A good place to start improving your factory’s efficiency is by attacking the most wasteful processes
by Daniel Small
• Specific bottlenecks that slow down production tend to be consistent from one modular factory to another and have proven solutions
• The most common bottleneck by far is wasted time during drywall finishing, which can be reduced with innovative materials that reduce long-run costs
• The author also recommends solutions and training to eliminate wasted time in other processes and to continually improve efficiency
Every process has a limiting factor, an activity or step that limits the flow rate of the entire process. This limiting factor, or constraint, is also known as a bottleneck or pinch point. The Theory of Constraints (TOC) is a method of identifying and improving the limiting factor. It’s a very straightforward way to improve the performance of a process.
Modular construction, of course, has its own set of constraints. In fact, I have found a very clear pattern of constraints in the modular factories I’ve worked with in my process efficiency research and consulting.
Self-Declared Constraints
In surveying multiple factory managers across the US about their operations, I asked them to identify their biggest problem stations as well as the types of problems they see in those stations. Overwhelmingly, the most common problem area is drywall finish, and by far the most common type of problem is time cost/waste.
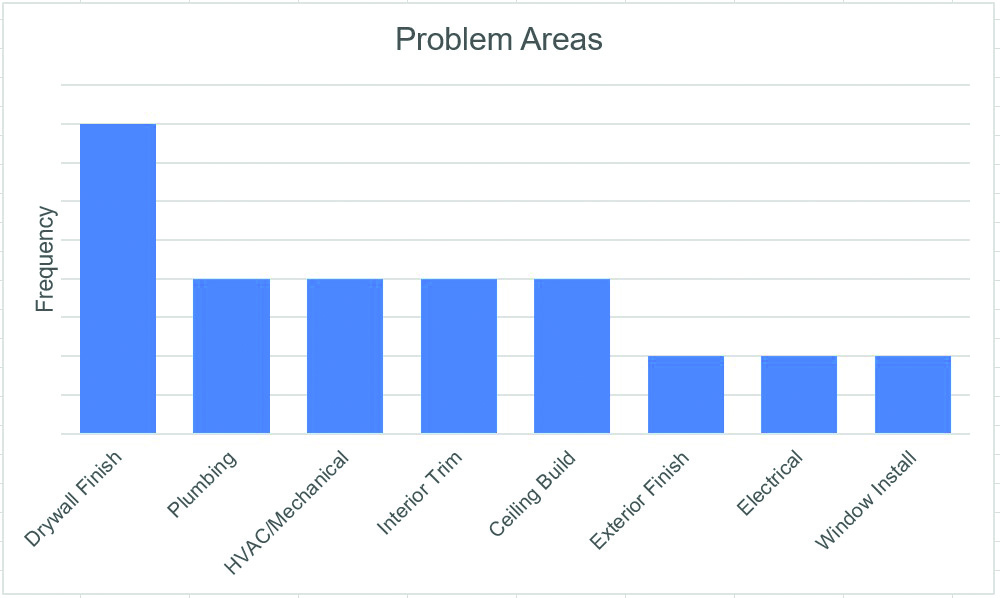
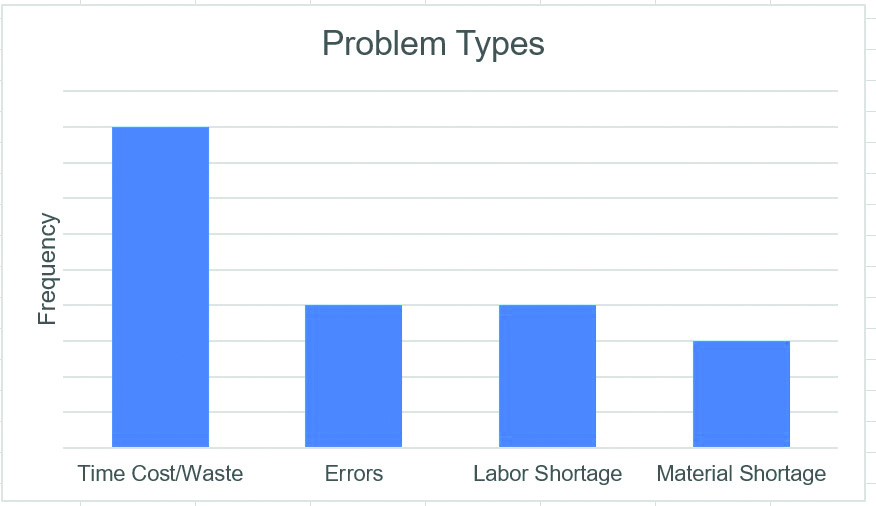
If you’re a factory manager, you are probably nodding your head right now. The process of getting interior wall surfaces finished to an acceptable level, then dried in preparation for painting, takes an inordinate amount of time and effort, often holding up the line.
To add insult to injury, the entire drywall system is prone to cracking and other damage during transport, which can lead to expensive field repairs.
Causes
The crux of this problem lies in the traditional materials currently used to create a smooth interior wall surface and the methods by which they’re commonly applied. Gypsum is a heavy, brittle material; it makes assembly difficult and slow and is prone to damage. Seams and imperfections are smoothed over using a hand-applied wet paste, which then needs to dry and be sanded down to its final finish. This is a complex, difficult, slow, and error-prone process requiring highly-skilled and experienced craftspeople.
Recommended Actions
I believe the key to removing the drywall constraint is partnering with innovative materials suppliers to develop a wall surface material that will provide the critical properties of gypsum (fire resistance, straightness, etc.) while reducing or eliminating the disadvantages mentioned above.
Observation-Based Constraints
In addition to surveys, my team and I also analyzed video recordings of multiple modular installation processes. Of the processes analyzed so far (shown in the chart below), the product categories with the lowest Process Cycle Efficiency, or PCE (the percentage of time spent on work that directly contributes to the result), were the following:
● Cabinets (16.8% PCE)
● Countertops (9.7% PCE)
● HVAC Duct Installation (10.5% PCE)
For a more detailed explanation of Process Cycle Efficiency, see my article “Why is Modular Falling Short of Its Potential?” in the February 2022 issue.
Causes
The inefficiency of these processes stems from various root causes. In the case of cabinets and countertops, transportation (carrying stuff around), planning (measuring stuff), and waiting (standing around) were the dominant forms of waste. These wastes are mostly caused by sub-optimized/poorly-designed processes, from staffing to inventory management to information flow.
Ducting installation is typically done by a crew of three to eight workers. Much of the waste in this process occurs while prepping materials for installation—preassembly, modification, etc.
Recommended Actions
The cabinet and countertop installations can usually be improved by making modifications to your process design. For example, using “flex” or “rover” workers to assist only with peak-demand tasks can reduce waiting waste. Storing materials in groups by module and close to the workstation can reduce transportation waste. Marking target installation locations on the module can reduce planning and inspecting waste.
To reduce waste in the duct installation process, working with materials suppliers and distributors to get more prep work done before the material is delivered to the factory can reduce prep waste.
Training is Your Productivity “Golden Goose”
In addition to the station-specific measures described above, one of the most powerful ways you can level up your factory’s productivity is through ongoing, specialized training in Lean Manufacturing and process optimization. This will create a continual source of constant improvement in a virtuous cycle.
Implement advanced training of certain personnel to begin creating a culture of continuous improvement and quality. Most workers want to be productive, and when they understand how to spot was
Provide your production managers and supervisors (beginning with your top problem areas) with training (initial and ongoing) in Kaizen, visual management, 5S, Gemba, statistical process control, Lean Management, TOC, and other Lean concepts. Consider Lean Six Sigma certification for upper-level production managers, to enable and empower them to proactively make continuous improvements. (Feel free to contact me at the information below if you’d like help with this training.)
Train the line workers in your problem areas in basic principles of Continuous Improvement, quality control, waste identification & reduction, etc. Select your most inefficient tasks that are constrained by process, rather than by product. These processes will be easiest to improve quickly without help from suppliers. Later, you can expand your efforts to include measures requiring long-term cooperation with partners.
Conclusion
Although the processes I’ve discussed here represent the most common constraints in the factories I’ve studied over the years, your factory’s constraints may be different, and for different reasons.
I encourage you to conduct your own process-efficiency assessment (for instance by using the method I described in my March 2022 article, “Sharpening Your Modular Saw”.) This will indicate, or confirm with data, where your constraints are.
Next, begin with the leading constraint and improve it until it’s no longer the leading constraint, and then move to the new leading constraint.
Meanwhile, begin now to institute an ongoing program of training your people in Lean thinking.
In this way, you can increase your productivity, efficiency, and profitability in the near term, while laying a foundation for long-term continuous improvement.
Daniel Small is a Denver, Colo.-based management consultant to the building industry. He specializes in Lean Construction and Manufacturing and Six Sigma methodologies. Contact him at [email protected].
[…] to crack during transportation. Because of these issues, the drywall process is considered the biggest problem station by modular builders, by a wide […]