Assessing the Benefits of Partnerships Between Modular Home Manufacturers and Panelized Construction
By Dennis Michaud, Managing Director of CertainTeed Offsite Solutions
In 2023, the total number of American homes sold annually plummeted to its lowest in nearly 30 years. Inflation and supply shortages drove mortgage rates higher and made costs prohibitively expensive for many potential buyers.
However, that slumping data is not indicative of actual housing needs — especially not today in 2024. According to a recent report, Freddie Mac estimates that 1.5 million new homes are needed to meet the current market demand. Lingering material supply chain issues, the cost associated with building regulations, and the perennial challenge of labor shortages continue to make the challenge of meeting that demand greater for home builders.
Traditional construction methods, while reliable, often come with significant drawbacks — extended timelines, unpredictable weather-related delays, and the amount of reliable on-site labor required.
These challenges are prompting a growing number of builders in the industry to explore alternative methods. Modular home manufacturing and panelized construction have emerged as viable solutions for delivering the efficiency, productivity, reliability, and innovation builders need and the aesthetic customization homebuyers want.
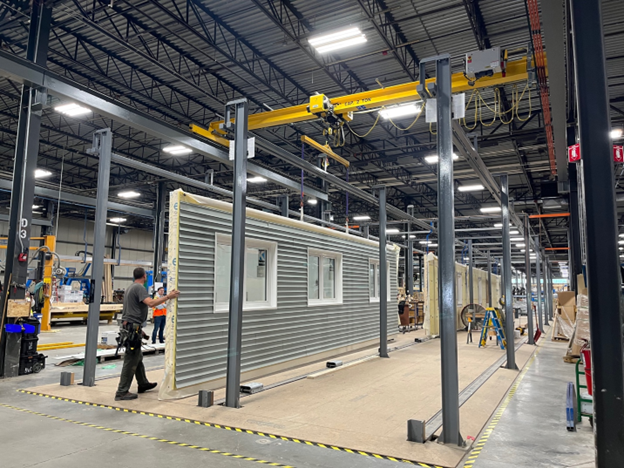
Synergizing Modular and Panelized Construction
Modular manufacturing involves prefabricated structures made up of multiple sections that are constructed almost entirely into a home in a factory setting and then transported to the building site. Panelized construction walls, floor, and roof panels are created in a factory setting and then transported to the construction site to be assembled.
Because of their factory-based production line approach, both modular home manufacturing and panelized construction offer efficiency advantages that traditional building simply cannot. However, the efficiencies of each can sometimes create unintended limitations. By combining the approaches, builders can create a synergy that enhances the process and construction capabilities even further.
There are a number of ways in which integrating modular and panelized methods can lead to faster, smarter, and more customizable homebuilding. Here are a few examples.
Enhanced Customization
One of the primary demands of modern homebuyers is the ability to customize their living spaces. By integrating modular and panelized construction, builders can offer a higher degree of personalization. Modular units can be tailored to include various layouts and features, while panelized components can be customized to match specific architectural styles. This combination allows for a broader range of design options, enabling builders to meet the unique preferences of each client.
Logistics
Transporting modular structures from the factory to the assembly site is not always straightforward. Roads may be restrictive, bridges may prevent throughways, and construction sites may be too crowded for staging full-sized mods cranes that are required for placing them. These factors may render a purely modular approach cost-prohibitive or even impossible. A hybrid approach between modular and panelized can optimize shipping methods and costs, making possible projects that would otherwise not work for modular alone.
Accelerated Construction Timelines
Combining modular and panelized construction can drastically reduce the overall timeline of a project. For instance, while the modules are being fabricated in the factory, the panels for the remaining structure can be simultaneously prepared. This parallel processing minimizes downtime and accelerates project completion. Furthermore, the assembly of panels on-site can be synchronized with the installation of modular sections, ensuring a seamless and efficient build.
Improved Quality and Consistency
The controlled factory environments used in both modular and panelized construction ensure consistent quality across all components. This leads to fewer defects, higher precision, and better overall durability. Most modular units and panels are built to the same standards or higher than traditionally built homes. When these high-quality modules and panels are combined, the resulting structures exhibit superior performance and longevity compared to traditionally built homes.
Cost Savings
Efficiency gains from the combination of modular and panelized construction can lead to cost savings for builders. Reduced build times translate to lower labor costs, and the optimization of materials in a factory setting minimizes waste. Additionally, enhanced quality control reduces the likelihood of costly repairs or rework after a home is constructed.
Sustainability
Both modular and panelized construction methods are inherently more sustainable than traditional building techniques. The factory-based approach reduces material waste, lowers energy consumption, and minimizes the environmental impact of construction activities. By combining these methods, builders can create homes that are not only efficient and customizable but also environmentally friendly.
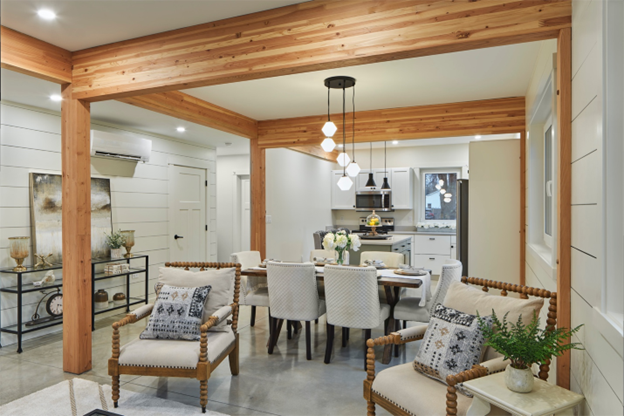
Unleashing the Creativity of Customization
As noted above, the integration of modular home manufacturing and panelized construction not only offers opens a world of possibilities for aesthetic and structural customization. The combination empowers builders and designers to create unique, personalized homes that cater to the specific tastes and needs of individual homebuyers.
Let’s explore the various customization options available through this innovative approach.
Interior & Exterior Design Options
One of the primary advantages of combining modular and panelized construction is the ability to achieve high levels of aesthetic customization. From exterior finishes to interior layouts, these methods offer unparalleled flexibility in design.
- Floor Plans: Modular construction offers a wide array of floor plan options, allowing for customized layouts that suit the homeowner’s lifestyle. Open-concept designs, multi-story layouts, and flexible living spaces are all possible. Panelized construction complements this by enabling floor plans that would not be efficient in a modular approach alone.
- Structural versatility: Because the goal of modular manufacturing is to yield nearly complete homes out of the factory, the results often end up in box-like structures. Homebuilders seeking to provide buyers with unique structural features, such as mezzanines or lofts, or just extra space, can benefit from the flexibility of adding panelized construction into the mix. These additions can be designed and built to complement the overall structure, connecting modules, or providing additional living or storage space.
- Architectural styles: Modular and panelized construction can accommodate a wide range of architectural styles, from contemporary and modern to traditional and craftsman. Builders can select or design modules and panels that fit the desired aesthetic, ensuring that the final product aligns with the homeowner’s vision.
- Roof designs: Panelized construction enables the creation of complex roof designs, such as gables, dormers, and overhangs. These features can add visual interest and curb appeal to the home. The integration of modular construction allows for the seamless incorporation of these roof elements, enhancing the overall aesthetic. Though it should be noted that more intricate roof pitches may not suit modular shipping standards.
- Fenestration: Customization of windows and doors is easily achievable with modular and panelized construction. Homebuyers can select from a variety of positions, shapes, sizes, and styles, including bay windows, sliding doors, and French doors. These elements can be positioned to maximize natural light and enhance the home’s exterior appearance.
- Materials and finishes: The use of panelized construction allows for the incorporation of diverse exterior finishes, including brick, stone, wood siding, and stucco. These finishes can be applied in the factory, ensuring consistency and quality. Additionally, various textures and colors can be chosen to match the homeowner’s preferences. Homebuyers can also choose from a diverse selection of interior materials and finishes, including flooring, cabinetry, countertops, and wall treatments, all of which can be customized to reflect personal tastes.
Finding the Right Panelized Construction Partner
If you’re a modular manufacturer, selecting the right panelized construction partner is crucial to maximizing the benefits of this innovative building method. A reliable partner can ensure that your project runs smoothly, on time, and within budget while meeting your customization and quality expectations.
Traditionally, panel fabricators are limited to framing and sheathing, and, rarely, windows. But some companies go even further. CertainTeed ONE PRECISION ASSEMBLIES panels, for example, incorporate structure, windows, doors, insulation, moisture membranes, house wrap, and siding.
Beyond the basic considerations of geographic proximity, reliability, and financial stability, here are key considerations for finding the right panelized construction partner.
Experience and Expertise
Look for a partner with extensive experience in panelized construction. A sound reputation in the industry is a good indicator of both experience and quality. Reputable companies generally have a history of satisfied clients, successful projects, and consistently delivering high-caliber results. Seek out partners known for their reliability, quality work, and customer satisfaction. Reviews, testimonials, and industry accolades can provide additional assurance of their capabilities. Experienced partners are better equipped to navigate challenges and provide valuable insights into optimizing the construction process.
Quality Control and Precision
A reputable panelized construction partner should have rigorous quality control measures in place. Factory-based construction requires high precision and consistency, so ensure that your partner uses advanced technology and adheres to stringent standards to deliver top-quality panels.
Panel Components
It’s important to understand what components are (and aren’t) included in the panels of a potential construction partner. While some panel manufacturers include basic interior and exterior components, others may cover everything from framing, sheathing, and cladding to weather-resistive barriers, insulation, and drywall to fenestration, electrical wiring, and plumbing connections. Additional performance features, such as sustainable and fire-resistant materials, may also be a standard offering from some manufacturers. Pre-Integrated panels with comprehensive features can be beneficial in offsite construction for their time savings, quality control, waste reduction, and cost efficiencies.
Customization Capabilities
Your partner should offer a wide range of customization options, from design flexibility to material choices. Discuss your specific needs and preferences with potential partners to ensure they can accommodate your vision and provide the necessary customization features.
Toward the Future of Homebuilding
The synergy of modular home manufacturing and panelized construction offers a revolutionary approach to homebuilding. This combination not only accelerates construction timelines and improves quality but also provides extensive opportunities for aesthetic and structural customization. Homebuyers can realize their unique visions, creating personalized living spaces that cater to their specific needs and preferences.
As the construction industry continues to evolve, the integration of innovative practices will further enhance the customization potential of modular and panelized construction. Builders who embrace these methods will be well-positioned to meet the growing demand for high-quality, customized homes, paving the way for a smarter, faster, and more innovative future in homebuilding.
Learn more about how partnering with CertainTeed ONE PRECISION ASSEMBLIES can benefit your company: certainteed.com/opa