A South Carolina company brings the efficiencies and quality advantages of offsite construction to a very traditional, handcrafted market
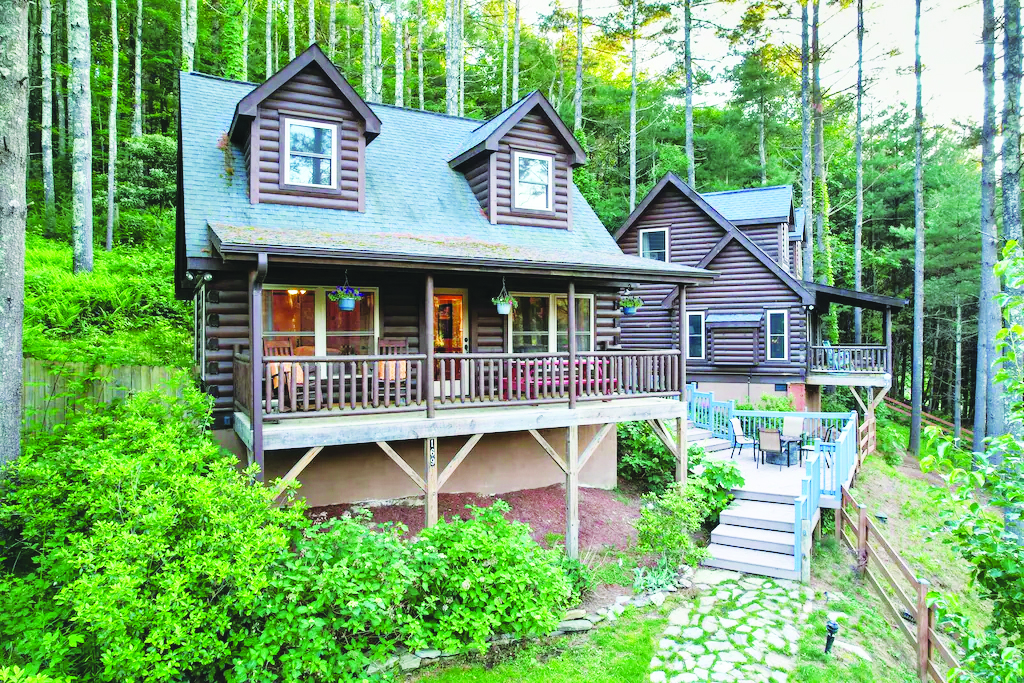
Although modular log homes may sound like a novel concept, they’re a proven construction method with strong appeal in some markets, especially rural, mountain areas. They often serve as second residences, and a growing number of investors are building them for use as short-term vacation rentals.
Some developers have even built communities with them. Blue Ridge Log Cabins in Campobello, S.C. has been in the modular log home business for 20 years, and while their core products are custom homes, they also complete a few developments every year, usually with 10 to 20 units, according to company president Chip Smith.
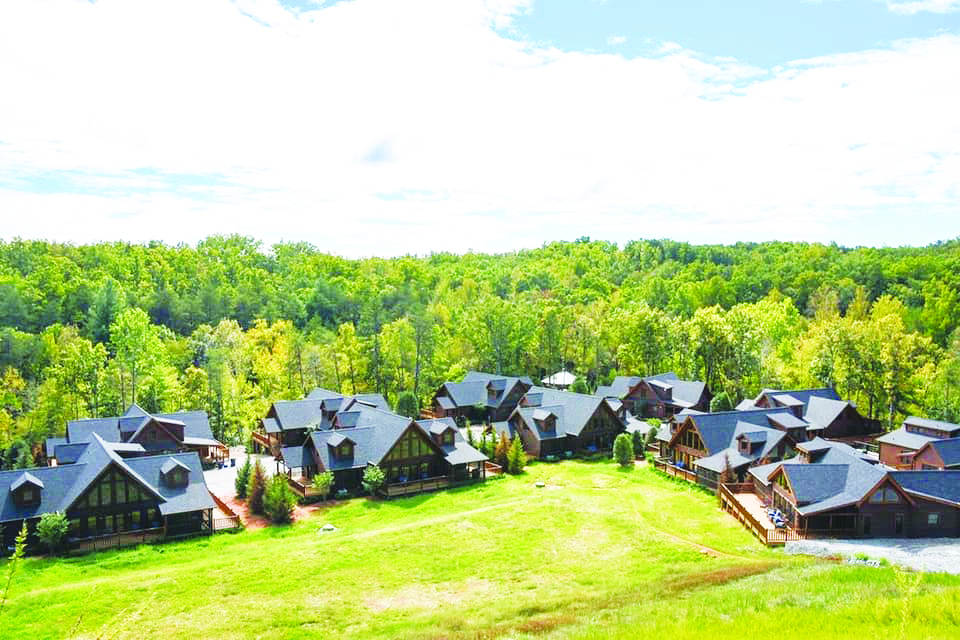
Blue Ridge isn’t the only modular log home manufacturer but while some companies limit themselves to single modules, its homes are multi-sectional—that is, any number of modules can be combined for any home design. That allows for larger, more complex structures. Modules are trucked to the site and craned into position, which for most projects takes less than one day.
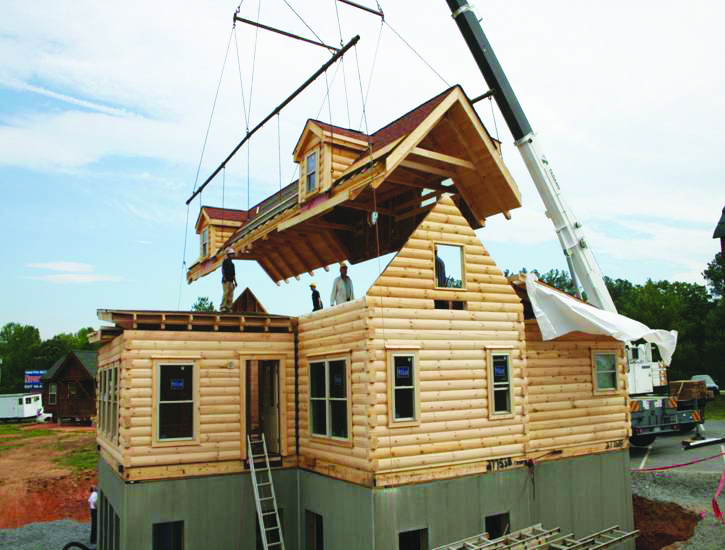
Exterior walls are solid log construction, not log siding. Customers around the country seem willing to pay for the real thing, despite shipping costs. “We have delivered to 32 states from Arizona to Colorado to Wyoming and Maine, as well as to Canada,” says Smith.
How They’re Built
Blue Ridge uses readily available Eastern White Pine logs. They’re kiln-dried to 18% or 20% moisture content then coated with an exterior stain that includes an insecticide. Customers can choose from various stain colors.
Smith describes the assembly process as “fairly complex.” The exact details used to fasten each log to the one below it depend on where the home is located, with the main variables being local code requirements for wind resistance and seismic bracing. In general, however, logs are keyed to one another with a double tongue and groove detail. Workers apply foam tape and caulk between courses to create a draft-free structure, and then drive screws through the logs to secure them.
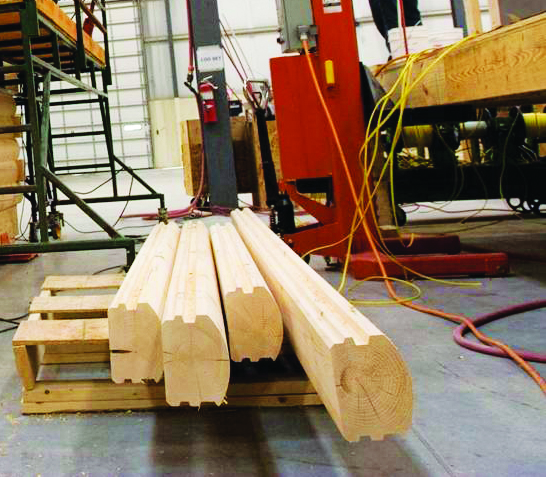
Interior walls are stick framed then covered with rustic-looking wood paneling. Floors and ceilings are also solid wood. Cabinets and most interior trim are also installed at the factory.
The modules arrive at the site pre-wired and pre-plumbed, which removes a common objection to log construction. “The typical electrician or plumber doesn’t like working with logs, but with our system, they don’t have to,” says Smith. On-site mechanical and electrical work involves making connections between modules where necessary and connecting the house to the utility services.
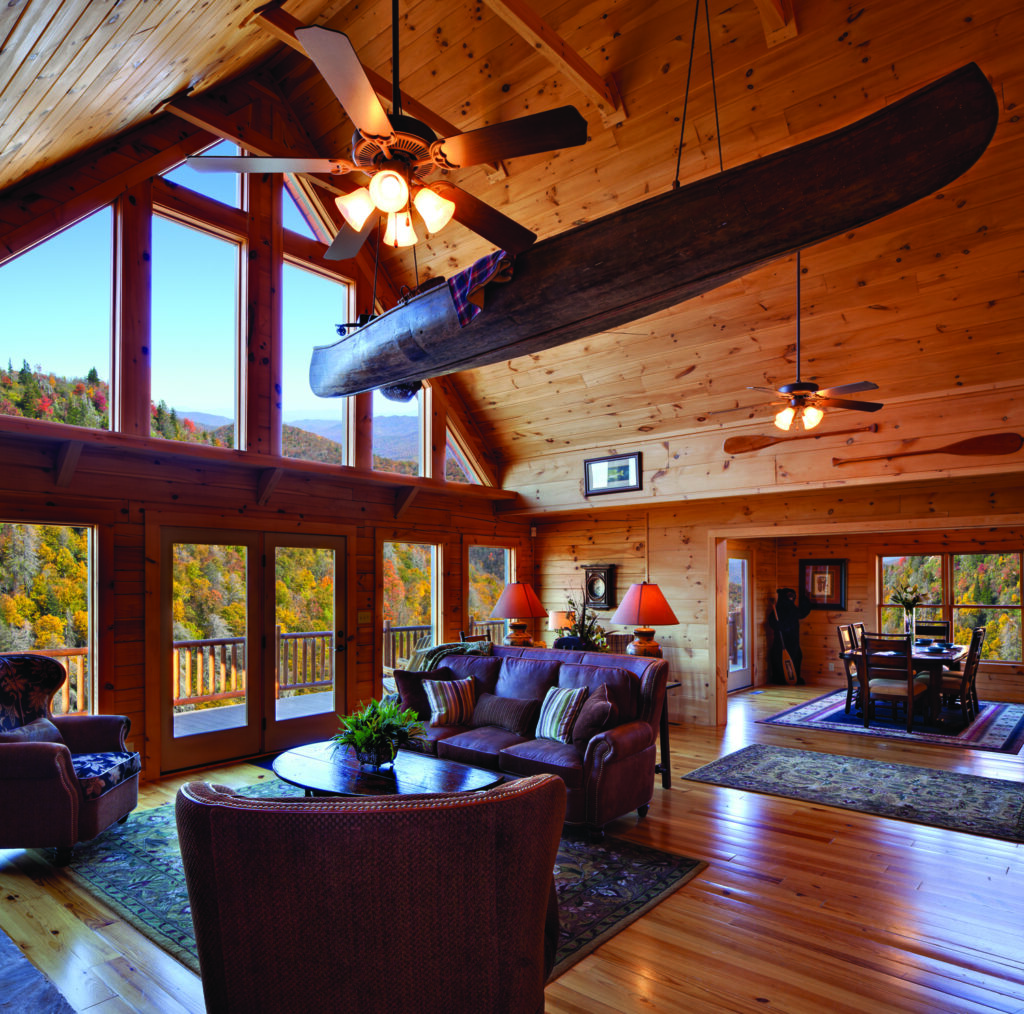
Most of the company’s homes have vaulted ceilings. Roofs are clad with architectural shingles. If the customer wants a metal roof, Blue Ridge will prep the home for it, but the customer needs to get their own roofing contractor to install the metal.
Modular Advantages
The first question most people ask is, why choose a modular log home rather than building a traditional site-assembled one?
Some of the advantages are the same as those offered by conventional modular, such as the ability to get homes finished more quickly. In addition, assembling logs on-site is a difficult job that needs to be done by workers with specialized skills but with modular, the small amount of site finishing can be done by standard carpentry crews.
There’s also a quality advantage, thanks to the fact that the kiln-dried logs are kept inside until the module is ready to ship. “It’s better to build in a factory where it’s dry and the logs don’t get wet before they’re used,” says Smith. A common complaint about log homes is that wet logs settle over time as they dry out, leading to cracked logs and creaking noises that homeowners don’t like. Assembling dry logs in a controlled indoor environment minimizes those problems.
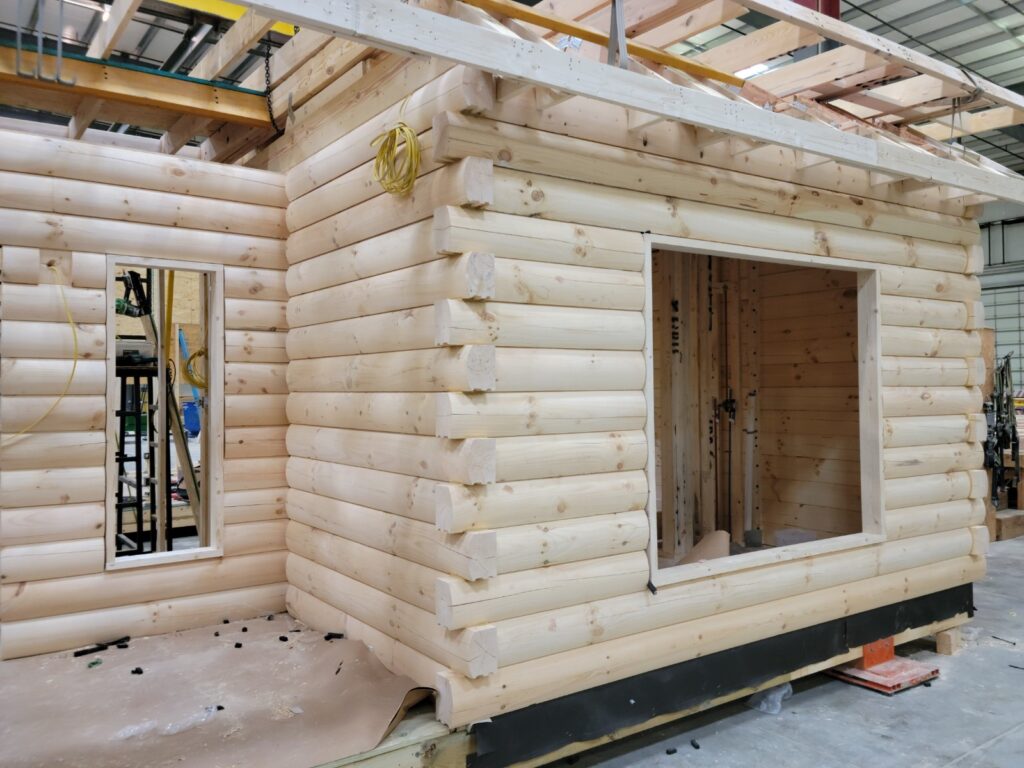
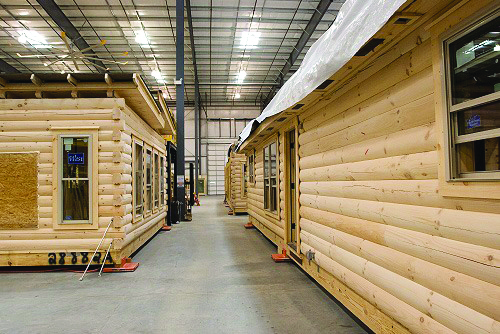
Then there’s the question of thermal performance. Does the lack of insulation in the exterior walls increase heating and cooling loads? Smith says no. In fact, log homes have to satisfy the same IECC and local energy code requirements as every other type of construction.
“The U.S. Department of Energy asked us to build a conference center at Oak Ridge National Lab,” says Smith. He knew the lab’s engineers would run many tests on the completed structure including a blower door test to measure air leakage and he was curious as to how the building would perform. “They called us to say that it was so tight that they had to put in more ventilation than they expected,” he says.
Blue Ridge also offers a non-log modular product with a similar aesthetic—its Mountain Architecture series. This design appeals to builders or developers who want the rustic interior offered by log construction, but prefer framed walls. Exterior stud walls are finished on the outside with board and batten siding and on the inside with the same rustic boards used in the company’s log homes.
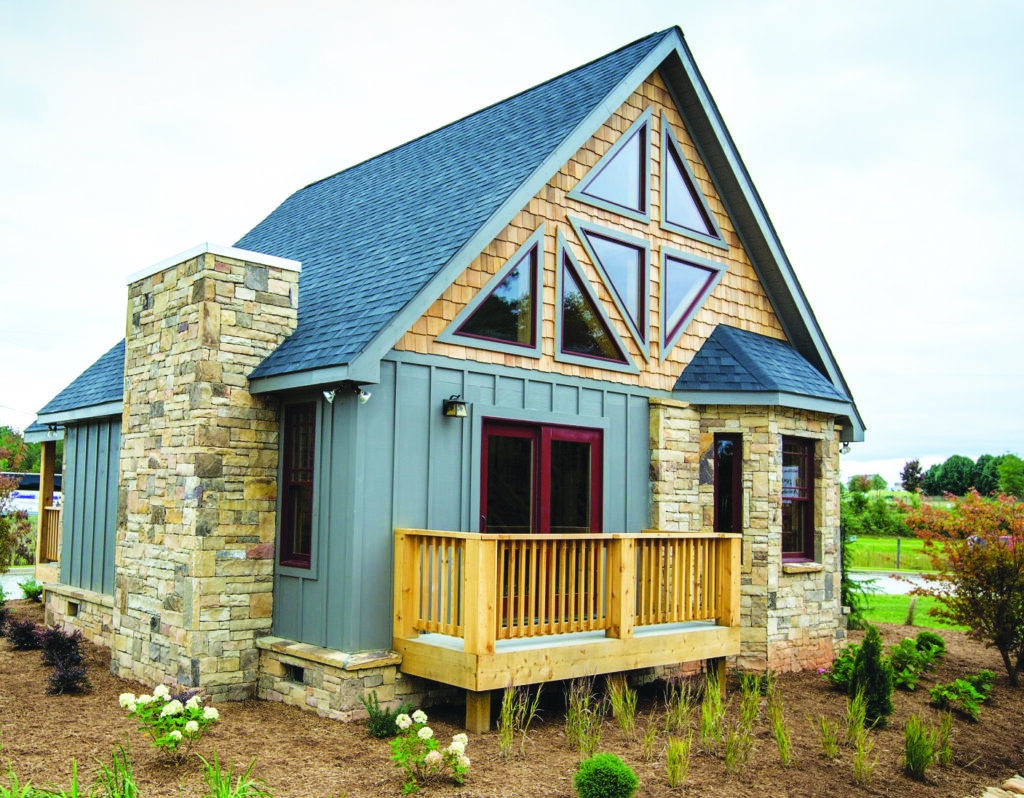
Interested builders, developers, and even homeowners are welcome to tour the factory. “Before COVID we used to host Open House days for buyers and prospective buyers, and typically had more than 100 people visiting the factory at a time,” says Marketing Director Sarah Smith. Tours have been on hold for the past two years, but she says they are about to resume.
The bottom line is that while log homes will always be a niche product, the modular approach makes them more practical for a builder or developer who doesn’t have the skills needed to assemble them on-site, yet works in a market where customers would be receptive.
It’s one of the many examples of the versatility made possible by offsite construction.