Unleashing Efficiency and Innovation in Offsite Construction
Most people think of “Lean” as a collection of tools, techniques and strategies to be implemented. A “to-do list,” if you will. In reality, Lean is much more than that. True Lean – persistent, sticky, effective Lean – is about culture. It’s about all the invisible, enabling principles that are built brick-by-brick, over time, and which support and sustain the visible practices.
In the fast-paced world of offsite construction, establishing and maintaining a Lean culture is essential for companies that want to to stay ahead of the competition. Lean principles are all about maximizing value and minimizing waste, and they can transform your company into a well-oiled machine that delivers projects with speed, precision and cost-effectiveness.
In the following paragraphs, I explore why adopting a Lean culture is crucial for your offsite construction company. I also provide practical steps on how to implement it, and more importantly, maintain it.
Why Lean? The Case Efficiency
If you’ve read my previous articles, you already know the answer to the question, “Why Lean?” But if not, imagine an offsite manufacturing process where each step flows seamlessly into the next. Waste is minimized, finished components are flying out the door to meet customer demand, and employees are safe, engaged and motivated. That’s the power of a Lean culture.
According to a study by McKinsey, Lean organizations are up to 50% more productive than their non-lean counterparts. By embracing Lean principles, offsite construction companies can achieve several key benefits:
Increased Productivity. Lean practices streamline operations, eliminate bottlenecks and optimize workflows. This efficiency boost translates into faster production, allowing you to take on more projects and expand your market share.
Reduced Waste. Lean is all about eliminating waste in the form of unnecessary movement, redundant processes, or other Non-Value-Add (NVA) activities. By minimizing waste, you’ll save on both costs and time.
Enhanced Quality. By focusing on continuous improvement, a Lean culture fosters a mindset of quality assurance throughout the organization. As a result, defects are reduced, customer satisfaction soars, and rework, callbacks, and warranty work become a rarity.
Empowered Workforce. A Lean culture empowers employees by encouraging their active participation in problem-solving and decision-making. This sense of ownership leads to increased engagement, creativity and job satisfaction, resulting in higher employee retention and easier recruiting.
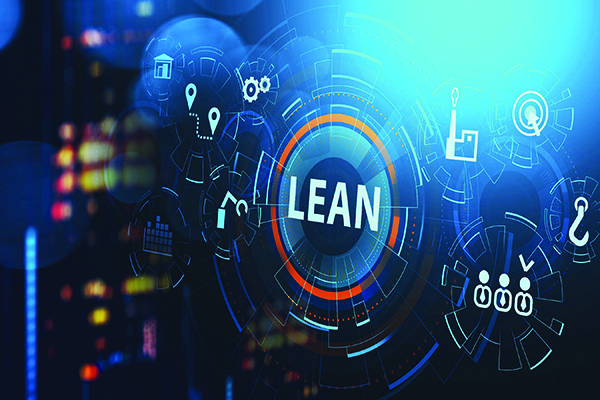
The Blueprint for Success
Now that we’ve (re)established the importance of a Lean culture, let’s dive into the steps you can take to implement and maintain it within your offsite construction company.
Success requires the following:
Leadership Commitment. Begin by establishing the commitment of top-level management to lead the Lean transformation. As the saying goes, “Fish rot from the head down,” so make sure that you as the leader embody the principles you want to instill.
Education and Training. Equip your employees with the necessary knowledge and skills to embrace Lean practices. When appropriate, partner with certified Lean experts to conduct workshops, provide training sessions and encourage key employees to seek certifications such as Lean Six Sigma. The more they know, the more they can contribute.
Visualize and Streamline Workflows. Use visual management techniques such as Kanban boards and Value Stream Mapping (VSM) to make workflows transparent and eliminate unnecessary steps. This visual approach will not only aid communication, but also help to identify areas for improvement.
Encourage Collaboration and Innovation. Foster a culture of collaboration, where individuals from different teams work together to solve problems and generate innovative ideas. Emphasize the importance of open communication channels and cross-functional cooperation.
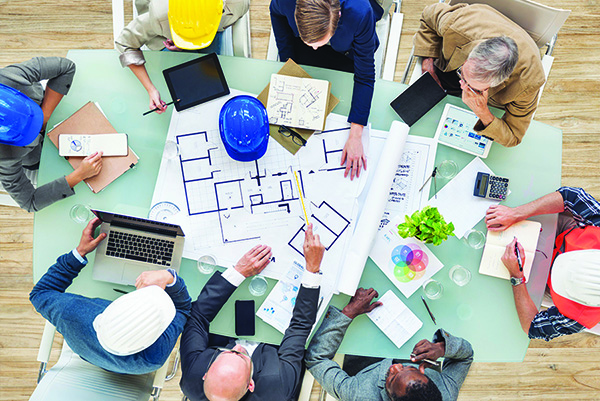
Measure and Celebrate Success. Establish Key Performance Indicators (KPIs) to monitor the progress of your Lean initiatives. Hold daily stand-up team meetings to celebrate achievements and recognize individuals and teams who have contributed to the success of Lean projects. This positive reinforcement will motivate others to follow suit.
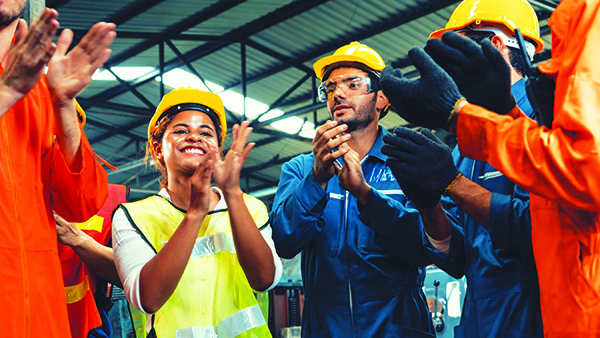
The Journey Never Ends
Establishing a Lean culture is not a one-time effort; it requires ongoing commitment and continuous improvement. Here are some ways to ensure that your Lean culture thrives:
Regular Gemba Walks. Gemba walks involve leaders going to the “gemba,” or factory floor, to observe processes and gather insights firsthand. By engaging with employees and listening to their ideas and challenges, leaders can identify opportunities for improvement and maintain a culture of continuous learning and adaptation.
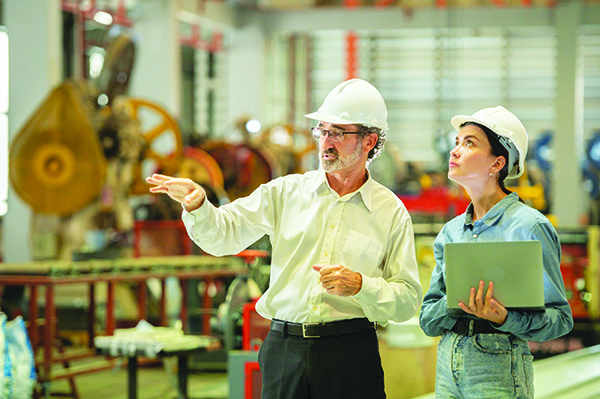
Kaizen Events. Conduct regular Kaizen events, which are focused improvement workshops aimed at addressing specific problems or bottlenecks. These events provide a platform for cross-functional teams to collaborate, brainstorm solutions and implement changes rapidly. Remember, small incremental improvements lead to significant long-term gains.
Sustain Employee Engagement. Keep employees engaged by encouraging their involvement in Lean initiatives. Recognize their contributions, provide avenues for feedback and create a culture that values their ideas and suggestions. When employees feel valued and heard, they become champions of Lean practices.
Embrace Technology. Once the process is optimized, leverage technology to support your Lean efforts. Implement digital production tracking software, collaboration tools and data analytics platforms to streamline processes, track performance and make data-driven decisions. Technology can be a game-changer in driving efficiency and continuous improvement.
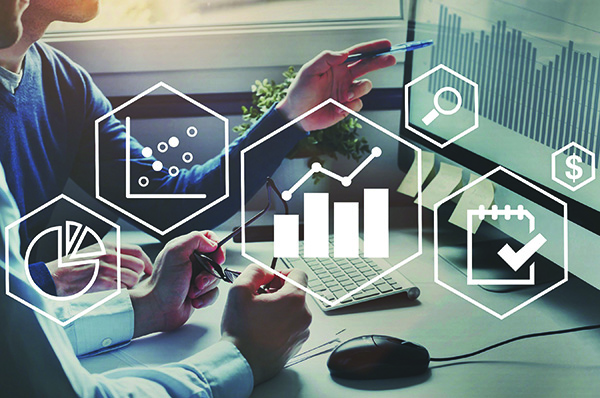
Stay Agile and Adaptive. The offsite world is constantly evolving, as it disrupts traditional construction. Embrace a mindset of agility and adaptability to respond to changing market demands, new technologies and emerging trends. Continuously seek opportunities to innovate and refine your Lean practices.
Building a Lean culture is not just a business strategy; it’s a transformative journey that can revolutionize your offsite construction company. By prioritizing efficiency, reducing waste and empowering your workforce, you can unlock the full potential of your organization and thrive in an increasingly competitive landscape.
Remember, a Lean culture is a continuous process, requiring leadership commitment, employee engagement and a commitment to ongoing improvement. So, embark on this journey with enthusiasm, a sense of humor and a determination to build a Lean and prosperous future.
As Taiichi Ohno, the father of the Toyota Production System, once said, “Progress is impossible without change, and those who cannot change their minds cannot change anything.” Embrace change, embrace Lean and witness the transformation of your offsite construction company into an industry leader.
Daniel Small is a Denver, Colo.-based management consultant to the offsite construction industry. He specializes in Lean Construction and Manufacturing and Six Sigma methodologies. For assistance with improving your offsite manufacturing process, contact him at 719-321-1953 or [email protected]. Or visit www.LeanOffsite.com.
[…] inspiration from the insights shared in “Building a Lean Culture,” which I wrote for the June 2023 issue, instilling a culture of data literacy is akin to embedding Lean principles into the fabric of your […]