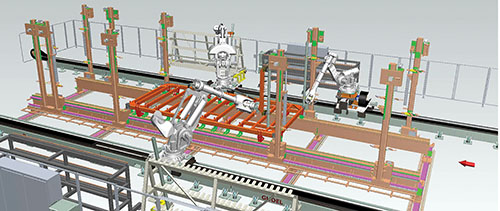
Image courtesy of: Brave Control Solutions Inc.
What Is a Digital Twin?
First, let’s define what digital twins are. In the case of a manufacturer, the term applies to virtual representations of the products being made, as well as of the production line that’s making them.
“A digital twin is a virtual, real-time replica of a physical asset, process, or system, which for offsite manufacturing could represent a complete modular unit, a production line, or individual components within the system,” explains Dan Pollard, a Production Director for Elements Europe, a UK-based manufacturer of modular and bath pod systems.
“Digital twins integrate real-time data from IoT sensors, machine learning and simulations to replicate not only the physical structure, but also its behaviors and interactions,” he continues. “For example, a digital twin created in Revit might be enhanced with live factory data to track module production, optimize workflows and even simulate on-site installation.”
Software providers and consultants play key roles in helping manufacturers implement digital twins. Software providers supply the tools, platforms and training needed. Consultants bring expertise in process optimization and industry-specific knowledge to guide integration and to ensure that the digital twin aligns with the manufacturer’s business goals.
The Cost of Digital Twins
The average net profit margin in construction ranges from 2% to 10%. This makes the industry notoriously risk averse; after all, risks that don’t succeed can be costly. When it comes to developing a digital twin, the risk is a price tag that can range from tens to hundreds of thousands of dollars.
Lots of factors come into play here. For instance, the actual cost of building a digital twin for a machine will depends on things like the machine’s complexity, the software platform used and the machine’s objectives. Initial costs might include hardware sensors, software licenses and development time.
The time required to create the twin will depend on the complexity of the machine. It might take a few weeks for simpler equipment, while for more complex systems, it could take several months.
One could build a digital twin for an existing or a new machine, yet the purpose and benefits might differ. For existing machines, the digital twin can help optimize performance, predict maintenance needs and extend its operational life by providing real-time data and simulations. For new machines, it will allow manufacturers to simulate performance, test designs and troubleshoot potential problems before physical production begins, thereby reducing development risks.
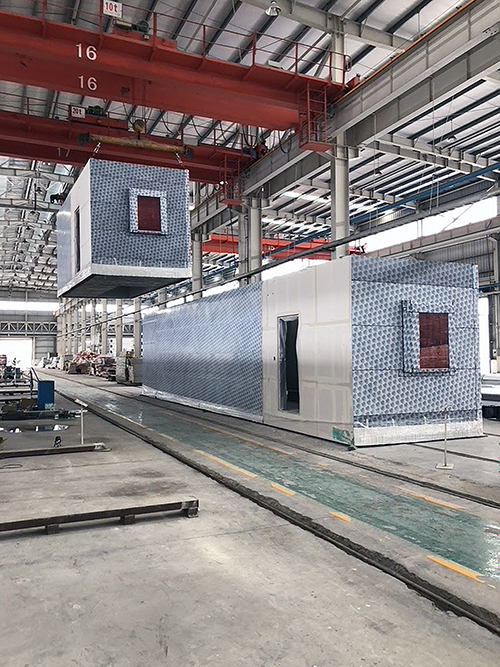
Photo courtesy of: Stack Modular Structures Ltd.
The Benefits
Users of digital twins claim that the technology offers many benefits.
For instance, a digital twin can enable manufacturers to monitor, simulate, and predict outcomes without disrupting physical operations, which can improve efficiency, quality and overall performance in real time.
Brent McPhail is Founder and former CEO of Brave Control Solutions Inc., a Windsor, Ontario, Canada-based company that specializes in building custom, made-to-order automation solutions for the construction industry. The company was an early pioneer in the adoption of digital twin technology.
McPhail originally began developing digital twins around 2010, using the video game software Unity, well before the concept gained mainstream traction. Reflecting on those early days, he notes how far the technology has come since his team began working on it.
His original focus was the automotive industry, where he provided custom automation for companies like Ford, GM, Chrysler, Honda and Goodyear. “Digital twins provided significant advantages, allowing [manufacturers] to visualize solutions and offer feedback early. For instance, new machines can be tested in simulation before they are built, which eliminates a lot of costs.”
When he pivoted to construction automation, he found even greater benefits — using digital twins to validate product feasibility before production. “By virtually loading new building designs into an existing machine’s system, we can simulate the entire production process digitally,” he says. “This allows us to test for potential issues, like collisions or access problems, before the designs hit production. Once identified, these issues are flagged and shared with the architects, who can then adapt their designs to align with the constraints of the automation.”
The technology lets them catch issues and optimize designs for manufacturability, refining them for automation. “We call this DFMA-RA: Design for Manufacture and Assembly – Refine for Automation, with the ‘-RA’ emphasizing the fine-tuning of designs to maximize automation efficiency.”
In home manufacturing, where designs are constantly evolving, digital twins provide ongoing value throughout the entire lifecycle. “They enable you to evaluate the feasibility of new products before production, continuously saving time and money,” McPhail says. “They offer initial cost savings and help future-proof your investments, ensuring adaptability in an evolving industry.”
The initial cost savings from digital twins come from virtual testing. “We build custom, made-to-order machines based on each client’s unique requirements. These machines involve multiple disciplines: mechanical design, process flow design, electrical systems and fluid systems like hydraulics, lubrication and cooling, along with control system design.” Being able to test them virtually before they’re built saves time and money.
Digital twins also contribute to efficiency and quality improvement. Manufacturers can use them to perfect everything from architectural designs to computer programs. “A digital twin ensures you have conformance [with the specs] before you build,” Dunn says. In an arena like offsite manufacturing, meeting precise specifications is invaluable.
“Through digital twinning, manufacturers can simulate conditions, test designs and anticipate potential issues before the physical build begins,” Pollard says. “This reduces the risk of defects and increases the likelihood of a perfect first-time delivery.”
A digital twin of a finished home or building also enables customers to engage more in the design process. How will changes to the design impact the look of the final product?
“This dynamic visualization helps customers make informed decisions faster and reduces the back-and-forth traditionally associated with [design changes],” Pollard says. “By offering a more intuitive, interactive experience, manufacturers can deliver precisely what customers want, reducing the risk of post-production changes and delays.”
Other benefits of digital twins that impact the bottom line include improved resource efficiency. Digital twins enable manufacturers to optimize material usage and reduce waste.
Finally, digital twinning is useful and valuable even after developing the physical item. “The digital twin of a project remains an invaluable resource, providing predictive maintenance, monitoring system performance and offering insights that can be applied to future projects,” Pollard says.
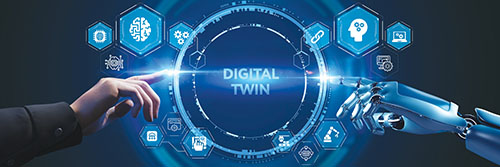
Construction Examples
McPhail and his company first turned to digital twins when constructing an automated parking garage. The team built a digital twin of the garage system to optimize car storage and retrieval times.
“It was like a solver-type game where, depending on where cars were parked, multiple moves were required to store or retrieve them,” McPhail says. “With the twin, we were able to run tens of thousands of virtual moves to figure out the most efficient way to handle this, cutting down operational inefficiencies significantly.”
McPhail designed the simulation using Unity Pro, a platform typically used for video game development. As they evolved, they used software from ABB, Siemens and Rockwell Automation as well as CAD programs like SolidWorks.
Dunn and Stack Modular regularly use digital twins. However, the company has used the traditional digital twin from Autodesk.
The team landed a job building numerous prisons for a government body. While prison walls are traditionally concrete to ensure security, the team was tasked with building steel prisons. Would the walls be sufficiently secure? “We had to confirm a bullet couldn’t go through,” Dunn says.
To test the wall’s capability, the team used digital twins. “It took us one step into the physical world as it allowed us to see how the wall reacts,” Dunn says. Ultimately, the team got the design right and delivered a product that met the client’s requirements.
A January 2024 McKinsey article cites a practical example where digital twins led to cost savings. “A factory digital twin developed and deployed for an industrial player was recently used to redesign the production schedule, compressing overtime requirements at an assembly plant and resulting in a five to seven percent monthly cost saving.”
Digital twins offer offsite manufacturers a step toward perfecting the process. Construction teams can be confident about constructability, customers can engage in the process on a deeper level and the manufacturing process is made more efficient. The potential of digital twins makes it a technology that offsite manufacturers should consider going forward.
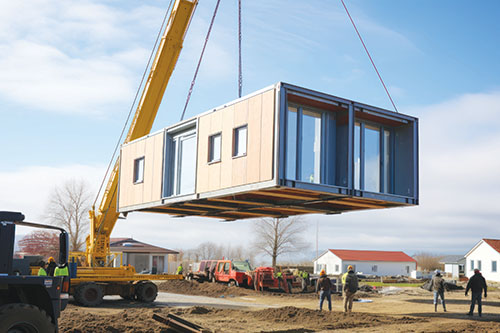
Larry Bernstein is a freelance writer based in northern New Jersey.